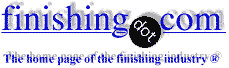
-----
Problem anodizing 7075 (7xxx) aluminum

Q. Hello all,
I came across your thread while looking for a solution to my problem with black anodized parts.
Indeed, I receive non-conforming parts from my subcontractor but he can't find a solution and he thinks it's due to the material.
I would like an external opinion because I see a lot of things on the internet.
You will find pictures of the defects below:
- Belgium
November 21, 2022
⇩ Related postings, oldest first ⇩
Q. I would like to know what causes pits in 7000 series aluminum. I am not sure about the type of anodize process, we just ask for black. I The pit appears to be burned.
I was once told that it is the Zinc in the 7075 etching out, but I don't understand why this would not always happen. These pits were created during the anodizing process.
Jason Light
- Richmond, BC, Canada
2004
A. From the pictures it seems that the base metal has been sanded in two directions. It is also my wildest guess that the sandpaper had been used on steel during the night shift when no one was looking. THe next day when you sanded the aluminum you imbedded small iron particles into the soft Kleenex-like aluminum. Then when you anodized the iron particles which do not "anodize" drew more current and the heat chewed away at the aluminum leaving a burned appearance.
Try some virgin 7075 that has non been mechanically messed up. There is no reason for 7075 to selectively have burned spots unless something else in those spots drew more current.
Another test you can perform to satisfy your own curiosity is to insert a small iron sheet metal screw and put it thru the line - then observe the burned spot.
Robert H Probert
Robert H Probert Technical Services
Garner, North Carolina
Q. The surface is as-machined in a CNC mill. The lines are milling lines. I have no reason to believe that the carbide tool would leave particles in the surface. I have also seen this in turned parts and on as-extruded surfaces.
Jason Light [returning]
- Richmond, BC
Q. I have been able to do some additional work on this pitting problem. I used an energy dispersive x-ray attachment on a scanning electron microscope to determine that at the center of each pit is copper. Copper is one of the main alloying elements in 7075 and is a second phase in the microstructure. So I now understand that the copper is etching preferentially during the anodizing process but I still do not understand why it does not happen all the time with 7075. Is it something to do with the deoxidizing step?
Jason Light [returning]
- Richmond, BC
A. We had seen this problem years ago & then I found an article describing the problem. It was in August 2000 "Products Finishing" & it is titled "Anodic Coating Blisters on 7075".
We eliminated the problem by reducing time in all tanks to a minimum - especially the black dye.
David A. Kraft
- Long Island City, New York
A. With all due respect to Mr. Probert, but I think the finer set of the lines is the grain direction of the extrusion (after etching), the thicker, very evenly spaced lines are left by the cutting tool, the pattern indicates tool feed/stepover/feed per tooth.
So I don't think this is contaminated sandpaper related, more to do with excess etching time and not enough desmutting later, perhaps the excessive etching time was due to reworking of the parts, or requirement of achieving matte surface finish.
Maybe ramp time was too fast or nonexistent, so the high current simply burns through the resistive layer and keeps eroding material creating deep craters that then trap chemicals which creates the white residue.
Could be all of these things combined.
Janis Ziemelis
- Riga
November 22, 2022
Bright anodizing of 7075 (7xxx) aluminum
Q. A supplier is claiming he cannot bright anodize 7075-T6 due to its copper content.
He says putting it in a caustic etch will make it black in colour.
Being relatively new to anodization I don't have all the facts but shouldn't a brightening dip be acid based, sulfuric or other.
And isn't it possible to bright anodize 7075-T6?
Would really appreciate some help with this really general query.
Jack Judge
Engineer - Ireland
2007
A. It's possible to bright anodize 7075 for shininess although the anodize will be colored, unlike that on the purer 5xxx alloys commonly used for reflectors and automotive trim. Brightness also decreases as anodize thickness increases.
That caustic etching leaves a black smut on 7075 is hardly relevant, as a) the smut is easily removed by deox/desmut solution and b) caustic etching should be omitted or at least minimized prior to bright dipping.
