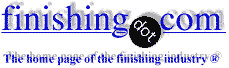
-----
Hot Dip Galvanizing: Reduce and Remove Zinc Dross

Q. Good day
We are a wire manufacturing company in South Africa and run a continuous galv line of 36 lines. Sizes ranges from 1.35mm to 6mm wire. Our wire gets cleaned through a pickling line which after the flux bath commence. We filter our flux bath through a flux filter press process on a continuous basis and flux composition and pH are well controlled. We have a steel bath of about 120t of zinc. our production levels are round 3200t of coated wire per month and the average DV is 145. since the inception of our flux filtration we have seen a significant reduction in our bottom dross which we are very pleased with, however an increase in our top dross. The bath is covered with vermiculite and we dross small amounts of top dross every day. We are however worried about the increase in top dross and would like to get some input on this.
- Gauteng Johannesburg, So. Africa
January 17, 2024
Q. Hello,
I would like to ask you to help with ideas regarding reducing of hard zinc (Dross). We have hot dip centrifugal galvanizing plant with shift capacity of 20 t. Standard galvanizing temperature is 535-540 °C. We have indirect heating system with 4 burners (the surface of zinc is heated and transferred under level of zink.
Flux has less than 1% of Fe. Our current dross % is 2,2 -- it means 22kg/1t galvanized material. 95% of our production is railway crews - bolts , 1000 t / month.
Is it a problem of chemical consistency of incoming goods (bolts) releasing too much Fe or low temperature for galvanizing?
If we increase temperature to 550 °C, not enough microns on galvanizing material base on ISO 14001 average 55 microns.
- Hustopece, Czech Re[ublic
January 26, 2024
⇩ Related postings, oldest first ⇩
for Engineers, Shops, Specifiers
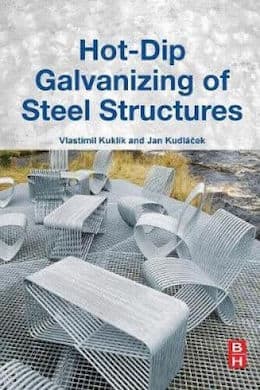
avail from eBay, AbeBooks, or Amazon
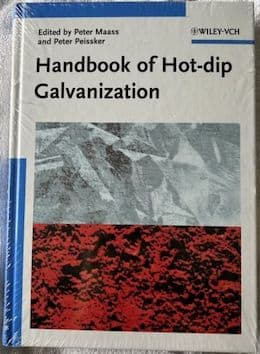
avail from eBay, AbeBooks, or Amazon
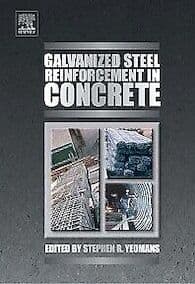
avail from eBay, AbeBooks, or Amazon
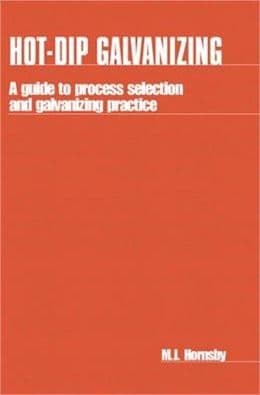
avail from eBay, AbeBooks, or Amazon
avail from Amazon
"User's Guide to Hot Dip Galvanizing for Corrosion Protection in Atmospheric Service" by NACE (1997 only rarely avail.)
avail from AbeBooks, or Amazon
(as an Amazon Associate & eBay Partner, we earn from qualifying purchases)
Q. Hello,
I'm having right now big problems with the dross in my galvanizing plant and I think someone here with more experience and acknowledge could help. First of all, I'm using high speed burners (heat the air that moves around the kettle with high speed) to control the temperature of the kettle, which is like 450 °C (working temperature). Sometimes the temperature rises to 460-468 °C and the burners stop and wait until temperature decreases.
