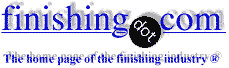
-----
Compare dual ni and triple ni decorative chrome plating
Quickstart:
When decorative articles claim to be chrome, it actually means they have one or more layers of nickel plating followed by a thin layer of chrome plating. Interested readers may wish to see our article "Intro to Chrome Plating"
Nickel-chrome plating is a "barrier layer" plating; once it's penetrated it accelerates the rusting of steel because steel is electrochemically sacrificial to nickel and chrome (the opposite of zinc boat anodes which dissolve to protect the steel hull).
It was found decades ago that the nickel could safely be made thinner by applying it in two layers called duplex nickel -- a semi-bright layer followed by bright -- because bright nickel is sacrificial to semi-bright and will corrode preferentially. These days the idea has been taken further with triplex nickel (three layers).
Q. Please compare the below mentioned decorative chrome types:
1. triple ni layer ( semi bright ni, bright ni, ni powder layer, chrome layer)
2. dual ni layer (semi bright ni, bright ni, chrome layer)
I read from the article below:
https://www.pfonline.com/articles/080801.html ⇩
that, by using triple Ni layer method we can reduce the overall thickness of ni layer consumed compared to dual Ni layer.
so is the triple Ni layer equivalent to the corrosion resistance of dual ni coating. which is cheaper of the two coatings.
engineer trainee - Nashik, Maharashtra, India
February 15, 2009
Ed. update: Sorry, that link is broken and the Wayback Engine of Archive.org has not indexed it.
A. Hi, Rakesh. Duplex nickel has been the minimum standard for OEM work for many decades. It is a fine finish but it is certainly not the ultimate: if you look at OEM specs from a number of manufacturers you will find many references to triple layers and even more.
Regards,
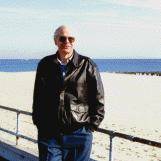
Ted Mooney, P.E.
Striving to live Aloha
(Ted can offer longterm or instant help)
finishing.com - Pine Beach, New Jersey
Q. Dear Mr.Mooney,
thanks for the reply.
Which among the above mentioned two process is cheaper?
What is the best method to measure the corrosion resistance of decorative chrome coating?
- Nashik, Maharashtra, India
A. Hi, Rakesh. Articles / promo pieces never suggest that their proposed process cycle is more expensive, less corrosion resistant, or inferior to the conventional approach that they are trying to supplant :-)
So, I think the implications of that article are clear, that the triple layer is better. If people feel that this should be challenged, I think they need to write to the editor of the periodical where it was printed. It wouldn't be fair to challenge the article in a different venue that the authors may not even be aware of. There are dozens of proprietary process cycles for high quality chrome plating and I don't think any one is superior to every other one in every situation. People switch from brand X to brand Y and back every day. But, in general, progress seems to be moving toward more & thinner layers rather than towards fewer & thicker layers.
Only real exposure testing can reveal which process is most corrosion resistant though. Most accelerated tests have proven to give erroneous results for a number of reasons, including the fact that sulfur in the test medium corrupts the sulfur-based potentials between the nickel layers that are so important to the corrosion resistance. But Dennis & Such ⇨
seem to indicate their preference for CASS (copper-accelerated salt spray) testing over alternative test procedures. Good luck!
Regards,
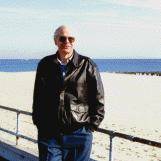
Ted Mooney, P.E.
Striving to live Aloha
(Ted can offer longterm or instant help)
finishing.com - Pine Beach, New Jersey
Readers may also be interested in these related threads:
• Topic #203/45 "How to compare ASTM B117 Salt Spray and ASTM B368 CASS Test?"
• Topic #370/01 "CASS and Chrome Plating"
• Topic #89/04 "Salt Spray Hours vs. real life exposure"
Q, A, or Comment on THIS thread -or- Start a NEW Thread