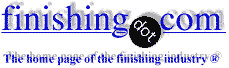
-----
Hot-Dip Galvanizing: best Nickel and Aluminium content?

[editor appended this to a thread already addressing it rather than starting a new thread]
Q. Hello, Geoff Crowley.
Good morning.
I hope you are in good health.
I am writing to ask for your help, if possible.
I have some questions about the addition of aluminum and nickel to the zinc bath.
I have a 56-ton of zinc In the kettle.
The nickel I have is pure nickel, in tablet form and with a content of 99.8%.
On the other hand, the aluminum I have is in alloy form (80% Zn-20% Al).
I would like your help with this.
What is the correct dose of aluminum and nickel that I should add to the 56-ton zinc bath to obtain an impeccable galvanization?
The type of galvanization is batch hot-dip galvanization.
It is known that nickel is quite active on reactant steel, that is, steel with a silicon concentration above 0.03% to 0.22% and gives a significant reduction in the thickness of the coating.
The same is true for aluminum.
Therefore, my concern is to add, for example, 500 ppm of nickel and 300 ppm of aluminum or vice versa, and after galvanizing, I will have problems with black spots and very low coating.
Please, I need your help.
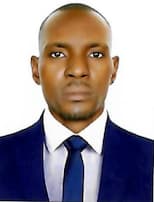
Domingos
- Luanda, Angola
May 11, 2025
A. Nickel (Ni) is used mainly to reduce coating thickness, but especially is steels that contain between 0.03 to 0.12% Si. It also has a lesser effect of reducing coating thickness in other chemistries too. The optimum Ni content is between 0.04 and 0.06%. It's important to keep within these limits. Less than 0.04% has no real benefit, but it costs something, so spending money without benefit is no god. Excess Ni tends to increase the incidence of floating dross.
Al is added for two reasons. Not for reducing coating thickness as you suggest, but to increase brightness of the coating and also to reduce the rate of oxidation on the surface of the zinc in the kettle. The optimum Al% is about 0.002 to 0.003%
Adding these:
You are using Ni tablets you say. They are not usually pure Ni, more often a mix of flux, wax and nickel. When you add Ni, (any method) it does not all dissolve in the zinc. Some goes to the dross, some to the ash and some dissolves. In tablets typically you need to keep adding 1.2kg tablets per tonne of zinc added to the kettle to keep up. If you have none to start with and need to add some to get to operating level, then this depends on the size of the tablet. For the most commonly available types (about 0.1kg Ni/tablet), you need 10-14 tablets per tonne of zinc in the kettle.
For Al, you can just add as you go along. How to add depends on the style of ingot. You say 80/20 Zn/Al, which is unusually high. 5% is more common and 10% occasionally. I suspect this that you have was not made for this purpose, but perhaps made for diecasting use. These 80/20 ingots might work. You are seeking 0.002% of your 56 tonnes (56000kg) to be Al. that's 1.12kg Pure Al equivalent. But your ingot is only 20% Al, so you need 5 times as much, or about 5.5kg.
Al doesn't last long. It oxidizes and forms some of the ash on the surface of the kettle, so you have to keep adding. For your small kettle (56t = about 8m3) I suggest that you should add a small amount each day, and it will be about 1-2kg.
To be adding any alloys to a galv kettle it is necessary to get the zinc analysed at least monthly. You need to know the Ni, Al, Sn, Pb, Fe content. Without analysis you will be operating blind.
Excess Al will cause small black spots on the surface of the coating (you also said that, so you know already).
You asked for a recipe for "impeccable Galvanization". Adding Ni, Al will help, but of course there are many more important aspects of the process to get "impeccable". But keep going, keep improving, and good luck.
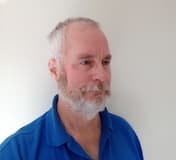
Geoff Crowley, galvanizing consultant
Crithwood Ltd.

Bathgate, Scotland, UK
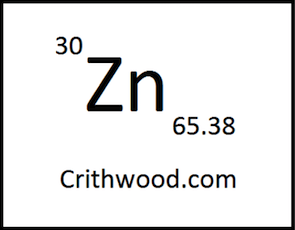
⇩ Related postings, oldest first ⇩
Q. Dear sir,
We are going to set up a new plant.
