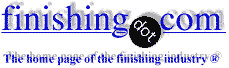
-----
Zinc plating defects (poor quality metal finishing)
Q. Dear Sir,
Shyam Tare Here from Ahmedabad and need your help to understand some issue we are facing after zinc plating.
We observed that after some time of good plated part surface changed to some grayish black spots.
Please let me know reason behind this and how to avoid such issue.
Regards
employee - Ahmedabad, India
September 2, 2024
A. Hi Shyam. We have hundreds of threads about zinc plating problems. Please help readers help you by providing as much basic info as you can: acid, cyanide, or alkali zinc plating ... rack, barrel, or wire plating ... hexavalent or trivalent chromating ... clear or yellow? Is the defect on all parts or only some; has it persisted for months now or a recent change?
Pending personalized answers, thread 55225, "Alkaline zinc plating problem: Black dots/spots that grow with time" and thread 30399, "Black spots on zinc plated parts with trivalent chromate" may be helpful.
Luck & Regards,
Ted Mooney, P.E. RET
Striving to live Aloha
(Ted can offer longterm or instant help)
finishing.com - Pine Beach, New Jersey
⇩ Related postings, oldest first ⇩
Q. We had a housing made from cold rolled carbon steel sheet and zinc plated with yellow passivation.
After opening it recently from the package after three months we noticed some fungus like white powder on the surface of the sheet.The housing was packed in an air tight polyethylene sheet. I would like to know the technical reason for this problem.
Thanks,
Ravi Gsa graphics - Bangalore, Karnataka, India
2004
A. It is, most likely, white corrosion product due either to the poor chromating job or the entrapped moisture (source/origin of which will need further investigation). A chemical analysis/characterization of white powder found on the part will be helpful in determining the root cause.
Raj Singh- Cleveland, Ohio, U.S.A.
2004
Multiple threads merged: please forgive chronology errors and repetition 🙂
Q. OUR ORGANIZATION DEALS WITH VARIOUS TYPES OF ENCLOSURES MADE WITH SHEET METAL (LIKE COLD ROLLED CARBON STEEL SHEETS). I OFTEN FIND DEFECTS LIKE WHITE PATCHES, PLATED SURFACE GETS FADING FEW DAYS AFTER OPENING THE AIR TIGHT BOXES IN WHICH ENCLOSURES WERE KEPT, BLACK MARKS ON THE PLATED SURFACE, RUST FORMATION ON THE PLATED SURFACE.
THE ABOVE ARE SERIOUS PROBLEMS I am FACING IN MY ORGANIZATION.
CAN YOU PLEASE SUGGEST ME THE SOLUTION FOR THE ABOVE PROBLEMS?
CUSTOMER - Bangalore, KARNATAKA, INDIA
July 14, 2009
A. Mr Subramanium
The defects cited by you constitute post and pre treatment faults that tend to show up after plating is over and some time has elapsed. Here is what you can do.
Set up an audit at your vendor after setting up an approved plating procedure.
OR
Change the Plating vendor.
Better still...
Use a consultant to set up the entire Plating process to avoid such problems.
As a buyer you can only conduct retrospective analysis and then arrive at conclusions of probable causes but a short walk down the plating line with a Plating Consultant and observation of work procedures will save you future agony.
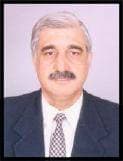
Asif Nurie [deceased]
- New Delhi, India
With deep regret we sadly advise that Asif passed away on Jan 24, 2016
A. Dear Mr Pal,
Are these problems prevalent during the monsoon period? Is your sheet metal of good grade steel? These two things need to be answered before looking at Plating.
Mr Nurie: your pitching so hard for a consultant makes me seriously want to look at an alternative career. Is business really that good?!?
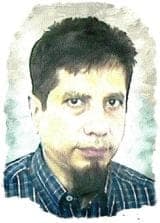
Khozem Vahaanwala
Saify Ind

Bengaluru, Karnataka, India
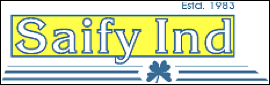
A. This forum is supposed to give free advice. So let us straight go and attend to the problems.
Dear Pal,
You will have to make a visit to the plater and get the details of the supplier of plating chemicals. Call the representative of the supplier and tell him to guide the plater. Check the following:
1.Proper Cleanings are done.
2.Plating thickness is proper (For Zinc 8-12 microns)
3.Chromating is proper
4.See they have good volume of soft water.
5.Proper cleaning after plating and Chromating is a must.
6.Hot water last swill is preferable.
7.Hot air drying is a must.
8.Should not pack air tight immediately after drying. Leave it for 24 hours minimum.
9.Remember to put some moisture absorber like silica gel in the packing box.
Still if you cannot cope with the situation consult Mr. Vahanwala who sits in Bangalore! It seems Mr. Nurie is ready but he stays in Delhi!
Regards,
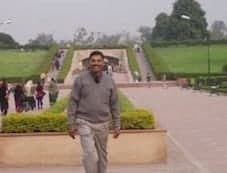
T.K. Mohan
plating process supplier - Mumbai, India
Now that we've heard from the buyer who is encountering the issue, and from a plating consultant, and from a plating shop, and from a supplier of the plating chemicals, every base has been covered :-)
The only summary point I would add is that either:
1). the work must go to a different, better plating shop, or
2). the plating shop must solve the problem, or
3). the buyer must visit the plating shop (whether alone or with a consultant or with a supplier rep) to see the problem and solve it.
