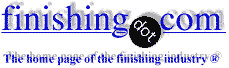
-----
Pitting and black spots during Anodizing

Q. Hi, Alaattin Tuna. I would like to know what your outcome was on these parts and what was the final result/solution. We are also struggling with this now, but only one one particular part and it was bead blasted by a different company.
I am not sure how to attach a photo if someone can assist to explain our problem
Michael van der Watt
- Western Cape
November 22, 2022
Ed. note: Attach the pic in e-mail to mooney@finishing.com please.
A. Hi Michael
You should follow this advice:
1- Check your anodizing bath for chloride contamination. Also check your rinsing baths before anodizing. Chloride concentration must be below 50 ppm.
2- All baths's grounding should be done, so check all baths's grounding connection. Also cranes's & hooks should be insulated.
3- You should not use rinse bath after neutralize bath before anodizing. Neutralization bath's rinse bath forms corrosion
- TURKEY Sakarya
⇩ Related postings, oldest first ⇩
Q. Hello:
I'm working on chromic acid anodizing plant (22 volts, 45 g/l free chromic acid). The sealing is performed using dilute chromates process. the material treated is wrought aluminum alloy 2024 and 7075 series. The problem I have is the presence of black spot on the surface of coating . The examination of the surface is done after sealing by X15 and X30 magnifier.
I ask if anyone may help me to understand the probable origin of these black spot and what is it?
Thank you for any help,
Said Ziane- Montreal, Canada
2001
A. This problem of black spots may be due to corrosion before anodising.
How do the parts come in to you - are they dry (not oiled)?
Are they degreased and left hanging about?
Try answering these questions and if you find the answer is yes to either of them you may have found your problem.
Walk the line with then and see if there is any step were corrosion could happen.
The corrosion has been halted by the anodising process but the parts need a concession, strip and re-process if you have tolerances to allow for the loss of base material from the strip op.
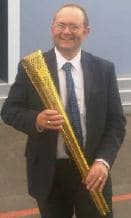
Martin Trigg-Hogarth
surface treatment shop - Stroud, Glos, England
Multiple threads merged: please forgive chronology errors and repetition 🙂
Q. We have recently run into a snag with our anodizing process. We are getting pitting on after the anodizing process. I'd like to know where to look to solve this problem. We've changed out our anodize solution but still have the issue. It seems that it's related to one customer and only polished parts... but the pitting is nowhere to be found on the non-anodized parts. All other customer parts seem fine, although the finish is not as high of a polish on most, but we did 4 batches of polished parts prior to this customer's parts and had no visible pitting; but on this customers parts there was severe pitting prior to dye.
Justin Martinmetal finishing shop - Liverpool, Pennsylvania
March 14, 2008
A. Let me guess, the parts were cast or extruded, then machined and then polished.
I will bet you a cheap cup of coffee that if you look at those parts after cleaning, etch and desmut, you will see pits with a 3 power glass.
I think that the pits have been smeared over and you are removing the smear.
Best effort would be to go to a non etch process for those parts. It is available from most chemical solution vendors.
- Navarre, Florida
A. Justin
You do not provide much information to be able to trouble shoot your problem remotely.
However, if you believe the material is root cause, have one of your competitor buddies run some of the parts and see if he has the same results.
- Colorado Springs, Colorado
? Hi,
Can you you please post some photographs of the pitting?
Thanks.
Srimay Basu
- Dubai, U. A. E.
A. What Mr Watts said PLUS: If wrought 7075, that is old or heat treated, the zinc has migrated into the grain boundaries and when you anodize you "de-plate" the rich zinc spots and leave a pit - and there is nothing you can do about that.
Or, what ever you mean by "polishing"? Are you imbedding iron particles from polishing media that has been used on iron? When you anodize a red spot or a pit is left behind.
Or, Chloride contamination in your new sulfuric anodizing bath. How pure was the acid? Was it yellowish or brownish? This would affect all parts but more pronounced on high polished parts. Also consider chlorides in the deox.
