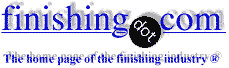
-----
Galvanizing Zinc Splashes Problem!
Hello Everybody,
We are a new galvanizing company opening in Egypt but during our researching steps we had a problem without any answers. Its all about the splashes coming out from the galvanizing zinc kettle during the immersion of metal tubes in zinc.
NB.
our production is mostly in the field of metallic pipes and angles.
Please advice about the applicable solutions without using the Enclosure.
Project Research Department - Cairo, Egypt
January 29, 2009
First of two simultaneous responses --
Most splash is caused by water. To avoid it, the steel should be dry. After fluxing (and make sure the flux is right chemistry), heat the steel to fully dry it and you will get almost no splash.
To test how well this works, do a test: Leave the work hanging above the zinc without lowering for a while to get it fully dry, then lower.
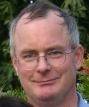
Geoff Crowley
Crithwood Ltd.
Westfield, Scotland, UK
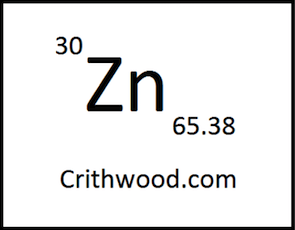
January 29, 2009
Second of two simultaneous responses -- January 29, 2009
Sir:
You need the proper flux solution and you need to know how to use it. What is your composition: double? triple? or quadraflux? What is your baumé (or density in g/ml)? What is the temperature of your flux solution? For a better understanding see the several articles that I authored in the journal: METAL FINISHING.
Regards,
Galvanizing Consultant - Hot Springs, South Dakota, USA
First of two simultaneous responses -- January 30, 2009
Sir:
For most types of products including pipes (done in a jig), and angles it is NOT necessary or desirable to heat the steel to dry the flux solution. Rather, by using the North American method, triple or quadraflux of low density, the steel is put into the hot flux solution long enough to heat the steel throughout. Then upon withdrawal from the hot flux solution, the steel drys by itself in a minute or two and there is virtually no zinc spatter. Quadraflux is best. A certain wetting agent aids in the drying. Leaving the steel hangind above the molten zinc is a horrible waste of time.
With an ACN higher than quadraflux and hot solution, I have seen a spin galvanizing zinc bath being operated by men in short sleeve shirts with no glass shield whatsoever. These men were NOT being burned by molten zinc. It's in the CHEMISTRY of the flux and HOW to OPERATE it. It is NOT like the European method. Each has advantages and disadvantages. Just different ways to "skin the cat."
Regards,
Galvanizing Consultant - Hot Springs, South Dakota, USA
Second of two simultaneous responses -- February 1, 2009
Thanks a lot Mr. Geoff Crowley and Dr. Thomas Cook
that was really great from you. Your help is greatly appreciated.
Also I want to ask if there is a special type of flux that could be used to prevent splashes as some researches said that using the triple salt flux decreases the probability of having splashes because it decreases the moisture on the steel.
- Cairo, Egypt
February 3, 2009
Dear Dr. Thomas Cook,
Would you please tell me he specifications and the components of the QuadraFlux solution.
"percentages of Chemicals"
Also I need to know if using that type of flux will prevent the occurrence of splashes permanently or not?!
Thanks in advance for your valuable support.
Best Regards,
- Cairo, Egypt
February 3, 2009
Sir:
The answers to your questions are in my article: "Composition, Testing, and Control of Hot Dip Galvanizing Flux" which is now published in the journal METAL FINISHING. Their website is www.metalfinishing.com.
Regards,
Galvanizing Consultant - Hot Springs, South Dakota, USA
February 4, 2009
Sir:
If you put in "quadraflux" into the search engine on this site you will get 21 responses. I hope this helps you.
Regards,
Galvanizing Consultant - Hot Springs, South Dakota, USA
I should clarify that the idea to hang the work above the bath of zinc to dry it and see if you get no splash is a test. This is not a practical way to solve the problem, but it will tell you that you need to do something about your flux.
As Tom says, the key is the chemistry of the flux. Get the flux right and there are few other problems in galvanizing.
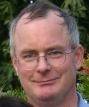
Geoff Crowley
Crithwood Ltd.
Westfield, Scotland, UK
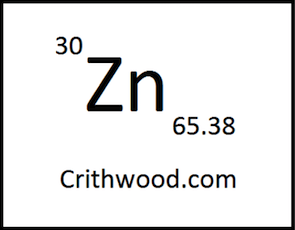
February 6, 2009
February 10, 2009
Sir:
As an experiment, dissolve 1.6 Kg of ammonium chloride and 1.00 Kg of zinc chloride in enough water to make 10 liters of flux solution. Both the ammonium chloride and the zinc chloride must not contain more than 1% sodium chloride (NaCl). This flux solution will be 13.5 degrees baumé (1.1027 g/mL) measured at room temperature. This is quadraflux and has an ACN = 1.60 (ACN = Kg ammonium chloride/Kg zinc chloride). In a porcelain coated steel cooking pot heat this flux solution to 71 deg. C. Put one piece of pickled and rinsed steel into this pot for three minutes, remove, allow to dry about three minutes, and then dip into the molten zinc. Let the readers of this site know your results.
Regards,
Galvanizing Consultant - Hot Springs, South Dakota, USA

Q, A, or Comment on THIS thread -or- Start a NEW Thread