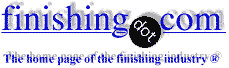
-----
Dow 20 finishing process on magnesium
Q. My company has recently experimented with the Dow 20 process on magnesium at the request of one of our customers. The only challenge we have had is removing the "smut" that remains on the parts after the final 2 rinses. The only way we have been able to remove the "smut" is to wipe it off by hand during the final rinse. Any ideas on what this smut is and how we can remove it other than by hand. Thanks,
Brad Smith- Evansville, Indiana
1999
A. Dear Mr. Smith,
I would look first at the alloying elements to see if any might be culprits in remaining on the surface after treatment. Also, smut is a typical problem in processing magnesium, and may be formed during almost any step in the cleaning and pickling of magnesium. Your challenge is to whip the process into shape so that smut, if formed, can be removed chemically instead of physically.
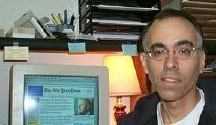

Tom Pullizzi
Falls Township, Pennsylvania
A. As mentioned above, this is a very typical challenge for the first time magnesium finisher. I would suggest, if you haven't already obtained it, to contact DOW Chemical and ask for their booklet titled "Operations in Magnesium Finishing". The last number I have for them is 1.800.447.4369. I have found that running several, and I mean several, scrap parts from your customer through trial processing cycles will give a great advantage in diagnosing the problem, and in establishing a production processing cycle. One overlooked item, is that the smut formation coming out of the DOW 20 can be minimized by trying different cycle times. One will notice that both too short and too long times will cause a greater degree of smut formation. Also, try a 50% diluted DOW 20 with various processing times, at different temperatures. One type of casting used to run better if heated up in a hot water rinse after immersion in a 6 oz/gal hot commercial alkaline cleaner and just prior to processing in a 50% dilute solution of DOW 20. Other parts produced less smut when run in an ambient 85% phosphoric acid pickle for ~10-15 seconds, and letting them drip above the tank for ~ 30 seconds and without rinsing, then were dipped in a 10% solution of ambient temp. 6 oz/gal sodium hydroxide. They were then rinsed in a cold water rinse and processed through the DOW 20. Be VERY careful to chart the etch rates in the solutions which cause metal removal as DOW solutions and/or pickles may result in a metal removal rate greater than a mil/minute which creates havoc with dimensional tolerances. This last rate mentioned was charted using alloy AZ91D in a standard, freshly made up solution of DOW 20. A 50% dilute solution at 66 degrees F. removed 4 tenths of a mil in a minute by comparison with the same alloy being tested. Both gave good color. One way to check smut is to use a scotch tape test on the part and then after pulling off, place over white paper next to the process cycle description which produced it. A comparison can then be mad e and used for QA/production purposes. Also, good chemical and temperature control during the charting process to determine the production cycle is critical, as is maintaining the baths in actual production conditions. Each alloy will run differently and magnesium loading in the pickles from high production rates, also will change etch rates/smut formation over time.
Ward Barcafer, CEFaerospace - Wichita, Kansas
1999
A. Dow has exited the magnesium business. I believe the finishing books are no longer available from Dow. They contain a section specifically devoted to smut problems on Dow 20. If you are interested a substitute process, Luke Engineering can offer the hard anodize, Magoxid-Coat.
Chris Jurey, Past-President IHAALuke Engineering & Mfg. Co. Inc.

