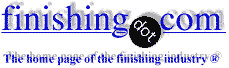
-----
Hardcoat Anodizing by Voltage or by Current?

(to provide context, hopefully helping readers more quickly understand the Q&A's)
Readers who want a quick intro to anodizing, please see our "ANODIZING of ALUMINUM Intro & FAQs". This particular thread focuses on the fact that one cannot anodize at a fixed voltage and suggests what to do instead.
The reason you cannot anodize at a fixed voltage is that bare aluminum is highly conductive so very high current would flow and burn the bare aluminum, but the anodized coating is highly resistive, so as the anodizing film grows, the surface becomes slightly resistive, then more resistive, then highly resistive ... so ever-increasing voltage is needed to keep building the anodized film.
It is theoretically possible to manually adjust the voltage gradually upward, but the responders explain why anodizing by amperage is a better approach.
Q. Hi, I am running an in-house plating shop and I have been asked to install Hard anodising. I used to be a service rep for a chemical company and saw an Anodiser hard anodising some parts and he was ramping up the voltage on his rectifier every 2 minutes to overcome the resistance of the anodic film. Is this a specified process? Or is it trial and error? His work was very good quality and I want to replicate it.
Mark Allabush- London, England
January 12, 2022
A. Hi Mark. We appended your inquiry to a thread on that subject. You will see that everyone does not agree on the precise optimum ramp-up method & values, but all agree on the necessity of generally what you saw :-)
Luck & Regards,
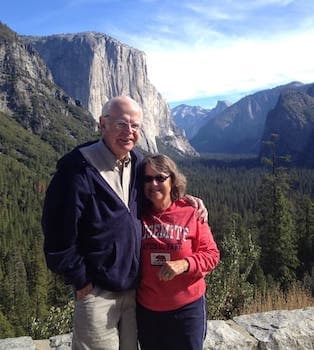
Ted Mooney, P.E. RET
Striving to live Aloha
(Ted can offer longterm or instant help)
finishing.com - Pine Beach, New Jersey
January 2022
January 14, 2022
A. I have tried desperately to find an "artful" way to hard coat by voltage, many do it, but not with consistent results. If you do it artfully by stepping the voltage, then when you cross section and look at the photograph you will see a step in the pore structure for every bump you gave the voltage.
Ideally, you must know the surface area (or use the "Parallel Circuit Method"), know the "target" amperage, spend 15 minutes from zero the target, switch over to current control and let the voltage automatically increase to hold the amperage.
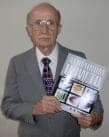
Robert H Probert
Robert H Probert Technical Services

Garner, North Carolina
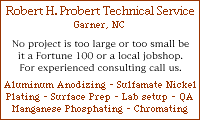
![]() |
January 18, 2022 A. Hi Mark, Chemist - A foresaken rock in the irish Sea A. There is no question about it, using ASF for anodizing type III is the way to go. The only problem is knowing the SQ FT of the parts -- all of them. If you know the SQ FT of one just multiply by the number of parts then use 24 or 30 ASF as the multiplier and then slowly raise the ASF to that number. Make sure your rectifier can gives 35 volts as the ramp requires it. Ramp should be 8-12 min. Good luck ![]() Drew Nosti, CEF Anodize USA ![]() Ladson, South Carolina ![]() January 19, 2022 |
⇩ Related postings, oldest first ⇩
Q. I know that for Hardcoat anodizing one needs a current density 36 ASF. As a job shop, how does one avoid burning parts having operators not calculating the surface area? Is it possible to run Hardcoat based on voltage as in conventional sulfuric anodizing?
Travis MoorePlating Shop Employee - Houston, Texas, USA
June 9, 2009
A. Hi Travis
One of the best ways to avoid burning is by using pulse anodizing. I have written a couple of papers and a book about this.
One of the rectifier companies sells a controller which doesn't need to have a calculation of surface area from the operators.
Running Hard anodizing by Voltage is as bad an idea as it is for conventional anodizing. You use too much energy and the process time is often prolonged so a soft coating is found on the surface instead of a hard.
Sunny regards
Anne
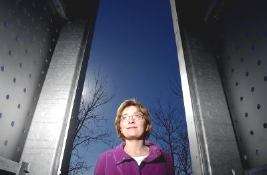
Anne Deacon Juhl
- - Trustrup Denmark
June 12, 2009
June 12, 2009
A. 36 Amps per square foot is fine for production and lab development jobs of all same size where you can tune the free acid, temp, current density for high current; but, a job shop with varying sizes and alloys needs to stick to 24 ASF to stay out of trouble.