Please inform us how to calculate initial and regular addition of zinc-nickel alloy and zinc-aluminium alloy for a 77 mt capacity zinc kettle.
What is the alloy ratio for zinc, nickel and aluminium?
engineer - Haridwar, India
March 24, 2010
![]() |
A. There isn't a definitive answer to this, it rather depends on what you intend to do. ![]() Geoff Crowley Crithwood Ltd. Westfield, Scotland, UK ![]() A. Sir: Galvanizing Consultant - Hot Springs, South Dakota, USA |
Q. We mainly galvanize angles which are in-house production. Therefore we are able to know the analysis of the products. Our galvanizing production is 4500 ton/month. 600 ton of it is job galvanizing material. I have decided to use nickel lo lower coating thickness and now nickel concentration in my kettle is 0,05 %. Pb is about 0,3% and Al is 0,0001%. Flux baumé is 22.
My problem is, having too much different coating thickness along a galvanized angle. (60 micron to 120 microns).
I would like to have 90 to 120 microns. What could be the reason? Flux or kettle?
- Turkey
March 31, 2010
A. Efe,
If you have control of the steel chemistry, what is the analysis? C, Mn, Si, S, P other?%
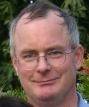
Geoff Crowley
Crithwood Ltd.
Westfield, Scotland, UK
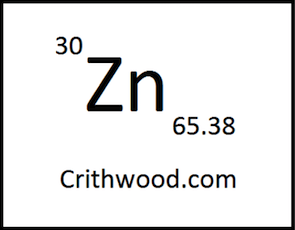
Q. Generally, Si 0,22 P:0,012
Si: 0,21 P:0,013
Si:0,19 P:0,017
Si:0,22 P:0,02
Si:0,19 P:0,022
Lead is %0,29 in my kettle. Should be %0,6?
- Turkey
A. Your steel doesn't really require Ni addition, especially if you have control on the steel chemistry to the stated levels.
If you don't have control, then 0.05 - 0.06 is reasonable.
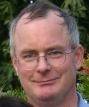
Geoff Crowley
Crithwood Ltd.
Westfield, Scotland, UK
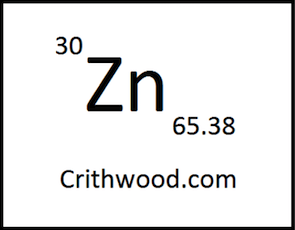
A. Efe,
Geoff is exactly correct. At about 0.2% silicon, nickel has almost no effect in zinc coating thicknesses. At 0.2% silicon there is a low spot in the Sandlin curve and having 0.05% nickel is a waste of money and nickel causes lung and throat cancer.
Where nickel is useful is between about 0.05% and about 0.15% silicon.
If I read your original question to Geoff, I believe you are having a "first-in last-out" problem. With your 22 deg. Be' flux (presumably double salt, contaminated with iron +2 and at room temperature or only warm), your going-in time is long (due to spatter) and you probably withdraw slowly. Thus the bottoms of your angles have thick zinc and the tops of your angles have too thin of zinc. As an experiment process a single angle and put it into the zinc quickly and then withdraw a few centimeters each minute. When I have done this experiment in the past, each minute gives about 1 mill (25 microns) more coating of zinc.
In the USA I saw a galvanizer using hot (71 °C) quadraflux (baumé= 14) immerse the angles very quickly (about 15 seconds for 6 foot long angles), have them in the zinc about two minutes, and then withdraw quickly (except for the last 2 inches to avoid icicles). The average zinc thickness was about 2 mils (50 microns) which is what they wanted.
On long angles you could try racking horizontally and do a first-in first-out experiment. I think this would not work without quadraflux.
Regards,
Galvanizing Consultant - Hot Springs, South Dakota, USA
Q. Dear Mr Geoff and Mr Cook,
What about Pb content in the kettle? %0,6 is ok or too much?
