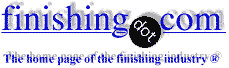
-----
High current density gassing in nickel plating?
August 30, 2011
-------First question
I have a small watts nickel plating bath of 2400 liters, agitation done by cathode rod movement, I guess it is constantly gassing because I see a white foam during operation(exactly the same as when a part is burning on the bath but with all the parts) a provider tells me and insist that I have some sort of contamination.
I usually plate high polished brass and CR and HR steel parts
I don't see that in other nickel baths for example competitors's baths.
My first question is
Is this normal?
------Second question
In the books
1)ASM volume 5
2)Modern electroplating fourth edition
(Despite the fact that the second book in that part look very similar to the ASM)
I saw a problem related to chromium contamination called "High current density gassing", so could it be the reason for this?
------Third question
How I identify this "High current density gassing" phenomenon? and can this be due to other types of contaminants?
Plating shop - Bucaramanga Santander Colombia
First of three simultaneous responses -- September 1, 2011
Contamination is a possibility.
My guess is that you are plating at a too high a current density which means a high voltage which means an evolution of oxygen and of hydrogen.
Increasing the agitation will reduce this. Adding an in tank pump is an easy way of doing this. Adding a sparger tube will help even more. This allows a higher current density. You may be able to get a slight increase in agitation from your mechanical, but I am going to guess that while it will help, it will not be enough for your needs.
Another benefit of the pump is that you can add a filter to it. Periodic carbon treatment will help the lifetime of your solution a bunch.
Send a sample to your solution vendor for a metallic and organic analyses. It is not that expensive and it will eliminate or confirm most of the common contaminate possibilities.
- Navarre, Florida
br
Second of two simultaneous responses -- September 1, 2011
Organic and metallic contamination lower the efficiency of the nickel plating solution and cause an increase in the evolution of hydrogen gas to one pole and oxygen gas at the other pole. Carbon treatment (try it first in a Hull Cell
⇦ huh?
or beaker [beakers on
eBay
or
Amazon [affil link] ) removes organics. Before it removes the bad organics it also takes out you desired surfactant. Then it may gas again until you replace the surfactant.
So carbon treat two times, (1) to remove the surfactant, (2) to remove the bad organics, then put new surfactant back in. Electrolytic purification (dummying) removes metallic contamination. Further, too low concentration of nickel sulphate will also increase the gassing. Too low chloride quits dissolving nickel off the anodes, the pH goes up, gassing increases. You need a qualified plating lab person to thoroughly wring out a complete analysis of your nickel plating problem.
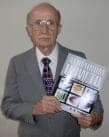
Robert H Probert
Robert H Probert Technical Services

Garner, North Carolina
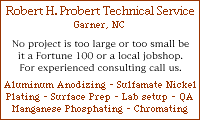
Third of three simultaneous responses -- September 2, 2011
Hi Daniel,
Watts Ni bath cathode efficiency used to close to 100% with few gassing. Abnormal gassing could be due to:
1. Gassing (likely oxygen) generates from anode as a result of improper dissolution of soluble anode (or even worse if you're using insoluble anode). The symptom is Ni concentration of bath solution keep dropping during electroplating (anode dissolution less than cathode plate-out).
2. Too low cathode efficiency due to chemical parameters out of control and/or bath contamination. The symptom is Ni concentration of bath solution keep increasing during plating (anode dissolution more than cathode plate-out). You may verify cathode efficiency by weight gain test.
3. Air leaking or suck inside circulation/filtration pump and generates lots of micro bubbles inside bath solution. Release any trap air inside circulation/filtration pump.
Regards,
David
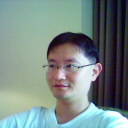
David Shiu
- Singapore
www.finishing.com/506/56.shtml
The last time you asked this question you got some pretty good answers.
It does not sound normal to me.
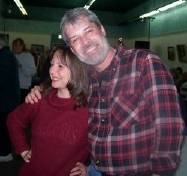
Trent Kaufman
electroplater - Galva, Illinois
First of three simultaneous responses -- September 2, 2011
Second of three simultaneous responses -- September 2, 2011
Thanks for your kind answers
well my bath lab analysis is this:
COMPOSITION OF NICKEL BATH RESULT
Niquel metalico(Metal content) 80,9 g/l
Sulfato de Niquel(Nickel Sulphate) 310,8 g/l
Cloruro de niquel(Nickel Chloride) 55,8 g/l
Acido borico(Boric Acid) 54,4 g/l
pH 3,9
densidad Be 27,0
hull cell test shows:
- Burning in high current density area
- Dark in LCD area
Thanks to James, Mr Probert and David Shiu!
- Bucaramanga Santander Colombia
Check the boric acid
Jon Diamond- Oakland, California
Third of three simultaneous responses -- September 5, 2011
The vitals look good. The burning and dark plate indicate contamination. Dummy a Hull Cell panel at 1/4 amp for 2 hours and if that does not clear up the dark and burn, then carbon treat a Hull Cell batch with sulfur free powdered activated carbon (none of that sulfur loaded granular stuff the filter people like to sell).
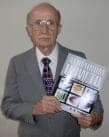
Robert H Probert
Robert H Probert Technical Services

Garner, North Carolina
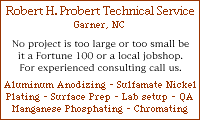
September 6, 2011
September 8, 2011
Yes!! it does not look normal for me too!!
I think despite the rule "keep it simple" sometimes it take a time for inexperienced people like me to find the answer
The last time I could not find the solution, maybe I did some mistake on the carbon treatment or the bath was highly contaminated.
Since that time the bath is still the same, this time I will try to do as Mr. Probert says, with double filtering with activated carbon following as ASM book suggest in each one.
And I was trying to connect the problem with the reason of it.
Anyway! if it is organic solution is activated carbon.
If it is metallic it will be dummy plating and high pH treatment as always.
But as a plater I have to find the reason using the information here obtained.
The lab result discard low boric, low metallic nickel, pH so the cause aims to organic and metallic contamination.
The bath is gassing on the cathode.
Here is my task. find the answer to these questions
Where all this contamination come from??
Metallic:
From the brass parts, Chromed hooks.
Organic:
Unknown. The brass parts are complex in geometry and maybe they hide caked buffing compound inside crevices(they were a headache some time ago). competitors don't plate the same amount of brass parts that I do.
The information that all of you provided is very useful, and mostly don't give the exact answer (which is very difficult) but guides you and show you the way to solve the problem.
I take it from here
Thanks again for your time and your kind efforts.
- Bucaramanga Santander Colombia
September 14, 2011
Hello,
Apologies to fellow responders, its been a long time. I have gone back in the Engineering field and am working 12 hours a day, which leaves little time for anything else.
Just a note for Daniel,I have found in the past that a hot soak cleaner followed by an ultrasonic cleaner or a direct current electrocleaner with a slightly weaker concentration than the hot soak cleaner. The soak cleaner loosens any buffing compounds and the electrocleaner will basically blow off any entrapped junk right off the part. Make sure you have enough anode area in the Nickel tank to support the area of the cathode. I like to use an anode to cathode ratio of 2:1. You may want to make sure you have enough wetter in the bath as well. Good Luck to you!
- Mesa, Arizona
Q, A, or Comment on THIS thread -or- Start a NEW Thread