Most anodizers do not have bright dip (chemical polishing) solutions, and not all bright dip solutions are suitable for 7075. Some phosphoric-sulfuric-nitric acid bright dips (including some Alupol & Phosbrite versions) can be used on alloys up to 8% Zn and 5% Cu. See The Surface Treatment and Finishing of Aluminum and Its Alloys, pages 110-116, 6th Edn.
Ken Vlach [deceased]
- Goleta, California
Finishing.com honored Ken for his countless carefully researched responses. He passed away May 14, 2015.
Rest in peace, Ken. Thank you for your hard work which the finishing world, and we at finishing.com, continue to benefit from.
A. Surely it's possible to bright anodize 7075-T6. There are other etchants besides caustic. Even castings can be brightened for anodizing.
John Hu
- Singapore
Dark streaks in colored anodize?
Q. We are producing a series of parts for the first time and are having a cosmetic issue with the anodizing. We are seeing dark streak that appear to be related to the grain structure of the metal (7050 AL). The anodize is a green color and the streaks are very subtle, but the cosmetic requirements are very strict.
We are using a new source for anodizing so I want to get some additional input from knowledgeable sources as well. Any help is appreciated.
Shannon Pell
Medical Instrument Manufacturer - Huntsville, Alabama
2007
A. Although lacking the process history, a reasonable guess is that excessive alkaline etching accentuated the grain structure and roughened the surface. For this alloy, about Al-6.2Zn-2.3Cu-2.2Mg-(<0.8%)other, an acidic etch is preferable if etching is required (e.g., to hide machining marks).
Some speckling is typical of anodized 7000-series alloys although it's often rather attractive.
Ken Vlach [deceased]
- Goleta, California
Finishing.com honored Ken for his countless carefully researched responses. He passed away May 14, 2015.
Rest in peace, Ken. Thank you for your hard work which the finishing world, and we at finishing.com, continue to benefit from.
A. The zinc in the 7000 series migrates to the grain boundaries with time and temperature (as in heat treatment or work hardening). This zinc left on the surface plates away when caught "out-of-alloy" on the surface and leave behind "mini-pits". Some 7000 metal, depending on the heat treatment absolutely is non-anodizable to a quality finish.
The streaks may be related to the rolling mill lines or the machining lines combined with the exiting of the zinc from then surface.
Try a lessor alkaline etch. Try a proprietary mixed acid deox. Then try a slower ramp on the start-up of anodizing, otherwise choose a different alloy and/or heat treatment.
Robert H Probert
Robert H Probert Technical Services
Garner, North Carolina
Inconsistency in Black Dye Appearance on 7075
Q. We have noticed an inconsistent appearance on many of our 7075 parts after pulling them from the black dye. We're using new titanium racks, freshly charged solutions in all of the prep tanks, new cable running from the rectifier (and even a new rectifier), and we still get some parts coming out with a nice, semi-gloss appearance, while others have a matt look to them and the dye rubs off. The only thing we haven't yet done is to replace the dye tank and we still haven't tried a strong, ammonium bifluoride / nitric desmut. It doesn't have the characteristics of a chemical problem, however, as chemistry cannot tell the difference between one part and another. I'm starting to think my customer has substandard alloy.
Thanks for your ideas.
Randall Fowler - Fowler Industrial Plating, LLC
Cleveland, Tennessee, USA
October 8, 2008
A. Randy
If some parts dye well and others don't, the dyestuff is not suspect. The powdery coating (wipes off black on a fingertip) suggest over-anodized/burned. Possibilities include inadequate solution agitation in your anodize bath; excessive dissolved aluminum; poor anode:cathode ratio; and poor electrical contact/racking.
If you perform a caustic etch prior to anodize, you might be able to detect variation in the aluminum by the residual smut. Play with the etch times to evaluate.