I take out dross 2 times a month with a shovel, if anyone wants to see it could send a picture of it, but I'm not sure if it is really the appropriate tool or device to do this and I think it is not working because the production of Dross is excessive. I see the liquid zinc on the surface but when I introduce a steel round bar to measure the level It feels kind solid or clay inside and I have to push the bar to the reach the bottom. As a result of this clay or solid zinc, the useful level reduces a lot.
For the flux, I'm using a combination of water, ammonium chloride and zinc chloride. I believe that I'm introducing to the kettle a great amount of free iron particles that sticks to each material in the flux.
I need to remove the dross from the pot and the reduce the production of dross.
Engineer - Barranquilla, Colombia
January 20, 2010
![]() |
A. Sir: Galvanizing Consultant - Hot Springs, South Dakota, USA A. There are two main systems of dross removal; ![]() Geoff Crowley Crithwood Ltd. Westfield, Scotland, UK ![]() |
Q. We normally do drossing every 4 months. With an average of dross of 18 tons every 4 months.
1) Will there be any quality problem on galvanizing products?
2) Any problem on hot dip kettle?
Based on monthly, our total output is 1200 mt average and dross ratio is 4 ton every month. I'm thinking to do drossing weekly.
Can someone suggest the best way to do drossing?
Thanks/Regards
Jeet
Galvanizing - Klang, Selangor, Malaysia
November 26, 2012
A. 4 months is way way too long a gap for drossing.
Do it little and often.
Weekly or fortnightly is best.
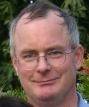
Geoff Crowley
Crithwood Ltd.
Westfield, Scotland, UK
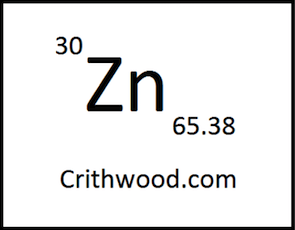
A.
1. Do you add lead to your kettle?
2. Have you checked your flux for iron content?
3. How often do you clean the water tank after pickling and before fluxing?
4. Do you check in the kettle twice a day if any dipped material has slipped in the kettle or not?
5. Have you checked for iron content in the zinc? It can be done by spectro.
See when you have excess of dross it sticks onto material that you are dipping. Secondly you are doing 1200 tonnes, so once in a month drossing is sufficient.
- Mumbai, India
February 23, 2013
Q. I am connected in a galvanizing firm producing 55% Al and 45 % zinc (galvalume)
How frequently should my dross removal be done? I'm operating at 21 tons/hr and producing 8000 tons/month on an average?
How to remove the dross? What's the procedure because we are doing the scooping once a month but the dross accumulation now in my kettle is very thick including the sides of the kettle approximately 60 mm thick from the wall?
- Trece Martirez city Cavite Philippines
July 17, 2013
A. Sir:
There are two types of dross using galvalume:
1)iron/zinc dross with about 6% iron and the rest zinc.
2)iron/aluminum dross and I do not know the composition.
The first type generally sinks to the bottom of the kettle whereas the second type floats on the zinc. Having a "dross" thickness of 6 mm on the sides of the kettle is likely problematic as the inside kettle walls may get too hot and burn a hole in the kettle walls. I have never worked with galvalume so it is likely I am not able to advise, although I have a kettle wall scraping device that works very nicely to remove dirt/ash/flux residue, etc., off the kettle walls. If the "dross" is not too tightly bonded to the kettle walls perhaps the device could work.
Regards,
Galvanizing Consultant - Hot Springs, South Dakota, USA
Q. I've read here discussing about dross pump, will it work in a galvalume kettle? It's true that there were accumulated scales in our snout and definitely it falls on the kettle bottom and accumulates forming a hard material like a bottom dross.
Arlene Canarias [returning]- Trece Martirez city Cavite Philippines
Q. Sir my question is that ammonium chloride sublimates at 388 °C and the furnace temp. is almost 468-480 °C, then how can it (ammonium chloride) reduces dross production if its sublimates at 388 °C? Exactly what reaction occurs between ammonium chloride and zinc, resulting in less production of zinc dross?
