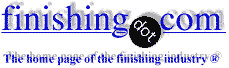
-----
Removal of Heat Treat Scale from Stainless Steel

Q. We need to clean the surface of steel after the quenching process.
My steel is 17-4PH which is solution heated at 1040 °C and tempered at 40 °C.
There is dust and rust on the surface of the metal. So, I want to clean it (I think that it's FeO).
Please give some ideas to cleanliness.
Thank for your help.
- Hanoi, Vietnam
December 13, 2022
⇩ Related postings, oldest first ⇩
Q. One of our products uses a threaded fastener that, by print, requires an Oil Quench Heat Treat prior to passivation. After Heat Treat the fasteners have a scale residue that is not affected by our cleaners or Passivation Processes. We have prescribed a mechanical removal but this is both expensive and difficult to monitor.
Is there a product/process that will remove the Heat Treat Scale without affecting the substrate. The material is 400 series SS.
Thank You
- Mishawaka, Indiana
2000
A. Lyndon: If neither nitric acid or hot CitriSurf formulations remove the scale, you probably have to go to nitric/HF solutions or potassium permanganate ⇦ on eBay or Amazon [affil link] solutions. The hot KMnO4 is safer to use, but can be very messy. Of course, you can remove it with electropolishing. Good luck!
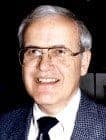

Lee Kremer
Stellar Solutions, Inc.

McHenry, Illinois
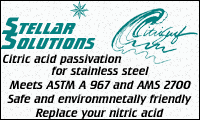
A. It sounds like you will have to acid pickle to remove the scale prior to passivation. The process that you should use will depend on the specific stainless steel alloy, its condition, and the nature of the scale. The residue may be oxide from the thermal process and/or from the oil quench. Start by referring to ASTM A380
for as a standard guide for cleaning and passivation.
The ASM Handbook Volume 5 also has excellent information about surface cleaning and passivation. It may take some experimentation to get the best method with the safest chemicals and minimum damage to your parts.
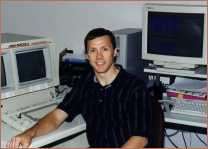
Larry Hanke
Minneapolis, Minnesota
A. In response to the Question of "Removal of heat treat scale from stainless steel", I find the quickest and the most logical method would be a form of electropolishing. With a small power supply, a hand held wand and less than a liter of electropolishing solution, the problem can be solved within a matter of seconds.
This is not to be confused with electropolishing, but rather weld stain clean-up or heat treat scale removal. The true advantages of this method is its portability, selectiveness of the area to be cleaned up and the time it takes to achieve the required results. This is a proven method that is user friendly with little waste.
- Cleveland, Ohio
A. Lyndon, Have you tried using inhibited HCl in conjunction with ultrasonics? This method has worked for me in the past. Good Luck,
Mark Kruzel- El Cajon California
![]() |
A. There is a specialty foil and foil baggie that you can put SS parts in that will significantly reduce oxidation (scale) on your parts and they can still be oil quenched with similar results as to what you are doing now. Do not know what the cost benefit tradeoff would be for your particular parts. On tight tolerance parts, it worked for me as we did not have to regrind them. James Watts- Navarre, Florida ---- Ed. note: "An ounce of prevention is worth a pound of cure". James has offered a good idea, and topic 10948, "Coating stainless steel to inhibit heat treat scale growth" discusses another prevention method. |
A. Lyndon: There is a new type of passivation now available that we call Selective Abstraction Passivation (SAP). It is a non-nitric/HF formulation that is electrolytic. SAP will remove heat treat scale, weld residues, etc. and give you a passive surface second only to electropolishing. This process is environmentally friendly and can be used by OEM's that do not have waste treatment or ventilation equipment. It is NOT a citric chelant product by the way.
Dan Weaver- Toccoa, Georgia
A. Lyndon: Is the quench oil in good condition? Excessive scale can be eliminated or greatly reduced if the proper quench oil is used and maintained correctly. I prefer the Potassium permanganate method of removal of scale after the quench has been looked at.
Regards,
Springfield, Massachusetts
Q. Is it possible to descale stainless steel (304 and 316) without stripping some of the surface away? We have a process where we have a small diameter rod (0.035") that are single use only because of the scale that builds up during our process. We've tried electropolishing but to no avail? Will any of the above methods affect the diameter of the rod? Our tolerance is not strictly defined but I reckon we can't use it if its shrinks by more than 0.002"
Alan Hughes- Ireland
September 16, 2009
A. We use a solution called Mirachem to remove heat tint at 3:1 water/Mirachem heated at 100-110 °F.
James Manning- West Bridgewater, Massachusetts
Thanks, James! Are you able to also tell us what TYPE of product this is pleaae, in addition to your supplier's name? Thanks!
Regards,
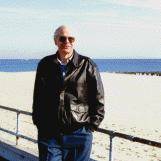
Ted Mooney, P.E.
Striving to live Aloha
(Ted is available for instant or longterm help)
finishing.com - Pine Beach, New Jersey
Q. Hello,
I was looking for some advice on the best way to clean small heat treated parts of 17-4. If I go straight to passivation they do not pass the copper sulphate
⇦ on
eBay or
Amazon [affil link] test.
Is a pickling paste of Nitric and Hydrofluoric alright? I am not talking a large quantity.
Thanks in advance,
Micheline
finisher - Rincon, Georgia
January 12, 2011
A. Micheline,
Has this always been a problem or is it something that has occurred recently? If it is a recent problem you need to find out what has changed to cause the change in results.
You say you go straight into the passivation, is this without pre-cleaning? The usual process would be to pre-clean using something like a mild alkaline soak cleaner followed by a rinse and a check that the surface is free of waterbreaks before going into the passivation solution.
Unless you have some sort of heat treatment scale on the parts I would try to avoid any etching process involving HF or similar chemicals, these are very nasty chemicals. You may consider blasting the surface to remove the scale.
Failure of the copper sulphate test is an indication of free iron on the surface. You may wish to try and find the source of free iron contamination of your surfaces.
Aerospace - Yeovil, Somerset, UK
![]() |
A. Hello, Micheline. I would also advise grit blasting before passivate. Pickling paste would also work great if you can apply it safely. ![]() Jon Barrows, MSF, EHSSC Kansas City Q. Brian, - Rincon, Georgia |
A. With a good passivation process, heat treat scale and other discolorations aren't normally a barrier to attaining a good iron free surface, more often the concern is a cosmetic one. Mechanical removal (grinding/blasting/buffing/etc.) and pickling (either a bath or paste) tend to be the best ways to remove scale and discoloration. Let us know if we can help.
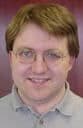
Ray Kremer
Stellar Solutions, Inc.