Willie Alexander
- Colorado Springs Colorado
A. Long time no see, Randy. You didn't mention if the difference you are seeing is in the same load, or in alternating loads. It sounds to me that it's possible the parts that are substandard are overheating in your tank, causing a very soft and worthless anodic coating. Any major difference in the alloys (parts) should be evident after your etch, I would think.
Is there any difference in the coating thickness between the good, and sub-standard parts?
Marc Green
anodizer - Boise, Idaho
A. For dye ruboff, check your seal quality and temperature.
If the part is sticky, we found the cause to be in the desmut tank.
7075 has a high amount of alloy material, particularly copper, so a good desmut step is really needed.
James Watts
- Navarre, Florida
Q. Our products have two aluminum materials: 6061and 7075. We've chosen the 7075-T6 to anodize the surface (black, and we don't care about brightness), but it's always having problems.
Sometimes had bubbles, and sometimes had paint peeling off; we cannot find the reason. Is the cause the suppler or material?
LEO SUI
- TAIWAN TAICHING
August 15, 2012
A. Hi Leo,
It is difficult to make judgements about your problems as you have given us so little detail, but let me give it a go anyway.
If you are not overly worried about material properties I would swap from 7075 to 6061. 7xxx series alloys are high magnesium^zinc alloys and can often suffer from pitting, white spots and various other problems, especially if the wrong current density is used. 6061 is a low alloy material, which is easier to anodise.
Your problem with paint peeling may be something to do with the anodising, but is more likely to do with the paint application. When parts are delivered for paint there are many factors that can affect adhesion, from contaminated surfaces to poor paint application to poor stoving. If you can give us a detailed breakdown of your process we may be able to advise you better, but at the moment all we can do is generalise.
Brian Terry
Aerospace - Yeovil, Somerset, UK
A. I think you will find that the major component in 7000 series aluminum after aluminum is zinc. White spotting is a common problem whit this alloy. Some have found that a 50% nitric plus fluoride helps in the deox stage. As far as bight dipping, it is nasty stuff and most try to avoid using it.
Drew Nosti, CEF
Anodize USA
Ladson, South Carolina
Hi Drew,
You are perfectly correct that 7xxx are zinc containing alloys (where was my brain?!)
Brian Terry
Aerospace - Yeovil, Somerset, UK
Q. I have machined parts from aluminum material 7075 T651 AMSQQA250/12, ASTM B209 that had a clear anodize finish applied per MIL-A-8625 / MIL-PRF-8625 [⇦ this spec on DLA] type 2 class 1. My customer is rejecting the parts because the finish is not clear.
discolored article on right
Don Ullrich
- Illinois, USA
April 17, 2013
A. Nowhere in MIL-A-8625 is a Type II Class 1 anodize described as "clear", only non-dyed (Ref. Para. 1.2.2). In fact, Paragraph 3.5 Class 1 states,"Any natural coloration resulting from anodic treatment with the various alloy compositions shall not be considered coloration."
Chris Jurey, Past-President IHAA
Luke Engineering & Mfg. Co. Inc.
Wadsworth, Ohio
A. Don
Show your customer section 3.5 of the specification. It clearly allows for natural coloration. The 7XXX series will show a fair amount of color (gold) as the coating thickness increases.
If your customer requires a colorless finish, the anodizer will need to cut back on coating thickness.
Willie Alexander
- Colorado Springs, Colorado
A. There is enough "slop" in the range of ingredients in 7075 for a color variation to occur. Also the brown,bronze, tint is very typical in 7075 that is within the range of ingredients
Robert H Probert
Robert H Probert Technical Services
Garner, North Carolina
A. Hi Don,
I think you are being told a few half-truths about why the color has changed. 7075 only contains 1.2 to 2% copper; its main alloying constituent is zinc at 5.1 to 6.1%. I can't imagine that the level of copper in the alloy would cause this problem. Now, if the anodising tank is heavily loaded with copper, then I could understand it a little; even then I'm not convinced it has anything to do with copper.