I'm sure that every "beat cop" the world over has heard from two men that they were innocently walking on opposite sides of the street, minding their own business, when the other guy violently charged them without provocation.
Similarly, while hints from 3rd parties will help you know what to look for, actually 'walking the line' is usually vital because the "story" and the reality usually differ greatly; often the shop management is unaware of exactly what the foreman or the operators are actually doing which is causing a problem :-)Regards,
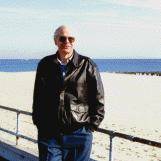
Ted Mooney, P.E.
Striving to live Aloha
(Ted can offer longterm or instant help)
finishing.com - Pine Beach, New Jersey
Post blue zinc plating defect -- rough texture
Q. We read the root cause of rough surface on post plated part was likely due to the plating current.
Why does this happened and how do we over come the situation ?
The rough texture produced could be reworked ?
The defect is only cosmetic or it's rust protection will also be affected ?
Regards !
Ken
Metal processing - Singapore
April 14, 2010
A. Hi, Ken. Rough texture can be caused by "burning" (excessive current density), but I don't think you have given us sufficient information to affirm your conclusion that that is the cause in your case. If the roughness is in high current density areas, and is not related to particulate matter settling on "shelf" areas, and if the roughness of the surface after plating exceeds its roughness before plating, yes, it may well be "burning".
The corrosion resistance may or may not be compromised. But the parts are defective; I wouldn't try to talk myself into them being non-defective by trying to quantify exactly how defective they are. The parts should probably be stripped and replated at lower current. Good luck.
Regards,
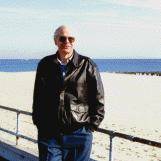
Ted Mooney, P.E.
Striving to live Aloha
(Ted can offer longterm or instant help)
finishing.com - Pine Beach, New Jersey
Zinc plating with Black Passivation defects
Q. I have an issue with Carbon Steel Gauge plates that have been Zinc and Black passivated to 14 um, approx 7-10% of the plates have a white mouldy deposit over the surface.
These have undergone a 1 month sea voyage.
Please advise on what could have caused this, and how to prevent in further batches.
I would suppose the only way to rectify these plates is strip and recoat?
Please see attached Picture.
- Beijing, China
January 24, 2013
Q. We are supplying forged, machined and subsequently Zinc plated parts to our European customers. This part goes into automotive application. The supply quantity is around 1.5 million per annum.
We are testing one piece per batch for salt spray test (as per customer specs) before the shipment and did not find any issues during test time. But in a very few cases (approx.- 25 nos) a gray color patch mark is observed on face of the part.
These parts were wrapped in VCI bag and packed in corrugated box.
It is our experience that such cases are usually noticed during monsoon seasons, i.e., between July to September period.
We need expert advice for cause of the defect and preferred solutions.
Please suggest
Best regards
- RAJKOT INDIA
November 25, 2020
A. Hi Manjunath. I may be jumping to conclusions, but the corrosion pattern in the first picture looks to me like it echoes the shape of cardboard corrugations -- indicating that the parts were touching the cardboard box rather than actually being in a VCI bag, or were wet inside the bag. So the first thing I would suspect is that the packaging is not always done quite as carefully as we might hope, and occasional parts are exposed to moist cardboard boxes.
Luck & Regards,
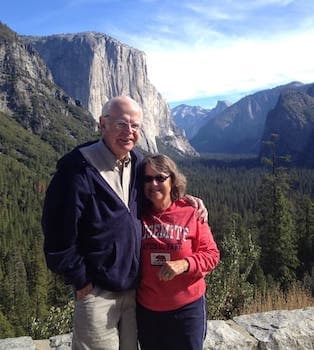
Ted Mooney, P.E. RET
Striving to live Aloha
(Ted can offer longterm or instant help)
finishing.com - Pine Beach, New Jersey
A. Hi Subhasis,
1) use cardboard and pack a few pieces for 72 hours.
2) pack without cardboard some others for 72 hours.
Inspect all parts after 72 hours for black spots, if you have black spot on cardboard use, then a packaging problem; if not, there is not a cardboard problem for black spot, looks like some dripping on parts or touching.
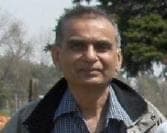
Popatbhai B. Patel
electroplating consultant - Roseville, Michigan
Q. I am new to the zinc coating process and my vendor is not being helpful in coaching me. There are visual flaws and I wonder if someone might be able to call out these issues in the picture with the correct terminology and what might cause the flaw.
I appreciate any "schooling" I could get.
Rex Hyzer- Grand Rapids
June 23, 2021
A. Rex Hyzer,
After zinc plate dull deposit and bright deposit on the same part
Run Hull Cell
⇦ huh?
panel for zinc bath in lab. Check the ratio on panel HCD and LCD , Should be 1: 1.1 OR 1: 1.2, I think you have unbalance brightener chemistry. low carrier( secondary brightener) in zinc bath.
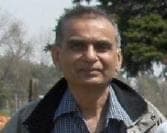
Popatbhai B. Patel
electroplating consultant - Roseville, Michigan
----
Ed. note: This is only one of dozens of threads about zinc plating problems. Please search the site with terms like "acid cyanide, or alkaline", plus "rack, barrel, or wire", plus the specific defect to find discussions about an exact plating problems.
Q, A, or Comment on THIS thread -or- Start a NEW Thread