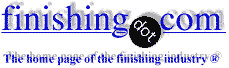
-----
Hardcoat vs. regular anodize of aluminum
Q. I need to know the difference between Regular anodizing vs. Hardcoat anodizing. Are the chemicals interchangeable, etc.?
Thank you.
Gary W. Schooley1997
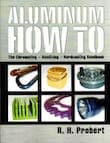
Aluminum How-To
"Chromating - Anodizing - Hardcoating"
by Robert Probert
Also available in Spanish
You'll love this book. Finishing.com has sold almost a thousand copies without a single return request :-)
A. Hi Gary. In anodizing, DC electricity converts the aluminum metal on the surface of the part to non-conductive aluminum oxide; simultaneously the acid in the electrolyte is dissolving the coating. The process is thus self-limiting -- because the oxide impedes current flow and when it reaches a certain thickness the current flow cannot build a coating any faster than the acid dissolves it.
So, in simplest terms, hard anodizing involves a higher voltage rectifier and lower temperatures (of about 28 °F rather than 68 °F) which allows more current to flow for a heavier build, while reducing the acid attack on the coating.
They both employ sulfuric acid of about 10 to 12 percent concentration by volume.
There can be proprietary extra ingredients that are added and which purportedly build a better coating or allow the hard coat process to operate at higher temperatures. Generally hardcoat is considered to be 0.002" thick whereas "regular" anodizing would usually be between a tenth and a third of that.
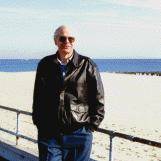
Ted Mooney, P.E.
Striving to live Aloha
finishing.com - Pine Beach, New Jersey
A. I have 30 years of experience in anodizing and I have found 16-18% Sulfuric concentration works best.
Raymond HendrixTroy, Tennessee
1998
Thanks, Raymond, I'm sure you're correct. My 10-12 percent, while perhaps approximately correct by volume, was not really the correct answer, and I appreciate your catching the error. Some published values in the reference books include, by weight, 15 percent and 185 g/l.
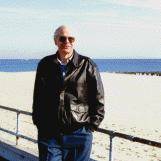
Ted Mooney, P.E.
Striving to live Aloha
finishing.com - Pine Beach, New Jersey
1998
Q. You mentioned additives that allow hard coat to be run at higher temperatures. What are they, where do you get them, and how high a temperature will they let you run at? Is any other special equipment needed?
Terry BurgessConsolidated Metal Technologies
1998
Treatment &
Finishing of
Aluminium and
Its Alloys"
by Wernick, Pinner
& Sheasby
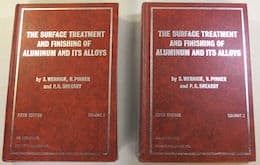
on eBay or Amazon
or AbeBooks
(affil link)
A. Terry,
There are several companies that offer an additive. Check out the list in the Metal Finishing Guidebook or similar reference. It does take a higher voltage and it does not produce a true hardcoat, but one with some of the properties such as a little less hardness, a little less wear. In some cases this will suffice for real hardcoat.
Most allow you to "hardcoat" in the 45 °F range vs. 32 °F. Some are higher.
James Watts- Navarre, Florida
1998
A. Hi Terry. These additives may involve glycolic and/or oxalic acid but, as James says, they're usually offered as proprietary additives rather than purchased as commodity chemicals. As James notes on another posting, these pseudo hardcoats, operating at a temperature in between MIL-A-8625 / MIL-PRF-8625 [⇦ this spec on DLA] Type 2 and Type 3 coatings are sometimes facetiously called Type 2-1/2 :-)
Regards,
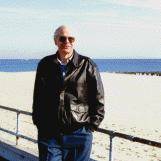
Ted Mooney, P.E.
Striving to live Aloha
finishing.com - Pine Beach, New Jersey
Q. Dear Sirs :
We are about to initiate an important aluminum operation in Peru (South America) and the only missing piece in our project is the anodizing plant. We haven't being able to contact directly manufacturers of these plants or second hand sellers and we would highly appreciate if you could recommend us where to turn for this information.
As extra information, we would be processing 300 tons a month.
Thank you in advance for your help.
- Peru
1998
A. Dear Manuel Tirado C.
In our Equipment Directory at www.finishing.com/equipment you will see some suppliers listed. You may also wish to consider to retaining an anodizing consultant if you don't have significant in-house experience. Good luck.
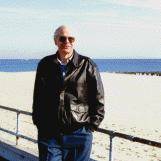
Ted Mooney, P.E.
