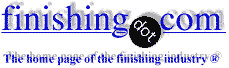
-----
Designing a Nickel Manganese Phosphating installation
July 17, 2013
Q. Hi there,
We are trying to set up manganese nickel phosphate line. We are getting good help from Chemetall rep.
1) Can we use poly tanks?
2) Any formula for minimum volume of chemical liquid so that it does not lose its potency after two immersions?
3) Where can we source SS tanks?
4) What type of heaters should we use and how to figure the number and size of heaters please?
Thank you very much
- Calgary Alberta Canada
A. Hi Gil.
1). Polypropylene tanks are good to about 180 °F; polyethylene to about 140 °F. I suspect the operating temperature of your proprietary bath may exceed that.
2). The Chemetall or other technical data sheet may have a recommendation on square foot of work per gallon. But it would be quite unusual to be able to fit enough work in a tank to radically affect the concentration with one or two loads. And what that means in turn is that, rather than building large tanks as solution reservoirs, you can use the generally superior approach of "bleed & feed" (a squirt of replenishing solution every so many loads or so many square feet). This gives you consistent processing load after load, rather than processing with gradually diminishing performance until a dump proves necessary.
3). For stainless tanks please see our Equipment Directory, or ask you chemical supplier, or get a suggestion from another phosphatizing shop, or consult the Metal Finishing Guidebook or the Products Finishing Directory. Sorry, we can't suggest sourcing in this forum.
4). Steam or hot water heat is much more cost effective than electrical. Stainless steel heaters should be fine. It is possible to do rather exacting calculations based on evaporative losses, wall losses, losses to cold work entering the tank, etc. And such calculations are increasingly important when operating temperatures approach the boiling point. But the easier approximation is to simply figure that the BTU's/hr equals the pounds of process solution times the temperature rise from ambient to operating temperature in °F divided by the heat up time. You will be close enough to boiling temperature that you should figure on 2-3 hour heat up time, as the operating losses will exceed the heat up losses if you go for a long heat up time. Good luck!
Regards,
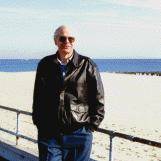
Ted Mooney, P.E.
Striving to live Aloha
(Ted is available for instant or longterm help)
finishing.com - Pine Beach, New Jersey
July 17, 2013
Q, A, or Comment on THIS thread -or- Start a NEW Thread