How and how often do I need to add Al to maintain %0,001 Al content in the kettle? (%5 Al%95 Zn)
- Turkey
A. Efe,
For most galvanizers, aluminum is added once a day. For a small kettle (especially spin), it may need to be added twice each day. The methods are those given in my answers to Anup.
Lead is an entirely different matter. In the USA, lead has been determined to be toxic, especially to children. Thus each state in the USA is restricting lead to lower and lower limits for any kind of coating. This started with paint and it is spreading to hot dip galvanizing. Thus in a few years, I expect all USA hot dip galvanizing zinc will be lead free.
Lead increases the fluidity of the zinc so that drain lines and icicles are reduced. It has been determined that bismuth at about 0.08% does a similar job, except it is expensive and there is evidence that it causes white rust. I am working on an alternative approach for lead free zinc now.
The higher the lead level the more fluid the zinc. Lead has a solubility of about 1.4% at 840 F. You also need a lead alloying device to attain that level as lead does not pass up through the dross. To use the dross bucket as a lead alloying device is a bad idea because it causes floating dross.
Regards,
Galvanizing Consultant - Hot Springs, South Dakota, USA
Multiple threads merged: please forgive chronology errors and repetition 🙂
Hazard of Nickel in Galvanizing
! The NIOSH Pocket Guide to Chemical Hazards ⇦ on
CDC.gov
lists the maximum exposure limits for airborne nickel as: NIOSH TWA 0.015 mg/m3 and for OSHA TWA 1 mg/m3.
For more than twenty years I wondered why the OSHA (a regulatory agency) limit was 67 times higher than the NIOSH limit. I just could not imagine a "company" with enough power to cause OSHA to set such a high exposure limit for airborne nickel. In 2012 I found the answer, downloadable on the internet (Google) at:
"Nickel Powder/Nuclear Weapons, The Untold Story" by Cliff Honicker
After reading this 26 page article, I would be happy to comment on any in-plant airborne nickel testing results that may be posted on this thread in Finishing.com.
Regards,
Galvanizing Consultant - Hot Springs, South Dakota, USA
May 30, 2012
Ed. update May 2025: The world wide web absolutely sucks in one way: articles & information simply disappear forever. We should have downloaded that article in 2012 because 2 hours of searching for it today were fruitless. If anyone has a copy please let us know.
reply: Hi, Dr. Cook. It is difficult to see a consistent point in this story. His central theme seems to be, not that OSHA levels of nickel are dangerous, but that the K-25 Oak Ridge workers were exposed to dangerous conditions that were deliberately covered up in order to not interfere with production, and that they were exposed to nickel carbonyl, microscopically fine inhaled nickel powders, UF6, and many other dangerous materials. He further seems to assert that the exposures were much much higher than the records indicate (i.e., dusts were allowed to settle for hours before measurement, so the records are not indicative of actual exposure levels).
I guess what I'm saying is that in making his point about how dangerous the conditions were for the workers and how they were deliberately misrepresented he seems to not have used anything from the records in a way to indicate that OSHA-permitted levels of nickel exposure are a problem. Yes, nickel exposure can be a problem, and it's possible that OSHA levels are not low enough, but I don't see how this article furthers that.
Speaking of those conditions at Oak Ridge in a lighter way though, get hold of Richard Feynman's "Surely You're Joking Mr. Feynman" ⇨
Feynman was the coolest scientist ever, as well as a Nobel prize winner, and this always amusing book includes a funny chapter describing his safety visits to Oak Ridge during the Manhattan Project, with the Army trying their best to keep Oak Ridge personnel from killing themselves & each other with radioactivity ... while also being very careful to not let any workers gain even the slightest clue about the materials they were working with because it was America's most closely guarded secret 🙂
Regards,
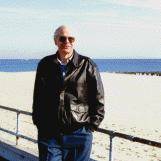
Ted Mooney, P.E.
Striving to live Aloha
(Ted can offer longterm or instant help)
finishing.com - Pine Beach, New Jersey
followup: Ted,
I agree the Honicker article has insufficient numbers and too many words. I also agree that the other poisons present confuse the issues. The article certainly presents some very useful information for hot dip galvanizers.