Priya Bhardwaj- HARIDWAR, U.P. INDIA
September 8, 2013
How many zinc ingots will be consumed in galvanizing 605 MT and drossing?
Q. `Dear Sir,
We have galvanized 605 mt of steel, what is the amount of zinc ingots I need to add after drossing to give me the same level of molten zinc in my kettle before drossing?
- Lagos Nigeria
July 29, 2016
Hi Bola. I don't know much about galvanizing, but it seems to me that your equation has too many unknowns to be solvable.
Regards,
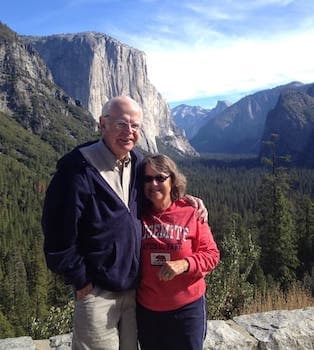
Ted Mooney, P.E. RET
Striving to live Aloha
(Ted is available for instant or longterm help)
finishing.com - Pine Beach, New Jersey
![]() |
A. Hi, Mr Bola, - Vadodara, India A. Yes, too many unknowns. ![]() Geoff Crowley Crithwood Ltd. Westfield, Scotland, UK ![]() A. What I summarise: I am sure that you are talking about Structures Galvanizing Plant. - Delhi. India |
Q. Dear Sir, can you tell me after how many days DROSS is supposed to be removed from ZINC BATH?
SATISH KORI- JABEL ALI, DUBAI, UAE
January 6, 2018
Q. Dear sir,
I'm operating a vertical Galvanizing kettle. Its depth is 4000 mm. We face excessive dross pimples on the Galvanized coating. We did drossing, using a dross grab, twice but still having same problem. We used potatoes to float unsettled dross. Finally, we started pumping compressed air -- contains almost 80 % nitrogen -- in the presence of Aluminum. It gave us excellent result.
My question is, is there any risk for kettle safety from compressed wet air?
Mohammed Farouk AbdallahBahra Cables - Jeddah, Saudi Arabia
February 13, 2018
A. I have used nitrogen in zinc bath; it reduces zinc consumption. Though many will argue that it will eat your kettle walls, I have not seen anything. Pimples can also be because of improper pickling of the material. Second you need to check your acid and flux for iron content; high iron content in flux tank will lead to eventually adding those free iron particles to your tank. This will result in high dross formation.
Vishal AgarwalINDANA STEEL PVT.LTD - Mumbai, Maharashtra, India
A. I would not put compressed air into zinc. While it certainly is 80% nitrogen, its 20% oxygen. That will react with the zinc consuming it, producing oxides that will flat to the surface, wasting zinc, messing up the surface.
Using pure nitrogen is different. We do this at same time as drossing and aluminium additions (just after) and find it helps even out the chemistry, and that results in less dross floating, more uniform aluminium distribution and nicer finish.
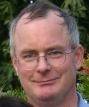
Geoff Crowley
Crithwood Ltd.
Westfield, Scotland, UK
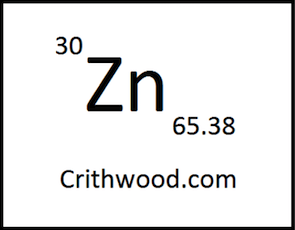
Q.
I'm having right now big problems with the Bottom dross in my Galvalume ^ aluminum-zinc hot dip line and I think someone here with more experience and knowledge could help me. First of all, I'm using Induction pot (with 4 inductors) to control temperature of the kettle (pot), which is like 605 °C (±5°) working temperature).
This pot is the second pot on the line. The previous pot was emptied of melt after 3 years (100,000 ton of product). The bricks and refractories of the body were repaired. The inductors were replaced and melting of Galvalume ^ aluminum-zinc hot dip ingots was performed again. But the current pot, after 45,000 tons (1 year), contains a lot of bottom dross. Bottom dross focuses more on the walls, especially at the corners. During the last 4 months with using the drosser equipment, the bottom dross has been collected many times, but after a short time large volumes of drosses are replaced.
