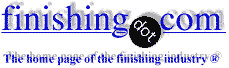
-----
Sulfamate Nickel Plating Problem: Compressive Stress
May 14, 2008
Q. I have been having problems with persistent compressive stress in my nickel plating tanks. From what I understand, the stress should progressively move towards the tensile side as more nickel is plated, but after plating for many hours at a high ASF, the stress does not change at all. I am using a bent strip test in a Hull Cell
⇦ huh?
to assess the stress level. I have read that the main cause of compressive stress is sulfur contamination. Could this be coming from the Ni S-rounds that I am using? The polypropylene bags surrounding the Titanium baskets are brand new and leached properly, and contain no rips or tears. The bath is relatively new, and the parameters are as follows:
Tank volume: 57 gallons
Nickel content : 76.5 g/L
Temp: 120 °F
pH : 4.0
Spec. gravity : 30 baumé
Barrett Additive 'A' : 22.5 g/L (chloride bearing salt)
Boric Acid : 45 g/L (saturated through use of polypropylene bag)
SNAP : 0.3 g/L
SNAC : 30 g
clear optical path manufacturer - Philadelphia, Pennsylvania
![]() |
A. What do you call high current density? What is the anode current density? What kind of anodes? Is saccharin used? In that small solution how much change in pH do you get in one run? Barrel or rack? ![]() Robert H Probert Robert H Probert Technical Services ![]() Garner, North Carolina ![]() May 16, 2008 A. If you have an organic contamination, such as saccharin, you will have compressive stress. If the nickel rounds are not active, you will have some plating from the baskets and insoluble anodes really drives the stress compressive. - Navarre, Florida May 16, 2008 A. Stress in a sulfamate bath is regularly controlled by varying plating parameters. Have you tried varying the current density? You didn't mention your ASF. Guillermo MarrufoMonterrey, NL, Mexico May 17, 2008 |
A. The sulfur in the deposit is coming from the sulfamate anion. it breaks down at the anode to form a volatile sulfur compound that functions as a stress reducer.
There are a couple of ways to reduce the tensile stress.
1. Let the bath sit overnight and bubble air through it. This gets rid of some of the stress reducer since it is volatile.
2. High current density dummying plates out the stress reducer.
3. Additions of chloride will make the stress go tensile and can neutralize the effect of the stress reducer.
Carbon treating is not very effective but helps a little bit.
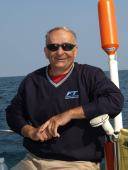
Pat Mentone
St Paul, Minnesota
May 20, 2008
Q. I have had some success in plating out the stress now using a large dummy cathode (23" x 23") and plating at around 5 ASF. After 5 days of plating, the stress has gone down from about 5 points on the bent strip test to a little less than 1. My mandrels are chromed glass that I use to produce this clear optical path targets. Because the chrome is so thin, my mandrels do not last long if I try and run them at anything above 20 ASF. Based on other troubleshooting solutions I had read before, I had plated between 75-100 ASF on a small dummy cathode (5" x 5") with no results. The pH has stayed stable through this, remaining at around 3.9-4.0. I had added a small amount of saccharin early on when the bath was running a little too tensile. I had also read about introducing NiCl to push the stress compressive, but it did not give me good results. Is there a specific type or method I should know about to introduce this into the bath?
Chris Hess [returning]- Philadelphia, Pennsylvania
May 22, 2008
A. Chris, I reckon your bath is in pretty good nick. From the information you give, I would expect to see a tensile deposit, although I would be slightly concerned about the high chloride level. Generally chloride induces tensile stress and most platers do not want that - they prefer either zero or slightly compressive stress.
sulfur depolarised nickel rounds are used with sulphamate nickel because the sulfur allows easy dissolution of the nickel without needing additions of chloride, that induces tensile stress. The beauty of sulfur depolarised nickel is that you do not need to add chloride to the bath to make the nickel dissolve; however, most platers still add about 10g/l nickel chloride, just to be on the safe side!
Sulphamate does not break down to sulphate and ammonia
⇦ on
eBay or
Amazon [affil link] below about
70 °C and this too induces tensile stress. Since you are operating at about 55 °C, there will be no problem with this.
