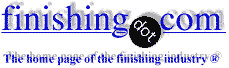
-----
Hardcoating 2011 - Is it possible to build up .002? Or should a different alloy be used
Greetings,
Here is the problem I'm having now. I have a customer that has 2011 material and he insists on my trying to build up a 4 mil .002 buildup/ .002 penetration coating for him to move his parts from a 2.497 dia to a 2.499 dia. sizing. Now I've already tried 4 of these and have been unsuccessful, and after reading more into it, the AAC has 2011 listed as unsuitable for hardcoat anodizing. Has anyone here hardcoated this material? What were your results. I gaged the parts I did and constantly got nothing more than .001/.001 instead of .002/.002. Would this person be better off going with another material (my first recommendation to him btw), such as 6061, or 7075 (since they want to maintain a hard base material, but the hardcoat on a 6061 exceeds the abilities of the same coating on a 7075.
Can you guys throw in your ideas, I'm trying to convince this customer that there are things that can be done to fix this problem but its not something I can physically do on my own because of the limitations of the material in question. I can't defeat the laws of science is how I put it to him.
Thanks in advance for any help anyone can offer me. I'm getting kinda frustrated with this as my explanations don't seem to be totally sinking in and I don't want to be hung out to dry for something that I can't possibly do no matter what the costs would be.
plating company - Toledo, Ohio
2000
2000
Hello again, Matthew:
You're starting to test the limits of my experiences as a hardcoater, at least the limits of my memory bank, as I hung up my hardcoaters' spikes, er rubber boots, some 15 years ago, but you guys keep bringing back some bad memories. I remember 2011 as extremely to hardcoat, and even when we got the thickness it wasn't very hard. The coating was a creamy color and you could actually feel that it was a sticky- soft, rather than the grey-bronze and slippery-hard coating on 2024.
I don't understand your comments about trying to get a 4 mil coating, but I do understand that you are trying to increase the diameter by .002", which means to me .001" buildup per side of the O.D. or .002" coating per side, assuming the 50:50 buildup:penetration rule. At any rate I can understand your frustration, as 2011 is very difficult to hardcoat. It has more copper in it than 2024, and the extra copper is undoubtedly the reason for the difficulty in hardcoating.
I believe one of your problems is that basic assumption that hardcoaters use all the time, but may not be necessarily true all the time- that 50:50 buildup: penetration rule. At 6% copper in the alloy, the copper is going to try to dissolve as fast as it loses its electrons, and this will take away current flow from the aluminum, which is trying to oxidize. The result is slow oxide buildup which in turn increases the percentage of aluminum oxide that dissolves in the sulfuric bath during the anodization. Result- higher penetration, lower buildup on the diameter. You might get 2011 to hardcoat properly with bath additives and/or a pulse current rectifier,but you could be talking big bucks.
If you need this as a testimonial, I agree with you that the real solution to the problem is to switch alloys. Assuming that your customer has a reason for picking a high copper alloy, presumably for ease of machining, 2024 or 2014, while having their own quirks, would at least be achievable in acquiring the O.D. that you need. If wear resistance is important in the ultimate use of the part, 6061 would be far superior to any of the 2xxx series. For maximum strength of the aluminum plus good wear resistance, 7075 would be the choice.
As in my years (only 16) as a hardcoater, I see that a major problem the aluminum parts industry still has is communication between people who design aluminum parts and the people responsible for producing the final finish. Very often the people who design the parts think they are doing themselves a favor by picking an alloy that their machinists can work with easily, not realizing they could be sacrificing the ultimate quality of the final parts by picking an alloy that is difficult to finish. It's the same kind of problem we have seen at this site from several anodizers trying to anodize die-cast aluminum, but don't get me started on that one- again.
Phil Johnson
- Madison Heights, Michigan
I was going to reply when I noticed Phil had beat me to the punch.. the only thing I can add to his comments is to increase your acid concentration, but regardless...your customers requirements sound like a very tall order..even if you were to get the required thickness, I think your coating would be crap. I would love it if all parts designers/engineers would attend an "anodizing 101" course..it would make everyone's job 10 fold easier.
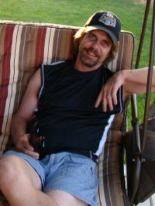
Marc Green
anodizer - Boise, Idaho
2000
2000
Hi Phil,
Well I'm speechless :-). I never thought I'd even partially stump you on anything. At least we're on the same page and yeah you're exactly right on the button, the creamy white coating is exactly what it is. I decided to take some of this 2011 scrap I had here and trying it with different setups, it makes no difference, whether its low C/D or high C/D, low voltage, high voltage.
The material just seems to "buck" the process out and as you stated it does resemble that yes the bath(s) are removing as much as they are putting on a coating. If the parts are sandblasted I can get
.001 on the Diameter, if the surface is left unblasted I get no buildup, even after many hours of dwell time. As far as why the blasted vs. unblasted parts have a dia. buildup my only explanation for that is that a portion of the copper that is there on the surface is being penetrated and/or removed by the blasting and allows the surface to be hardcoated in very small thickness increases.