Striving to live Aloha
finishing.com - Pine Beach, New Jersey
1998
Multiple threads merged: please forgive chronology errors and repetition 🙂
Q. I am currently in a debate with a customer who insists our product supplied to him needs to be hard anodized. I do not think the environment (outdoor marine/saltwater) surrounding his part suggests using a hard anodize - I think a sulfuric anodize is sufficient.
Can you provide me with technical data or anything else to convince my customer that a sulfuric anodize will stand up to the marine environment. Or if I am wrong, can you explain to me why a hard anodize would be preferred?
Kevin Hess- Dayton, Ohio, USA
2000
TUTORIAL
for readers trying to learn from these discussions, but needing a bit of intro first --
Conventional anodizing of aluminum involves immersing the parts into a bath of dilute sulfuric acid and subjecting them to anodic current, which converts some of the aluminum on the surface to aluminum oxide/hydroxide/boehmite. This surface is hard, non-conductive, attractive, semi-transparent, & corrosion resistant, and includes millions of small open "pores" that look like miniature drill holes extending almost down to the aluminum surface. After anodizing, the component is often dipped into a dye tank so the pores can absorb colorful dyes, and then into a "seal" tank of boiling hot water or other liquid which swells the anodizing to close off the pores and seal in the dye (and seal out dirt).
"Hard anodizing" or "hardcoat anodizing" or "hardcoating" is essentially the same process, but involves lower bath temperature, higher voltage, and longer immersion times to build a much thicker anodized layer. Because wear-resistance is often critical, hardcoating is usually not "sealed" because that would somewhat soften the surface.
Mil spec MIL-A-8625 is often used to specify anodizing and mentions three types: Type 1 (a somewhat different process utilizing chromic acid instead of sulfuric), Type 2 ('conventional' sulfuric acid anodizing), and Type 3 (hardcoating).
Organic dyes are usually used for coloring, but are subject to fading; Marc makes an allusion to 'electrolytic coloring' whereby inorganic salts are used to deposit metals in the pores to impart more fade resistance.
A. Kevin.
I agree with you, a well sealed Type 2 coating should be sufficient. I would suggest sending a sample of your work out for salt spray testing, and assuming you pass the Mil Spec, show your customer the results. Sealing is the key here. Your parts must be well sealed to stand up to constant salt spray and sunlight,; and even then, after a long period of time, your parts may eventually fade. It sounds like the best coating would be electrolytic coloring. I'm sure there are others in here that are more knowledgable on that process than myself.
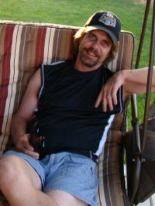
Marc Green
anodizer - Boise, Idaho
2000
A. Reporting from the International Hard Anodizers Association's Technical Symposium in Barcelona, Spain.
Hard coating is a thicker, denser version of commercial sulfuric anodizing. It is better in wear, corrosion, and insulation protection. If you want maximum protection it should be specified. However, the added costs should be considered. Regular anodize is used successfully in a lot of applications.
Chris Jurey, Past-President IHAALuke Engineering & Mfg. Co. Inc.

Wadsworth, Ohio
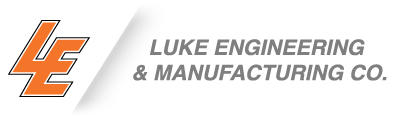
2000
Multiple threads merged: please forgive chronology errors and repetition 🙂
Hard Type II Anodizing?
January 3, 2008Q. Hi All,
Love these forums as getting the experts opinions helps greatly.
I have a handle that is 6061-T651 with a specification of "Hard Anodize per MIL-A-8625 / MIL-PRF-8625
[⇦ this spec on DLA] Type II, Class 2, Nickel Acetate Seal."
I'm looking to compare type II and type III finishes for wear resistance.
Questions
1. Is there a Type II anodize that is Hard and Not Hard? I thought I had seen references to 1 mil oxide being Type II and 4 mil oxide being a Hard Type II. Or is the finish specification just written wrong?
2. If there is a difference between Hard and Not Hard, how would a hard coating compare to a Type III Coating.
3. If you had a part with a Type II finish and really needed a Type III is there a way to update the Type II to a Type III finish?
Thanks in advance for the info!
Medical Industry - Lawrence, Massachusetts
A. Type II is conventional room temperature sulfuric anodize and in is never referred to as "hard anodize." Type III is also done in a sulfuric acid electrolyte, however, it usually involved lower temperature, a bath additive to inhibit dissolution of the aluminum oxide back into the sulfuric acid, and/or higher current density and voltage. The result is a HARDER, DENSER (and thicker) oxide layer for Type III coatings. My guess would be that someone made an error in calling out Type II.