As a generalisation, the higher the cathodic current density, the more tensile the deposit becomes.
I am perplexed about the compressive stress you are getting as there is no mention of any stress reliever, such as sodium saccharin - can you please confirm what additives are in the bath? I am not acquainted with the Barrett bath compositions, so it would also be helpful if you could say what SNAP and SNAC are chemically.
Finally, what stress levels are you aiming for? I do not understand what you mean by 5 points.
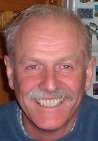
Trevor Crichton
R&D practical scientist
Chesham, Bucks, UK
May 27, 2008
A. In his last post, Chris says that he added a "small" amount of saccharin. Small is a terribly relative term and it is apparent that he added several fold too much.
James Watts- Navarre, Florida
May 29, 2008
January 20, 2015
Q. Hello everyone,
We do Nickel Sulfamate electroforming at the laboratory scale with [Ni]=75 g/L; [Cl]=4.4 g/L; [H3BO3]=30-40 g/L; at a controlled pH between 4.1 and 4.3 Maximum, and at 56 °C. The bath volume is about 6.5 L and under constant Filtration/recirculation through PP cartridge. Anode is a bagged Pt/Ti basket stacked with S-rounds.
The Substrates are Gold plated circular Silicon Wafers with photoresist pattern, and we deposit an average of 300 microns of nickel.
Additives are Commercial and include a wetting Agent and another Commercial formulation that is designed for mild leveling and stress reducing.
Previously our Wafers, plated at 1 ASD (10 ASF) over 28 hours would vary from mildly to extremely tensile in nature. With it, adhesion Problems, and Wafer breaking during subsequent processing steps were our daily lot.
We recently implemented both carbon filtration and double-legged stress strip tests in an attempt to control our process and master it. We also started making regular additive additions DURING Deposition. According to the manufacturer, every 1000 g of nickel deposited should be added around 500 mL of stress control additive and 25 mL wetting Agent.
So we decided that we would follow this procedure at a lower scale, because our bath volume is small compared to the quantity of Nickel we deposit every time (about 14 to 16 g).
Since these steps have been implemented, our Wafers vary from fairly flat to rather compressive.
Stress strips indicate from -93 to -77 MPa (-14000 to - 12000 PSI) very consistently.
My Problem is as follows: I would like to have complete control over my stress Level. This means I would like to be able to make more tensile or more compressive at will, not for practical matters, but because only complete mastery of my process will allow me to produce proper results and, well you know how it goes.
We tried plating the strips from 1 to 15 ASD (10 to 150 ASF) and the measured stress scatter is still within the previously mentioned margin.
A Wafer plated at 1 ASD however was slightly curved, while the next Wafer plated at 4 ASD showed a much stronger compressive tendency.
Therefore I'm having doubts whether I can trust the Strip method. Or is there an Explanation why the strips would indicate a fairly stable stress Level (±)20 MPa while the Wafers seem to react differently -- perhaps the plating of 300 microns and the unavoidable Gradient of thickness/current density from Center of Wafer to edges has an important effect?
Stress is supposed to become more tensile (less compressive) when increasing current density from what I gather.
What is your take on it?
Secondly, I believe that this level of stress is a bit too highly compressive, but I am very hard pressed to become more tensile through normal parameters. In fact, even reducing the temperature drastically (from 56 °C to 28 °C did not show a noticeable change on the stress strips; if anything, they seem even more compressive (we are not yet ready to waste a wafer on this).
Could you wager explanations and advice?
Best regards.
Development Engineer - Bern, Berner Oberland, Switzerland
![]() |
A. We used to occasionally plate a part with an inert anode--Pt plated Ti to drive the tensile strength down. - Navarre, Florida January 20, 2015 A. It's been many moons ago, but for several years I worked at making large, heavy, complex shaped nickel electroforms. Significant stress, compressive or tensile was an issue since the electroforms would distort. ![]() Jeffrey Holmes, CEF Spartanburg, South Carolina January 20, 2015 January 20, 2015 A. 1. The stress "reducer" you are using is probably saccharin which causes compressive stress - stop using it, start over, you cannot get it out of the solution. Saccharin is sold as a proprietary additive as a stress "reducer", it lowers tensile stress, and if too much takes it down into compressive. ![]() Robert H Probert Robert H Probert Technical Services ![]() Garner, North Carolina ![]() |
January 21, 2015
Hello and thank you for the prompt answers.