When you come back, and always, the first thing we want to know is the alloy !
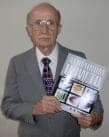
Robert H Probert
Robert H Probert Technical Services

Garner, North Carolina
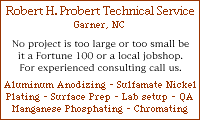
A. We ran into this problem a couple of years ago, it was very frustrating. We did however track the source of the problem and correct it. When we Polish or parts we first wet tumble, then dry polish. It turns out that the city had added a large dose of chlorine to counteract contamination from the runoff from a snow storm. It was this chlorine that leached into the parts after tumbling for several hours. We added a RO system for all incoming water and Voila, problem solved. Best of Luck
Dennis Paulson- Victoria, BC, Canada
Q. I have encountered this problem on and off for the past six months with bare 2024T81 sheet during phosphoric acid anodizing. The pits occur in clusters where the ink stenciling used to be (as applied by the mill). After PAA, you could still read the raw material ID. I suspected that the heat treater did not remove the ink prior to aging from T3 to T81 or it was simply left on the part prior to processing in PAA.
If anyone else has encountered this, I'm curious to hear what you think the root cause really is.
- Winnipeg, Manitoba, Canada
April 2, 2008
Multiple threads merged: please forgive chronology errors and repetition 🙂
Q. Hey all
Did you have any luck?
We have 1 mm anodized aluminum sheet which develops black spots.
We have not found the cause. We degrease the sheet with an acid based hydrocarbon degreaser, but if there were any imperfections, the acid should make white spots. it only seems to occur when we send the goods to a warmer region.
Dishwashing liquid removes the spots. is this because it is alkaline?
Bahrain sheet techies think it is foreign matter on the sheet which in some way is removed after anodising and leaves small mill finish spots which in turn corrode.
How can we neutralize the corrosion in an economical way?
All suggestions welcome
Regards
signage - Melbourne, Victoria, AUSTRALIA
June 30, 2008
? What is the thickness of the anodic coating? Is this thickness uniform all over the thin panel? Dimensions of the panel? How is it sealed? How reliable is the seal? Does it pass the ASTM B136 seal test?
It is very difficult to get thickness on thin panels.
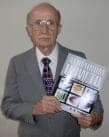
Robert H Probert
Robert H Probert Technical Services

Garner, North Carolina
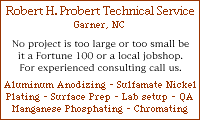
A. Hi Fons,
I would like to ask more questions about the nature of the black spots. For example, are they smooth and hard or of a "fluffy" nature like corrosion products often are? However, here a some comments and suggestions.
Perhaps the Bahrain techies are right and there spots on the aluminium which the acid fails to remove. If so, perhaps a light alkaline etch might be effective.
My own suspicion is that the problem lies in corrosion occurring in the sealing stage. Sometimes intermetallic compounds within the aluminium form electrolytic cells causing holes (pits) in the coating. The effect is usually most severe if racks have electrical contact with tanks and cooling coils. Titanium racks (where electrical contact is unavoidable) can also exacerbate the problem. However the electrical potential from the intermetallics can be such that corrosion occurs with the surrounding aluminium.
Actions to take are to electrically isolate racks from tank: strips of plastic will do the job. Keep the seal water at a low conductivity.
Whatever the cause, as the problem only happens when you send parts to hot climates, I wonder if they are completely dry when packed? If not, you will be dispatching them in a mini corrosion cabinet complete with heating to accelerate any corrosion. This will be particularly troublesome if you are wrapping in polythene.
Of course, even if you can avoid the problem during transit, the question of whether the product will corrode in use remains. The questions raised in the previous reply by Robert Probert take you back to fundamentals.
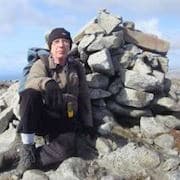
Harry Parkes
- Birmingham, UK
Thank you Mr Parkes and Mr Probert for your response. Sorry it took a year to respond but I am new to this internet game.
