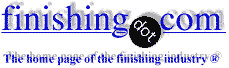
-----
How to electrowin/recover copper (plating waste)
Hi there.
I have a basic copper electroforming bath approx. 200 g/L Cu and 60g/L sulfuric.
I'd like to reduce the overall copper concentration down as much as possible using electro winning as a precursor to disposal.
I have a variety of titanium baskets. Could I use them empty as a the anode and just plate out the copper on to stainless steel sheet?
I ask because I'm having some difficulties and finding the anodes passionate quite quickly.
I've seen some titanium anodes with Ruthenium-Iridium Coating online and am wondering if I need to be using something like that as the anode?
Any help appreciated. There isn't great disposal options for hobbyists.
Hobbyist - Brooklyn New York
September 23, 2024
A. Hi Raphael.
You're making me really feel old today because I remember that when I first started traveling by air I would, believe or not, sometimes see old automobiles and other scrap steel sitting in rivers downstream of factories, placed there deliberately to remove copper from the water by displacement with iron :-(
Those days are thankfully long past, but the concept still works. Simply put some clean soap-free steel wool into a sample of your waste solution, and tell us what happens. It's much simpler than electrowinning, and may be more appropriate to your needs.
Luck & Regards,
Ted Mooney, P.E. RET
Striving to live Aloha
finishing.com - Pine Beach, New Jersey
Q. Hi Ted, I've used steel before and experimented but its slow and its not a realistic option for the scale I'm working at (50 gallon tanks)
I have all the equipment including circulators and unused anode baskets -- why not try and use the winnowing method. I'd prefer to recycle the copper rather than throw it away.
(and ps I do have a big chunk of steel in my slop sink so - you aren't so far off lol)
hobbyist - brooklyn new york
September 23, 2024
A. Hi
In thread 14472, "Electro-refining of Copper" Lyle Kirman and Tom Baker offer some great advice.
They suggest a polished titanium plate for the cathode, and iridium-oxide (MMO) mesh for the anode, which is the perfect solution ... except of course for the outrageous cost of the appropriately sized electrodes :-)
Luck & Regards,
Ted Mooney, P.E. RET
Striving to live Aloha
finishing.com - Pine Beach, New Jersey
⇩ Related postings, oldest first ⇩
RFQ: I am looking for some electrowinning cell (or system) vendors to recover copper from a spent copper sulphate ⇦ on eBay or Amazon [affil links] plating bath. Can you recommend any suppliers from the West (near California)?
Thanks in advance for your help.
b maeda-California
1998
Ed. note: This RFQ is outdated, but technical replies are welcome, and readers are encouraged to post their own RFQs. But no public commercial suggestions please ( huh? why?).
Q. I just wanted to know whether only copper can be taken out from rota cat which is dissolved in sulfuric acid or rota cat can also be used to recover metals like nickel in hydrofluoric acid, chromium in hydrofluoric acid, iron in hydrofluoric acid, zinc in sulfuric acid?
Would be delighted to have an answer.
VIDU GOYALMETAL WORKS - Rewari, Haryana
2002
A. I assume by the term "rota cat" that you are referring generically to a rotating cathode system, and not a particular system commercially sold as a Rota-CatTM. They are two entirely different concepts.
The rotating cathode design (normally a rotating metal cylinder onto which metal is electrodeposited) is useful for a variety of electrowinning applications. The caveat here is that you need to have a proper design on the other side of the reaction -- the anode -- to allow electrowinning from these types of solutions that you mention. Sulfuric acid based electrolytes are amenable to most electrode designs, however caution must be used on ionic strengths. More is not necessarily better.
The use of any type of anode in a HF environment is severely limited due to the materials of construction and the cost. You would at a minimum require a niobium substrate and platinum catalyst coating. Normally, this has to be either a hot dipped platinum coating (i.e the patented "DeGussa Process", or the platinum could be clad onto niobium in small sheets and slit and expanded to get larger geometries. Depending on how much surface area that you need, you are likely to pay several tens of thousand dollars for anodes in a system such as these -- and they might not last 3-6 months time.
There has been some limited success in the use of ion specific membranes to envelope the anodes. This requires a separate electrolyte solution to promote conductivity between the membranes and the electrodes. Fluoride, being a very small ion, will permeate the membrane over time, and you will have to deal with the issues it causes.
I would stay away from any precious metal oxide based electrodes, as these are micro-cracked coatings and will allow free fluoride attack on the substrate, which will dissolve, and the coating will literally fall off in a process called exfoliation.