Brian Terry
Aerospace - Yeovil, Somerset, UK
Q. Hi, Experts,
This is Chuck from China, I am an anodizing engineer; I'm have trouble with an anodizing process.
After type II (MIL-A-8625 / MIL-PRF-8625 [⇦ this spec on DLA] type II, Class 1) anodizing on a forging 7075-T73 alloy part, we found that some areas of the part have discoloration (the discoloration area was penetrated from inside to outside). By the way, these part's raw material was re-heat treatment and re-aging during the forging process since the Tensile yield strength and Tensile ultimate strength cannot meet specification requirements. And we also anodized some normal forging process part without this discoloration issue, also some other parts were anodized at the same time, no discoloration issue, so we excluded the discoloration being caused by the machining or anodizing. We suspected this is a forging raw material issue, and we have did Metallurgical testing, can't find any difference between the normal area and the discoloration area.
1. What is the root cause of the anodizing discoloration?
2. What analysis method can we use to find the root cause?
Thanks a lot.
Chuck Huang
- Shanghai China
March 4, 2014
Want to get brighter finish on 7000 series aluminium
Q. Hi, any advice on getting a brighter finish on 7000 series aluminium? More like 6000 series.
I polish very highly and desmut then anodise for 75% of the time of 6000 series. I run at 12 ASF.
Chris Pocock
- Manchester, UK
May 11, 2014
Clear Anodizing 7075 Aluminium
Q. I know, reading the title, many of you will go, "oh no, not another one...!" :) but yes, after going through a lot of stuff on 'our' dear website as well as lots of others, I still decided to post! So here goes...
The common complaint is from the customers is that "we need a nice bright clear finish after clear anodizing 7075 aluminium" and My definite need is also a coating thickness between 10-20 microns to meet the standards, which, as we all know, is easier said than done. (I am one of those guys who never suggests compromising on the coating thickness just for the sake of the color shade but most of the time the customers remain unconvinced).
So, what I would like to hear from any and all of you experts out here is this...
What are the recommended pre-treatments according to you that would assist in reaching the objective?
What would be the most ideal process parameters to maintain for this alloy?
Please elaborate.
Rubbing salt into the wounds, so to say, was when my son came along and told me that the latest Apple iPhone case was made out of 7075 and it has come out in 3 beautiful pastel color shades as well! I am sure we all agree that they would have had to get a pretty decent 'bright clear' first, in order to get close to the pastel shades launched ... agreed we may not be blessed with the huge technological reach of a corporation like Apple ... still can't help but wonder...
So are there any tips and tricks for this particular alloy, will be highly obliged if you all can share them here, for frankly I am tiring of constantly answering the same questions from too many customers, who couldn't care less about either us or our 'technical' problems :(
I also take this opportunity to wish all our dear forum members out here, a very happy 'Ganesh Chaturthi' coming up soon on the 17th of September, the annual festival of the Elephant headed God who is the god of learning, knowledge and enlightenment and also known as a remover of obstacles and problems! (Now you all know what I will be praying for this time) :)
Ravi Rao
- Belgaum, India
September 12, 2015
Hi Ravi. It would be great to know the anodizing thickness on the new iPhone 6S if an early adopter gets one and has a thickness measurement gauge. "Pastel" is another way of saying "low-saturation", so as a guess supported only by this flimsiest of evidence, I suspect that Apple's thickness is
under 10 microns [see update below].
I'm not claiming that the pretreatment answer is in Robert Probert's "Aluminum How-To" book (I don't know), but I will say that both Apple and Google bought multiple copies of that book from us :-)
Regards,
Ted Mooney, P.E. RET
Striving to live Aloha
finishing.com - Pine Beach, New Jersey
Q. Hi! Ted, Thanks! Letter no 46468 ... hmm ... is this going to be the most discussed in the anodizing forum? I wonder.
Iphone6s ... someone please test thickness and confirm coating (after the dye, even that wouldn't be accurate though.)