The shipping in a mini corrosion chamber probably was the culprit. these aluminum panels had acrylic faces on them, which in turn sealed in moisture and slightly moved around during transport thus creating bold spots at the high points on the alum sheet, moisture got in and the rest is history. happy days. we inserted paper in between and no more spots.
Stay tuned for my next adventure into the insane.
sign industries - Melbourne, Victoria, Australia
Q. Gents
I have a problem of black spots occurring after Anodize. The position of black spots is random though on extrusion profile I had a quick chat with an expert in Anodizing process and he said that this comes from extruded operation. I don't 100 percent believe him yet cause I think the Anodizing process parameter is one of root cause.
If an expert in Anodizing process suggest is right what should I improve or avoid?
Thank you for your cooperation.
- Lamphun , Thailand
July 20, 2009
![]() |
A. If your anodizing expert is really an expert, you should believe him - unless you have a strong reason to not believe him. - Navarre, Florida ? More information: alloy, titanium or aluminum racking, material of dye tank stainless or plastic, process sequence, free acid, dissolved aluminum. ![]() Robert H Probert Robert H Probert Technical Services ![]() Garner, North Carolina ![]() |
Q. How about chemical composition in Alloy I alway found in Al6061 do we need to look into Alloy composition?
Nakaret R. [returning]- Lamphun, Thailand
August 17, 2009
"Pretreatment Steps for Anodizing of AW 2017 Aluminum?"
Q. Hello respected Anodizers,
We are doing 10% Sulfuric Acid Anodizing with Oxalic acid using titanium racks. Item is made of Aluminium rods, Type 2017.
Process sequence:
Degreasing (Caustic + Soda Ash at 40 degrees Cent.)
1 x rinsing in tap water
Chromic acid pickling
1 x rinsing in tap water
Anodizing
1 x rinsing tap water
Sodium dichromate passivation at 85 °C. (in Iron tank)
Sealing in Sealant at 85 ° (In iron tank)
1 x DI Water rinse.
We are frequently getting black spots on the surface of the items anodized which are in the form of small black pits when observed under a microscope.
As per our experience these are due to the oil stains or dirt left over during previous machining operations and left on the items due to ineffective cleaning.
Can some experienced anodizer please help us as to what are these black spots and how to get rid of them?
Thanks
Yasir
- Karachi, Pakistan
May 7, 2013
Q. Hi all...
We have a strange problem of pitting after anodizing. This problem occurs sometimes on some racks (not all racks). Also we see this pitting on racks stick. So I don't think it's related to source of extrusion. Is there any comment?
- Sakarya, Turkey
July 20, 2013
Q. I have a problem about pitting with some anodized profiles. These pits do not occur on every rack. I realize this problem before the anodizing bath. Also we can these defects on racking rods, so I suppose it is related to the etching bath.
But than I ask myself: why doesn't it occur on all racks? Also sometimes I think about metallurgical reasons like corrosion or extrusion quality. So, I have a dilemma ... how can I get rid of this trouble?
Regards,
- Turkey
December 21, 2013
A. As per the photograph it appears like chloride corrosion. Please get your anodising bath solution analysed for chloride. It may have been contaminated. At the same time check all the incoming water to your anodising line for chloride content as well. Perhaps you can apply a simple straight forward check on your incoming water by using few drops of 10% Silver Nitrate solution in to the water sample which will tend to milky/ cloudy precipitation if there is chloride even in traces.
The only remedy if chloride contamination has taken place then clean the entire anodising line and replenish only with fresh solutions.
Anything from 65 ppm of chloride content corrosion would begin without any specific pattern; but if the content escalates around 120 ppm then problem would occur quite vigorously in every load of anodising.
It has been found sometimes that whenever any anodising line uses city water in the pretreatment baths without proper control those lines usually get contaminated.
- Dubai, U.A.E.
