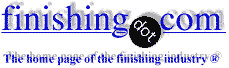
-----
Consumption of iron with hydrochloric acid in galvanizing
Q. Hi,
I'm currently working in hot dip galvanizing unit and I've got problem with the rust consumption by hydrochloric acid. We analyzed our pickling bath every weeks and some weeks for 10 g/L less of HCl we've got 10 g/L more of Cl2Fe some weeks it's 2 or 12 !
The ratio Delta(C(HCl))/Delta(C(Cl2Fe)) should be constant.
Our bath temperature is 20 °C and we've got 110 m3 baths.
student - Troyes, France
April 20, 2009
A. Your question seems to have lost something in translation.
If you are talking about losses of Fe into the HCl in your cleaning (pickle) tanks where you clean the steel before immersing in zinc, then this is normal.
The oxides of Fe on the steel should be dissolved in the HCl forming iron chloride. If you have an inhibitor (a chemical) this will prevent the steel itself from dissolving. If you don't have inhibitor, the steel also goes into solution.
As you clean more steel, then more acid is consumed and becomes iron chloride.
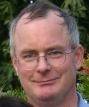
Geoff Crowley
Crithwood Ltd.
Westfield, Scotland, UK
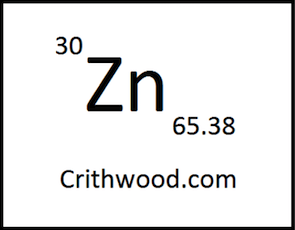
April 21, 2009
Q. I mean between two analysis sometimes for 1g/L of acid spent we've got 1 g/L of Fe2+ more in the bath, but sometimes we've got only 0.5 g/L more or 2 g/L.
Christian Couly- Troyes, France
April 23, 2009
A. Hi Christian,
In order to measure the acid consumption, you are taking the small difference between two large numbers. Whatever analysis procedure you use to measure the acid concentration is, like all procedures, subject to random error. The magnitude of the random error might well be satisfactorily small in terms of the concentration that is being measured. When you take the DIFFERENCE between two concentrations you get a small value for the difference, but the random error applying to that difference is not correspondingly small - it is in fact the sum of the absolute random errors in the two concentrations, so the small value you get for the difference has associated with it a relative error which is vastly greater than the relative errors in the concentrations you subtracted. So the DIFFERENCE calculated for one sampling interval might have a large error in one direction, and for the next sampling interval might have a large error in the opposite direction.
Exactly the same argument applies to the determination of the Fe2+.
Then when you divide the change in Fe2+ by the change in acid, your answer is greatly affected by the high relative errors in the components of the calculation.
This doesn't necessarily indicate a problem with your analytical techniques - the problem is that you are putting an unjustified amount of faith in the precision of the small difference between two large values, for each of the analytes that you are considering.
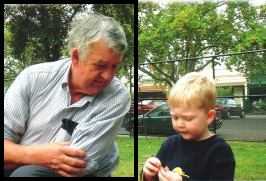
Bill Reynolds [deceased]
consultant metallurgist - Ballarat, Victoria, Australia
We sadly relate the news that Bill passed away on Jan. 29, 2010.
April 23, 2009
A. If I understand the question right, you're saying that you get different answers from your analysis each time.
So either:
1. The analysis technique is faulty, or
2. The sample is not homogeneous.
If you are taking a sample from the tank, then analysing it, and then taking another sample from the tank and analysing and getting a different result, then I'd suspect that your sampling is not giving a representative sample of the tank. Suggests that the tank contents are not homogeneous.
If you take a single sample, stir, take some for analysis, the stir again and take a bit more for analysis do you get different answers? This might help to determine if the analysis technique is faulty or not.
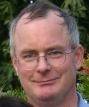
Geoff Crowley
Crithwood Ltd.
Westfield, Scotland, UK
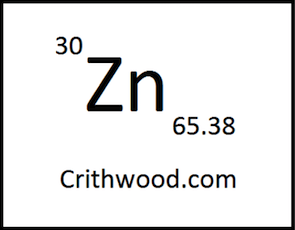
April 23, 2009
April 27, 2009
A. Sir:
I presume you work for the large pole Mfg/Galv plant in Troyes (pronounced Twa). I consulted for your company twice, about 15 years ago. I converted your plant to quadraflux, designed your automated ash recovery box, and installed one advanced technology. Ash was reduced four-fold, but dross increased 10% via the ash box and %GZU was reduced via the advanced technology.
I also presume that you are measuring HCl use and especially generation of "spent" acid in relation to tons of product galvanized. That is: liters of spent acid produced graphed against tons galvanized. I presume the purpose of your study is to reduce the volume of spent HCl.
Likely your measurements of acid concentration decrease and iron+2 increase/ton galvanized do not "match-up," the respective deltas not being in the same ratio is that you may not be taking into account the zinc stripping on rejected steel. In other words, you would not only need to measure the Fe+2 increase but also the Zn+2 increase for each ton galvanized. Another possible factor, considering that your HCl temperature is only 20C, you may have very excessive long pickling times (e.g. all night on weekends). If you could give a better idea of actual pickling times and how consistent they are, it may be useful.
Many years ago, I did experiments pickling 0.060 inch thick steel with 17% HCl at 90 °F. Using a clear glass beaker [beakers on
eBay
or
Amazon [affil link] during the first five minutes nothing much seemed to happen, then suddenly the blue-black iron oxide mill scale just seemed to disappear from the steel surface. Then with increased time the acid started attacking the base steel and evolving hydrogen gas. The mill scale removal was simply the iron+2 oxide DISSOLVING in the acid and then the base ELEMENTAL iron was attacked by the acid. Thus mill scale removal is:
FeO + HCl equals FeClsub2 (simply dissolved)
Whereas base steel (elemental iron) attack is:
Fe + HCl equals FeClsub2 + Hsub2 (gas)
In the first reaction HCl is NOT consumed.
Whereas in the second reaction HCl IS consumed.
Thus taken to the limit, properly inhibited acid should last a very, very long time and would build up in iron+2, but the acid would NOT be consumed. Thus is shown the importance of proper inhibitor and proper temperature for HCl pickling. Of the 100 or so inhibitors that I have tested for HCl, only 5 or 6 were quite good. The others were ineffective, put smut on the tank walls, accelerated the attack of the base steel, smelled very bad, etc. I published an article in
Metal Finishing on how to choose a good pickling inhibitor and how to test for its presence in the pickling tanks.
Regards,
Galvanizing Consultant - Hot Springs, South Dakota, USA
![]() |
Oh dear, I must disagree with Dr. Cook's statement that solution of mill scale in hydrochloric acid does not consume acid. ![]() Bill Reynolds [deceased] consultant metallurgist - Ballarat, Victoria, Australia We sadly relate the news that Bill passed away on Jan. 29, 2010. May 7, 2009 May 11, 2009 Bill, Galvanizing Consultant - Hot Springs, South Dakota, USA |
Q. Dear Dr. Thomas,
How are you doctor? I hope you are OK. A long time now I did not talk to you because I was busy building my new hot dip galvanizing plant in Egypt.
Actually I am interested to discuss pickling accelerator as well how to mix the degreasing and pickling into one process. So do you have any idea about saving the time also the number of pickling and degreaser tanks?
galvanizer - egypt
May 12, 2014
----
Ed. note: We deleted Mr. Ahmed's reference to a particular proprietary pickling accelerator because we discuss technical issues here but we do not post testimonials or dis-recommendations for specific proprietaries.

Q, A, or Comment on THIS thread -or- Start a NEW Thread