The anode is a stack of S-rounds so I expect the actual exposed surface to be higher by order of magnitude more than the exposed cathodic surface.
My point here is that I expect a low anodic CD. According to literature this, with S-rounds, should be the least of my worries.
I did suspect that Saccharin was accumulated when I realized that Carbon Filtration only had very minor effect.
The carbon itself is Sulfur-free according to manufacturer.
The manufacturer of additive recommends the following:
- Carbon filter periodically for about an hour (we do two hours with twice the recommended load of g/L in the cartridge) and then add 100% of the initial surfactant value (no surprise there) and 35% of the stress reducer.
This hints at the stress reducer being highly loaded in Saccharin or other Sulfur containing, non carbon treatable substances. Would you agree?
We'll have a new made-up bath with no additives at first and stress testing over the course of next week. I'll Keep you posted.
Best regards.
- Bern, Berner Oberland, Switzerland
A. I think no organic additives is a good idea. With good agitation and a clean bath, you should not need a wetting agent.
You might consider lower chloride, although it's effect probably isn't great.
And you could try a robber or shield around the perimeter to improve thickness uniformity.
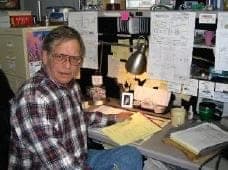
Jeffrey Holmes, CEF
Spartanburg, South Carolina
January 21, 2015
Q. The Absence of additives might be problematic however as they seem to be essential for obtaining the nano-crystalline Nickel that we Need for mechanical properties considerations.
Two questions:
- It seems that the Nickel Sulfamate has a high tolerance to overdosage of Saccharine, yes the stress becomes highly compressive and stays there. But it is exactly what it does, it stays there (in our case, around -100 MPa). Am I correct?
- Considering that we Need the additives for the micro (nano) structure of our material, do you believe that a combination of higher chlorine and lowering the temperature is a sensible approach to mitigate the stress back into the "slightly" compressive state (-20; -5 MPa).
Are there critical drawback to such an approach that I am not seeing?
Best regards.
- Bern, Berner Oberland, Switzerland
January 22, 2015
A. You're making this more complex.
Two ideas for low stress and small grain size.
1. Pulse plating in the few microsecond range. Whether it's too expensive to try ... depends, I suppose.
2 Replace the nickel chloride with cobalt chloride. Cobalt will happily co-deposit with nickel and will interrupt grain growth enough to produce small grains. A few percent cobalt/balance nickel have physical propensities virtually indistinguishable from 100% nickel. And you can then, unless some other concern pops up, run your bath organic-free.
In the distant past, when nickel was in shortage or outrageously expensive, more than a few platers simply added cobalt anodes and went right on plating.
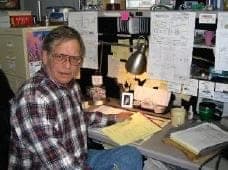
Jeffrey Holmes, CEF
Spartanburg, South Carolina
January 24, 2015
Thank you for this proposition.
We thought about pulse deposition but this represents a whole factorial design of experiment with 4 supplementary parameters (T-on, T-off, freq, peak current density) and that is if we go for simple waveforms.
For now in DC we are already close to a very satisfactory and repeatable result so this is not in our priority.
However, I'm looking seriously into Co additions. Having an organic free bath seems interesting.
If any of you is interested, carbon treatment did change something important : between 56 °C and 33 °C we now switch from compressive to tensile in a substantial manner. So we are looking for a balance between additives and temperature; given our very efficient temperature control setup it should work fine. We found the near zero stress parameter, let us see if we can keep it...
- Bern; Berner Oberland; Switzerland
January 26, 2015
February 6, 2015
A. I have 30 years working with Nickel Sulphamate without any problem; you should have a Preventive Maintenance Program in place.