Milt Stevenson, Jr.
Syracuse, New York
January 4, 2008
A. Milt is 100% accurate, as he comes from a leading high reliability anodizing shop that would never call Type II "hardcoat". That said, in the real world of all sorts of job shops, there is no fine line definition between Hard coat and soft coat. The Mil Spec says 0.002 inch "unless otherwise specified". Picatinny Arsenal has some purchase orders out calling hard coat: 0.001" thick, dyed, and sealed. The Mil Spec does not even mention "hardness" - they talk about abrasion resistance. Hardness, which is pore size, varies with temperature, concentration, and current density, and OH, alloy too. Five shops in the same Florida county will give you five different pore sizes, five different colors, and five different thicknesses.
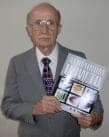
Robert H Probert
Robert H Probert Technical Services

Garner, North Carolina
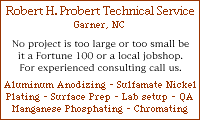
January 7, 2008
A. I typically see this mistake on many customers callouts every year, describe to your anodizer the nature of the application (what is the part application) and decide whether or not a functional, or a decorative finish is desired.
If the anodizing is for part identification, maybe type 2 is appropriate, if the coating is intended to provide wear resistance, or corrosion resistance, type 3 would be more appropriate.
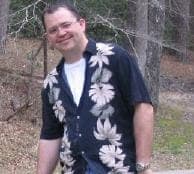
Ryan Cook
Toccoa, Georgia
January 12, 2008
Thanks Ryan. Your posting is right on, but offers an opportunity to present an example of Robert's about dyeing & sealing "hardcoat". To clearly distinguish between live rounds and dummy rounds, a military installation might want to dye them different colors and seal them even when the thickness of anodizing they require & specify exceeds Type II anodizing.
Luck & Regards,
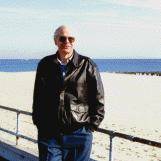
Ted Mooney, P.E.
Striving to live Aloha
finishing.com - Pine Beach, New Jersey
on AbeBooks
(rarely avail.)
or Amazon
(rarely avail.)
(affil link)
Q. Chris,
You stated above the following: "Hard coating ... is better in wear, corrosion, and insulation protection."
The literature I have found agrees that hard coat is definitely harder and more insulating than conventional anodizing.
However, I am having a hard time verifying the assertion that hard coat is more corrosion resistant than conventional anodizing with any published studies that I can find.
I assume that the required testing would need to control two of the three factors that Brace.
lists as influencing corrosion resistance (aluminum alloy and sealing quality). The third factor of film thickness would obviously vary between the groups.
Do you (or anyone else) know of a study/reference that addresses the relative corrosion resistance of conventional vs. hard coat anodizing given the groups are of the same alloy and seal quality?
Thanks in advance for your help!
- Alexandria, Minnesota, USA
A. Hi Mike. Just to minimize crosstalk and make sure that we are all using the same language and understandings in discussing your question, are we conceding that the most basic difference between conventional anodizing and hardcoating is the thickness? (Hardcoating being approx. .002" thick, whereas conventional anodizing might range from perhaps .0002" for many uses through maybe .0007" for architectural use). In other words, hardcoating is about 3 to 10 times as thick as conventional anodizing.
Please try to tell us what you are up to, as people & their problems are interesting, but dry & abstract discussions about parameters aren't much fun. Thanks!
Regards,
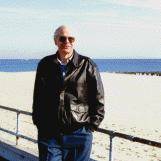
Ted Mooney, P.E.
Striving to live Aloha
finishing.com - Pine Beach, New Jersey
November 2013
November 8, 2013
Q. Ted,
You had stated above, the following question: "are we conceding that the most basic difference between conventional anodizing and hardcoating is the thickness?"
Yes, I agree with that.
Per your request, the back story is as follows:
I have a customer that currently contracts our finishing operation for anodizing services. The substrate is usually a 6000 series and the thicknesses are usually in the 0.0004" - 0.0007" range of sulfuric acid anodizing and sealed in nickel acetate based sealer.
That customer is looking to improve the corrosion resistance of these parts.
They would believe that the thicker nature of the hard coat (and yes, it would be sealed) would yield better performance against corrosion.
My basic question above was trying to address if this customer could justify the extra expense of hard coat vs type II anodizing by knowing that the parts would better resist corrosion.