Two other article of interest are:
"Nickel: A Review of Its Occupational Health Aspects" by Ernest Mastromatieo , M.D., D.P.H., D.I.H.
Am. Ind. Hyg. Assoc. J. 47(10):589-601 (1986)
and
An Evaluation of Airborne Nickel, Zinc, and Lead Exposure at Hot Dip Galvanizing Plants by Dave K. Verma and Don S. Shaw. AM. IND. HYG. ASSOC. J. 52(12):511-512(1991)
The first of these articles shows historically many, many cancers caused in nickel refining plants (wherever a dust is present). This article was recommended to me by the Nickel Development Association so as to show me how safe nickel is. It had the opposite effect.
The second of these articles gives airborne nickel numbers in actual galvanizing plants. This second article was financially supported by the nickel industry. My view is that there are problems in this article.
To obtain these two articles try inter-library loan or purchase off the internet.
Regards,
Galvanizing Consultant - Hot Springs, South Dakota, USA
Q. Has anyone yet come up with an effective alternative to control "Sandelin" steels in galvanizing other than microalloying with Ni? If so what is it?
June 5, 2012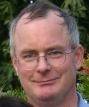
Geoff Crowley
Crithwood Ltd.
Westfield, Scotland, UK
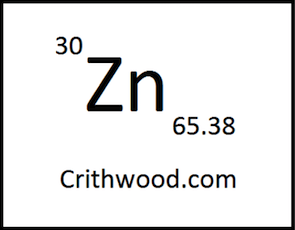
A. Geoff,
Yes. Me. NiftyGalv.
Regards,
Galvanizing Consultant - Hot Springs, South Dakota, USA
A. Dr. Cook, you are an extraordinary contributor to the site and a priceless help to our readers!
But please remember that advertisers make this site possible so we can share camaraderie and interesting technical discussions here. Commerciality that might steer business away from them and towards non-advertisers, may make them change their minds about supporting the site. Thanks!
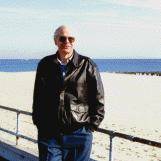
Ted Mooney, P.E.
Striving to live Aloha
(Ted can offer longterm or instant help)
finishing.com - Pine Beach, New Jersey
Ted,
My primary reason for presenting information about nickel in hot dip galvanizing is a "heads up" for galvanizers to prevent future health problems in workers. I have also exposed my "hidden agenda" of having a competing process which does not use nickel or lead. To you I apologize for submitting an obvious advertisement and to your supporting advertisers I also apologize. As you know I financially supported finishing.com for one year, but it was not beneficial to my business. I do very much appreciate the opportunity to present what I have found in the literature and some experimental results:
From a state (in the USA) regulatory agency, five hot dip galvanizing workers (kettle skimming and ash "working") all had an exposure of about 0.013 milligrams/m3). This plant does not have a kettle enclosure, exhaust system. or bag house. The second row of the below table shows what percent above maximum exposure level 0.013 is:
In the first row of the table below are presented the current and proposed maximum airborne exposure limits for nickel (all in units mg/m3):
OSHA NIOSH NIOSH(A) CALIFORNIA(B) (2007) (2007) Proposed Proposition 65 (1976) 1.0 0.015 0.005 0.001 1.3% 87% 260% 1300%
(A)The 0.005 value NIOSH Proposed (1976) comes from page 2 of the Honicker article.
(B)The 0.001 value comes from an article on the internet as NICKEL AND COMPOUNDS-SCORECARD HOME "An acute Reference Exposure Level (REL) of 1 microgram per cubic meter is listed for nickel compounds in the Air Control Officers Association Air Toxics 'Hot Spots' Program..."
It is my understanding that OSHA is a regulatory agency and NIOSH is a conservative, scientific agency concerned with health aspects of workers. It is troubling that OSHA has 67 times higher limit on Nickel than does NIOSH.
In the Honicker article a lag in time of 20 to 35 years is mentioned from exposure to the onset of major health problems. Also mentioned is the use of urine nickel testing. The Honicker article lists sub acute, chronic symptoms of substantial nature.
Nickel chloride added to flux is currently being marketed in the USA. I recommend airborne nickel testing results be presented by the sellers of this product.