Update on material selection: Its a no go, just as you said its easy to machine for them and that was what they thought was the 1st thing to think of, when it comes to plating of any type I always liked this statement: Finish first then pick material according to finish type(s).
And yes you're right a hardcoat on a 6061/7075 would far far exceed the abilities of this material + hardcoat. I dunno I guess its just one more story for me when I too retire from the industry Phil :-)
Thanks Again Phil
plating company - Toledo, Ohio
While 2011 is a difficult to hardcoat alloy.... with the proper hardcoat system nothing is impossible. We have 2 different hardcoat systems here in my shop. One for normal work & one, called "IMPERV-X", for difficult to coat alloys, like 2011 & 2024. I don't think it would be a problem to do this job in our IMPERV-X system. What type of hardcoat system are you using? What are your parameters?
David A. Kraft- Long Island City, New York
2000
Impervex means nothing to 99% of the readers of this site. The original posting asked a question looking for information. It is an item of interest to many for the reasons stated by more than one respondent. Your reply is more of an advertisement than information.
What hardness do you get? What color do you get? What modern equipment or additive is available that will allow it to be done? What is your reject rate? What is your destroyed part rate? What special racking or handling does it require?
- Navarre, Florida
2000
Hi David,
It's a standard hardcoating based process 20% H2SO4 with a 2.5-3% additional hardcoat anodizing additive agent. The tank runs @ 40 deg F no matter what the load on it is (I know it's a little on the high side, but I gotta get a new Temp Controller installed on my chiller before I can go from 40 to -15 deg F.) Other than this there's nothing fancy about it, I go by the book and I have no real problems most of the time.
I think I ran into a brick wall for my capabilities. Basically David we've found a workaround for the limitations of the material and I think the engineer that picked said material has learned now after spending a few hours with me and some "back me up" data learned that the material is unacceptable for this use, but alas, they already have a batch of them made so they have to be blasted to add .001 and then H/C'ed to add another .001 (which is the max I've been able to get from them).
I know there's nothing wrong on my end, I can HC all other materials without a problem its just this thorn in my side 2011 stuff
:-). It anodizes Type II just fine, no problems whatsoever, but you hardcoat it and its worthless. Heck if you can hardcoat 2011, more power to you David cause I can't figure out how, with the setup I have.
plating company - Toledo, Ohio
2000
I apologize if people felt I was advertising; what I was trying to say is that there are proprietary hardcoat systems that can process almost anything. I was looking to inform a fellow finisher about special hardcoat systems out there that he or she can setup themselves. Sorry if I offended anyone.
David A. Kraft- Long Island City, New York
2000
A number of hardcoat anodizers have developed proprietary hardcoat processes to coat difficult aluminum alloys. It is possible to form thick, hard anodic coatings even on high copper 20 series alloys and high silicon die-castings. Some of these processes are more capable than others. Due to the competitive nature of our business and the time and effort required to develop this technology, it would be very unlikely that anyone would share these secrets in an open forum like the Internet.
Academic research and other published data is mostly dated or non-existent. However, an average hardcoat on a good alloy, such as 6061-T6, is normally as good or better than the best proprietary coating on a difficult alloy. Even though Luke Engineering's Lukon family of processes can effectively hardcoat these difficult alloys (including high silicon, high pressure diecastings, Phil), we encourage our customers to specify the better alloys wherever practical.
Luke Engineering & Mfg. Co. Inc.

Wadsworth, Ohio
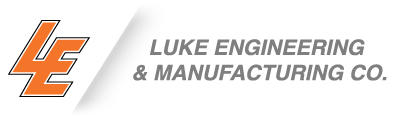
2000
by Brace & Sheasby
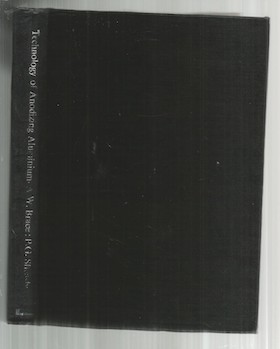
or AbeBooks
(affil link)
Ed. note: We can't expect David Kraft and Chris Jurey to give away expensively acquired trade secrets, but James Watts is also right that we don't want this technical information site to read like a 1950's toothpaste commercial: "Brush with Gleem -- only Gleem has miracle ingredient GL70!"
Update: If supporting advertisers mention their products we'll consider it a paid ad and we'll clearly mark it as an advertisement. Otherwise, we can't suggest brands & sources here anymore anyway ( huh? why?). The proliferation of automated spambots and the resulting 1000+ spams a day have made it impractical to do anything but throw away such submissions anyhow :-)
Q, A, or Comment on THIS thread -or- Start a NEW Thread