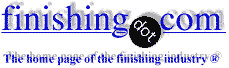
-----
Thermal Spray / Ceramic Spray Q&A's: Metco parts, Blistering, Porosity Issues
Q. Our company is looking for information about a ceramic composite thermal spray powder coating for repair of metal journals on rollers. We have a thermal spray coating process using nylon and tungsten carbide powders and we're looking for sources of the ceramic powder, specifications, and applications. If you see this and can add some understanding, please post a reply.
Thanks,
Larry W [last name deleted for privacy by Editor]- Arlington, Texas, USA
2001
A. Larry,
Hardness does not necessarily equal wear resistance. Armed with that thought, my guess is that a nickel or cobalt with chromium or tungsten carbide would give you a good coating.
MCRAlY (M normally equals nickel or cobalt) chromium, aluminum, yttrium has some nice wear and high temp properties, but is probably a little more prone to chipping and is a lot harder to get identical alloys from one day to the next.
If your current thermal spray rig will not support high energy deposition, I would look at a detonation process, not necessarily a "D" gun, but something that is very high energy. The deposition that you can get from them is an order of magnitude better as it is extremely dense.
Haul out the thomas register and start asking questions. Folks like Metco will bury you with information. I do not remember all of their names, but there are like 5 major players in the field of high energy.
James Watts- Navarre, Florida
2001
A. Try Praxair too.
Jerry Wilkins- Paducah, Kentucky
July 14, 2012
Need 7MR Power Supply 380v, 50 hz, 3 phase
RFQ: Power supply for Metco 7MC plasma controller, set up for 380 volts, 50 cycle, 3 phase operation.
James E. Baker- Cincinnati, Ohio
2003
Ed. note: This RFQ is outdated, but technical replies are welcome, and readers are encouraged to post their own RFQs. But no public commercial suggestions please ( huh? why?).
Need Metco plasma 7MC Unit
RFQ: Need Metco 7MC Console unit only.
Ken N [last name deleted for privacy by Editor]Metallizing - Houston, Texas
2004
Ed. note: This RFQ is outdated, but technical replies are welcome, and readers are encouraged to post their own RFQs. But no public commercial suggestions please ( huh? why?).
Sealing ceramic coating porosity from corona discharge
2005Q. Hi everyone,
I work for a company name which is involved in the drinking water treatment and we use ozone for the disinfection of the water.
We actually test a new electrode for corona discharge in the production of ozone,and have some problem regarding the concentration of arc discharge on the ceramic caused by the porosity of the ceramic.The porosity of the ceramic cause that any contaminant in the air reaching the electrode tend to clog the pore and give a way to electrical discharge to concentrate at one point and burn the ceramic.We use a stainless steel tube covered by a layer of plasma sprayed ceramic(Aluminium oxide+titanium oxide+silicon oxide).We seek for a way to seal that ceramic that can withstand high voltage(up to 10 Kv),high temperature(100 to 120 °C).Having good dielectric properties and good ozone resistance,that product must be applied on the ceramic without affecting the properties or integrity of the latter.
We already try with some epoxy,but it tend to disintegrate in the high corona discharge rate.We have heard that teflon or kapton can do the job but we still search for more info on the way we can put it on the ceramic to have the best job that will last a long way.
Thank you for your attention.
Bruno Riberdy- Granby, Quebec, Canada
A. One approach would be to reduce the porosity rather than trying to fill it. Look into higher energy plasma deposition such as HVOF or "D" gun or gator gun or Metco's J gun or whatever the latest is. Except for select uses, regular plasma deposition is in the dark ages of the deposit you need.
James Watts- Navarre, Florida
2005
Q. I forgot to say that one of the contaminant is water,and that the info we have say that the ceramic is able to absorb this one and make a way to concentrate the corona discharge.We treat the air,but we discover after some tries that if something go wrong with the treatment, humidity can still make is way to the electrode.
Bruno Riberdy [returning]- Granby, Quebec, Canada
2005
ERW Galv tube with weld repaired by zinc spraying shows bubbles/blisters after powder coating
Q. We have a problem with our Galvanized ERW Tube after being powder coated. Presently on our ERW Tube Mill our tube is formed then welded. A Metco zinc spray gun then sprays zinc over the un-repaired weld. The tube then passes through a coolant tank followed by sizing, cutting then packing. Some of our tube is then powder coated and when it comes back,there is a bubbling effect of the edge of the zinc spray. This is most prevalent in our larger sizes (25.4 to 50.8 mm) but seems to be OK for the 16.1 mm round. The spray gun we use is a Metco 12E which a zinc wire is feed thru and Mixed fuel (Oxygen/Acetylene)heats the zinc to allow it to spray. Presently we set the height of the gun to one particular height above the tube for all sizes and the zinc wire feed is dependent on how fast the mill is running.
Trevor CollinsTube Mill Manufacturer - Hamilton, New Zealand
July 16, 2009
A. Sounds like out-gassing from the applied zinc coating. The heavier the applied zinc the worse the gassing I suspect?
Try pre-heating the problem items (to remove the air held with in the zinc) prior to applying the powder.
Birmingham, United Kingdom
July 20, 2009
Q, A, or Comment on THIS thread -or- Start a NEW Thread