I know that at thin deposits of 0.0002" - 0.0004", the corrosion resistance is not very good. But at thicknesses of 0.0004" - 0.0007" (which we are normally at due to the parts being dyed), I understand that the corrosion resistance is better.
The $64,000 question is would a hard coated and sealed part do significantly better than a type II anodized and dyed part anodized to 0.0006" thick?
I am mostly interested in finding a study or reference from a paper or book that has addressed something like this scenario. I would love to be able to show my customer data that addresses this question directly.
If nothing exists, perhaps I will anodize some test samples and send them out for testing. Maybe that will be a good subject for a short paper at the next AAC or NASF conference.
Thanks in advance for your time and advice.
- Alexandria, Minnesota
A. The .002" coating will certainly give you much better corrosion resistance IF...and I mean IF, it is properly sealed. Your typical 15 min mid-temp nickel acetate seal that one could use on a type 2, class 2 coating would not be adequate on a typical hardcoat subjected to a corrosive environment. An old-fashioned 2-3 min/micron sealing in deionized water @ 200-212 °F, held within a tight ph range, is a far superior seal for corrosive environments than your standard mid-temp nickel acetate seal.
I believe it was either Products Finishing, or Metal Finishing magazine that had a fairly solid article comparing different types of sealing, and the resulting effects on the coating properties. It was quite some time (years) ago, so the article could be hard to locate.
Bottom line here Mike, is that there are things an anodizer can do not only to the coating itself by tweaking processing parameters, but also with the sealing techniques, that can greatly enhance the corrosion resistance properties of the coating. You can cite all the articles you'd like, but if you're not following the same processes as detailed (or not detailed, as the case may be) in the articles, it really does little good.
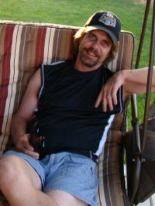
Marc Green
anodizer - Boise, Idaho
November 13, 2013
Q. Hi,
I have a regular design of anodized valve housing.
Now if I go for hard anodised process is there any changes in tolerances or dimensions? Any more twisting or warpages in housing that can happen in this new process?
- GGN , HA , India
October 13, 2014
A. Hi Pankaj. Hard anodizing is usually considered to be 0.002" thick, which is probably at least 3 times thicker than your present anodizing, so there will be significant dimensional changes. I doubt that it will cause twisting or warpages in most parts, but there could be very thin parts where it might be a problem. Good luck.
Regards,
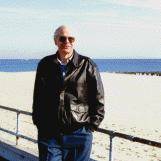
Ted Mooney, P.E.
Striving to live Aloha
finishing.com - Pine Beach, New Jersey
December 2014
October 21, 2020
Q. Hi everyone,
ACRONYMS:
M.E. = Mechanical Engineer
UUV = Unmanned Underwater Vehicle
I am an M.E. at a company that works with UUV's and we have a part that is made of 6061-T6 and was originally Anodized w/r to MIL-A-8625 / MIL-PRF-8625
[⇦ this spec on DLA] Type II Class 1, with a DiChromate seal.
Our situation deals with a lot of obviously, saltwater. and the component hard hard metal-metal seals with various stainless steels. In those metal-metal seals we see advanced corrosion.
Backstory complete, we are upgrading to a Type III DiChromate seal to combat the cracking at the Metal-metal seal and the advanced corrosion due to higher surface hardness and corrosion protection. That was until we were told about Cold Bath Anodizing. I wanted to ask the forum who I learned most of this topic from about the cold bath anodic coating and if it is worth it to go the extra mile, (apparently it is harder to accomplish and more expensive).
I would appreciate any information, Thank you,
Luke
- Newport Rhode Island USA
A. Hi Luke. I think you are correct that Type III anodizing will be more corrosion resistant than Type II -- for one thing it is much thicker, 0.002" rather than the 0.0003"-0.0006" you were probably using before -- but see Marc's important note about proper sealing.
But I don't think you need to worry about "cold anodizing". Although I'm not familiar with that particular slang, Type III doubtless IS the "cold anodizing" someone is telling you about. Type II operates at about 68-72 °F but type III operates at about 28-32 ° F.
As a brief explanation, two opposing things are happening during anodizing, an electrically insulating oxide film is being grown on the parts while the sulfuric acid is simultaneously attacking and dissolving that film. To get the thick anodized film associated with Type III anodizing in the face of that insulating film tending to stop further anodizing, plus the acid attacking it, requires higher voltage rectifiers than Type II, plus keeping the sulfuric acid cold so it is less corrosive.
