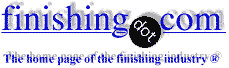
-----
Best way to decrease carbonate content in Zinc Plating process

Q. Dear Sir,
I would like to know the best way to decrease the carbonate content in alkali zn plating by carbolux or sedimentizing (by using the low temperature/subzerro), because it's normally happen (increase of carbonate content)in the process.
Thanks for the answer.
Best Regards,
Engineer - Tangerang, Indonesia
March 18, 2009
A. THE BEST METHOD FOR REMOVING CARBONATES FROM ZINC BATH IS FREEZING OUT PROCEDURE.
FREEZING OUT IS DONE AT TEMP. +4 TO -3 deg C.
FIRST IN LAB THE EFFECTIVENESS OF THE PROCEDURE SHOULD BE ANALYSED.
TAKE 500 ML ZINC SOL. IN A beaker [beakers on
eBay
or
Amazon [affil link] PUT IN REFRIGERATOR
AT ABOVE TEMP. AND OBSERVE AMOUNT OF CARBONATE CRYSTALLIZATION SAY AFTER EVERY 6 HOURS.
SAME PROCEDURE CAN BE APPLIED FOR WHOLE TANK SOL.
THANKS,
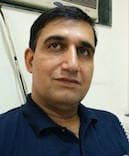
Ajay Raina
Ludhiana, Punjab, India
A. Please consider the different freezing out temperature which is necessary by using potassium or sodium hydroxide based processes.
Regards,
Dominik
- Mexico City, Mexico
A. Dear Dedi,
Carbonate in the solution, I assume that you are using Sodium bath in your Alkaline Zinc plating.
I believe in your country, energy cost is very expensive, therefore I agreed with Dominik, try to use Potassium bath instead of Sodium bath to eliminate your Sodium Carbonate problem.Instead of "FREEZING" the bath, if you have small bath/tank should be OK, but if you have
"giant" tank I think it's not wise to do so.
Beside that try to find out why your Sodium carbonate level increment so fast?
Or try other organic system that can resist high level of Sodium Carbonate but did not sacrifice your efficiency of plating (speed of plating).
Good luck.
Best Regards,
electroplating chemicals supplier- Jakarta, Indonesia
A. Hello
Alkaline zinc plating baths have a high concentration of Sodium Hydroxide,100 to 140 gpl.This is gradually converted to Sodium carbonate due to Sodium Hydroxide absorbing atmospheric CO2.You may chemically analyse fortnightly for CO3- content and also monitor the density of the solution.When the CO3- is increased(as indicated by analysis or density check),usually medium c.d will be dull in a Hull-cell test as well as in production parts.A trial dilution of the solution with demineralized water and adding additives will improve the Hull-cell plate brightness.The same may be implemented proportionately on the production plating tank also improving the brightness of zinc plate.
Good Luck!
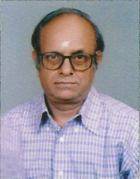
Subramanian Ramajayam
consultant - Bangalore, India
A. Cutting the bath will be a better idea as yours is a Zinc plating bath.
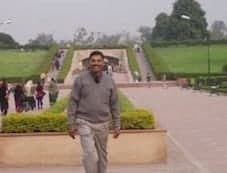
T.K. Mohan
plating process supplier - Mumbai, India
A. Calcium glycolate can be used to precipitate carbonates from alkaline plating solutions including zinc. In a storage tank, add the required amount of calcium glyconate stir, let settle and filter back into the plating tank.
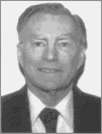
Don Baudrand
Consultant - Poulsbo, Washington
(Don is co-author of "Plating on Plastics" [on Amazon or AbeBooks affil links]
and "Plating ABS Plastics" [on Amazon or eBay or AbeBooks affil links])
Multiple threads merged: please forgive chronology errors and repetition 🙂
Carbonate Refrigeration Equipment
RFQ: I'm looking for some vendors to supply (rent/purchase) some refrigeration equipment to reduce the carbonate levels in our zinc bath. Thanks
Robert Holderman1999
Ed. note: This RFQ is outdated, but technical replies are welcome, and readers are encouraged to post their own RFQs. But no public commercial suggestions please ( huh? why?).
A. Here is a response that just might save you some money. One alkaline zinc user purchased second hand, one milk chiller from a dairy farmer. Every part of the unit is stainless steel, so there is never any attack by the solution.
By appearance, the unit has a compressor unit, plus the cooling vessel which is cylindrical and sits on supports in a horizontal fashion. This unit has been in use for several years and serves the shop very well. The price was, "pretty low," in the words of the owner/user.
Hope this sheds a new light on chilling your zinc solution.
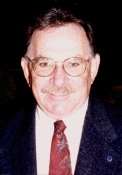

Ed Budman [deceased]
- Pennsylvania
With deep sadness we advise that our good friend Ed passed away Nov. 24, 2018
A. The U.S. Army came up with a system that consisted of a stainless steel box you would fill with dry ice and then hang over the edge of the tank. The box was covered with rough metal screening so that the carbonates would stick as they froze out. The box would be removed in the morning and the carbonates would melt off in a tub. This approach would be good if you only have to treat the tank once in awhile. A quick search of the patent literature should turn up more info on this method.
Mike CallahanQ, A, or Comment on THIS thread -or- Start a NEW Thread