Q. Dear Mr. Basu,
I won't agree with you because firstly, I'm confident of anodizing bath's solution. We use RO water; we check it weekly. Also I mentioned about problem; it doesn't happen every rack. If we think your thesis right, all racks must be like that? So we couldn't produce any. I don't know, do you think I'm wrong?
Regards,
- Sakarya, Turkey
A. First of all I would check if pitting occurs on preferential surfaces pr all around the profiles. In your case, most probably it occurs on preferential ones. If this is the case, you may have a storage problem and the action of alkaline fumes, both from the ambient and from proximity with etching baths which will deposit tiny corrosive particles on the exposed surfaces of mill finished bundles of profiles or on skips. Acidic etching even would not remove the defect and the only solution, should you identify the problem by close examination before anodising is to polish the contaminated surfaces, at time deeply. Same solution in case you strip the anodised metal: polish it before re-anodising.
Richard Reed- Naples, Italy
A. Dear Alattin,
I am sure that you must be using RO water in your anodising baths and so the others. But as I have said in my previous reply that there will be no specific pattern of occurrences when Chloride content is low; but when it exceeds 150 ppm then one would expect in almost every load. Anodising bath gets contaminated through carry over from each load and gradually it gets build up over a period of time.
It will be better if you get your bath analysed for chloride content only perhaps to be sure.
Good luck....
S. Bassu DUBAL
- DUBAI, U. A. E.
A. The reason for pitting may be cell effect (galvanic corrosion) if the flight bar / work piece comes in contact with the process tanks.
Timur Ulucak- Istanbul, Turkiye
Treatment &
Finishing of
Aluminium and
Its Alloys"
by Wernick, Pinner
& Sheasby
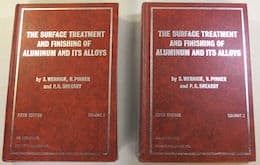
on eBay or Amazon
or AbeBooks
(affil link)
A. In my 30 years of experience building, managing and operating anodizing facilities, this appears to be galvanic corrosion. This can occur when a cleaned load is allowed to sit in a rinse tank containing low pH rinse water for an extended period of time. The fact that it is not every rack or piece does not always rule out this effect, as there are slight differences in the resistance of the connections to the work bar from the racks. If you need to store cleaned loads prior to anodize, make certain the pH of the rinse, especially after desmut is neutral, preferably low in chlorides, as the chlorides act as an accelerator to the galvanic effect. We are talking very slight voltages between the work bar and the tank solution, often expressed in millivolts and milliamps of voltage and current. Proper grounding of the rinse tanks helps solve this problem, as does storing loads in an RO water rinse tank, using polypropylene tanks, or filtering the city water to remove the chlorides, or all the above. When properly designed, a load can be safely stored in a rinse prior to anodize for up to 15 minutes without issue, but an improperly designed system may exhibit this issue in as little as 2-3 minutes or less if the pH is very low and the work bar rests on a metal support on the tank providing continuity. Insulation of the work bar from the tank at the tank set down point is the first thing to verify.
Scott
- Green Bay , Wisconsin
A. I agree with Scott.
Seen this condition or similar many times. Usually when you see a defect it is rarely attributed to the tank it just came from. First rule is generally always look back. I have seen this condition also caused by contaminated rinse tanks that are either not grounded properly and a small amount of current is present and causing an anodic reaction.
What had peaked my interest and hence my response is that the defect is not prevalent within the entire load. Albeit the question did not state if it was random, or exhibited to one end; I have seen one side of the rack exhibit these characteristics and after confirming all rinse and or process tanks in specification, it took following some loads around the line to determine source. That took some time as on both manual and automatic running lines, there are delays that are not necessarily consistent form load to load. Particularly manual lines, difficult to pin point this cause as operators are more on the ball moving loads in a timely fashion when the Manager is monitoring. What we found on warm days was the operators would open an overhead door on one end to let in fresh air. If the wind was blowing in the door, it was partially drying the load closet to the door and even if timely movement of the load to next tank took place, it was too late.