Ted, I think you are right, it would probably be less than 10 microns. But what surprised me is that they were confident enough to go to the consumers with color shades on this alloy, do you think the shades will be consistent enough? Will the 'rose gold' match perfectly all the time ?! If it is yes, and under 10 microns, well, OK...maybe it is not that difficult. The new plans to trade in the device after an year. along with other things, will also mean that we will not hear about the fades and patches ... am I right? Anyway we do not want this discussion to sidetrack to the new wonder device of the year :) All the best to its launch and success.
But still, an interesting alloy, and I suspect more and more applications are turning to it and we might as well take a serious re-look at what we anodisers can 'tweak' to the best of our abilities.
Ravi Rao [returning]
- Belgaum, India
Hi again Ravi. Yes, I'm trying to combine threads on similar topics instead of starting a new thread with each question for 3 reasons: short threads get no respect from Google, so nobody can find them once they're off the current forum index; the thread makes for better reference material if it includes a variety of replies and perspectives; sometimes good answers to a question have been posted already, and the questioner may want to read them and fine tune his/her questions :-)
The material is definitely 7000-series aluminum, and one cross-section microscopy I googled showed the thickness to be 10.5 micron.
Apple is quite careful; I'm confident that their colors will match. We all have a tendency to call difficult things "impossible", and the new iPhones should serve as inspiration to the rest of us that although color consistency on 7xxx is difficult, it is indeed possible.
Regards,
Ted Mooney, P.E. RET
Striving to live Aloha
finishing.com - Pine Beach, New Jersey
Q. As I scour through the numerous chats on the 7075 clear anodising and its associated difficulties, I would like to specifically point out to a problem that has been presented in this very thread just a few communications above, by Chuck from China, which also appears to have been unanswered....the dark shadow like patches are the types that I am experiencing as well although they are not as symmetrical as the ones in the pics posted by Chuck.
Have tried the proprietary deoxidiser solutions, have tried the chromic phosphoric stripping composition as a pre treatment, have tried the sulfo-chrome composition etch, have tried the alupol V composition, have once again tried the caustic-nitric and a double nitric desmut....nothing seems to help.
Of course my bath is regularly tested and is compliant with the normal Type 2 ranges for sulfuric and aluminium content.
temperature between 20-22 °C - controlled.
Titanium racks on Al-Bus Bars
Good air agitation...
Frequent DM Water rinses and double rinses...
Although I am quite sure that the shadow like patches must be material related or heat treatment or forming related,
I still need to get rid of it as it is an aesthetic requirement for the customer...
I wonder if there is anything out there...
Am also attaching some pics for all to get an idea of what I am talking about, only hope that they are clear enough as it was under tube lights and taken in the night shift.
Ravi Rao [returning]
- Belgaum, India
October 7, 2015
Prep of aluminium 7108 before anodizing
Q. Hello.
I need to anodize aluminium of 7108 quality (Al and Zn alloy).
It tends to get a powdery surface.
Anyone who have experience with this and how to solve it ?
Geir Lexau
- Norway
September 15, 2018
7136-T76511 parts Pitting
Q. When we do sulfuric acid anodising with red dye we are facing pitting problem (find our attached photo)

Our bath didn't have any chloride content.
The chemical composition of the material are,
1) Si-0-.12
2) Fe-0-.15
3) Cu-1.9-2.5
4) Mn-0-.05
5) Mg- 1.8-2.5
6) Cr-0-.05
7)Zn-8.4-9.4
8)Ti-0-.10
9)Zr-.1-.2
UMARAJ S
Employee - India
March 28, 2019
? Hi cousin Umaraj.
Based on the fact that you have given us the composition of the alloy, but no process information at all, you seem to be implying that you are confident that the problem is with this particular alloy. You are successfully anodizing other similar parts and dyeing them red? And the only problem you have is with parts made of 7136-T76511?
Regards,
Ted Mooney, P.E. RET
Striving to live Aloha
finishing.com - Pine Beach, New Jersey
Q. Dear sir,
We are facing problem only on this alloy.
Other aluminium alloys are good under same process parameters.
