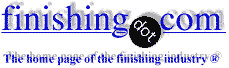
-----
Silver vs. Tin Plating of Low-Voltage Contacts made from Copper & Brass

this text gets replaced with bannerText
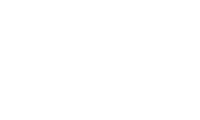
May 2, 2022
RFQ: Hello All,
After reading many posts about similar subjects and searching for a thread more specific to our project I started this new thread. Apologies if there is an existing thread.
I don't have much experience with plating, and am doing my best to get a crash course in it for an application we have for some 24 V (a.c. or d.c.; up to 2 amps) spring-loaded contacts for a gate switch.
As a starting point for our design, we looked at a contact set that has two parts. One _appears_ to be either matte silver or tin plate on a copper substrate. We would do a test on the plating to determine what it is (thinking of acid tests available for silver).
The other contact appears to be brass with matte silver or tin plating. They both have the same appearance. And, the reference design is intended for higher voltages of 120 or 240 V, so from what I read I assumed that arcing might be more of a concern that would justify the more expensive silver plating.
If I am understanding what I have read, the differing copper and brass substrates may be to reduce the chances of the plating galling. Does this make sense? The spring-loaded contacts have a rubbing or wiping effect due to the curved path of movement, so we want to be sure to consider the possibility.
And in the case of either substrate, we would probably want a barrier layer of (matte or bright nickel?) plating, perhaps 1.25 microns thick.
It sounds to me like tin plating over nickel might be the thing to use over both substrates for economy and durability, and that we don't really need silver.
This is a contact that opens and closes anywhere from every several minutes, 24/7, to maybe once a day.
What I am wondering is what thickness would be appropriate for the top coat? I saw mentions of tin alloys. Is plain tin sufficient, or should I consider something different for better wear properties?
Is 1.25 microns of nickel the right choice for the barrier layer?
Do we also need an anti-tarnish layer? What kind and thickness?
Sorry for going on so long, but I wanted to make it interesting and specific enough, based on the little knowledge and information I have.
What we really would like is a vendor (or vendors) who can quote making the parts, and provide us with some guidance so we donŐt have the kinds of issues people post about on finishing.com!
Thank you
Mike
- Milwaukee, Wisconsin
privately respond to this RFQ
Ed. note: As always, gentle readers: technical replies in public and commercial replies in private please (huh? why?)
Q, A, or Comment on THIS thread -or- Start a NEW Thread