Just another item to look at.
- Calgary Alberta Canada
Q. I AM HAVING A PROBLEM THAT DURING sulfurIC ACID ANODISING PROCESS, AT 14 °C TEMP, 10% SOLUTION, THE JIGS ARE MELTING IN BATH AT THE EXACT LEVEL OF ELECTROLYTE SOLUTION. AND ALSO THE COMPONENTS ARE GETTING PIITING. PLEASE SUGGEST.
KATARU EDUKONDALU- HYDERABAD,TELANGANA, India
July 14, 2015
A. Hi Kataru. We appended your inquiry to a thread which should offer you some good hints about the pitting issue, while also suggesting the kind of information readers would probably need to comment further. The aluminum alloy which you are anodizing, and the form (cast, extruded, machined) would be vital info. As you see, a photograph of the pitting would help. Also, is this a new problem on an anodizing line which has been running successfully for a long time, or is it a new installation which has never yet yielded satisfactory production?
Regarding the dissolution of your anodizing racks at the solution level, are you certain that this is happening in the anodizing tank per se, and not in an earlier tank like the etch tank or de-smut tank? Thanks.
Regards,
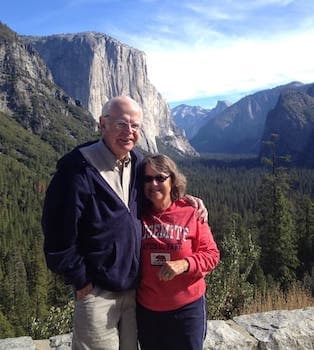
Ted Mooney, P.E. RET
Striving to live Aloha
(Ted can offer longterm or instant help)
finishing.com - Pine Beach, New Jersey
Q. Hi Ted Mooney,
regarding my question of dissolution of racks in anodising bath, bath was new, and there is no problem in etching, & desmutting. The components are machined, small aluminium plain washers. The problem is the components are getting pitted and along with racks. We are not facing the pitting problem in other components.
Regards.
- HYDERABAD,TELANGANA, India
Pitting after anodising
Q. Can anyone tell me why a batch of 6 parts that are anodised, 3 of them would come out with pitting and a crack on them and the other 3 came out okay. They were plated all at the same time; the faces that had the problems on them were all masked with lead tape and plated at temp of 40 °C for 42 minutes.
andrew thomasplating shop worker - uk
September 22, 2015
![]() |
A. Lead tape is not good for a mask in the anodizing process. ![]() Marc Green anodizer - Boise, Idaho A. The temperature was too high for one. But give us more info: free acid, dissolved aluminum, ALLOY, heat treatment, then come back, ![]() Robert H Probert Robert H Probert Technical Services ![]() Garner, North Carolina ![]() |
Q. Further to my post about pitting and crazing during plating, I said that we use lead tape. What would be a better solution? Also, we plate at temperature 40-42 °C, which from the reply I got, was too high. What should be the correct temperature?
Foot note: I've only been on this process for 18 months and that's the temperature that they have always plated at. Thanks.
andrew thomas [returning]plating shop worker - uk
September 29, 2015
Hi Andrew. Your temperature seems a bit high for chromic acid anodizing -- it's normally 95 °F ±4°F (35 °C ± 2 °F -- but not outlandish. I think the issue there was that I and the other readers assumed you were doing sulfuric acid anodizing rather than the ever rarer chromic acid anodizing.
Regards,
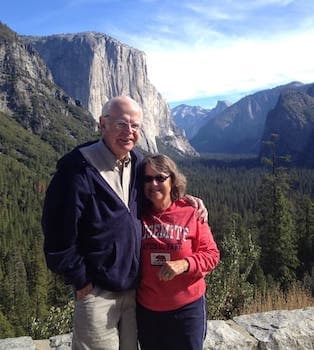
Ted Mooney, P.E. RET
Striving to live Aloha
(Ted can offer longterm or instant help)
finishing.com - Pine Beach, New Jersey
A. Ted is correct, I assumed you were talking about sulfuric acid anodizing. My knowledge of chromic acid anodizing, and proper masking materials is practically non-existent.