Regards,
Galvanizing Consultant - Hot Springs, South Dakota, USA
A. Dr Cook is making some interesting and noteworthy comments. I would particularly like to comment on his statement about nickel refineries and cancers. It has been known for many years that workers in nickel refineries can suffer from excessively high occurrences of cancer; the most common cancers are lung, nasal sinuses and laryngeal. A lot of work has been done on the relative causes in relation to the types of nickel the workers are exposed to and it has been found that one of the most hazardous sources, in broad terms, is water soluble nickel.
However, when considering nickel refineries, water soluble nickel is a secondary interest because the airborne nickel is not in a soluble form. The important issue with refineries is the type of nickel ore being refined. It was established back in the 1920's or 1930's by, I believe, Gawkrodger (don't rely on this name, as I am not absolutely sure of it), in some work done in English and Welsh refineries. He showed that nickel subsulfides are particularly carcinogenic. This work has been replicated on numerous occasion since then and has confirmed these findings. The findings also strongly suggested that suboxides are also a high risk source, but subsequent work has not totally confirmed these findings. However, the bottom line is that when the refineries studied in the early work changed their nickel ore sources to non-subsulfides or suboxides, the incidences of cancer decreased.
One of the major problems with studies involving airborne pollution and cancers is the interference of smoking -- this is well known to cause cancers and can sometimes give false results in studies involving respiratory illnesses and diseases.
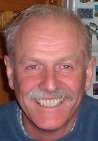
Trevor Crichton
R&D practical scientist
Chesham, Bucks, UK
Trevor,
I am well aware that nickel has caused many cancers in workers in the nickel refining industry. Perhaps 30 or more years ago nickel METAL was listed as a suspected or likely cancer causing agent in humans. In lab animals cancers were often induced using nickel powder. On page 224 of the 2007 Ed. USA NIOSH Pocket Guide to Chemical Hazards (CDC), Nickel is listed as: "TO: Nasal cavities, lungs, skin [lung and nasal cancer]." Thus it is clear that Metallic Nickel need not be soluble to cause cancer. On finishing.com letter number 58320, a steel worker laid her face down on a galvanized steel I-beam and had an allergenic reaction to the galvanizing. I believe that the galvanizer who galvanized that I-beam has 0.05% nickel and 1% lead in his zinc. He did not have a hexchrome quench.
The following methods may reduce Nickel (or Lead) worker exposure in hot dip galvanizing:
(1) Use dust masks (N95; with one rubber band) or personal respirators (two rubber bands and an aluminum nose clip) during periods of visible smoke or dust.
(2) Use a pipe to vent smoke/dust from an ash/skimmings recovery furnace to the outside of the building. This pipe (stack) will corrode though in a year or two due to high temperature and high chloride in the smoke, ash, dust.
(3) Wear a two rubber band personal respirator when transferring ash from the recovery barrel to the transport barrels.
(4) If the kettle has an enclosure, air extraction, and bag house, then be sure they are properly operating.
(5) Some galvanizers advocate rotating the workers (especially the ash/skimmings processing guy) so that one worker avoids excessive exposure. The problem here is that more workers would be exposed.
(6) Good hygiene can reduce worker Nickel (or Lead) exposure. Proper hand washing, not smoking cigarettes which have been soiled by dirty hands, keeping soiled clothing out of the lunch room, can all reduce Nickel (or Lead) exposure for workers.
(7) Grinding or sanding zinc icicles off the product or grinding or sanding before painting the galvanized product needs be properly done (likely with masks), and carefully cleaning up the floor dusts can reduce worker exposure to Nickel (and lead).
(8) If Nickel powder (or lead ingots) is stored, then put it in an isolated non-working area and keep the area around the powder or ingots vacuumed up.
(9) Do timely periodic worker urine/blood testing to determine the actual levels in the workers. Metals of interest include, but are not limited to: Nickel, Lead, Tin, Bismuth, Zinc, and any other metals that may be present.
