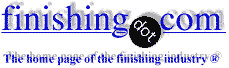
-----
Galvanising - Reduce & Recover Zinc Ash and Dross

Q. Dear Sir,
You reference an Ash Box, what is this and how it is able to reduce the ash % please do share your advise on this.
Thanks,
GM, Galvanizing - Chennai, Tamil Nadu
April 22, 2022
A. An "ash box" is one name for a system of keeping the ash trapped at one end of the kettle, floating on the zinc. The hope of some is that this will allow some metallic particles to separate into the bulk of the zinc, allowing ash to be removed with lower Zn metal contained. It sometimes works. More useful though, is that it can concentrate the ash at one place so that it can be agitated in order to break down larger lumps, and free metallic pieces to re-join the bulk of the zinc. The ash box is sometimes called a "weir" (as in a dam that is open at the bottom. It is usually steel, and forms a barrier across the width of the kettle, and is perhaps 10-20cm deep.
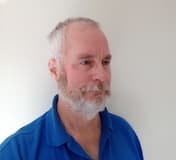
Geoff Crowley, galvanizing consultant
Crithwood Ltd.

Bathgate, Scotland, UK
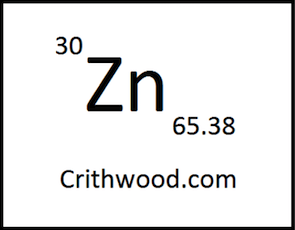
[editor appended this entry to this thread which already addresses it in lieu of spawning a duplicative thread]
Q. Hi,
1) How calculate Ash and dross consumption in hot dip galvanizing process?
2) It depends on total wt. of production or Total Area?
- Gujarat, India
April 30, 2024
Ed. note: Let us know if questions remain after reviewing the thread.
⇩ Related postings, oldest first ⇩
for Engineers, Shops, Specifiers
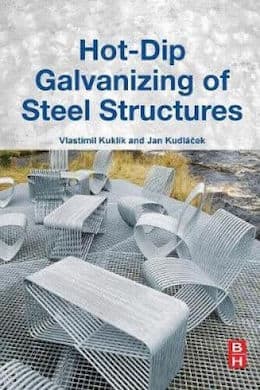
avail from eBay, AbeBooks, or Amazon
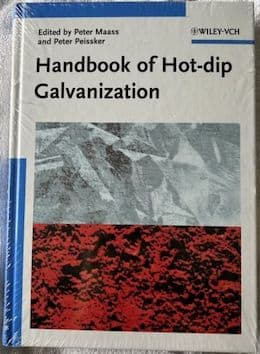
avail from eBay, AbeBooks, or Amazon
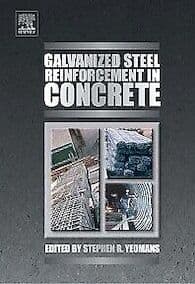
avail from eBay, AbeBooks, or Amazon
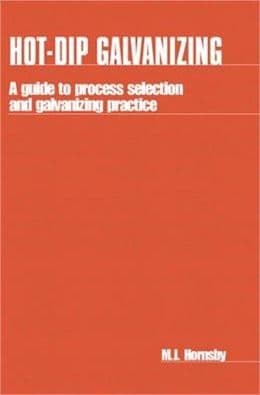
avail from eBay, AbeBooks, or Amazon
avail from Amazon
"User's Guide to Hot Dip Galvanizing for Corrosion Protection in Atmospheric Service" by NACE (1997 only rarely avail.)
avail from AbeBooks, or Amazon
(as an Amazon Associate & eBay Partner, we earn from qualifying purchases)
Q. Dear sir:
I am interested in knowing if there is a relationship between the production of my galvanizing plant(Ton) and the production of Dross and Ash, under normal operation of the plant (controlled temperatures on the kettles 450 °C).
Should a galvanizing plant have these values under a specific percentage?
What are these percentages?
Thanks for your help.
General Galvanizer - Medellin, Colombia
2005
A. In Italy we see these numbers as correct:
ash < 12% zinc consumption
dross < 13% zinc consumption
optimum when ash+dross< 20% zinc consumption
greater numbers are generated by problems in flux-dryer or pickling operations
Kindly regards,
- Verona, ITALY, EU
Multiple threads merged: please forgive chronology errors and repetition 🙂
Q. We have a galvanising plant which has been operating very successfully.
We would like to know what should be the percentage of Zinc Ash and Zinc Dross, of total Zinc consumed in the process.
What could be the reasons for high ash and dross generation?
Plant Manager - Sharjah, UAE
January 12, 2008
A. Sir:
Thirty years ago I related ash, and dross to zinc consumed. In those days ash above 13% and dross above 10% (both related to zinc consumed) was considered excessive. Thus 77% of the zinc was on the product.
In more recent years I related ash, and dross to product galvanized. Ash above 0.8% (no ash box), ash above 0.4% (manual ash box), and ash above 0.2% (motorized ash box)in relation to production is considered excessive. Dross above 0.6% in relation to production is considered excessive.
Excessive ash is usually a result of bad flux, and excessive dross is usually a result of poor kettle furnace design or poor kettle maintenance.
