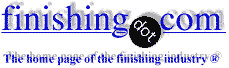
-----
Q&A on Barrel / Bulk Electropolishing of small stainless steel parts
2000
Q. We want to electropolish small parts (1/4 inch long and 1/8 inch in diameter) in batches of 2000 at a time in a barrel. The parts are made of 316 SS.
1. What is your experience of barrel electropolishing?
2. Will it work as well as rack ?
3. Any particular care we should take ?
Any suggestions?
Thank you for all replies
New Jersey and India
A. Mr. Malo, Most electropolishing processes that utilize bulk methods are proprietary to individual companies.
Dave McKayCleveland, Ohio
A. Hi, R. Unfortunately I guess I have to agree with Dave. I did a quick lit search and came up empty on guidance for barrel electropolishing. I've seen electropolishing done in little bowls for dental and medical needs; I've seen large production electropolishing in a rack operation, and seen the inside of tanks electropolished -- but sorry I've never personally seen barrel electropolishing. Chemical polishing, vibratory finishing, or tumbling might be alternatives.
Regards,
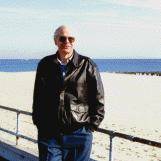
Ted Mooney, P.E.
Striving to live Aloha
(Ted can offer longterm or instant help)
finishing.com - Pine Beach, New Jersey
October 18, 2008
Electropolishing of small carbon steel parts
Q. We are manufacturing screwdrivers of Slotted head (-) and Phillips head (+) types. We use different metals to manufacture screwdriver bits like carbon steel, stainless and bronze metals. We are facing descaling, deburring and polishing problems. Currently we are using tumbling barrel with some media and chemicals but the result is not satisfactory. Some days ago we electropolished some screwdriver bits of carbon steel in laboratory by using a solution of phosphoric acid 75%, sulfuric acid 15%, chromic acid 10% and have excellent results. Can we use electropolishing method for bulk quantities for deburring and polishing the above three metals (carbon steel, stainless steel, bronze)?
What type of equipment should use? What type of solution will give best result? Can we replace chromic acid with some other?
- Lahore, Pakistan
2002
A. Hi Naveed. If you can feed these screwdriver bits with a vibratory feeder to align them and load them into plating racks, you may find it easier than electropolishing in a barrel or basket because the variable current involved in bulk electropolishing can result in etching instead of polishing. Good luck.
Regards,
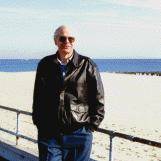
Ted Mooney, P.E.
Striving to live Aloha
(Ted can offer longterm or instant help)
finishing.com - Pine Beach, New Jersey
Q. How can small stainless steel parts (bolts/nuts/washers) be polished cost-effectively?
Please help.
- Johannesburg, South Africa
2001
A. Barrel electropolishing is a recognized technology. The barrel is indexed periodically and current is applied with the barrel at rest. Titanium screen is the material of choice for barrel construction.
Dan Weaver- Toccoa, Georgia
2001
A. A very efficient and economical way to electropolish small pieces is through a barrel process. Several parts can be placed in the unit and achieve the finish. You do, however, have to be cautious on the type of parts and how they are going to placed. There may be some "dead" areas on the parts where no contact has been made, edges may overlap, and the ID's cannot be critical.
Donna Nowak- Cleveland, Ohio
2001
RFQ: Hi,
I am looking for someone who can BARREL electropolish stainless steel. I would like to electropolish small stainless steel rings about 1/4 - 3/8 in diameter. We do approx. 100,000 at a time. Rack electropolishing is not cost effective.
Thanks,
- Bartlett, Illinois, USA
2003
Ed. note: This RFQ is outdated, but technical replies are welcome, and readers are encouraged to post their own RFQs. But no public commercial suggestions please ( huh? why?).
