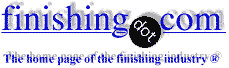
-----
Yellow Zinc Plating vs. Clear Zinc

January 19, 2011
Q. I am trying to persuade our engineering department to allow us to make the switch to have our hardware clear zinc plated. I was hoping to reach out to you to help me with this research.
Previous Engineers felt that YZP made hardware last longer based on salt tests, etc. (especially when it came to the bulk bin hardware). But the real question is how many hours of salt spray the hardware can take before the onset of white rust. Our engineering department is hoping for 96 hours.
I guess this leaves the following questions to be answered:
1. Does Yellow Zinc outlast Clear Zinc?
2. Will we see significant savings in going to clear zinc? Will lead times be shortened?
3. How many hours of salt spray can the hardware take before the onset of white rust?
4. Can anyone supply us hardware with 96 hours at a reasonable price?
5. Will you supply us with a statement on letterhead stating that the clear zinc chromate will have equal or greater salt spray resistance as the yellow zinc chromate?
6. In general, please give me your thoughts on YZP VS Clear Zinc
I really appreciate you taking the time to help us out. This is a major project that we are undertaking.
Buyer - Coldwater, Ohio
A. Hi, Jon. Ten years ago ±, most zinc plated components were conversion coated with hexavalent chromium compounds, which are yellow in color. If this protective coating was thick and robust, the parts were strongly yellow. If the coating was very thin, or used trivalent compounds instead of hexavalent, the coating would be less yellow or not yellow, but it would provide far less protection. So your previous engineers were exactly right.
But then RoHS came along, effectively banning hexavalent coatings for most purposes, so robust trivalent coatings were developed, and most plating shops switched to them. In this case the yellow color is usually just dye. So there is probably no longer an advantage to specifying yellow zinc plating.
You will probably not, however, see cost savings or reduced lead times. Many plating shops have tanks for both colors, and switching is as easy as flipping an electrical switch. The contracted plating shop may put guarantees on letterhead.
Regards,
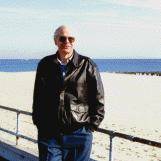
Ted Mooney, P.E.
Striving to live Aloha
(Ted can offer longterm or instant help)
finishing.com - Pine Beach, New Jersey
January 19, 2011
Q. Ted,
Thank you for your quick response.
Our VP of Engineering, keeps harping on the # of hours the hardware can take before the onset of white rust. Does Yellow Zinc or Clear Zinc make any difference when it comes to this? What is the standard?
Thanks!
Jon
- Coldwater, Ohio
January 19, 2011
A. Hi, Jon. As I tried to explain, your VP of Engineering was correct a few years ago, but isn't any longer as, in this age of new-technology trivalent chromating, the yellow color is probably just dye. The old standard for hexavalent chromating was 96 hours, so you should have no problem meeting that with today's proprietary trivalent chromates.
Regards,
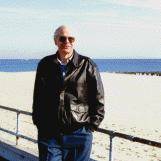
Ted Mooney, P.E.
Striving to live Aloha
(Ted can offer longterm or instant help)
finishing.com - Pine Beach, New Jersey
January 20, 2011
A. Ted is right. The yellow hexchrome based post treatment for zinc plating is out. The new trichrome based treatments with or without a sealer, can withstand more than 96 hours in NSST.
Promises are not on any letterhead. You can test each batch in NSS. Most platers have this device in their premises and can provide the test.
Anyhow, the test is only good for the batch tested.
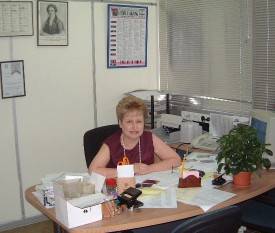

Sara Michaeli
Tel-Aviv-Yafo, Israel
January 20, 2011
Q. Hello everybody.
Sorry if my question is so rudimentary.
Could you please tell me the difference between Zinc plating and Chromating?
Automotive industry - baku, Azerbaijan
November 18, 2018
A. Hi cousin Mehrdad, your question is very welcome.
As you know, steel rusts and corrodes away. One of the most practical ways to deter that corrosion is to zinc electroplate the item. But zinc, in turn, is subject to rather quick "white rust" (ugly and voluminous corrosion of the zinc plating). For that reason, zinc plating is almost aways chromate conversion coated because the chromate is good at deterring that white rust.
But the thing is that although some metals (like zinc) can be beneficially chromate conversion coated, other materials (like steel) cannot. So there is no such thing as deterring corrosion of steel with chromate but without plating.
Regards,
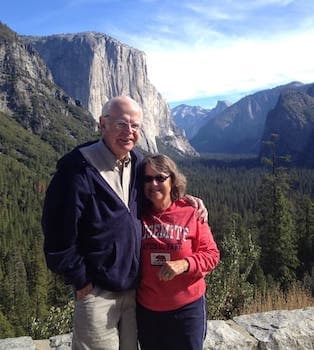
Ted Mooney, P.E. RET
Striving to live Aloha
(Ted can offer longterm or instant help)
finishing.com - Pine Beach, New Jersey
November 2018
Thank you Ted for your detailed description.
I learned a lot today, I like that!!
- Bonny Doon, California
March 4, 2022
Q, A, or Comment on THIS thread -or- Start a NEW Thread