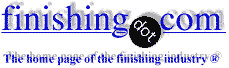
-----
Sizing calculations for a electroplating line
May 8, 2017
Q. Hello,
I am a student of industrial engineering, and I am developing a project about sizing an electroplating line. But I have never done anything like that. I have questions about how to do the calculations.
I am going to raise the doubts that have arisen for now and I hope you can answer me.
1- How to calculate the electric volume. I have read that a liter / amp ratio is used. But I do not find any information about it.
2- How to calculate the surface of the anodes. I have read that an anode / cathode ratio of 1: 1 is often used, although sometimes they vary but would require all the relationships or a theoretical form of calculation. For example with amperage.
If you have any questions because you do not understand me, ask me.
If you have a good book on the dimensioning of this type of lines, or some example on the subject would be of great help to me.
Thank you.
- France
May 2017
A. Hi Xavier. Happy to try to help! But to keep things in perspective, after graduating from engineering college I worked for 15 years for 3 different plating equipment suppliers before I considered myself competent to offer to serve as a consultant advising people how to size and design plating lines. So if this is a student learning exercise, it's great; but if you're actually trying to design a real plating line as an intern with no experience, not so much :-)
The first thing you need is a laboratory-proven sequence of operation for the parts you will be plating, and the plating process you will be applying. From this you'll know the sequence of operation (cleaning, acid activation, plating parameters, post treatment steps, immersion time in each tank, etc.)
The next question is whether the parts will be plated in continuous strip form (as used in electrogalvanizing of sheet metal, and the selective plating of metal frames of electronic integrated circuits); or in plating barrels (as frequently used for nut, bolts, and small stampings); or as discrete, individually racked, components. Sometimes the plating process affects that choice (it may be relatively easy to zinc plate nuts & bolts in a barrel, but nearly impossible to chrome plate them that way, for example).
But assuming that this is an exercise, let's assume that the components are individually racked. Then you can go to "The Electroplating Engineering Handbook".
and review the "Design, Installation, and Maintenance of Plating Racks" chapter because, in truth, almost all of the time, the size and shape of the plating rack, rather than "liter/amp ratio" is what determines the size of the tanks and everything else.
It will go something like this: you start with the number of parts you need to plate in an hour, and divide by "about 10", and that's how many loads of parts you need to plate per hour, with each load consisting of 1/10 of the hourly production need. This "about 10" number arises because 20 loads or more per hour will be too many loads to handle, too much running around, too short a rack loading time, too little immersion time in too many tanks, etc. Whereas a production rate of less than about 5 loads per hour will usually not be economically feasible because the process tanks will be empty too much of the time. (Again this is just a starting rule of thumb for most processes, not applicable to some processes and some types of plating lines, and subject to other factors). And while there are also "rules" for anode sizing, the usual practice is simply anode rods, the full width of the tanks, on both sides of the plating racks (as you will see in that textbook).
Another book which is very helpful in understanding plating equipment, and which includes many illustrations, is "The Canning Handbook". Good luck.
Regards,
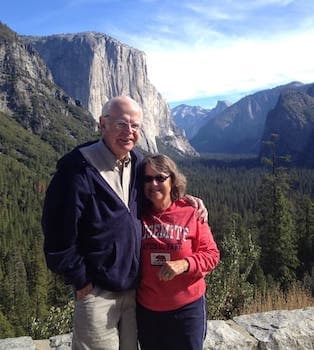
Ted Mooney, P.E. RET
Striving to live Aloha
(Ted can offer longterm or instant help)
finishing.com - Pine Beach, New Jersey
Q. Thank you very much for your response and help.
It is a project, which in theory should work in reality. But as you have said and as I have been informed it is very difficult that with the knowledge I have acquired to fully develop it.
I have the phases of the lines and cleaning already thought and raised, theoretical times and maximums necessary in electrochemical baths, washing, activation ... But there are certain calculations like the ones I have exposed that do not make them.
The project would be developed for small pieces that should go in baskets and for a production of 60-80 kilograms per hour.
Thanks again, and sorry for my English if you do not understand me.
- Bordeaux, France
May 9, 2017
A. Hi again Xavier. In the plating industry, we use the word "plating barrel" rather than "basket" because it is constantly rotated during the process. Please see our library article "An Introduction to Barrel Plating" for pictures and a quick understanding.
The same principle of "about 10" loads per hour applies to barrel plating lines, but maybe a bit less because plating barrels drag out so much more waste water than plating racks that it is good to allow more draining time ... so you could pick a plating barrel designed for handling a load size of, say, about 10 kilograms. If you google "plating barrels" you will find some vendors and you will be able to download their catalogs, and choose a plating barrel size. Good luck.
I agree that your project should be as realistic as possible. But when a student starts medical school, they don't get to operate on people, nor should engineering interns design real plating lines :-)
Regards,
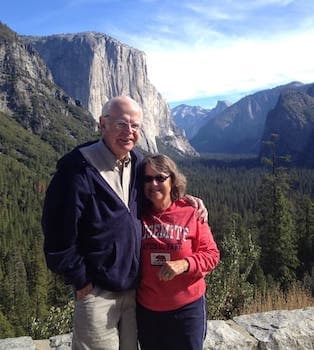
Ted Mooney, P.E. RET
Striving to live Aloha
(Ted can offer longterm or instant help)
finishing.com - Pine Beach, New Jersey
May 2017
Q, A, or Comment on THIS thread -or- Start a NEW Thread