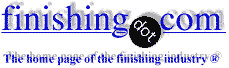
-----
Effects of bath contamination in tin plating, limits for metallic impurities?

this text gets replaced with bannerText
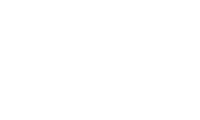
⇦ Tip: Readers want to learn from your situation;
so some readers skip abstract questions.
Q. Hi all,
For a lead free tin electroplating, I would like to know the maximum level of impurities (ppm) for the following metals:
Nickel
Copper
Iron
Thank you,
Process engineer - Israel June 9, 2016
A. Hi Dana. The usual source for that info is the technical data sheet offered by the supplier of the particular tin plating solution you are using. If that is not available for some reason, you might be interested in this quote from F.A. Lowenheim in the Garden State Branch American Electroplaters Society 'Electroplating Course Manual':
But electroplating is complex and 'general' questions usually aren't answerable. In this case the answer de pends on whether you are running an acid, MSA or stannate process; they're quite different. Are you doing rarrel, rack, or continuous plating? CRS substrate or something else? Any under-layers of other plating? Please carefully detail your situation and the readers can probably help. Thanks and good luck.
Regards,
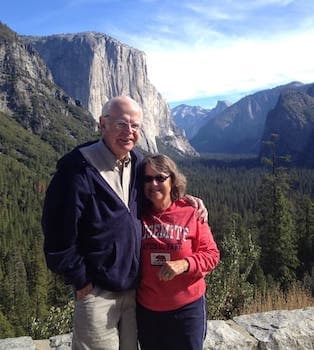
Ted Mooney, P.E. RET
Striving to live Aloha
(Ted can offer longterm or instant help)
finishing.com - Pine Beach, New Jersey
Q. Hi Ted,
Thank you for your reply.
The information offered by the supplier is not available.
Metallic impurities have an effect on the wetting properties of solder.
Our process is:
*MSA
*rack plating
*no under layers, no other plating (just lead-free tin electroplating)
Thank you,
- Israel June 13, 2016
A. Control Limits:
Fe <200 ppm
Ni <200 ppm
Cu <25 ppm
- Hermosillo, Son, MX
June 27, 2023
Q, A, or Comment on THIS thread -or- Start a NEW Thread