There are three ways to get 24 ASF on the load. (1) Measure the surface area, (2) Use the "parallel circuit method" published by Dr Harold Weisner in the 1958 AES Proceedings and plagiarized by me in Aluminum How-To, (3) Using 16 volts for all alloys except 21 volts for 2000 alloys, spend 7 minutes slowly ramping up to 16 volts, now look at the ammeter, note the total amps at 16 volts, spend the next 6 minutes slowly ramping up to EXACTLY TWO TIMES THAT NOTED AMPERAGE, set the automatic current control, walk away; while you are gone the voltage will automatically increase to hold that current steady at 24 ASF.
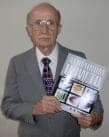
Robert H Probert
Robert H Probert Technical Services

Garner, North Carolina
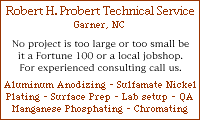
A. Travis
As mentioned, running by volts is not the best way to anodize.
If your operating parameters are sound...
Manually ramp (3-5 minute duration) to 24 volts and hold for 5 minutes. After 5 minutes, increase voltage 2 volts every 5 minutes and continue. Check your thickness when you see fit. Current density will start out < 36 ASF, increase to > 36 ASF, and drop off substantially towards the end of a 2-mil thick run on 6xxx. You can play with the later intervals.
Also consider that burning is typically caused by localized overheating. Do you have enough agitation?
- Colorado Springs, Colorado
June 17, 2009
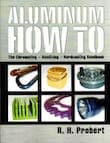
Aluminum How-To
"Chromating - Anodizing - Hardcoating"
by Robert Probert
Also available in Spanish
You'll love this book. Finishing.com has sold almost a thousand copies without a single return request :-)
Q. Thank you for your quick responses. Mr. Probert, I recently purchased a copy of your book and am interested in trying the parallel circuit method. After reading your book I was impressed with its easy to understand methodology. I am curious though; as a job shop, our racking material is almost exclusively 6061 Aluminum. If I were to hardcoat a part that was 2024, the current would be preferential to the rack. Is there any way to mitigate this without buying 2024 racks?
Travis Moore [returning]- Houston, Texas, USA
June 18, 2009
A. Mask the 6061 with platers tape or paint-on maskant. Try heavy anodizing of the 6061, perfect seal, trim off the bare contact marks, rack after clean and deox then quick dip back in the deox. Small parts CAN be hard coated on titanium. The two leading rack manufacturers in the USA do not agree with me on titanium, but there is a limit as to how much it will carry and how wide the contact area must be to get twice the amps.
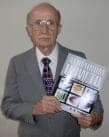
Robert H Probert
Robert H Probert Technical Services

Garner, North Carolina
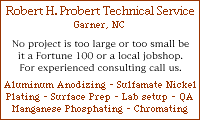
June 19, 2009
A. Hi Travis
You could mask the 6061 racks, or try a titanium rack. I know a lot of people don't like to use titanium racks because it doesn't conduct the current as well as the aluminum.
Titanium racks are useful in a hard anodizing process when 2024 alloys are processed. You just need to be very sure that the contact from rack to part is good.
Sunny regards
Anne
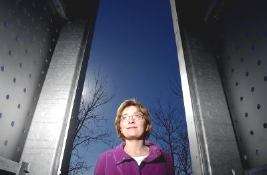
Anne Deacon Juhl
- - Trustrup Denmark
June 19, 2009
Thank you guys for your helpful responses. I am going to try to find some plastisol and mask off that way on our existing 6061 racks.
- Houston, Texas, USA
June 24, 2009
Q. I have been doing hard anodize for quite some time and realize some of the problems especially with 2000 series.
I have been talking to a company who claims to have a hard coat controller that you can enter in your desired thickness and the controller will do the rest. I consider this very unlikely knowing some of the factors we face after running the process. I would like some other opinion about the feasibility of this.
Hard Anodize - Warner Robins, Georgia
March 1, 2012
Q. I want to know the process of hard anodizing in H2SO4 bath.
I have made a bath with 1.15 density. We are processing each batch with 200 pieces each; the area of one piece is 17500 sq mm per piece. Our cycle time is 65 minutes with 400 amp. We are starting at 50 amps and increase 50 amps every 5 minutes to maximum 400 amps, with bath temperature +2 to -2 °C. Is it correct ? Or what should be real process?
- India
June 15, 2012
A. Hi Nilesh.
So the area per load is 3.5 sq. meters (37.7 sq. feet)? If so, the amperage seems low.
I'm not personally familiar with your idea of starting out at very low amperage. Low voltage to prevent burning, yes. But a very long, very slow ramp-up of current seems wasteful of potential productivity. Perhaps those with more hard anodizing experience will correct me.
