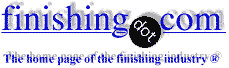
-----
Need dip tank paint to avoid drips sags and runs
We are a custom ornamental iron fabrication shop with some less than satisfied customer complaints with the Powder Coating finishes that we have been contracting out to a reputable firm that has been finishing our iron work for the past 15 years. The past five years we have had many call backs with the finish coming off, and the firm will only offer a one year warranty. I have paid many times out of pocket to have the iron work removed, stripped, and recoated, and reinstalled. I need an alternate low cost method to finish the iron work by spraying or dipping, my concern either way is drips, runs, and sags in the finished product. Many of the pieces have a lot of ornate forged, and cast pieces that could be difficult to reach with spraying technique unless there is a better paint that is designed to reduce this from occurring.
The dip method is something we may be able to do, but it will limit us to the size and configuration of all of our pieces. Since we do out source our Powder Coating on our product, the travel time is about one hour to and from the company that does our work, then another trip to pick it up when it is ready. With today's economy we need to save the customer as much as possible and begin to put some profit back into the business, and avoid having to apply the finish twice. Being able to locate a suitable alternative would get us going in the right direction. The powder coating firm does a beautiful job with the finish work, the problem is it just will not stay on the steel wrought iron, that we install outside, of course it is not even a issue for the interior work. We are not near the coast line, nor even subject to pool conditions (most of the time).
Any advice to begin searching the best paint and or methods of application, or per-cleaning to iron components before assembly which may help to improve the life span of our product, and inhibit rust from occurring causing the callbacks.
My company has been in business since Oct. 1982 and we elected to outsource our paining needs until now, I think that we need to bring the control back under our roof.
Looking forward to some comments and direction of proven methods for the ornamental iron industry.
Kindest Regards,
- Carthage, North Carolina, USA
January 4, 2010
First of three simultaneous responses -- January 5, 2010
Powdercoating onto steel wrought iron and cast with some corrosion protection is sure to fail. It will look really good, but only for a few months, after which the coating (which is slightly porous, as are virtually all paints) will allow water to meet the steel/iron and cause rust to start, and this in turn causes delamination of the coating.
In my opinion the only answer is galvanizing before coating. Using this 2 stage process (galvanizing then powdercoating), with an extensive pretreatment to ensure the powder adheres to the zinc, a finish that lasts for >25 years (guarantees for 25 years available).
Its likely that someone near you can do this too, but its not cheap, certainly not as cheap as PC on bare steel, but it never needs redoing within decades.
This process isn't some rare specialist one, though must be done competently. Many hundreds of tonnes of such fabrications as you describe, from the materials you use, are coated every week in the UK. You might have to enquire of the galvanizer first to find out if they do this, or if they work in cooperation with a powdercoater.
Coating coming off within a year as you describe probably means wrong process. If you use paint systems, you'll have the same issues.
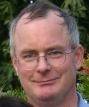
Geoff Crowley
Crithwood Ltd.
Westfield, Scotland, UK
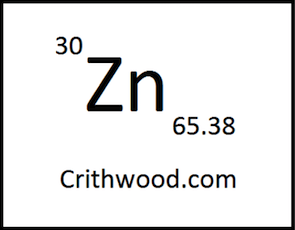
Second of three simultaneous responses --
Have you asked your painters what they could do to improve the outdoor product? Seems like they run the same pretreatment process on all of the fencing. For outdoor durability you will need zinc instead of iron phosphate. Adding another step isn't what you're looking for but if you bring everything in house and do what they are doing you will get the same results. Nothing cuts cost better than eliminating the reworks.
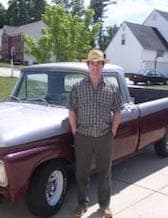
Sheldon Taylor
supply chain electronics
Wake Forest, North Carolina
January 5, 2010
Third of three simultaneous responses --
My advice would be stay with PC as it offers far superior weathering characteristics. The disbondment during its external life depends upon the thoroughness of the pre-cleaning and anti-corrosion preparation. Applying powder direct onto metal for exterior work without a phosphate pre-treatment is not recommended.
The ideal finish would be to galv, phosphate pre-treatment then PC with an architectural quality polyester powder. This should offer 25+ years of service.
Birmingham, United Kingdom
January 5, 2010
"Disbondment"? Are you making up words again Terry? :-)
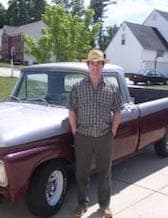
Sheldon Taylor
supply chain electronics
Wake Forest, North Carolina
January 7, 2010
Nah. We Americans have 19,000 words; the British have 78,000. Disbondment is just one out of nearly 60 thousand they hadn't sprung on us yet. Like in a British movie -- just when you get to the good part you can't understand another word.
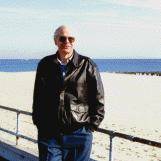
Ted Mooney, P.E.
Striving to live Aloha
(Ted can offer longterm or instant help)
finishing.com - Pine Beach, New Jersey
January 7, 2010
January 8, 2010
According to Google there are 25,200 references to the typed in word "DISBONDMENT"... for instance your own ASTM G95 -07 states:
Standard Test ASTM G95 Standard Test Method for Cathodic Disbondment Test of Pipeline Coatings (Attached Cell Method) , anode, attached cell, cathodic, disbondment, ...
One up to the Limeys :-)
Terry
Birmingham, United Kingdom
Cool. Credit given where credit is due! :^)
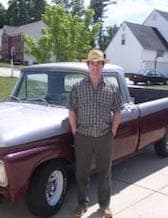
Sheldon Taylor
supply chain electronics
Wake Forest, North Carolina
January 13, 2010
Ted also said the Sierra Club is disbonded, disbonded, disbonded! Well, close to it anyways... Hey, nobody said we couldn't have fun here.
![]() Bob Utech Benson, Minnesota |
![]() Ed. note: Bob is the author of: "High Performance powder Coating" on eBay or AbeBooks or Amazon [affil link] |
Yes, I did repeat it a few times, didn't I? :-)
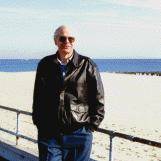
Ted Mooney, P.E.
Striving to live Aloha
(Ted can offer longterm or instant help)
finishing.com - Pine Beach, New Jersey
January 14, 2010
Q, A, or Comment on THIS thread -or- Start a NEW Thread