My suspect is the alkaline cleaner which has formulation of potassium silicate, in which zinc reacted and forms pits which are visible only after dyeing.
And other suppliers at initial stage of development faced the same problem; but now they sorted it out and didn't have such problem now. They are Denied to tell the process.
Kindly help us to rectify the problem.
Regards,
S umaraj [returning]
- Chennai, Tamil Nadu, India
March 29, 2019
Q. I am a chemist with over 30 years in Electroplating and Metal Finishing.
I am managing a new aluminium anodizing plant for parts in a Greek company. The plant is fully automated processing aluminium with electrocoloring and organic colors.
I have a request for the anodizing of 7075 alloy. I tried but the result is a dark grey to brown appearance after the anodizing tank. Thus after the electrocoloring in black color there is no actual color.
The customer insists that this can be done and is done by other anodizing shops abroad.
So, I need your advice on this. Can it be done? How ?
Thanks
ANTONY NNIKOLAIDIS
PRIVATE CONSULTING IN ELECTROPLATING AND WASTE WATER TREATMENT - VRILISSIA ATHENS, Greece
April 7, 2020
A. Hi Antony,
We have successfully anodised and black dyed 7000 series alloys for a long time. There is nothing special we do. Simple sulfuric anodise solution, operated at the usual conditions and a standard black dye, with a nickel acetate seal.
Maybe if you can describe the actual process and conditions, we might be able to spot where things can go wrong, or where you can treak your process to making the anodising more receptive to dyes.
Brian Terry
Aerospace - Yeovil, Somerset, UK
![]() |
Q. Terry thanks for the info. A. Hi Antony, |
Q. No, it is not a hard coat anodize solution. It is a common sulfuric acid solution working at 16-18 °C, with a 20% concentration of sulfuric acid. The aluminum content is about 8 gr/liter.
Anyway, I will try the organic dye as you advised.
Would you advise for any other than plain nitric acid desmutting solution?
Does the time in the caustic soda ⇦liquid caustic soda in bulk on
Amazon [affil link]
etch affect the appearance of the alloy?
If you need to have matte appearance on the part would you do it with the etching solution or with mechanical matte finishing or with no etching at all?
Thanks.
Antony Nicolaidis [returning]
- Athens , Greece
A. Hi Antony,
For desmutting, I would stick to nitric acid, this works perfectly fine.
Length of time in the caustic will affect appearance, but be careful, caustic etches aluminium aggressively and you may affect dimensional tolerances if you immerse for too long.
I use both mechanical and chemical methods for making the surface matte. You are less likely to affect dimensions with a mechanical system, however, caustic is so much easier to use for complex shapes. So, it really depends on what you are anodising for your choice of pre-treatment to obtain a matte finish.
Brian Terry
Aerospace - Yeovil, Somerset, UK
Q. What can cause Aluminum surface erosion?
We doing type 2B SAA on Aluminum 7000 series.
After anodizing process, we found one of the holes has erosion. But the surfaces are well coated.
We not using the holes for any jigging or contact point.
Amer Anaqi
- Penang Malaysia
August 21, 2020
A. 1. Is it work hardening around the hold from a dull cutting tool?
2. Is it gas evolution from behind/thru the hole?
Robert H Probert
Robert H Probert Technical Services
Garner, North Carolina
A. Amer
It looks like an oversized bore was sleeved with something other than aluminum as a repair.
Willie Alexander
- Green Mountain Falls, Colorado
I think you win, Willie :-)
It never would have occurred to me, but that's sure what it looks like now that you've said so :-)
Luck & Regards,
Ted Mooney, P.E. RET
Striving to live Aloha
finishing.com - Pine Beach, New Jersey
Q. Hi Willie,
Thanks for the explanation.
If the current flow not good, would the hole may be impact? due to burn?
Amer Anaqi [returning]
- Penang Malaysia
A. Hi. I think Willie is saying (if his guess is right, and I think it is) that the material at that hole is not aluminum, so it cannot be properly anodized; the defect is not your fault, and it was not within your power or anyone's power to anodize it correctly.