McHenry, Illinois
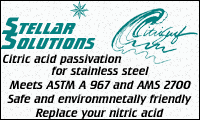
A. Paste is very labor intensive and since they are small parts, I would set up a small pickle tank with a solution appropriate for 17-4. You can find this in good reference books and on line at a few sites.
James Watts- Navarre, Florida
A. Have you tried Electropolishing the parts - this should clean out any heat scale and will also passivate the parts. Good luck.
Lavanya Narne- Newark, California, USA
![]() |
? Are the parts clean before heat treatment? Baked on oil can be extremely difficult to remove and can prevent the passivation from access to the surface. ![]() Geoff Smith Hampshire, England A. Instead of using complex processes and products to remove scale after heat treatment, it may help to use an effective anti-scale compound. The anti-scale compound is used by coating on the component before heat treatment and allowed to dry completely. The coated component is heat treated. After heat treatment, scaling is either zero or substantially reduced. The results depend on your heat treatment cycle. However, many users of anti-scale compound have reported satisfactory level of scale reduction, if not complete elimination of scale. ![]() Srikar Shenoy - Mumbai, India ---- Ed. note: "An ounce of prevention is worth a pound of cure". Srikar has offered a good idea, and topic 10948, "Coating stainless steel to inhibit heat treat scale growth" discusses another prevention method. |
A. After many years of trying various chemicals and mechanical methods to remove heavy carbon, smut, and a very tenacious oxide layer, I happened to stumble upon an old military document written by Northrop back in 1952 that really works...
Use an aqueous (distilled water) alkaline solution of 0.5 molar of Potassium Permanganate, 3.75 Molar of NaOH, and 1.5 Molar of sodium carbonate
⇦ on
eBay or
Amazon]
(Calcium Carbonate also works good, same amount). Heat up part in this solution to 190 °F for 2 hours, or 150 °F for 4.5 hours (what I do).
If you are not wanting to heat up a bath (especially a large bath), and you don't need such fast results, you can instead use 0.4 molar of Potassium persulphate & 3.75 molar of NAOH. At 70 °F it will take approximately 12 hours. I have not tried this bath method, but according to Northrop you get the same results.
You'll need to google the molecular weight of each of those chemicals, and then use a molar calculator (again, google it)., to figure out the correct amounts to use for the amount of solution you are making.
The next step is to rinse the solution off of your parts. Most carbides & oxides can be wiped off, or (my preference) taken off with a short ultra sonic bath in plain water (fast, very effective).
A quick dip in an inhibited hydrochloric acid bath (3~5 minutes at room temp) will clean up any remaining smut.
Another water rinse, then passivate the surface with either a nitric or citric bath (the surface is "activated" by the HCl bath, so you'll want to passivate it). I have found that it doesn't take as long to passivate an activated surface like this.
- Browerville, Minnesota, USA
Permanganate De-scaling of Stainless Steel
Q. Hi all, We are currently reviewing our Stainless Steel de-scaling operation in an attempt to increase the effectiveness and efficiency of the process. The current bath make-up is 20 oz/gal sodium hydroxide
[affil link] and 12 oz/gal sodium permanganate, operated at 190 °F. This is a legacy formulation. However, in researching formulations, I have noticed that many include a fair amount of sodium carbonate
⇦ on
eBay or
Amazon]