Regards,
Galvanizing Consultant - Hot Springs, South Dakota, USA
A. Cliff Honicker gave me the name of a woman that worked 1 1/2 years as an office person (1996) in the "nickel plant" during the enrichment of uranium for the U.S. government. She told me that her urine nickel test showed 26 times the maximum allowable nickel in her body. She was also exposed to 14 different kinds of toxic and radioactive materials for which she is receiving compensation from the U.S. government. Thus no conclusions can be made regarding the toxicity of nickel alone, however she thinks the sinus problems that she experiences are due to nickel. Since her exposure was only 16 years ago, the cancer possibility has likely not had time to show up. This entire thread is a "heads up" for galvanizers using nickel in their zinc bath.
Regards,
Galvanizing Consultant - Hot Springs, South Dakota, USA
Q. Dear Sir,
Currently one of my suppliers is introducing to me a product called "MZS nickel cakes" -- each is 150 g.
Does anyone know of this technology?
According to the supplier, there is no criteria to add this product into hot dip galvanizing pot.
I'm worried if this product will cause problem to zinc in the pot.
I have a few questions if anyone can help me:
1) The temperature required to add this product?
2) Disadvantages of this product?
- Rawang, Selangor, Malaysia
September 21, 2012
A Guide to process Selection & Galvanizing Practice"
by M. J. Hornsby
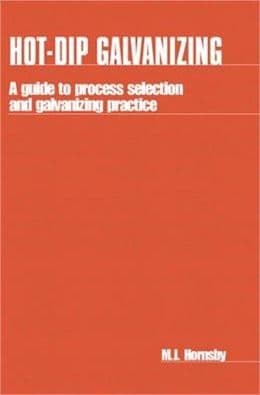
on eBay or Amazon
or AbeBooks
(affil link)
A. Hi PJ. We can't comment on proprietary products ( huh? why?), but are we to assume that these are 150 gram chunks of nickel metal, perhaps sintered or aerated or with trace ingredients to aid in melting and dissolution?
Did these cakes fall off a truck? It's certainly strange that someone selling these cakes doesn't know their advantages and disadvantages, how much to use, how to make the additions, or when or why 🙂
Regards,
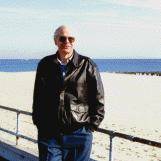
Ted Mooney, P.E.
Striving to live Aloha
(Ted can offer longterm or instant help)
finishing.com - Pine Beach, New Jersey
A. Sir:
The nickel cake you speak of is likely nickel powder, zinc chloride, ammonium chloride, all mixed into a wax "block." In the USA this type of product has/is being used but in a larger block of 500 grams. I do not know of any safety study to determine the airborne nickel that may/or may not result from the use of these cakes. These cakes are thrown onto the surface of the molten zinc at normal galvanizing temperature and they burn like a fireball. Recovery into the zinc and loss into the air is not known.
The target nickel is normally 0.05% nickel in the zinc and problems occur (e.g. excessive dross, pimples, etc. if 0.06% or higher is attained).
There are other ways to reduce steel reactivity.
Regards,
Galvanizing Consultant - Hot Springs, South Dakota, USA
Q. We are having 9 m length kettle pot, 3 m height and 1.5 m width.
1)To start up plant what is the best ratio of zinc calculation to be added?
2)Lead?How much?
3)Aluminium?
-To maintain flux conductivity, what is the best formula?
-What is the point for pure flux chemical?
ph, density?
Thanks/Regards
PJ
- Rawang, Selangor, Malaysia
Q. Hi, recently I added a product called "nickel cakes" into the zinc bath. But now, after dipping all these products have brown stripes on the surface.
1)Nickel contain in the zinc bath is 580 ppm.
Can anyone help me -- what are these brown stripes and why do they appear?
It is "tiger stripes"?
Thanks/Regards
Paramjeet
Galvanizing - IPOH, PERAK, MALAYSIA
A. Sir:
On finishing.com I used the term: "Tiger Stripe" in describing the look of properly fluxed (with quadraflux) steel sometime in the past. My term does NOT describe galvanized product. I have already previously responded to this thread about wax nickel powder bricks.