Wadsworth, Ohio
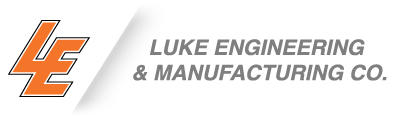
1999
Q. Hi, I'm with a plating company in Singapore. Would really appreciate if anybody could give me any, I mean any information on "Dow 20" for magnesium. I have no idea whether it's a chemical or a process, or whatever, therefore I appreciate if somebody could give me a lead.
Andrew Lee- Singapore
2000
A. Dow #20 aka Chemical Treatment #20 aka Modified Chrome Pickle, was developed to provide a more uniform colored coating than Dow #1.
It is mainly used for:
- protection during shipping & storage
- good base for paint (more uniform on castings than Dow #1).
- Long Island City, New York
2000
Q. Hi David, Thanks a lot for your response. I have tried calling Dow Chemical to see whether they sell the Dow 20, but they claimed that they don't. Do you know where I can buy them? Regards, Andrew Lee
Andrew Lee [returning]- Singapore
2000
Q. I am a young researcher in Shanghai Jiaotong University, China. I am engaging in research work about magnesium alloy finishing, I want to buy a booklet put out by DOW called "Operations in Magnesium Finishing" or other relative handbook. Who can tell me where and how to buy them? Thanks!
Xingwu GuoShanghai Jiaotong University -Shanghai, China
2000
by Dow Chemical Co.
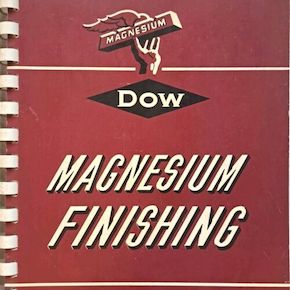
is sometimes available on
AbeBooks,
eBay, or
Amazon
... but if not, you can find libraries which have copies on WorldCat.org
(affil link)
A. Dow Chemical Co. developed a number of finishing processes for magnesium, including Dow 20. They published the details in a book entitled, Magnesium Finishing. All of the chemicals and equipment necessary are non-proprietary. However, Dow has exited the magnesium business and I do not know where to send you for a book. Maybe Ted can help.
Chris Jurey, Past-President IHAALuke Engineering & Mfg. Co. Inc.

Wadsworth, Ohio
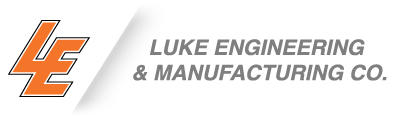
2000
A. Sir,
Dow stopped their involvement in mag finishing many years ago. The handbook we have on Dow finishing is worth its weight in gold.
- Long Island City, New York
2000
March 2014
A. Hi Andrew, hi Xingwu. If unable to locate a copy of Dow's Magnesium Finishing, Durney's Electroplating Engineering Handbook has a 10-page chapter by H.K. DeLong (of Dow) titled "Anodizing and Surface Conversion Treatments for Magnesium". It includes info on the Mil-M-3171A, Type 1 Chrome Pickle (or Treatment #1 and #20).
Treatment #20 is
- Sodium Acid Fluoride 2 oz/gal
- Sodium Dichromate 1-1/2 lb/gal
- Aluminum Sulphate 1.3 oz/gal
- Conc. Nitric Acid 1 pt/gal
It's operated at 70 - 90°F for 20-30 seconds for diecastings.
Regards,
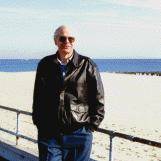
Ted Mooney, P.E.
Striving to live Aloha
(Ted is available for instant or longterm help)
finishing.com - Pine Beach, New Jersey
1999
Q. We are developing a very complex die casting with thin walls.
Due to this, I am becoming VERY wary of using an aluminum die cast part - primarily due to the need of a high quality as cast surface and the resultant low die life.
We are investigating a magnesium die casting (materials heavier than aluminum are out). However, this is a part that will be exposed to the elements and will have mating parts of steel and brass.
My research to date is that Dow Chemical 20 (a chromate process I assume) is the best volume process to go with.
It is also my understanding that we can use it in the shop as a touch-up process during assembly (nicks, etc.)
Can someone point me to the right firm that could supply me with a sample and technical information on this?
Thanks!
- St. Louis, Missouri
Ed. note: This RFQ is outdated, but technical replies are welcome, and readers are encouraged to post their own RFQs. But no public commercial suggestions please ( huh? why?).
A. An alternative that would be more expensive but might be well suited for "a part that will be exposed to the elements" is electroless nickel. Atotech offers a process designed specifically for magnesium, which they call Magenta.
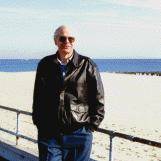
Ted Mooney, P.E.
Striving to live Aloha
(Ted is available for instant or longterm help)
finishing.com - Pine Beach, New Jersey
1999
A. Many of our customers who have mating parts to their magnesium parts have tried to use Dow 20. It seems that Dow 20 doesn't provide enough protection and our customers always end up coming back to electroless nickel.
Brad Smith- Evansville, Indiana
2000
adv.
Luke Engineering offers a hard anodic coating for Magnesium, Magoxid-Coat®. It is vastly superior to chromates and other anodizing processes for magnesium in both corrosion and wear resistance. Due to the hazardous nature and regulation of chrome containing processes, they are becoming more difficult and expensive to find. Magoxid-Coat contains no chromium or other heavy metals. The thin version, 8 to 12 um, is very price competitive with Dow processes.
Luke Engineering & Mfg. Co. Inc.

