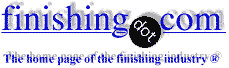
-----
Pretreatment required before Alodine (Chem-Film on Aluminum)
Q. I am designing some aluminum parts for a pulsed power device. The parts will conduct a very large but short duration current pulse. I am considering having the plates Alodine treated after machining. First, I want to make sure I specify the most conductive version of Alodine. I believe that would be Type 1 Class 3.
My main question is how best to pre-treat the metal parts before the chromate conversion. My ideas are:
1. Some type of chemical etch
2. Glass bead blasting
If a chemical etch would be best, how do I specify that process? This is for Aluminum.
- Livermore, California USA
February 24, 2017
Ed. note: This RFQ is outdated, but technical replies are welcome, and readers are encouraged to post their own RFQs. But no public commercial suggestions please ( huh? why?).
(to help readers better understand the Q&A's)
When processing aluminum alloy components, the chromating or anodizing process only reacts with the aluminum, so it is generally necessary to "de-smut" or strip away any copper, silicon, or other alloying materials from the surface.
The need for this de-smutting step is more acute if any etching is being done because the caustic etch will dissolve aluminum while leaving behind those contaminating materials.
A. Hi Mark. Although an acidic bifluoride etch may be possible, alkaline etching is much more common. If you're only making a few pieces you can probably do the process in a sink without a bunch of tanks, but for a production situation you need a tank for each step in the process, and there's more to it than etch => conversion coat. A fairly typical processing sequence would be:
Non-etch soak clean => rinse => alkaline etching (strong caustic soda ⇦liquid caustic soda in bulk on Amazon [affil link] ) => rinse => rinse => de-smut* => rinse => rinse => chromate conversion coat => rinse => rinse.
* The de-smut step is probably the most variable one as it will depend on what alloy you are processing (whether you need to remove copper, silicon, or whatever) and what environmental pressures your shop is feeling (no chromates, no nitric acid, or whatever). The vendor of the chromate conversion coating process can probably advise on the cleaner, etch, and de-smut.
Regards,
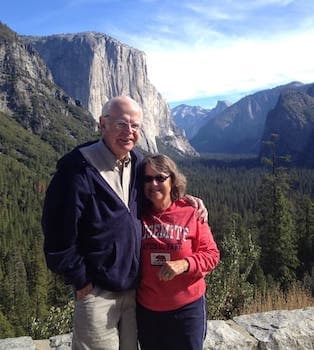
Ted Mooney, P.E. RET
Striving to live Aloha
(Ted can offer longterm or instant help)
finishing.com - Pine Beach, New Jersey
February 2017
Q. Thanks for the reply. We won't be doing anything in the sink. We will be choosing a commercial outfit to do the cleaning and chromating as a complete process. I have since talked to some vendors. It has been suggested that we skip the caustic etch and only do the "deox" step otherwise the finish can look blotchy.
I am still looking for input on best electrical conductivity. It has been suggested that Type 1 Class 3 Clear has better conductivity than Type 1 Class 3 Yellow as there is less Chromate with the clear version. This is consistent with another post here that suggested "less time in the tank" gives better electrical performance. I have searched but have not found any actual data comparing Clear to Yellow assuming Type 1 Class 3.
- Livermore, California USA
February 24, 2017
A. Hi Mark. If a product has been qualified for Type 1 Class 3, it successfully chromate conversion coats while keeping the resistance within spec. Hexavalent chromium is yellow, so it would seem to me as well that the fainter the color the lower the resistance. But unless you find a vendor with a proven claim or you actually conduct tests, I think it remains just an educated guess. Good luck.
Regards,
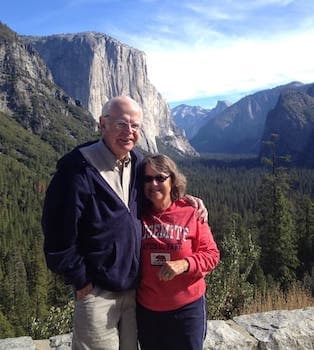
Ted Mooney, P.E. RET
Striving to live Aloha
(Ted can offer longterm or instant help)
finishing.com - Pine Beach, New Jersey
Q, A, or Comment on THIS thread -or- Start a NEW Thread