As far as the actual process goes (electrode issues aside) the strength of the acids and such will determine the efficiency of the process. You have to be your own gauge on whether the costs to operate the unit, including power, man-hours to maintain and remove deposits, and replacement parts have a positive value as compared to the recovered value of the metals. Zinc and tin are the least likely to be economical, copper fluctuates, and nickel is usually a positive to break-even consideration. I am not aware of anyone who has successfully electrowon iron from solutions on a commercial scale.
You need to be prepared to run an electrowinning unit much the same as a plating bath, which means additives, buffers, and other things will be required in the case of some metals, such as nickel. Also, remember that deposit integrity is a must - you're trying to get a thick deposit, and EVERY inconsistency in the deposit will be magnified, which usually means dendrites, and low quality plating.
Lastly, I would tend to stay away from any electrowinning cell that requires the use of raw media (other than reusable substrates like stainless steel or titanium) to plate on to operate. In some cases, they might tell you that you need copper shot as a starting media. It might have a value of US$3.00/kg, but as soon as you put in the cell and use it, its value drops to type 1 scrap or less - which means you lose money right from the start. Titanium makes for an excellent cathode, and if polished and used correctly, will give you almost immediate release of the reclaimed metals. I have seen too many cells where cathode prep was non-existent, and they use air chisels ⇦ [air chisels on eBay or Amazon [affil links] to try to remove the metal deposits.
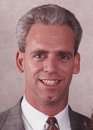
Tom Baker
wastewater treatment specialist - Warminster, Pennsylvania
Super informative posting, Tom. Thanks!
Regards,
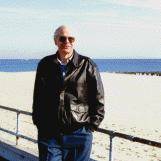
Ted Mooney, P.E.
Striving to live Aloha
finishing.com - Pine Beach, New Jersey
Q. Hello,
I am electrowinning copper chloride with a membrane. In an older post in this forum, I read that chlorides stress the deposit and consequently, it grows doing trees and dendrites and takes a lot of space on the cathode for a few grams ... and that is my problem.
I am would like to know if there is some bath additive that can reduce considerably the formation of dendrites?
Thanks,
metal technician - Bogota, Colombia
October 3, 2011
A. Try adding some gelatin, coumarin or naphthalene trisulphonic acid. I have never done it with electrowinning, but try about 1 g/litre.
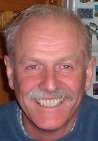
Trevor Crichton
R&D practical scientist
Chesham, Bucks, UK
Q. Thanks, I will give a try to gelatin. Do you recommend a special one? from pig? or other?
The solution contains about 10 g/liter of copper. I reduced it first to get only Cu+ chloride complex, else the solution etches my cathode. pH is adjusted to 2. Chloride concentration is about 20 g/L.
Regards,
- Bogota, Colombia
Q. Hello,
I am electrowinning copper from chloride media.
I succeeded once to get a thick, compact and adherent deposit until 1 g/L Cu but now I am suffering to get the good conditions again. My solution has around 15 g/L cuprous chloride (not cupric). I use gelatin as additive. The solution has 2 g/L Zn and 1 g/L Ni, lots of Cl-, Na+, [SO4]2-.
At the beginning of my new attempt, I got brownish and dendritic copper with 0.3 M H+.
I cleaned the cathode to remove the dendrites then I raised solution acidity to 1M H+. The new deposit was compact and adherent but my deposit has still some brownish areas in the top part the cathode. I don't see hydrogen evolution but I suppose this could be the origin of the brownish color. Electrolyte flow is 5.7 m^3/hr which is already quite high but necessary considering low copper concentration.
Why my copper deposit gets a brownish or reddish color instead of the sweet pink copper color ? should I raise acidity ? or improve circulation ?
Thanks,
metal technician - Bogota, Colombia
July 16, 2012
A. As the copper concentration decreases, you will need to do one or more of the following.
Reduce current density, and/or
Increase agitation, and/or
Use a high surface area cathode (which is the same effect as reducing current density).
consultant - Cleveland Heights, Ohio
Dear Lyle,
I think I figured out what happened. My solution had more impurities than previously, especially Ni. Increasing the acidity made the impurities less active at the cathode surface. My flow rate is around 10 m/h (m^3/h per m2 cathode) and I got nodular but compact deposit which is enough for my application.
Pedro T.