The "easy" answer to the stripes on your galvanized coating is that the nickel is not evenly distributed throughout your zinc. If this is the answer, then the stripes should go away after a few days of galvanizing. Your nickel in the zinc, by your numbers, is 0.058% nickel (move the decimal four places to the left to convert from ppm to %). The recommended is 0.05% to not exceed 0.06%. It would be informative to know how much nickel you added by the nickel powder wax bricks.
Regards,
Galvanizing Consultant - Hot Springs, South Dakota, USA
Q. Hi Dr Cook,
Good day to you.
May I ask if Nickel in Zinc increases the fluidity of the bath and thus reduces coating thickness (even on low Silicon steel)? I've not seen anyone mentioning about this in this forum, but have heard many claims from suppliers that it does.
Regards,
- Selangor, Malaysia
March 7, 2013
Q. Hi Dr. Cook,
you mentioned that during production the Nickel addition has to be three times to maintain the level of .05%. Why is it so?
Thanks,
Steel products Ltd - kolkata,w bengal, India
November 22, 2015
Q. Hi, currently we are having white dots on hot dip galvanised finish (otherwise good) products. It appears directly after quenching, and most common thing, it only appears on top edge of guardrails.
Can anyone help me on this?
Thanks
- Selangor, Malaysia
May 12, 2016
by Kuklik & Kudlacek
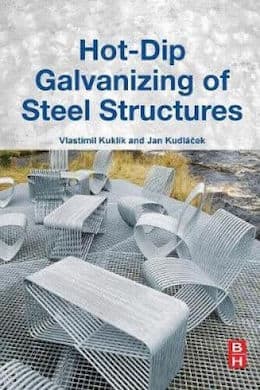
on eBay or Amazon
or AbeBooks
(affil link)
A. Hi Samuel. I am not a galvanizing expert and will have to wait for someone who is.
But meanwhile, I noticed that, out of the many threads we have on hot dip galvanizing, you chose to add your inquiry to this particular one. So I'm guessing that you suspect that your aluminum or nickel content may be causing this issue? In which case, please tell us what your aluminum and nickel content are. Thanks.
Regards,
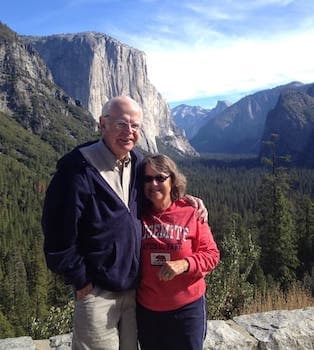
Ted Mooney, P.E. RET
Striving to live Aloha
(Ted can offer longterm or instant help)
finishing.com - Pine Beach, New Jersey
A. Pictures will help diagnose this problem. It could be many things. Please list all operating parameters.
Flux type, chemistry strength and temp.
Zinc chemistry and temp
Immersion time.
Quench type, chemistry.
Trying to diagnose a problem described as sparingly as you have done with so little information is like going to the doctor and saying "it hurts, please fix it".
What? where? when? etc
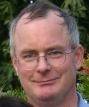
Geoff Crowley
Crithwood Ltd.
Westfield, Scotland, UK
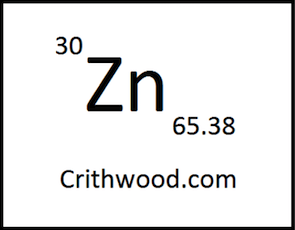
A. I am unable to understand the problem. Pictures may help us.
It can be because of base material chemistry, Zinc bath chemistry, dipping time, Quenching, many reasons.
Do one thing:
1. lower the zinc bath temp to 445 °C. Do not add any Ni or Al. and try.
Galvanizers & Consultant - Delhi. India
A. Mr. Samuel Singh,
It seems that there is some unwanted substance (Ca,Na) in your Quench tank. Please check TDS in quench tank. Minimize chloride carry over in Quench tank. You can try water softener and chloride remover to resolve the problem.
Your flux chemistry can be cause of the problem. It is advisable to maintain ratio of flux ingredients.
- Vadodara, India
----
Ed. note: Here is the graphic for Samuel's problem. Apologies. It was submitted under a different user name than Samuel's posting and we did not initially know what it was :-)
A. Firstly this issue of "white dots" doesn't cause the finish to fail to pass ISO 1461, it is still within the standard.