Luck & Regards,
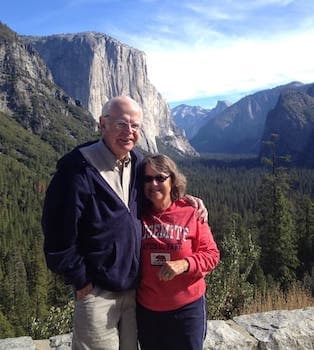
Ted Mooney, P.E. RET
Striving to live Aloha
finishing.com - Pine Beach, New Jersey
October 2020
A. Hi Luke! If you haven't run Type III "cold anodizing" also referred to as "hardcoat anodizing" due to its excellent abrasion resistance ... beyond Ted's advice, the additional pointers I have are to take extra care in ensuring that any fasteners on your racks are both snug, and VERY clean prior to starting work. If you re-use racks, as I assume most of us do, not only should you verify stripping, but take the extra time to disassemble and inspect them and sand/grind contact points. Use virgin bolts for reassembly. Any stray anodic coating that increases resistance can cause mid-run conductivity failures and burning due to the increased current.
Another tool is the surfactant "anti burn" additives that can be added to the plating bath. This is not a substitute for good rack maintenance, but will help protect the load. They're very expensive, but at less than 1% of total bath volume worth the money.
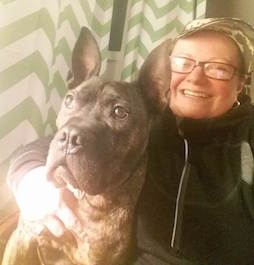
Rachel Mackintosh
lab rat - Greenfield, Vermont
October 24, 2020
October 26, 2020
Q. Thank you both Ted and Rachel.
The shop we are working with has been making Type III Anodic coating with the diChromate seal but at their shops ambient temperatures:
Tests 1/2:
Time: 45-50 mins
Voltage: 15-18V
Temp: 66 °F
The thickness is to spec but another coworker had worked on a project where it was specifically called out to use a bath temperature under 34 °F to achieve the denser coating.
I was wondering if you two and anyone else would have any additional input on the overall difference between Anodizing at the higher temperature and the lower temperature.
Thank you,
Luke
- Newport Rhode Island
A. Hi again. I just took a quick look through MIL-A-8625 to refresh my memory, and it does not require that Type III anodizing be done cold, although some people, perhaps a bit facetiously, call it "Type 2-1/2" when it's not done cold :-)
There is also no corrosion resistance required of hardcoat unless sealed. And although the spec says it's 0.002" thick, it also says "unless otherwise specified". And there is an abrasion resistance spec in section 3.7.2.2, but it doesn't apply after sealing. So it's pretty hard to say exactly what hardcoat is & isn't.
But because you are suffering an abrasion-corrosion problem you are currently trying to fix, I'd probably suggest that you do an abrasion & accelerated corrosion test on what you're getting now, plus find a supplier who does actual cold hardcoating and do an abrasion & corrosion test on that rather than conjecture.
Luck & Regards,
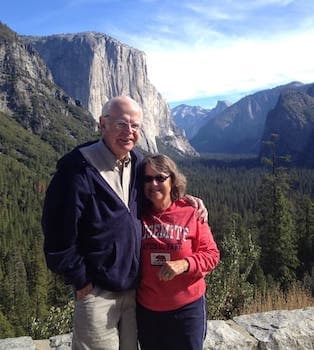
Ted Mooney, P.E. RET
Striving to live Aloha
finishing.com - Pine Beach, New Jersey
October 2020
A. Checking in as someone who facetiously calls it "type 2-1/2"! :)
We like it for a certain product range (think recreational outdoor products) that are more desirable with a slightly improved abrasion resistance, but have to be dyed (organic azo dyes) to jewel tones. The lighter colored anodic layer, when compared to "cold" tyIII, allows this. 32 °F/0 ° "cold" hardcoat is a deep charcoal color and to shamelessly misquote Henry Ford, "You can dye it any color, as long as it's black".
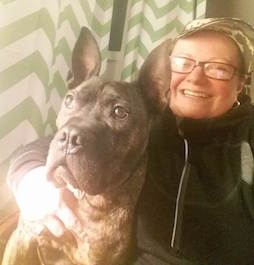
Rachel Mackintosh
lab rat - Greenfield, Vermont
October 26, 2020
Q, A, or Comment on THIS thread -or- Start a NEW Thread