Luck & Regards,
Ted Mooney, P.E. RET
Striving to live Aloha
finishing.com - Pine Beach, New Jersey
Q. Stains in anodized A7075 valve plunger
We are manufacturing different valve plungers made with A7075. The typical dimensions are D. 10x L.50.
After the anodizing we found dark grey stains over the cylindrical diameter d.50. The stains are like spots of 1-2 mm.
Could it be from copper oxidation ?
Or could it be from zinc segregations ?
Must we take care with the anodizing process?
P.S. The stains appears in the diameter d. 10 mm of the plunger d. 10 x l. 50 mm.
Imanol Ibarra
- Andoain Gipuzkoa Spain
December 18, 2020
Q. I was anodizing 7075 al. Alloy and the work piece severely eroded.. an erosion happened the piece lost 3 grams from its weight from the whole dimension of the piece .. any solution for this problem and what should I check first
Shaymaa ahmed
- Cairo/ egypt
April 1, 2021
Q. Hi, I'm from Argentina and I'm trying to anodize some sprockets made of 7075 T6 Aluminium for cometic purpose. The process that I'm doing is:
1. Machining the sprocket.
2. Clean with degreaser (I have a ultrasound that I could use but I haven't implemented it yet.
3. Immerse the sprocket in caustic soda ⇦liquid caustic soda in bulk on
Amazon [affil link]
(18%) until it takes a dark color all over the piece (if i don't do this the color after the anodizing is not uniform)
4. Immerse the piece in hydrochloric acid (20%) 10 second
5. Anodize in sulfuric acid (18%), for a sprocket of 7 Dm2 I use 10 Amp 18 Volt for 120 minutes at 18 °C, Use cathode of aluminium double the size of the sprocket. I don't use agitation (I need help with this too)
between steps I clean with water.
6. Put the sprocket in aniline for cloth 30 min at 50 °C
7. Put the piece in boiling water for 10 minutes.
Julio Vacca
- Buenos Aires - Argentina
July 29, 2021
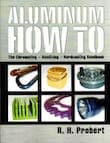
Aluminum How-To
"Chromating - Anodizing - Hardcoating"
by Robert Probert
Also available in Spanish
You'll love this book. Finishing.com has sold almost a thousand copies without a single return request :-)
A. Hi cousin Julio. I don't know if you're a hobbyist with a one-time interest to anodize your bicycle parts, or if you're trying to run a professional anodizing service. So I don't know what you have access to, and what you can afford. But the inconsistencies are the result of compromises -- not doing things quite right in numerous places -- so there is probably no single thing you can change which will give you consistency :-(
3. This step is probably okay, but should be done for a fixed amount of time and at a fixed temperature.
4. HCl is not a proper desmut/deox chemical.
5. 18% sounds too high. Can we assume you mix this from electronic grade rather than using battery acid ⇦ on eBay or Amazon [affil links] ? Is 7 dm2 the surface area of one side or both sides put together? Can we assume that you slowly ramp up to 18 volts? 120 minutes sounds terribly long. 20 °C would be better. Good agitation either with a pump or air is absolutely necessary. The parts will get warm from the electrical power without it and anodize inconsistently.
6. Fabric dye is somewhat similar to anodizing dye, but not the same thing.
7. If you are anodizing for 120 minutes, then 10 minutes of sealing is not even half enough.
I think you need to see a good anodizing book, and your national library has at least one. Good luck!
Regards,
Ted Mooney, P.E. RET
Striving to live Aloha
finishing.com - Pine Beach, New Jersey
A. Hi Julio
it would be to your benefit to use a more standard etch time rather than to etch until ... this may be the very source of your splotchy appearance. 7075 tends to freckle as etch time is increased. 7075 material can be etched for 10 seconds maximum to stay away from the splotchy appearance that you are referring to. There is normally no freckling appearance with a light etch. Also I have to agree, anodizing at 18% seems rather high. 14% seems much more sane.