Current bottom dross is so much so that the equipment (especially Sink roll and stabilizer) sometimes do not fall into place. I need to remove bottom dross from pot, please guide me.
- Iran- Qazvin City
April 4, 2021
A. Captain Obvious here.
(1) You are having technical problems with 'Galvalume'.
(2) Galvalume is a licensed process and they provide technical support to their licensees.
(3) Galvalume has no licensed applicators in Iran per their website.
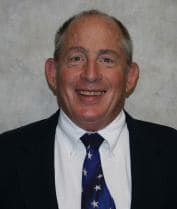
Tom Rochester
CTO - Jackson, Michigan, USA
Plating Systems & Technologies, Inc.

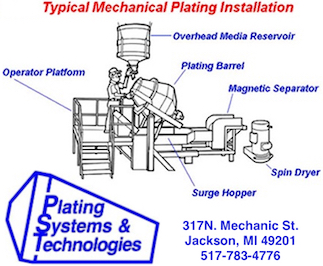
Thanks Tom. Indeed, Galvalume® is a registered trademark, and "BIEC International Inc. is the worldwide licensor of the technology and know-how associated with 55% Aluminum-Zinc alloy coated sheet steel (better known as GALVALUME)."
We want this site to be as helpful as possible, but don't want to contribute to dilution of trademarks nor to facilitate crowd-sourcing of trade secrets. It can sometimes be easy to discern them, and sometimes difficult :-)
Thanks for pointing out that an Aluminum-Zinc installation in Iran is probably not 'Galvalume'.
Luck & Regards,
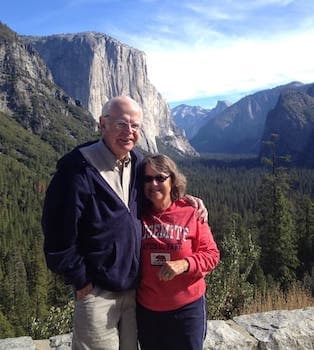
Ted Mooney, P.E. RET
Striving to live Aloha
(Ted is available for instant or longterm help)
finishing.com - Pine Beach, New Jersey
A. Dross always is a problem for strip galvanizing. There are several factors you can check as below,
1. Degreasing section: Please check degreasing result is ok or not.
2. Furnace section: Adjust O2 and H2 to reduce oxidation.
3. Pot section:
3.1 Charging alloy from pre-melting furnace instead of directly (if happened)
3.2 Control the pot temperature strictly. For example,600°, solubility of iron is 0.463%, 608°, solubility of iron is 0.500%. If pot temp. was changed from 608 to 600, then 0.037% Fe becomes dross, even temp. was increased from 608 again, dross still there.
3.3 Air knife system: First, better air knife design will reduce dross. Second, change normal air to Nitrogen can reduce dross also.
Integrated supplier of Galvanizing - Shanghai
⇦ Tip: Readers want to learn from your situation;
so some readers skip abstract questions.
Q. You are adding nitrogen in zinc kettle? In which form? Either it's in liquid form or in gas form?
Is there any effect of nitrogen on zinc coating or percentage of zinc usage?
How do we reduce zinc coating on material with using nitrogen?
Please give me a suggestion.
Employee - Maharashtra
December 15, 2021
A. You didn't explain your circumstances well, are you in continuous strip galvanizing, or batch? In batch galvanizing, Nitrogen is added to make the zinc melt homogeneous. It doesn't save zinc.
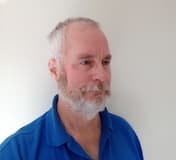
Geoff Crowley, galvanizing consultant
Crithwood Ltd.

Bathgate, Scotland, UK
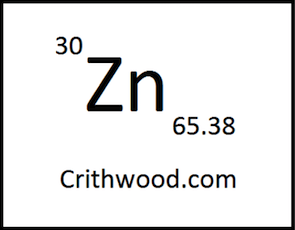
Q. We have batch galvanizing plant.
We want to add nitrogen in kettle for quality work.