October 1, 2014
Q. We are a supplier of small Stainless steel Capillary pieces as per below dimensions:
ID: 0.58 mm
OD: 0.82 mm
Length: 45 mm
We are currently doing Electropolishing with Sulfuric Acid. But we are not getting good shine and surface of Capillary pieces still remain dull after electroplating.
Please suggest some process or chemical by which we can shine our capillary tube pieces in bulk quantity.
thanks
- Ahmedabad, Gujarat, India
A. Hi Chintan. Please review the electropolishing chapter in the Electroplating Engineering Handbook
to understand what they call the "etching" range and the "polishing" range of current density. Because the current swings radically during conventional barrel processing, you probably cannot get polishing. Some hints are given in the above dialog that a titanium barrel which periodically indexes, instead of constantly rotating, may be one of several keys towards getting the process to run satisfactorily. Best of luck.
Regards,
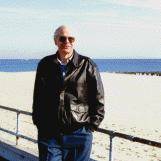
Ted Mooney, P.E.
Striving to live Aloha
(Ted can offer longterm or instant help)
finishing.com - Pine Beach, New Jersey
A. Bulk electropolishing of small stainless steel parts is possible and doable. We have installed such process already in BAMA company in Turbigo, Italy.
adv.
It requires Universal electrolyte, which we have licensed to them. Electropolishing is conducted in the device, similar to the wheel, submerged into the electrolyte.
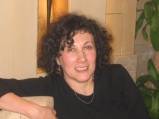
Anna Berkovich
Russamer Lab

Pittsburgh, Pennsylvania
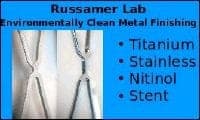
October 1, 2014
A. You can definitely Electropolish 316 stainless small parts in bulk using a barrel. I had one and used it to polish several million stainless jewellery parts. My barrel was constructed from titanium mesh supported on a bearing at one end only. It had an extra titanium mesh anode suspended inside from the open end. It was excellent and would polish approximately a 200 ml cup of small parts in a few minutes. Current and exposure time needed careful experimentation to optimise results. Quantity was determined by a fully exposed layer of components laying across the base of the barrel. Barrel would rotate slowly at about 5 seconds per single revolution. A few minutes additional polish in walnut shell media ⇦ on eBay or Amazon [affil link] media with a centrifugal or vibro bowl ensures a chrome like silky brilliant shine.
Ed PalmerLondon, UK
September 6, 2017
Barrel/Tray Electropolishing Help Please
Q. I work for a small company, we machine parts for water craft or anything that need excellent corrosion resistance. Lately we've been growing our orders but slowly have a backlog growing. Our main bottle neck is the Electropolishing stage. We currently have a Ti-Cu rack system set up. Our parts are machined from 316 stainless steel, we use a sulfuric and phosphoric electrolyte and then do a nitric acid passivation. Our current rectifier pumps out 15v @ 300A.
My question is regarding how to set up a barrel or tray system for bulk electro polishing. I have the basic knowledge about each system, but when it comes down to revs/sec or material to use I draw a blank.
From looking on the site I see that for the barrel system it's a guessing game for how fast the barrel should spin or how often if you are using periodically rotation. Does anyone have a solid time frame that produces good results?
I've also seen people post on here about using titanium/copper/ phospro bronze as the mesh/tray material. But has anyone had experience with Incoloy 020, 25-6, or 825? I've seen good results from those materials regarding chemical resistance but nothing on Electropolishing.
Last question (I hope) for the barrel Electropolishing, does the rotation of parts scratch or ruin the finish? Or is there a step afterwards to buff out such imperfections?
I know this is basically a guess and check thing finding out what works the best for us, but any ideas that'll shorten our R&D time is appreciated. Also any reference material on this subject to read would also help!
Employee - Bozeman, Montana, USA
August 2, 2019
Ed. note: This RFQ is outdated, but technical replies are welcome, and readers are encouraged to post their own RFQs. But no public commercial suggestions please ( huh? why?).
Q, A, or Comment on THIS thread -or- Start a NEW Thread