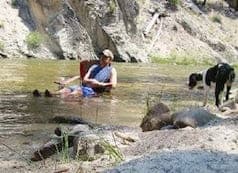
Marc Green
anodizer - Boise, Idaho
A. Hi Andrew,
40 °C is pretty standard in the UK for chromic anodising, usual range you find for wrought materials is usually 38-42 °C, for cast materials you would want to drop the temperature to 32-35 °C.
What alloys are you anodising? 2xxx series alloys with relatively high copper content (4.4% nominal for 2014 and 2024 alloys) and commonly suffer from localised corrosion, which appears as little black spots. If the corrosion is present in the material before anodising the anodising can emphasise the fault.
Aerospace - Yeovil, Somerset, UK
October 7, 2015
Corrosion of 7075 Aluminum after Alkaline Cleaning
Q. We have been experiencing some trouble with 7075 aluminum. The parts were received for anodizing and when the parts are coming out of the mild alkaline cleaner/soap, they have been dotted with corrosion markings on them that were not evident when racked for processing. This only seems to happen with 7075 and has happened a few times lately. Has anyone experienced this or does anyone know what may be the cause?
Charlene NAUSSPLATING SHOP OWNER - DARTMOUTH NS CANADA
February 22, 2016
A. Until you send more information I will wild guess what is going on. Apparently the cleaner is slightly etching. Apparently the 7075 has been heat treated or the surface has been heated by machining or forging. The heating brought some of the zinc out of alloy as a molecule, then on the surface the cleaner etched away at the exposed molecular zinc, showing you a corrosion spot. Very common with Chinese/Mexican metal and/or with forged gun receivers.
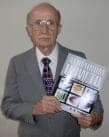
Robert H Probert
Robert H Probert Technical Services

Garner, North Carolina
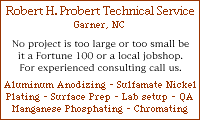
A. I have attached 2 photos showing the problem we have experienced on 2 different parts within the last 2 weeks.
I want to thank Robert for his reply. We have not had this happen before but now that it has happened twice on 2 different clients parts, we want to try to figure out what may be the cause.
We suspect a bad shipment of aluminum but there is no way of knowing that. Then we thought it may be contaminated at the manufacturing of the parts with cutting fluid.
We had to hand sand using Scotch Pads and just did a light etch and black dye and they turned out acceptable, but what a nuisance to have to do 300+ parts and to keep our clients satisfied with our service.
Charlene NAUSS [returning]PLATING SHOP OWNER - DARTMOUTH NS CANADA
A. Your pictures are typical of what I have seen before on some batches of 7075. Thee is really nothing you can do, but anyway, just try a slower ramp and let us know. Also let us know the free acid and the dissolved aluminum.
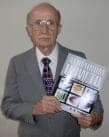
Robert H Probert
Robert H Probert Technical Services

Garner, North Carolina
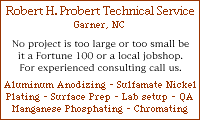
February 23, 2016
![]() |
A. Good day Charlene. Aerotek Mfg. Ltd. - Whitby, Ontario, Canada A. Charlene - Colorado Springs, Colorado |
Q. Hi.
To anodize AW 2017 how are the pretreatment steps done?
The alloy contains 1,5-2 percent copper.
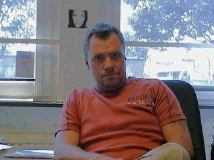
Anders Sundman
4th Generation Surface Engineering
Consultant - Arvika,
Sweden
July 24, 2020
A. Spend 2 or 3 minutes ramping up to 21 volts, otherwise same as any other alloy.
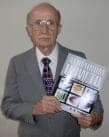
Robert H Probert
Robert H Probert Technical Services

Garner, North Carolina
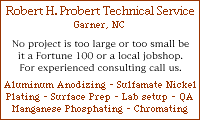
July 24, 2020
Hello.