Follow these items:
Carbon Treatment every 6 months.
pH test every week
Nickel and Boric Acid tests every month.
Anti-pit every month
Dummy 3 hours every week.
And, do not add any chemical that is not in the tech. data sheet.
- Miami, Florida
A. Low or zero stress nickel requires the use of nickel sulphamate baths. If you use S nickel rounds as the anode you technically don't need any chloride in the bath, but most users add up to 10g/l NiCl2; you can also add nickel bromide instead of chloride and this creates less stress. You should also not exceed 65 °C, otherwise the sulphamate breaks down to sulphate and ammonia and this creates stress. I would prefer to operate at about 2-3.5 A/dm2, as this also minimises stress, anything higher runs the risk of stress. Nickel baths are quite flexible with pH, but I would suggest you run at 3.8-4.2, as this keeps stress under control; lower pH's will increase stress. Regarding additives, I am a strong fan of sodium saccharin, but at low concentrations - up to 0.5 g/l; this not only gives a bright and hard deposit, but it also acts as a mild stress reliever. The down side of saccharin is that is contains sulfur, so the deposit can suffer from sulfur embrittlement if its I exposed to 150+ °C, so an alternative is to use cobalt as a brightener, but only at low levels. The cobalt will electrodeposit in preference to nickel, so you need to keep the bath content low (6.5% Co in solution gives about 30% Co in the deposit); say about 1-2% in solution. the other key essentials for low stress nickel are good filtration and excellent process control.
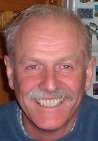
Trevor Crichton
R&D practical scientist
Chesham, Bucks, UK
February 10, 2015
A. Stress is a continuum. At zero sulfur content of the deposit, the stress is very tensile. As the sulfur content of the deposit increases the tensile stress becomes lower, goes to zero and then becomes compressive as the sulfur increases further.
Current density affects the sulfur content of the deposit. The higher the current density the higher the amount of sulfur in the deposit. Saccharin can be removed by high current density dummying.
Pulsing is very interesting. You can have many duty cycles and still keep the same plating rate or average current density. Low duty cycles mean high peak currents. High duty cycles have lower peak currents. The high peak currents plate out more sulfur than lower peak currents. So it is possible to keep the same plating rate and vary the sulfur content of the deposit by varying the duty cycle.
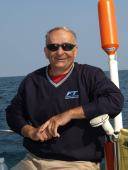
Pat Mentone
St Paul, Minnesota
February 12, 2015
A. Pat's comments are interesting. I like his idea of pulse plating nickel, as this certainly alters the grains structure and size, so if you get the conditions right, you should get a stress free deposit. There are even more opportunities with Periodic Reversal pulse plating, but you will have even more variables to alter to get exactly the right conditions.
Regarding a simple sulphamate bath (300 g/l Ni(NH2)2SO3)2; 30 g/l NiCl2; 30 g/l H3BO3) - it should have a zero stress at a cathodic current density of 5 A/dm2, increasing to about 110 Mn/m2 tensile at 16 A/dm2. My preference would be to reduce the NiCl2 and reduce the stress further. Ni-Speed baths are in comparison more compressively stressed at the same current densities. As previously mentioned, I like sodium saccharin - you can achieve zero stress at quite high current densities (35 A/dm2) with 1 g/l sodium saccharin, although at lower saccharin levels the deposit is tensile at this CD. If you wish to plate at only 10 A/dm2, you only need about 0.2 g/l sodium saccharin.
As Pat says, stress is a continuum and it is closely linked to the bath composition. However, the stress does start to flatten out at concentrations over about 3-4 g/l sodium saccharin, when the (compressive) stress is linked to the current density; the higher the cd, the lower the compressive stress.
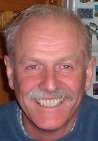
Trevor Crichton
R&D practical scientist
Chesham, Bucks, UK
February 16, 2015
adv.
"The Sulfamate Nickel How-To Guide"
by David Crotty, PhD
& Robert Probert
published Oct. 2018
$89 plus shipping
Q, A, or Comment on THIS thread -or- Start a NEW Thread