But you might have a customer who has stated a requirement above and beyond the international standard?
If so, the post above suggesting quench contamination seems the most likely.
Something dissolved in the quench is drying onto the surface, but that's pretty normal, and many galvanizers and most customers would wonder what you're worrying about.
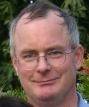
Geoff Crowley
Crithwood Ltd.
Westfield, Scotland, UK
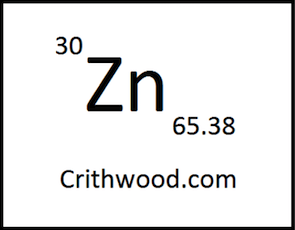
Kettle surface oxidizes immediately, leaving oxide lines on galvanized coating
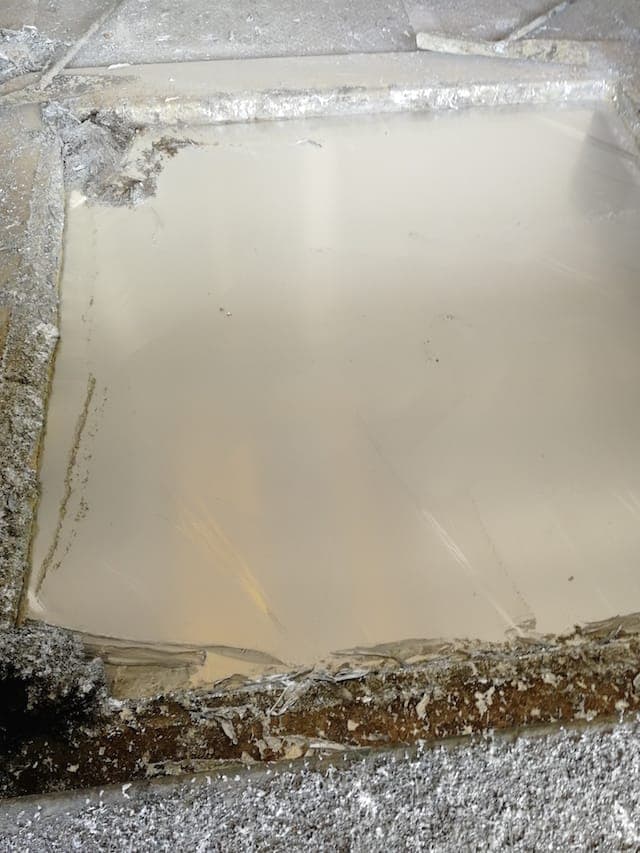
Q. Dear sir,
We are Galvanizing light steel items - 2mm thickness -. These days we having a problem of zinc surface at kettle top get oxidized immediately after skimming and will withdrawal of articles out of kettle. It gives crossing oxide lines of the Galvanized coating. Some of our customers complain about the appearance. Could you please give a suggestion how to reduce the oxidation rate of molten zinc surface.
We are a manufacturer of cable tray systems. We are operating vertical galvanizing furnace. From time to time we are asked by our marketing team to supply some samples for new customers. They need a very shiny coating free from oxide lines. Recently we start facing an excessive oxidation lines on the Galvanized coating.
We're adding aluminum scrap wire to molten zinc to achieve the needed shininess. In the last few days we noticed that within a minute after skimming, the surface of molten zinc get oxidized -- a thin layer of skimming appears. Our working temperature is 445 to 456 °C.
What is the recommended temperature to reduce the rate of molten zinc surface oxidation? And what elemental additives could be used to have attractive zinc texture?
Bahra - Jeddah
February 15, 2018
A. Hello Mr. Abdallah, oxidation rate of kettle surface can't be efficiently reduced through changing the bath temperature (in fact you will create more additional problems...) but avoiding the excessive moisture that enters the area above the kettle (wet material, drying over the kettle, air currents if kettle is not enclosed).
Also, prefer using pre-alloyed ZnAl rather than aluminium scrap as control of surface oxidation (if well dosed) will be much better.
- Hagen, Germany
Q, A, or Comment on THIS thread -or- Start a NEW Thread