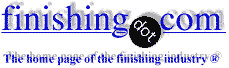
-----
Electroplating thickness for mild steel sheets
Q. Could you give me the standards required for minimum thickness of mild steel sheets using electroplating method. Mild steel sheets is used for cubicle, box, panel.
Mohd Anuar- Petaling Jaya, Selangor, Malaysia
October 16, 2009
A. Hi, Mohd. Your question is a bit vague, in that we don't know what metal you want to plate (zinc?), and possibly even backwards because standards often don't start from the electroplating end but from the product requirements end.
But I would say that, generally, zinc plating would rarely be specified to be less than 0.0002" thick even for mild (interior) exposure conditions.
Regards,
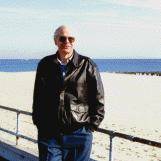
Ted Mooney, P.E.
Striving to live Aloha
(Ted can offer longterm or instant help)
finishing.com - Pine Beach, New Jersey
October 16, 2009
Q. Mild steel sheet I've mentioned earlier is zinc. I've written in my spec the thickness needed is 25 micron. Is it OK?
Mohd Anuar [returning]- Petaling Jaya, Selangor, Malaysia
February 1, 2016
A. Hi again cousin Mohd. The purpose of the zinc plating is corrosion resistance, so without knowing the severity of the environment, it is difficult to suggest the thickness. But I think ASTM B633 is a good guide to zinc plating thickness. It says:
- 5 microns for mild exposure,
- 8 microns for moderate exposure,
- 13 microns for severe exposure,
- 25 microns for very severe exposure.
If these cubicles, etc., are outside, 25 microns is probably right. If they are for interior use, 25 microns sounds like a very generous thickness. It is probably not practical to zinc electroplate beyond 25 microns thickness anyway (if you needed thicker coatings than that, another technology like mechanical plating or hot dip galvanizing would be better). Good luck.
Regards,
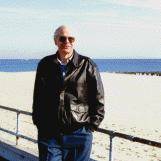
Ted Mooney, P.E.
Striving to live Aloha
(Ted can offer longterm or instant help)
finishing.com - Pine Beach, New Jersey
February 2016
Q, A, or Comment on THIS thread -or- Start a NEW Thread