- Bogota, Colombia
Copper electrowinning parameters
Q. Hello everyone,
I'm currently working on electrowinning of copper from copper sulphate solution.
The initial specifications for the copper sulphate solution are:
Copper content: 21000 ppm
pH: 1
I used the following parameters for my electrowinning of copper
Temperature: 38 °C
pH: Adjusted to 2 using ammonia
⇦ on
eBay or
Amazon [affil links] hydroxide of 1M
Boric acid of 30 g/L
Cathode: Stainless steel 316L
Anode: Titanium coated with platinum
Current density of 400 A/m2
However after 5 hours of plating and maintaining the pH to less than 2, I realise dark brown powder coated onto the cathode. I assume that is copper but I don't understand why is it not adhering to the cathode. I'm expecting it to be plated out like a sheet of copper.
Can anyone enlighten me if I have done anything wrong or change any of my parameters?
Thank You
- Singapore
August 25, 2014
A. Hi Yan
Many things in your question suggest that you are not an experienced plater or chemist and it would be interesting to know how you arrived at your starting conditions ... but I will try to point you in a more productive direction.
It is important to know what you mean by electrowinning. It usually applies to a method of extracting copper from ore or a crude copper anode e.g what you might get from melting electronic scrap. In that case, your objective is to obtain as pure a deposit as possible and the appearance does not matter because it will be melted down. Therefore you would plate onto a copper plate and avoid additives. The cathode plate is either stripped or, more usually, smelted with the deposit. Electrowinning is a crude large scale operation using impure materials with very little control of the plating conditions.
The term is sometimes used to describe extracting metals from rinse waters.
Firstly, if I have counted all those zeros correctly, you have about 21 g/l of copper, which is rather low. In a practical electrowinning situation, you would want it as high as possible to allow more current to pass and speed up the process.
You should aim for about 100 g/l of sulfuric acid. Unless you have very specialised equipment and knowledge, pH values under about 3 are meaningless.
I have no idea why you are adding ammonia. It is a very bad idea as it will complex with the copper and cause endless problems.
Similarly, boric acid has no use here.
If you really must have a fine grain deposit, the simplest additive is probably gelatin about 1-2 g/l but some will be in the deposit. It is rarely used in electrowinning
Current density is about 3-5 A/dmsq at room temperature (neither is critical).
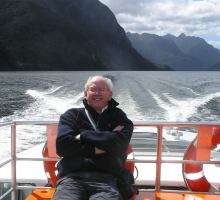
Geoff Smith
Hampshire, England
Electro-won copper is fragile and only the density of a cookie
Q. Hey there...
I'm getting copper electrolyte from sea water leaching process, in which 01 Washing stage in SX, with not that high chlorine level in electrolyte.
I'm working in a copper sulphate electrolyte tank house and we tried to electro-win copper -- but it was very fragile & easy to rip out.
Conditions:
- Cu: 28 g/lt
- H+: 180 g/lt
- Cl: 40 ppm
- T: 25 °C
- Amp: 6000 Amp
- Density 45 A/m2
What's the reason for the "cookie" density copper?
Thanks
- Sta Rosalia, BCS, mexico
November 21, 2014
Electrowinning Research: Copper is turning black during electrowinning
Q. I am working on a project for extracting copper from powder-form raw material which is a waste from brass industries, containing 7-15% copper, 20% zinc and around 10% iron.
I have taken 3 samples of 25 grams and dissolved in mild H2SO4, HCl and CH3COOH in three beaker [beakers on
eBay
or
Amazon [affil links] s. I tried to apply direct DC current using Carbon Cathodes^Anodes (+) to pass electricity as the copper is already dissolved in the solution and a Copper anode^cathode (-) to accumulate extracted copper. But the thing is when I switch on the electricity some bubbles start to form and copper anode^cathode suddenly turns black. In this experiment the main target is to extract copper from raw material (not finishing).
Please help. I have no clue what is exactly happening in my cell. And please give some suggestions.
Thank you.
M.Tech Chemical Engineering student - Kadi, Gujarat, India
December 14, 2014
A. Hi Apurva. Your nomenclature is reversed. The negative pole where you are accumulating your plated-out material is the cathode, and your carbon positive pole is the anode. I am assuming that you succeeded in dissolving the powder into the acids before you started trying to plate it out?
You haven't given us any details on pH, current density, etc., but from your description of bubbles and "suddenly turns black", it sounds like the current is far too high. What you probably need to do as a first step is to maintain a current density so low that copper plates out preferentially to iron, nickel, and hydrogen.
