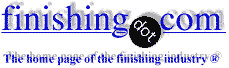
-----
Current density in barrel plating
Q. Hi, I plan to electroplate some spherical parts using a small barrel plater. Presently, I am checking the impact of bath temperature and current density by plating experiments with some flat sheets of the material. For the flat sheets, I have a well defined area, so I can find the combination of temperature and current density that gives an acceptable coating. However, when I barrel plate, I can calculate the area of the parts in the barrel, but I am not convinced that the optimal current density for a flat plate will be the same for barrel plating. In the experiments with flat plates, to a first approximation, all the area is equal, but this may not be the case in the barrel. Is there a factor used in industry to convert current densities for tank plating to current densities for barrel plating? Or to put it another way, is there a factor that converts tank plating and barrel plating current efficiencies? Or is this a part of the black art of electroplating.
Regards
David
Engineer - Porsgrunn, Telemark, Norway
March 21, 2016
A. Hi David. Sometimes it does seem like a small miracle that barrel plating can work at all, what with some parts touching each other and conveying electricity from one to the next to the next, rather like children playing tag and offering "electricity" from home base. And some parts on the surface of the jumble at a given time, and some buried in the middle of the pile.
Based on the calculated area of the parts, the current density for barrel plating is as low as 1/10 the current density for rack plating, but the explanation of the matter is probably not that successful bright plating can be done at 1/10 of the normal current density, but rather that only 10% or so of the surface area of the parts is on the outside of the jumble and being plated at any given time.
Regards,
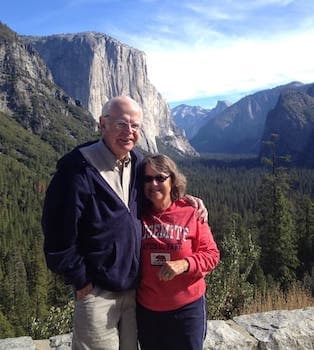
Ted Mooney, P.E. RET
Striving to live Aloha
(Ted can offer longterm or instant help)
finishing.com - Pine Beach, New Jersey
March 2016
![]() |
A. Hello, just a quick addition to Ted's comment. In barrel plating you are relying on solution transfer in and out of the barrel. Because there is only a limited amount of solution present in the barrel at a given time, fresh metal ions are not replaced fast enough to plate at the same current density as let's say rack plating, or in this case, plating a flat sheet. Good luck with your venture. Mark BakerProcess Engineering - Phoenix, Arizona USA March 21, 2016 Q. Hi Ted, thanks for your quick response. If I was tank plating with a current density of 0,02 A/cm2. To get a similar surface finish in a barrel plater, do I keep the same current density, but plate for a longer period (factor of 10 or otherwise), or do I reduce the current density (by a factor of 10 or otherwise) and plate for much longer? I have an XRF analyser in the same lab, so when barrel plating, I can measure depletion of my plating metal in the bath pretty much in real time. I guess I could use this to determine plating rate? David Waller [returning]- Porsgrunn, telemark, Norway March 22, 2016 |
A. Hi again David. In the interim, Mark has reminded us of something that can be a limiting factor on barrel plating current. So it's a bit of Mark's limit and a bit of my claim that only a portion of the work is exposed for plating at any given time, that accounts for barrel plating current densities often being down as low as 1/10 of rack plating current density. But it would be next to impossible to say what percentage of the surface of the parts is actually being plated at a given time anyway, some at high current density and some nooks & crannies at various lower levels of current density. If you are rack plating at 0.02 A/cm2 (18.6 A/ft2), yes, you'll probably be barrel plating at something like 1/4 to 1/10 of that depending on part size and barrel size, etc., and you'll probably be plating for several times as long -- all calculations tempered by Faraday's Law of Electrolysis that 96,485 Ampere-seconds will deposit one equivalent weight at 100% efficiency. Can you tell us what metal the spheres are made of, and what metal you're trying to electrodeposit on them, and how thick, and what size the barrels are? -- because although electroplating is not a 'black art', a lot of the science is based on empirical findings rather than being derivable from first principles.
Regards,
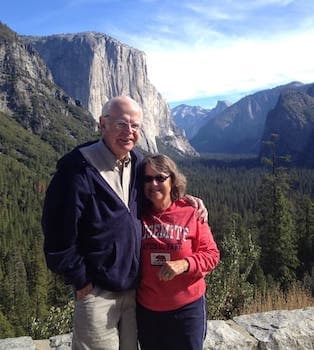
Ted Mooney, P.E. RET
Striving to live Aloha
(Ted can offer longterm or instant help)
finishing.com - Pine Beach, New Jersey
March 2016
![]() |
Q. Hi Ted, the barrel plater is a small one from Sterling plating. The total barrel volume is about 1.5 L, with mesh walls. The parts have a nickel plated surface. I aim to deposit a functional layer of circa 10 microns (0.01 mm) of a platinum group metal. This will be an expensive experiment. Regards, David David Waller [returning]Yara - Porsgrunn, Telemark, norway March 23, 2016 A. Good day David. Aerotek Mfg. Ltd. - Whitby, Ontario, Canada March 23, 2016 |
A. Hi David. I don't know whether you can get help in your area from Technic or DeGussa or another vendor of precious metal plating processes, but they may have a plating development lab that can run test parts for you to reduce the time and cost of the development cycle.
Regards,
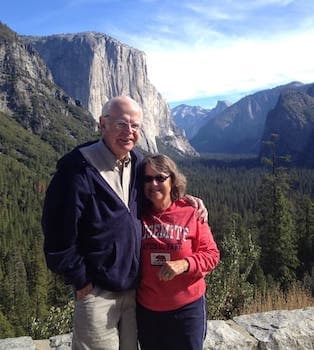
Ted Mooney, P.E. RET
Striving to live Aloha
(Ted can offer longterm or instant help)
finishing.com - Pine Beach, New Jersey
March 2016
Q, A, or Comment on THIS thread -or- Start a NEW Thread