Regards,
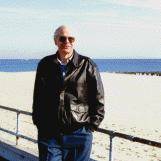
Ted Mooney, P.E.
Striving to live Aloha
(Ted can offer longterm or instant help)
finishing.com - Pine Beach, New Jersey
June 15, 2012
A. Ted is correct, the amperage is way too low. You should be more in the 950-1000 amp range, at minimum (assuming Ted's math is correct). You'll want to ramp to that final current setting amps in about 5 minutes total. That should put your process time at a little over an hour to produce a 50 µm coating (typical hardcoat thickness). You say your cycle time is 65 minutes, at the current settings you mentioned, that should produce approx. a 25 µm coating.
Your temperature is fine. You'll want to keep your dissolved Al content at around 8 gr/lt max.
Those are just the basics.
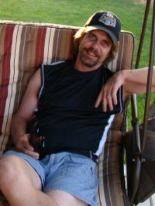
Marc Green
anodizer - Boise, Idaho
June 22, 2012
October 2, 2014
Q. Hope you can shed some light on increasing the primary barrier anodizing layer thickness for increased corrosion resistance to a 5% HCl acid testing in a Type III Sulfuric bath.
We are also trying to increase our dielectric breakdown voltage with increasing the primary anodizing layer.
We have a 15% H2SO4 bath system with cooling at 28-32 °F.
Our materials are Aluminum 6061-T6 forgings with some bar stock.
We are trying an initial ramp of 13 ASF at 13 V for 18 minutes.
The 2nd anodizing pore layer is run at 30-35 ASF with a 12 min ramp and then held at constant current for a total of 63 amps until 60 volts is reached .
Should we alter this approach and include pulse plating or modify the initial ramp rate and current density of 13 ASF?
- redwood city, California USA
A. Hi Daniel. Pending getting a response to your situation specifically, you can read Anne, Robert, and Willie's suggestions on the subject earlier in this thread, and also see letter 13351, "Suggested ASF for hardcoat anodizing". Good luck.
Regards,
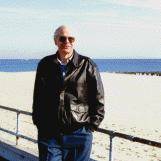
Ted Mooney, P.E.
Striving to live Aloha
(Ted can offer longterm or instant help)
finishing.com - Pine Beach, New Jersey
October 2014
Q. I need to know the percentage of sulfuric acid in water for hard anodizing. I created my own tank to run a few tests but the solution starts eating aluminium within 5 minutes of starting the process.
The tank I used was of 12 x 3 x 3 feet and starting voltage was 15 volt. I ran 3 tests with aluminium but every time the aluminium part starts to get damaged within 5 minutes.
Can you please suggest what is wrong with my process?
- India
May 8, 2017
A. Hi Pradeep. 15% by weight 66 °Baumé sulfuric acid is used for general anodizing and can, with luck, we used for hard coating. However, many if not most people add glycolic acid and glycerin-based proprietary additives to this.
We appended your inquiry to a thread that may help, but I suspect you "burned" the aluminum with too much current. Although the hard anodized coating is of very high electrical resistance, bare aluminum has almost none. So -- while you need a high voltage near the end of the cycle to keep the current flowing despite the high resistance -- at the beginning of the cycle you need a low voltage. Read the earlier responses for specific instructions, but most people solve the problem by limiting the amperage rather than the voltage. Are you sure you have very good local agitation to keep the temperature down to about 32 °F (0 °C) right at the parts?
Please introduce yourself and your situation so we can understand what you probably already know vs. what you might not. Although I don't think someone with no plating or anodizing experience can be taught how to do hardcoating in the few paragraphs appropriate to this public forum, you might already know 99+% of what you need to know, but we can't tell yet. If you have no experience, a 15 foot x 3 foot x 3 foot tank is quite large for introductory experiments.
Luck and Regards,
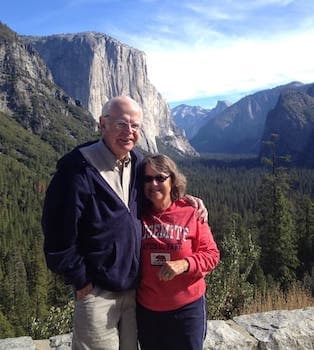
Ted Mooney, P.E. RET
Striving to live Aloha
(Ted can offer longterm or instant help)
finishing.com - Pine Beach, New Jersey
May 2017
Q. We believe we are successfully hardcoating at 65-70 ASF. I am running 65-70 ASF with no issues with burning parts. Are there any other issues that I should be concerned with at such high amperage?
If my parts look good and are passing the Taber test, am I fine to run 65-70 ASF?
- Sierra Vista Arizona USA
April 25, 2018
Q, A, or Comment on THIS thread -or- Start a NEW Thread