One more thought... all is not lost. The freckling can normally be removed with a scotch brite pad or steel wool. Light to moderate pressure is all that is required while rubbing the part.
Philip J. Verzal
supervisor - Cicero, Illinois
Saporito Finishing Co.
Q. Hi. I am trying to start a motorcycle accessories manufacturing venture and I wanted to do the anodizing on my own. I am willing to make the necessary investment to obtain the expected results, here in Argentina it is not so easy to get some things but we are looking for it, so any suggestion will be welcome
2. OK one thing I have to improve is that
3. OK
4. What do you recommend? Nitric acid is hard to get here
5. i use battery acid
⇦ on
eBay
or
Amazon [affil links]
;
7 DM2 is the total area.
I'm not ramping voltage
With less time I don't have better results.
I'm going to put in some agitation....
P.S.: Etch time is the time in the time in caustic soda ⇦liquid caustic soda in bulk on
Amazon [affil link]
right?
P.P.S.: I almost forgot: I already requested a book in the library, but it's closed for covid :-(
Julio Vacca [returning]
- Buenos Aires - Argentina
August 9, 2021
(affil links)
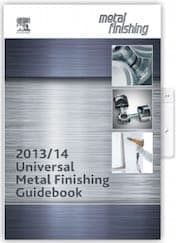
free pdf is currently available from academia.edu
A. Hi again Julio.
4. Robert Probert knows a lot more about anodizing than I do, and his book seems to suggest that proprietary tri-acid salts are the thing to use if you can get them.
5. Battery acid is not ideal because it may contain contaminants including lead; see if you can get any specs on it.
Since you're treating 7 DM2 with a 10-Amp rectifier, the available current density is 1.43 A/dm2 or 13.3 ASF, and that's okay. Depending on your rectifier you may not strictly need 'ramp control'; if your rectifier cannot and will not exceed the amperage rating you set, that will suffice, because what you're trying to avoid is current gone wild when the aluminum is bare, causing burning.
Sometimes the cleaner tank is largely caustic soda ⇦liquid caustic soda in bulk on Amazon [affil link] , but it's not a great idea to try to use a single tank as both the cleaner and the caustic etch.
While you are waiting to get the library book you're seeking, you can consult the anodizing chapter of the Metal Finishing Guidebook, available online.
Luck & Regards,
Ted Mooney, P.E. RET
Striving to live Aloha
finishing.com - Pine Beach, New Jersey
A. Almost everything you are doing is incorrect, let us start here:
1- Parts must be waterbreak-free cleaned
2- 7000 series is loaded with zinc so only etch for a short time 1-2 min
3- HCl is not a good de-oxidizer, switch to nitric or a proprietary tri-acid.
4- ASF should be 20-24 ASF and for around 60 min
Drew Nosti, CEF
Anodize USA
Ladson, South Carolina
November 29, 2021
A. Hi Julio,
By using HCl in your process you are introducing a chemical that is a well known antagonist to good anodizing results. Any amount of chloride dragged into the anodizing bath is going to be detrimental. Even the amount left in city supplied drinking water is often too much! A normal desmut of sulfuric and nitric acid with a bit of ferric sulphate is better, but of course you still need to minimize dragthrough.
You should not have chloride in your process at all. If you can test your anodize tank for contamination, it should be under 10ppm free chloride for ideal results. Its possible it can be higher and still work, and hopefully someone more experienced can give an upper limit, but I only know what I hold to aerospace spec for a dual use Al/Ti tank, and it's 10. But please choose a different desmut solution.
Rachel Mackintosh
lab rat - Greenfield, Vermont
December 28, 2021
A. The above from Mr Mooney covers all but one other possibility. Electrical contact reliability influences thickness and color.
Contact must be "tight" and "wide enough to deliver the current".
Robert H Probert
Robert H Probert Technical Services
Garner, North Carolina
December 29, 2021
Q, A, or Comment on THIS thread -or- Start a NEW Thread