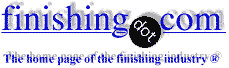
-----
Conversion Coatings and Plating on Aluminum
2000
I have a few related questions: Part 1) Regarding conversion coatings and plating on aluminum. I need to treat these parts to prevent the significant corrosion that they have incurred.
The parts that I want to treat are used in a process that is essentially microwave heating of products in water. My prototype consists of metal plates of ALUMINUM that come in contact with water at around 121C (250F). I often use deionized water, which, I am told, is very ion hungry and contributes to corrosion. Otherwise I use tap water.
I have read that chromate conversion coatings on aluminum fail at temperatures far below what I am using. The alternative that is readily available is anodizing, but that leaves the surface non-conductive. I can make a non-conductive surface work if I have to, but would prefer something else that leaves a conductive surface.
Q1: I have read that alternative conversion processes exist, but it is difficult to know where to find what I need in the wealth of information this forum and the website itself provide. Is there a suitable alternative?
Q2: How difficult is it to plate aluminum with tin or silver? Will either peel at high temperatures? Is there an alternative that will leave a more conductive surface?
Part 2) In the same device I have copper plates that will be subjected to the same conditions. Other parts of the machine were reportedly subjected to an electroplated flash coating of tin. They operated for a long time at a high temperature in a humid environment and turned black. They came clean after immersion in a bath of hot water, baking soda [in bulk on
eBay
or
Amazon [affil link]
, and aluminum (which turned colors itself). This was a home remedy intended to clean silver, but it worked here.
Q3: Does a tinned surface corrode and come clean by the process I have described, or do I really have silver plated parts?
Q4: Am I likely to see corrosion using silver or tin (Stannite?) plating if I use them for plating the copper that comes in contact with water?
thanks timothy
Washington State University - Pullman, Washington
2000
1.) If not mistaken, Metalast has a Type II and Type III finish that while it is anodize, they can also re-instill the properties of conductivity of the material. I think Ling from Metalast reads the forums occasionally, you might have to get more information from them. Other than that, there isn't really any other "alternative" that would fit your bill of needs that I know of
2.) Its not difficult to plate those two materials on aluminum, but if not mistaken ( limited knowledge here) you have to zincate the aluminum + copper flash then tin/silver plate. I'd have to read the material I have to be sure. You can also electroless copper on aluminum to the best of my knowledge, along with electroless nickel, but I'm straying away from your questions by going into all that. Basically your answer is Yes it can be done, and yes many people can do this for you (I am not one, but there has got to be someone on finishing.com that can).
In regards to the plating of tin on the copper, was it Stannate or was it Acid Tin (otherwise known as bright tin, where stannate is dull). Because I have seen bright tin used on copper conducting rods for Square D Transformers, it apparently works quite well for their application. As far as cleaning of the plated material with that solution, can't help you there, no way of telling exactly how that would correlate to the type of plating that you have on there.
I know this sounds crazy, but I remember reading where
silver will tarnish quickly when subjected to a common household egg because of the sulfur
⇦ on
eBay
or
Amazon [affil link]
in the egg tends to destroy the silver finish. If that is the case, I'm going on a limb here, but sulfur, sulfuric in the cleaner, you probably have tinned parts, I know that with bright tin, you add sulfuric to moderate and accelerate the bath to some degree, from that I come to the conclusion that the sulfuric would not damage the tinned finish. It might not damage the silver either, but I'm going with tin as the finish.
For the last question, I can get you the information, but I don't know it off the top of my head. Where I do none of these processes most of my knowledge is 2nd hand and just passed on to me from others sources I speak with.
I believe Tin is like zinc, its sacrificial, it will allow itself to be destroyed, in return for saving the basis metal. Someone want to confirm/deny that statement for me? I believe thats one of its many uses, but you guys that plate should know that one for sure for me, and feel free to correct me if need be
- Toledo, Ohio
2000
Interesting conditions, why doesn't the water boil off?
Is it pressurised? De-ionised water, at high temp' with lots of micro waves bouncing around, sounds like corrosion city. 1. Chromate conversion coatings fail at lower temperatures (forgotten the actual temp') because the chromates form a gel coat and this dehydrates
(most of this information I've picked up from finishing.com check around previous postings). As the aluminium is under water this won't happen, however I can't see why it wouldn't simply dissolve. Why not anodize? Oh right sorry you need to maintain conductivity.
2. the blackening of the tin on copper could be tin oxidising (my tin anodes blacken in acid conditions). I Couldn't say how easy plating tin on to aluminium is but tin is very good at adhering to surfaces once plated.
3. If it is tin oxidising it should just wash or wipe off, if it needs the chemicals you speak of then maybe it is silver (I haven't worked with silver so can't say more).
4. Tin is not normally sacrificial (mostly a barrier protection), but it is more active than copper and so will corrode to protect it. Silver I think wouldn't being more noble than copper.
I do have a suggestion, I think you use de-ionised water to guarantee purity for experimental purposes. So use distilled water, this is pure and is no more corrosive than tap-water (depending on your local supply).
Good luck!
university - Glasgow, Scotland
Q, A, or Comment on THIS thread -or- Start a NEW Thread