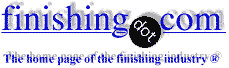
-----
Finishes for Bolts on Galvanized Structural Steel
April 9, 2009
Q. We are a structural steel fabricator/erector out of Detroit Michigan.
We are in the planning phases of a structural steel project. The entire steel structure will be hot dipped galvanized. We would like to use plated ASTM A325 bolts, in lieu of our standard bolts which are usually painted after the structure is bolted and assembled.
All the bolts will be exposed to the elements, but not a salty environment. (West Virginia) Which is the best system to use?
Hot dipped would offer best corrosion protection, but will gum up threads, and proper tensioning of bolts is critical in our industry.
Zinc Plated-These should have less problems with tensioning bolts, but more susceptible to corrosion.
CAD Plated-will cadmium be compatible with the rest of the zinc galvanized structure, I understand cadmium will be the best for lubrication of the threads.
Are there any other downfalls I should think about?
Steel Erector - Detroit, Michigan
A. Mechanical Galvanizing with zinc offers good salt spray (better than hot-dip), good thread profiles, and no hydrogen embrittlement. With a wax, it gives good lubricity. That's why a lot of structural fasteners are done by this process.
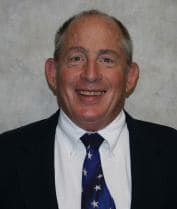
Tom Rochester
CTO - Jackson, Michigan, USA
Plating Systems & Technologies, Inc.

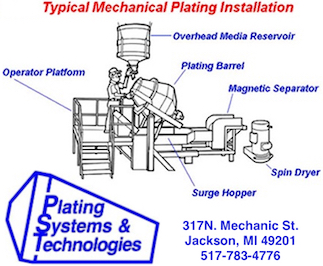
April 28, 2009
A. Zinc plating is OK; the least expensive. Cadmium is very good, but not many platers offer cadmium plating due to the regulations. It is highly toxic. I suggest zinc-nickel alloy + a conversion coating. (Zn-Ni is very corrosion resistant even without a conversion coating.)
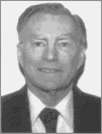
Don Baudrand
Consultant - Poulsbo, Washington
(Don is co-author of "Plating on Plastics" [on Amazon or AbeBooks affil links]
and "Plating ABS Plastics" [on Amazon or eBay or AbeBooks affil links])
April 30, 2009
A. If the parts are Heat Treated, doing the electrical plating is Risk due to Hydrogen embrittlement. to avoid the risk better do some electrolytic method coating like mechanical zinc plating or zinc-aluminum coating
Kannan Boopathi- Salem, Tamil Nadu, India
May 4, 2009
A. Choosing Zn-Ni alloy plate with ~12% Ni and a tri-Cr based seal coat (aka conversion coat) will give good performance and will keep your product "green" versus the choice to go with Ni-Cd or Cd coated parts.
Note that AMS2417 makes no mention of tri-Cr and the most common Type II coating specifies use of a hex-Cr seal -- again, don't go there if you want a "green" stamp. There are numerous coating suppliers using a tri-Cr finish with excellent results and depending on the specific requirements for your parts, barrel plating may be an option. Barrel plating tends to make for a very inexpensive coating operation, though even if rack plating is required, it should still be most viable in regards to cost.
Best of luck,
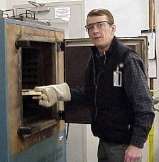
Thomas Hanlon, Materials Engineer
aerospace finishing - East Hartford, Connecticut, USA
June 19, 2009
A. Hi Patrick,
This thread has a lot of time gaps in it, so maybe it's too late to consider more options. But...
Hot-dip galvanizing would be good. Bolts are done by cutting the thread diameter undersize so that the hot dip coating brings them up to size - this is an established practice. Nuts can be galvanized as blanks and threaded afterwards, which avoids the possibility of excess zinc not draining from the internal thread. The absence of zinc on the nut threads is of no consequence, as they are in contact with the zinc on the bolt threads.
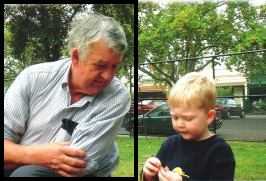
Bill Reynolds [deceased]
consultant metallurgist - Ballarat, Victoria, Australia
We sadly relate the news that Bill passed away on Jan. 29, 2010.
June 19, 2009
A. I would look into a zinc rich dip/spin coating. Specifically you should look into GEOMET, Magni or Dorken. I know that the GEOMET is approved for structural bolts, I am not sure about the others. These finishes offer excellent corrosion protection at a very thin film thickness.
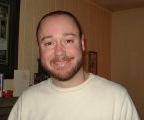
David J. Wolf
Medina, Ohio
June 22, 2009
August 17, 2009
A. Patrick,
Check out my article in my reply to letter 52457. For your application, I recommend hot dip galvanizing, but from a good spin operation. There are a few good spin lines in the USA, which will provide the required bolts.
Regards,
Galvanizing Consultant - Hot Springs, South Dakota, USA
A. I would recommend hot dip galvanized coating. ASTM A153 clearly states that the threads must be clean enough to allow a nut. There are a number of galvanizers around the country qualified to do this job. If hydrogen embrittlement is an issue, have the bolts mechanically cleaned and avoid the acid bath in the galvanizing process.
David JayeHouston, Texas
September 25, 2009
Q. What is the difference between Geomet coating and Hot dip galvanizing? Are Geomet and Zinc flake coating the same? What are the advantages of both? I'm buying some Geomet plus bolts.
Mohammed Afeef- Kannur, Kerala, India
August 3, 2017
A. Hi Mohammed. Geomet is one brand name of zinc flake coatings. We don't compare specific brands against each other on this site, but you can contact the vendors for their sales info about why they think their zinc-rich dip-spin coatings are better than their competitors'. Hot dip galvanized coatings are generally more corrosion resistant and much thicker; that thickness is probably an advantage on large fasteners and a disadvantage on small threaded fasteners.
Regards,
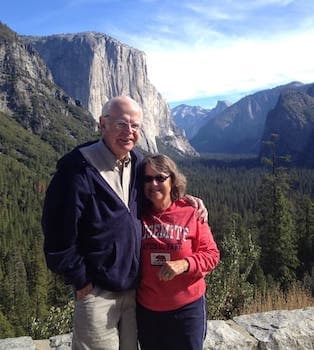
Ted Mooney, P.E. RET
Striving to live Aloha
(Ted is available for instant or longterm help)
finishing.com - Pine Beach, New Jersey
August 2017
A. Dear Mohammad,
Geomet is the proprietary trade name for Chrome free coating from NOF Japan.
Yes Geomet and Zinc flake coating are the same.
The advantages are high corrosion resistance at low coating thickness. A combination of sacrificial and barrier protective coating as well.
Geomet plus bolts have an inbuilt COF reducer that both increases corrosion protection and permits higher torquing allowances.
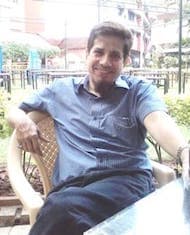
Khozem Vahaanwala
Saify Ind

Bengaluru, India
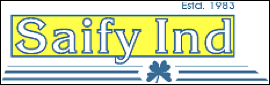
December 14, 2017

Q, A, or Comment on THIS thread -or- Start a NEW Thread