. My question is, "Does anyone know why the carbonate is included in these formulations?"
Thanks for your assistance.
Plating Shop - San Diego California USA
March 4, 2015
A. Good day Steve.
Here is some reference material, maybe relevant to your question.
"In domestic use, it is used as a water softener in laundering. It competes with the magnesium and calcium ions in hard water and prevents them from bonding with the detergent being used."
Perhaps it assists with the removal of the scale, leaving the surface cleaner as smut/scale free.
Regards,
Lab Tech. - Whitby, On, Canada
Q. Hi, I am james and am from Thomson Engg Works. Currently we are manufacturing rod type "U" clamps. We have got a new order to make stainless steel "U" bolts or "U" clamps. We are going to heat only where it's to be bent and I want to remove the scale from heating … please tell an economic way to remove the scale.
James alfredThomson engg works fasteners - Chennai tamilnadu india
May 23, 2018
Hi James. As you see, we appended your question to a thread which already discusses it in quite deep detail. Please feel free to pose your question in terms of the responses you can read here. I especially liked the postings about stainless bags and anti-scale compounds. Good luck.
Regards,
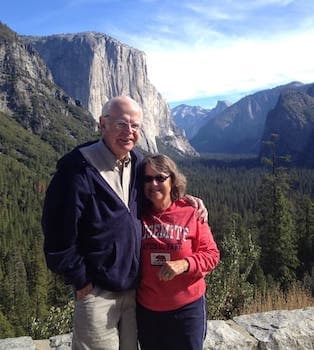
Ted Mooney, P.E. RET
Striving to live Aloha
(Ted is available for instant or longterm help)
finishing.com - Pine Beach, New Jersey
Q. Hello,
We are producing stainless steel drills which are used for dental surgery operations.
After the heat treatment operation we observe some scale on parts; we apply acid/passivation and polishing operation after heat treatment to remove that scale from surface, but also this process wears off some surface … then our products are OOT, our tolerances are 0.01 mm.
So could you please advise method of chemical that removes scale without wearing off the surface.
Nucle - IZMIR, Turkey
August 28, 2018
A. Hi Arda. The scale is a reaction product of the stainless steel with the heat treating atmosphere & chemistry. If you remove the scale and nothing but the scale, no matter how carefully, the dimensions will still be reduced because some of your stainless steel was converted to scale.
Although you can look for less aggressive pickling, polishing, and passivating procedures, I think you'll either need to build the component to a dimension that allows for scale or institute measures to reduce the amount of scale.
Regards,
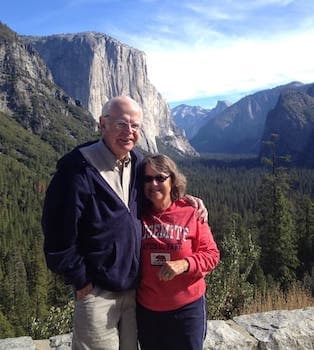
Ted Mooney, P.E. RET
Striving to live Aloha
(Ted is available for instant or longterm help)
finishing.com - Pine Beach, New Jersey
Remove heat treat scale from stainless steel
Q. I would like to know how to remove heat treat scale off of precipitated hardened stainless steels in order to prep for liquid penetrant testing.
Micheline ForthEdwards Interiors - Rincon, Georgia USA
May 20, 2019
A. Micheline,
This would be "descaling", either mechanical (abrasive) removal such as tumbling or media blasting, or acidic (a.k.a. pickling) typically using a nitric-hydrofluoric mix.
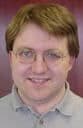
Ray Kremer
Stellar Solutions, Inc.

McHenry, Illinois
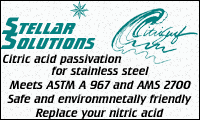
Q. Thanks for your response but I have been told acid is not an acceptable choice. I can blast the heat treat scale but have concerns that smearing may occur and then I will have no way of removing. Since I posted my question I have been looking at alkaline cleaning. Some products I've looked at contain approx. 15% potassium hydroxide.
Micheline Forth [returning]- Rincon, Georgia USA
Q, A, or Comment on THIS thread -or- Start a NEW Thread