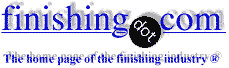
-----
Required Tin Plating Thickness on Copper?
Sir, what is the best electroplating thickness of tin on 0.61 mm thick copper sheet for a tank made to store drinking water with TDS around 200 ppm and pH around 7.
Shekar GKEngineer - Bangalore
June 30, 2021
A. Hi Shekar. There is rarely a definitive answer to such questions because it depends on the smoothness of the copper sheet, how well its pretreated, what the situation is with the solder lines, and how uniform and robust the tin plating layer is. But we've attached your inquiry to a thread where 3 µm was found inadequate but 5 µm seemed to be adequate ... so that should be at least a starting point.
You might entertain historical tin wiping as an alternative to electroplating (see thread 25553 and thread 29192).
Luck & Regards,
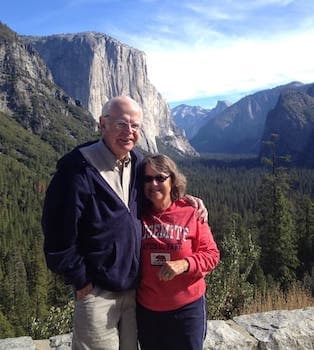
Ted Mooney, P.E. RET
Striving to live Aloha
(Ted can offer longterm or instant help)
finishing.com - Pine Beach, New Jersey
June 2021
⇩ Related postings, oldest first ⇩
Q. Hello,
I am a manufacturing engineer workings with our product design team for specifications and sourcing for applications where we require strip plating C110 copper strip with bright tin for a bolt down electrical component. We recently had a concern due to "dog bone" effect (although the edges of application are receiving the minimum specified 5 µm of tin plating, the center of the strip is about 3.5 µm of tin plating).
Unfortunately we have caught the issue after it is too late to send material back for rework. The material is stamped and the end application is connected into application via bolt down on M8 or M5 studs. The material is 1 mm thick copper C110 and then plated. I believe the 5 µm specification is used as a safety factor to assure adequate plating coverage against corrosion. What is an adequate thickness for tin strip plating to protect copper from corrosion? And, what is best testing method to validate? Not to ask too many questions but this is related: For another application where the copper is 0.8 mm thick we use 3 µm minimum of tin plating as adequate coverage. Does the thickness of plating as a barrier to corrosion need to be related to the thickness of the work piece?
Thank You
Product Designer - Chicago, Illinois, USA
September 26, 2012
A. I don't think that a tin coating of only 3 microns thickness will be sufficient. At this thickness there will probably be pores or small areas of no plate that allow corrosion to occur. If the pretreatment is excellent, than you will probably need a minimum of 5 microns.
Dog-bone effects can be minimized by good racking and or shielding techniques.
consultant - Cleveland Heights, Ohio
September 28, 2012
Thank you for your response Lyle. Our comparative salt spray results after 48 hours per ASTM B117 agree with your assessment that 5 µm minimum should be used as protective barrier thickness specification.
Q. Related, does it matter what thickness the workpiece when specifying the minimum protective plating thickness? Specifically we run parts that are 0.6 mm to 1.2 mm thick C110 for the base material and we vary plating thickness based upon thickness of base material. It just seems to me that if 3 µm on 1.0 mm thick copper is not enough to eliminate effects of porosity then 3 µm on 0.8 mm thick copper would also not be enough.
- Chicago, Illinois
October 2, 2012
Q, A, or Comment on THIS thread -or- Start a NEW Thread