Good luck.
Regards,
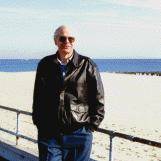
Ted Mooney, P.E.
Striving to live Aloha
finishing.com - Pine Beach, New Jersey
Q. Thank you so much for your reply. It helped a lot. I have used hydrogen peroxide to increase leaching but as it is strong oxidant; I suppose that's why I get black copper. I am using 20% sulfuric acid for leaching and electroplating in same cell. I am using 5V 0.4A DC source for plating. My raw material is smelter slag containing copper, zinc, and iron in major part. So I am directly mixing 25 grams of sample in 20% sulfuric acid and apply electroplating in same cell. My main target is to recover copper and zinc from the raw material. Please guide me in right direction. Am I doing it right?
My questions are:
1. At what voltage I can only get copper from the produced mixture of copper sulphate, zinc sulphate and iron sulphate.
2. Should I use different solvent to increase electroplating efficiency?
3. I have heard about some organic chemicals that can separate copper sulphate and make it float over the solution. Is it true? If it is then suggest some names.
4. Can I recycle electrolyte?
5. Can I recover zinc and copper both from the same solution? What changes should I apply.
6. Can I use iridium oxide coated titanium anodes for this application to eliminate anode corrosion? Or to provide better anode.
Thank you so much for helping.
I guess you are my only hope.
Thank you.
- Kadi, Gujarat, India.
A. Hi Apurva. I'm sorry to hear we're your only hope because my experience is in electroplating, and while there are certain similarities, I can't help you very much in the details of differential electrowinning ...
Yes, a strong oxidizing agent like peroxide can wreak havoc on electrodeposition -- hopefully there is little of it remaining by the time you do the plating. Bubbling the solution should help it escape.
1. Copper is more noble than iron or zinc and will selectively plate out if you keep the voltage below the voltage needed to plate those other metals out. But it's not quite as easy as looking up the potentials in the galvanic series because it depends on concentration. 5V sounds Way too high unless the anode is quite far from the cathode so there is over 4V of solution resistance.
2 & 3. I have not heard of such in my limited experience.
4. Recycling may be possible to some extent, but the acidity is consumed whenever hydrogen bubbles are released from the process. 2H20 ⇨ H2^ + 2OH-1, leaving the solution more alkaline.
5. In practice I doubt that you will be able to recover the zinc. Zinc electroplaters generate tons of zinc-rich sludges, and even in their more favorable position of having solutions richer in zinc and lower in other metals, practical zinc recovery escapes us.
6. Yes, I think iridium oxide coated titanium anodes would be fine. Good luck.
Regards,
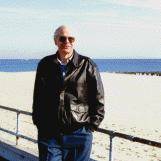
Ted Mooney, P.E.
Striving to live Aloha
finishing.com - Pine Beach, New Jersey
Ed. note: Readers, please also see letter 14472 "Electro-refining of copper" for additional discussion on this topic.
Q. In our company dealing with copper cathode and rod production, we have cathode nodulation problems. How we can solve this issue?
Khagani Asadli- Baku, Azerbaijan
May 16, 2016
A. Hi Khagani. We appended your inquiry to a similar thread to give you some food for thought. Please get back to us with additional detail or your comments on the solutions that were proposed. Thanks.
Regards,
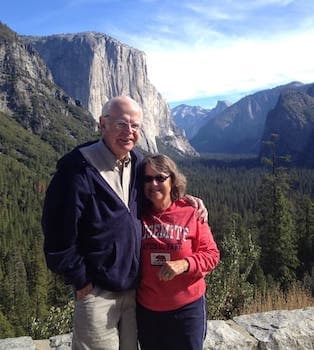
Ted Mooney, P.E. RET
Striving to live Aloha
finishing.com - Pine Beach, New Jersey
A. Nodulation is normal on thick deposits, especially in high current density areas. Are the nodules in just one area of the part or all over? Is it possible that your current density is too high?
Lyle Kirman- Cleveland, Ohio USA
Q. This is a wonderful effort by a group of experts worldwide with a view towards finding out minor faults in operation. Appreciate all your work!
We, at Jay Somnath Industries, are having a melting unit with a rotary furnace for melting of brass residues and recover copper ingots (98.5% Cu) along with collecting zinc oxide (80%+ ZnO). We are thinking of further refining copper to a high-grade copper ingot and zinc ingots from 80% Zinc Oxide powder via electrowinning.