Wadsworth, Ohio
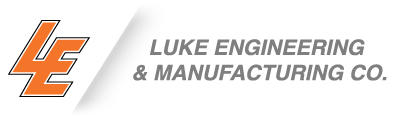
2000
Multiple threads merged: please forgive chronology errors and repetition 🙂
Q1. I need datasheet of "Dow 20" finishing process on magnesium.
Q2. For how long a time does salt spray 5% resist on magnesium AM60B?
- Rishon Le Ziyon, Israel
2003
A1. Dow 20 (Modified Chrome Pickle) was developed to provide a more uniform colored coating than Dow 1. Treatment 20 may be used on all magnesium alloys but is particularly adapted for magnesium DIE castings. Sodium Acid Fluoride 2 oz/gal, Sodium Dichromate 24 oz/gal, Aluminum sulphate 1 1/3 oz/gal, Nitric Acid (70% Nitric) 1 pint per gallons. 5 seconds to 2 minutes. I can copy Dow's book which is three pages on this subject and slow mail to you if you come back. Need a more complete address.
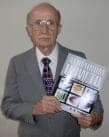
Robert H Probert
Robert H Probert Technical Services

Garner, North Carolina
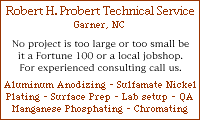
2003
A2. It stays not more than 8 hours. That is all.
Ilya OstrovskySurface Treatment - Germany/Israel
2004
Q. I am looking for a coating for magnesium that gives me some corrosion protection BUT ALSO does not inhibit electrical conductivity. The application is an electronic enclosure that needs to be conductive for grounding purposes.
Thanks,
Univ. of Chicago - Chicago, Illinois, USA
2003
A. Can it be a plating like electroless nickel, or must it be a surface conversion chemistry?
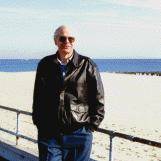
Ted Mooney, P.E.
Striving to live Aloha
(Ted is available for instant or longterm help)
finishing.com - Pine Beach, New Jersey
2003
Q. I would prefer it to be chemical conversion instead of plating.
Tim Rennick [returning]Univ. of Chicago - Chicago, Illinois, USA
2003
A. Hi Tim. Maybe Dow 7 or Dow 1 or 20 treatment will do. Please see Tom Pullizzi's excellent article on Finishing of Magnesium. Good luck.
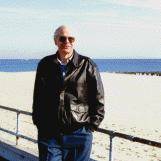
Ted Mooney, P.E.
Striving to live Aloha
(Ted is available for instant or longterm help)
finishing.com - Pine Beach, New Jersey
2003

Q, A, or Comment on THIS thread -or- Start a NEW Thread