So we have already adding aluminium in kettle.
But for to reduce percentage zinc usage in product, we want to add nitrogen.
So in which form nitrogen added in kettle?
In liquid nitrogen form or pure nitrogen gas form?
And how much nitrogen added in kettle daily?
Please tell me sir
Employee - Maharashtra
December 31, 2021
A. Nitrogen isn't used to reduce zinc consumption, it is used to stir the zinc after drossing to achieve homogeneous mix. You might have added Ni, Al, Pb or perhaps some other alloys, but these can separate out a bit. Bubbling gaseous N2 through a steel pipe leading the gas to the bottom of the kettle will agitate the bath and mix it well.
But this doesn't reduce zinc consumption.
It is not done daily, but perhaps after each time you remove dross, which might typically be every week or 2 weeks. About 1-2 m3 of gas can be bubbled. It is not absorbed by the zinc, merely bubbles up and so stirring the zinc. The reason for using N2 is that it is inert to zinc, and unlike compressed air, will not oxidize the zinc as it rises. You could equally use Ar, but that costs more.
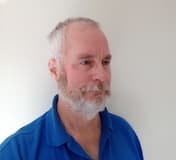
Geoff Crowley, galvanizing consultant
Crithwood Ltd.

Bathgate, Scotland, UK
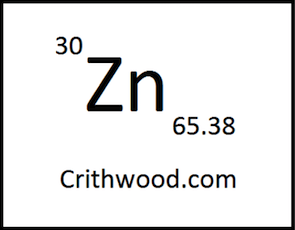
Q. We are facing a lot of drossing in our Zinc bath with the below condition.
Flux - Iron content 0.05%, Temperature of flux tank 40 °C and our dryer temperature 110 and using Hindustan Zinc with 99.99 purity. Also in bath chemist lead shows 0.05%.
Can some one please to suggest to reduce the Dross.
Employee - Pondicherry , India
March 18, 2022
A. You didn't say how much dross. It might be that you are not making an unusual amount and it might be normal. Dross production is often reported as tonnes dross per tonne of steel galvanized.
Best to know if there is a problem before trying to solve it.
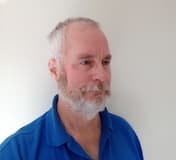
Geoff Crowley, galvanizing consultant
Crithwood Ltd.

Bathgate, Scotland, UK
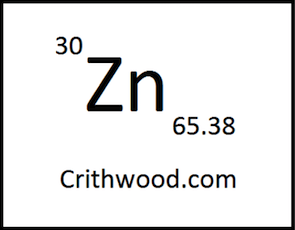
⇦ Tip: Readers want to learn from your situation;
so some readers skip abstract questions.
Q. Dear sir,
I need to know what should be ideal frequency of drossing in a galvanizing bath with no flux blanket.
I need the documentary evidence / references for the same.
Please Reply ASAP
Regards
- Ajman UAE
October 27, 2022
A. You are unlikely to find "documentary evidence" for answers to this question. But the answer is "it depends".
It depends on tonnage galvanized, time, temperature operated at, and type of steel galvanized. Generally though, a time based frequency of not more than 3 weeks, and a tonnes based frequency of 1000 tonnes. In other words, every three weeks or every 1000 tonnes, whichever comes first.
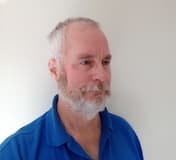
Geoff Crowley, galvanizing consultant
Crithwood Ltd.

Bathgate, Scotland, UK
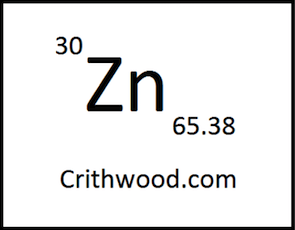
A. Dear Friend.
Drossing cycle will be based on your Production cycle.
It's better to do drossing every week or maximum by 10 days for better efficiency.