Specification of copper ingot:
Weight - 60 kg
Length- 20 inch
Width- 8 inch
height- 5 inch
Avg. spectro result of Copper:
Zn: 0.028 %
Pb: 1.077 %
Sn: 0.114 %
P: 0.00 %
Mn: 0.0106 %
Fe: 0.027 %
Ni: 0.391 %
Al: 0.009 %
Si: <0.005 %
Ag: 0.043 %
Co: 0.003 %
Cu: 98.298 %
First of all; Is it possible to purify such ingots with electrowinning? If it so, then we can operate with existing ingot size or should we have to change the size that fits with the requirement?
Secondly, does zinc oxide have some future with electrowinning?
Please enlighten to concepts with your life long experience.
Regards,
Jay Somnath Industries - Gujaratr, India
September 21, 2016
Q. Design Project: Recycling Copper through Electroforming/Plating
Hi all. I am a beginner copper electroformer and am learning the ropes by making my own bath from scratch with sulphate. However, I am working towards a design project that aims to reclaim copper from copper waste (mostly in e-waste), and then use that electrolyte to plate other objects.
I'm hoping to make my own acid electrolyte but rather than adding sulphates, charge the electrolyte with a waste copper pipe.
Any ideas on a recipe? So far I am thinking 1 L distilled water, 70 g sulfuric, 1 drop of hydrochloric - then run the anodes (pipe) at 3 volts overnight and more as needed to charge the electrolyte. Will the colour be my main indication of copper concentration (along with regular samples)? I've heard vinegar
⇦in bulk on
eBay
or
Amazon [affil links] is a good base but since I have 98% sulfuric at hand, is vinegar even needed? I would like to get this as professional and predictable as possible - hopefully to suggest ways in which we can make and reclaim metals from our environment more sustainably.
One last question about calculating Surface Area (e.g. 31 inch2 /81 cm2) & Anode SA. The 1 inch: 0.1 Amp ratio I get, however, I have not mastered the anode dance of 1:2. My anodes are flattened pipes (approx. 5cm L X .3-.5cm W), can someone talk me through the calculation for how much anode to put in the bath?
I assume it's also by SA of a 'rectangular tank' so in my cm calculation I need something like 2cm total in the bath? (I dropped out of math at 14, BIG MISTAKE!).
- Eindhoven Netherlands
April 9, 2021
A. Hi. I have only ever seen one shop do actual production copper electroplating with scrap copper as the source of the copper. If you are serious about your project try to reach out to Laurens Willard of Galvan Industries, Harrisburg, NC and see what he can share with you. I went there on a consulting assignment many years ago and learned at least 10X as much from him as I taught him, and I don't feel at liberty to reveal even what little I now know about it. So you'll have to wait for another reader to talk about the chemistry because I can't.
But I think it will be terribly difficult to use scrap as the source of a reliable plating solution without analysis and instrumentation, so I think you'll need to up your game quite a bit before you'll succeed :-)
You already made a math error because 31 inch2 is not anywhere even close to 81 cm2 :-(
Although it's true that you multiply inches by 2.54 to convert to cm, to convert inches2 to cm2 you need to multiply by 2.54 twice, whereas to convert in3 to cm3 you have to multiply by 2.54 three times.
Anode to cathode ratio is not critical, you can just eye in making the surface area of the flattened pipe twice as big as the part you are plating. But I suspect another error: the width of a flattened cocktail straw might be 0.3-0.5 cm; surely the width of even a small flattened copper pipe is way bigger than that.
Luck & Regards,
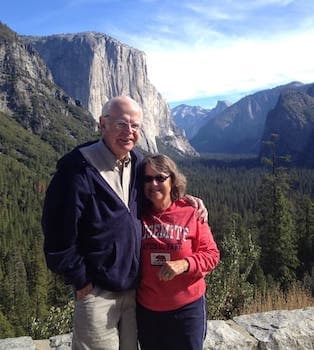
Ted Mooney, P.E. RET
Striving to live Aloha
finishing.com - Pine Beach, New Jersey
.
Q. We have a small copper EW cell for recovering copper from rinse plating process.
1. What is the optimum concentration or % of free cyanide in the operating cell?
2. Is there a safety hazardous from emission of the HCN around the cell?
3. What is the frequency of cleaning the cell?
Thank you.
- Grosse Pointe Woods, Michigan
February 28, 2023
Q, A, or Comment on THIS thread -or- Start a NEW Thread