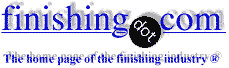
-----
Reddish-orange deposit on anodizing tank cathodes?
Q. We have a lot of reddish orange flakes of stuff coming off one of our anodizing tanks' cathodes and getting into the bath. We had the anodes fabricated in house and we told them to make them out of 6061, 6063, 1100 or 1350 aluminum, but I am not sure which if any of these the cathodes were made out of. What is this stuff does anybody know?
Thomas. Brownplating shop employee - Colorado Springs, Colorado
January 19, 2009
![]() |
A. Sounds like mostly copper to me, which is present in most Al alloys, getting dissolved in the bath during the anodizing process, and is getting plated onto the cathodes. ![]() Marc Green anodizer - Boise, Idaho January 21, 2009 A. It is copper that has dissolved out of the parts when anodizing initially starts. It normally results when you anodize 2,4,7xxx alloys which have a high copper content. A better desmut step can reduce this, but removal of the cathode from the tank and wet brushing it will also work which is cheaper but messy and labor intensive. James Watts- Navarre, Florida January 21, 2009 A. My guess: copper metal. ![]() Dave Wichern Consultant - The Bronx, New York January 21, 2009 A. Apparently you have been running some 2000 alloys and are plating the 5% copper onto the cathodes. Sulfuric Acid and copper sulphate
⇦ on
eBay or
Amazon [affil link] are
(1) a standard copper plating solution and (2) standard anodizing solution. Years back, Metal Finishing published a research paper whereby controlled and varied periodic reverse was used in a copper containing anodizing solution to alternate between positive and negative and deposit copper direct on aluminum without a zincate and without a stannate. I do not think the process ever caught on. ![]() Robert H Probert Robert H Probert Technical Services ![]() Garner, North Carolina ![]() January 21, 2009 |
![]() |
Q. I learned that the cathodes are made up of 6101T6 aluminum. Plating shop - Colorado Springs, Colorado January 22, 2009 January 22, 2009 A. Thomas - Colorado Springs, Colorado January 22, 2009 A. Thomas, ![]() Trent Kaufman electroplater - Galva, Illinois |
A. Trent, it is actually badly plated copper as the cathode is negative. Also, it dissolves back into solution if left alone over the weekend, so it is not immersion plate.
James Watts- Navarre, Florida
January 23, 2009
A. We Anodize a fair amount of 6000 and 2000 series aluminum and see the same effect. We determined that it was copper from the alloying elements dissolved from the aluminum in process and deposited on the Cathodes. We now periodically remove the Cathodes and clean during regular bath maintenance and see no adverse issues.
Paul Slater- Cedar Rapids, Iowa, USA
January 28, 2009
Sulfuric Anodized part burned to copper color?
June 10, 2020Q. I'm hoping someone will be able to help me understand what happened with this part. It was one part of an order of 18. Most of the order came out fine. A few did not take, but no others have this issue. Material 2124-T851 Processed as follows:
Alkaline clean, rinse, rinse.
Deox, rinse, rinse,
Sulfuric Anodize, set voltage 18, Ramp 5 volts per min. 30 min at peak. The parts were racked with insulated gator clamps and a power clamp.
It looks like a burn but with copper plating in the center of the burn. I got thickness reading as high as .32 mils on the copper area. I can't seem to find any information on how an anodizing part can somehow reverse the process in a localized area and be plated? This may not be what happened, but we can't find other explanations.
The shielding around the cathodes is intact and nothing seem out of ordinary in the tank. Pictures:
Thank you for any insight on this.
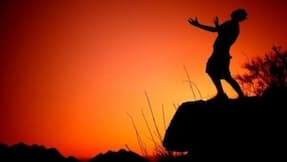
Tyler Barnhart
- Chanute, Kansas, USA
![]() |
A. If you are running 2000's alloys you have a copper plating solution in the tank. When the rack broke electrical contract, in a bi-polar way, it became negative with respect to the other racks, so it copper plated in the high current density areas. ![]() Robert H Probert Robert H Probert Technical Services ![]() Garner, North Carolina ![]() June 10, 2020 A. This looks like a copper immersion deposit; Most likely the parts were burned enough so very little current was in those regions allow an immersion deposition to take place. - Sidney, New York USA June 10, 2020 |
Q. Thank you Robert and William for your Responses. Would you both recommend nitric as the best method to remove the copper? If so, what would you recommend for a ratio of mixing? we Have nitric 65-67%.
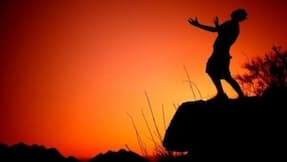
Tyler Barnhart
- Chanute, Kansas, USA
June 11, 2020
A. If you have a high copper concentration in your anodize bath, then there are several ways to reduce it. The aluminum foil to immersion plate the copper method is simple and can be effective, and should probably be your first attempt at copper removal. However, if this is not effective, then a more active removal method is needed. Dummying the bath with high surface area cathodes is an effective method to remove copper. Other methods can also remove aluminum as well as copper.
Lyle Kirman- Cleveland Heights, Ohio
June 17, 2020

Q, A, or Comment on THIS thread -or- Start a NEW Thread