Gunatit Builders

Manjalpur, Vadodara, Gujarat
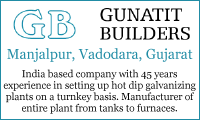
Q. Dear Sir,
I am into the production of Low carbon annealed and hot dip galvanized wires. The wire diameter ranges from 1.40 - 4.00 mm. The line DV is 150. (Divide 150 by wire dia. and get linear speed in meter / min. for each wire diameter).
We have a ceramic zinc bath which is top fired. The 2 burners are mounted on the opposite sides of the hood and heating and melting is through convection. We went for ceramic bath to avoid hassles of metal tank replacement every 1-2 years. Also, dross formation in metal bath is more as compared to ceramic bath. Not talking about ash formation here as the prime concern is dross formation.
The amount of dross we generate is somewhat abnormal. We remove dross once a month and it is about 15 tons and we still feel that more can be taken out. Seems like a bed of clay / sand has formed at the tank bottom. To produce around 1500 tons of galvanized wire, we are generating 15 tons of dross per month which is around 1% of the production. Is quite high. What could be the possible reasons?
We use perforated spoons to remove dross. Our flux tank temperature is 60 deg.C and we maintain zinc chloride and ammonium chloride in the ratio of 1:2. Specific gravity of flux as maintained is 1.10. Drying oven temperature is around 200 deg.C. We have air wipes between the flux exit and drying oven. Zinc bath temperature is 450 deg.C (+/- 5 deg.C). We cover the molten zinc surface with coarse grain vermiculite. Zinc bath burners are nozzle mix type and fired with LPG. The molten zinc temperature is measured by a thermocouple inserted in a DSQ steel tube.
Please help on reduction of dross generation.
Regards,
- Thika, Kenya
March 24, 2023
A. Several things occur to me about your description of your setup. (thanks for a good description, it helps those trying to help you to understand)
You said you have an air knife between flux and dryer. Would this not just remove the flux from the wire? So that the wire enters the dryer with almost no flux? And so with no flux on rusting starts, and Fe2O3 formed would help make more dross in the zinc.
Then you said the flux density is 1.10. That sounds a bit low. Density is a measure of the strength of the flux (and easy and quick way to estimate strength), but a more normal SG would be in the range 1.19 to 1.22. 60 °C for flux is OK, but with that air knife removing it, why bother fluxing? The job that flux does is at the kettle. To reduce water in the flux, the wire is best dried (as you do), but you want the dissolved NH4Cl / ZnCl2 to remain on the wire to do its job at the immersion into zinc.
You mentioned having a ceramic kettle to avoid having to change the kettle every 2 years. Depending on your production level (you said 1500 t/ month), then a steel kettle could last 8-10 years. Something is wrong if you're only expecting 2 years.
15 t of dross a month is high (from 1500 t wire). For your plant size I'd expect more like 0.75%, not 1.0%
What is your flux %Fe?
You said the dryer runs at 200 °C. That is too high. 120 °C is about the max. The reason is that as the water evaporates leaving crystalline flux behind on the steel (normally, perhaps not if your air knife removed it!), then if you heat the wire too hot, then the water of crystalisation boils off exploding the flux into powder, none of it still on the steel.
But you didn't say where that temp is measured? Is that air temp in the drier at 200 °C or metal temp? It can be OK to have air temp in the drier if the residence time of the product is so low that the flux doesn't get burned off as the steel doesn't get hot enough.
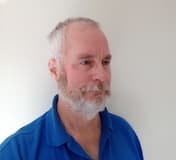
Geoff Crowley, galvanizing consultant
Crithwood Ltd.

Bathgate, Scotland, UK
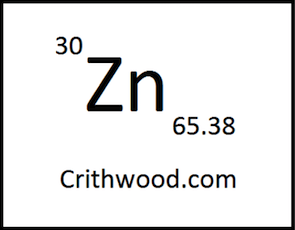
March 26, 2023
Q, A, or Comment on THIS thread -or- Start a NEW Thread