I am also trying to anodise aluminium 2017 4-4,5% Copper
but process fails--
1. degreasing
2. rinse
3. etching- 1-5 mins, part stays black
4. rinse
5. Nitric acid (30%). first step 1 minute, black oxide goes almost off, then washing, washing, and second dip in nitric. it cleans material much better.
6. anodising.
6.1. tank 200 g/l H2SO4, SS (316) anodes, temperature 5-20 °C. Tried different temperatures from 5-20, no difference. time- 30-40min. 24 volts (ramp) and 1-2 amps
6.1.2. coloring- 30 min. after coloring all part is with black dots, like black sand. Can wash off with water, but leaves marks.
6.1.3 sealing 90 °C 30 mins. part is with dots and like black rain.
6.2. chrome salt 35 g/l + H2SO4 120 g/l.
6.2.1. time 30-40 mins. 24 volts 1-2 amps/dm.
6.2.2. coloring black-- can see little black dots
6.2.3. after sealing is black dots again. Much less than in H2SO4, but still it is error.
I tried lot of variations with rectifier.: slowly ramp, fast ramp 1-24 volts ... no results.
After anodisation all looks normal, no errors, just after coloring it happens.
Photos attached with errors.
Normal aluminium is working Okay.
Also I am interested to anodise these aluminium alloys:
1.AW 6082
2.AW 2011
3.AW 2017
4.AW 2024
5.AW 7020
6.AW 7075 T6
Any help? Thanks
- Latvia Liepaja
July 30, 2020
Ed. note: google Ignus Sudzhis' name to see his work on pinterest, youtube, etc.
A. The first thing I would do is reduce the etch time to as short as you can get away with. You are seeing the 'grain' of the stock material, which is made more apparent as the etch process removes various components of the alloy at different rates and exposes/leaves behind material that will not anodize, and therefore not color, evenly.
The higher the Aluminum content in the starting alloy, the less it will be prone to this problem. And related to that, alloys that are high in Magnesium or Copper are quite difficult to get the very even finish you are looking for after dyeing.
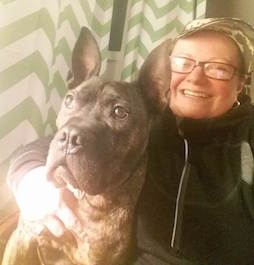
Rachel Mackintosh
lab rat - Greenfield, Vermont
July 31, 2020
Q. Dear sir,
We are facing black dot or spots issue on the aluminum anodized surface please let us know what is the reason for this and solution to rectify this problem.
Please find the below pictures for your reference.
Best Regards,
K Tarun Reddy, Managing Directormetal finishers - Hyderabad, India
July 25, 2021
A. Hi K Tarun.
You will see that we appended your inquiry on the subject going back to 2001. Also, you'll see lots of photos very similar to yours on thread 45421. Please do a brief review of the two threads and you will either quickly solve your problem or at least be able to offer a detailed follow-up that readers will be able to help you with.
Luck & Regards,
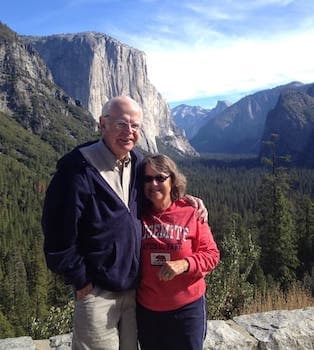
Ted Mooney, P.E. RET
Striving to live Aloha
(Ted can offer longterm or instant help)
finishing.com - Pine Beach, New Jersey
Readers -- please see thread 45421, "Black spots problem in anodized aluminum" for many more photos and possibilities.
Q, A, or Comment on THIS thread -or- Start a NEW Thread