Ash is now often reclaimed to zinc with a machine that looks like a small cement mixer/heater. A recovery of 70% to 80% is common for a "dry" kettle galvanizer.
Regards,
Galvanizing Consultant - Hot Springs, South Dakota, USA
A. Iron (Fe) in the flux (possibly due to poor or no rinsing after acid pickling) is a prime cause of dross formation. Fe concentrations should be kept below 1% in the flux.
Very wet steel entering the zinc is another prime cause of ash formation.
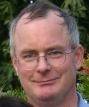
Geoff Crowley
Crithwood Ltd.
Westfield, Scotland, UK
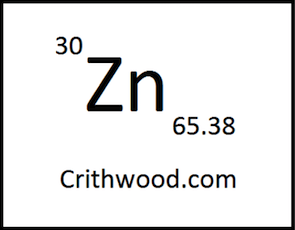
Geoff,
In the early days, I purified many, many flux solutions. This involved removing the iron +2 using hydrogen peroxide and ammonium hydroxide, by testing first and then using formulas and methods that work. In plants using sulfuric acid the sulphate was removed from the flux using barium chloride dihydrate (anhydrous powder barium chloride is too dangerous). These were all "dry" kettle galvanizers. Many of these galvanizers were looking forward to less dross after iron +2 removal from their flux. It NEVER happened. The dross formation was unchanged after iron+2 removal from the flux solution. Their %GZU was decreased by 10% to 30% (mostly thinner zinc on the product and less dry ash). I suspect that iron in the flux is converted to small "dross islands" in the zinc surface on the galvanized steel.
I have no experience with iron+2 removal from a "wet" kettle galvanizer's flux solution. I suspect that it WOULD reduce dross because the top flux would collect iron from the flux and then form dross at the top-flux/zinc interface. Some "wet" kettle galvanizers change out their top flux often and I suspect that they have found that this reduces dross formation.
In recent times we have found other methods to improve galvanizing, to the point, where many galvanizers use very, very bad flux and still they get excellent results. It is amazing how new technology changes "the rules of the game."
Regards,
Galvanizing Consultant - Hot Springs, South Dakota, USA
Q. For molten bath temperatures in the range 475° C are required. I am investigating the best suited type of heater for this duty. I suppose that electric induction heaters are a recent phenomenon; but I doubt its utility in the areas where power shut-downs are frequent. Does ruling out this option not leave behind any other than furnace oil (dirty but potentially cheapest fuel) heaters. I look forward to hear from the experts. Thanks a lot in advance.
Rajesh Kulkarni- Pune, Maharashtra State, India
May 2, 2008
⇦ Tip: Readers want to learn from your situation;
so some readers skip abstract questions.
Q. Hello.
Sir, I want to know what should be percentage and actual percentage of Zinc Ash & Zinc Dross during manufacturing of Galvanized Steel Pipes and input/output ratio of Zinc for this process.
- Jaipur
March 30, 2011
⇦ Tip: Readers want to learn from your situation;
so some readers skip abstract questions.
Q. How to purify zinc dross to get pure zinc?
Ganesh Gaikwadstudent - Thane, Maharashtra, India
August 3, 2011
Q. In a galvanising line with 120 MT Zinc bath, is dross generation of 5 MT per month, on an average production of 4500 MT high or acceptable ?
Shishir DesaiProduct engineer - Mumbai, India
September 17, 2011
A. Sir:
Your dross to production percent is:
%Dross/Production = 100% times 5/4500
%Dross/Production = 0.11%
This is four times lower than ANY I have ever calculated.
I suspect that you have a new kettle and have not had enough production yet (likely only 3 months or less of production) to experience normal dross levels. Another possible answer is that you are not getting the dross out of the kettle (e.g., using a clam), thus allowing the dross to accumulate.
Regards,
Galvanizing Consultant - Hot Springs, South Dakota, USA
⇦ Tip: Readers want to learn from your situation;
so some readers skip abstract questions.
Q. How to reduce ash formation in galvanizing.
abhijit palaskar- dubai, uae
June 23, 2013
A. Hi Abhijit. We appended your inquiry to a thread which offers good hints. We also have several other threads on the subject if you are patient with the search engine. If you have a highly specific question on the subject, feel free to post detailed data and people can try to help you. Good luck.
Regards,
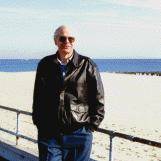
Ted Mooney, P.E.
Striving to live Aloha
finishing.com - Pine Beach, New Jersey
Q. Hi
Thanks for your helpful comments
We have some problems in our dry jobbing galvanizing line, too. Some problems are usual, but the high amount of ash, produced in our line, is not usual and I'm looking for a solution to reduce it.
We have a steel kettle (6*1.5*1.2) and use Hydrochloric acid, and Ammonium chloride for flux -- about 0.01 Al and 20 Cm Pb at bottom, and no ash box.
We are galvanizing usual low carbon steel, and in little part, the cast iron.
My Question is how much ash production is normal in our line ?
Is there any way to reduce it ? or, is there any alloying metals or additional materials to use for reduce ash production ?
I heard Cd, Mg, Sn and Sb can effect on ash production, is that true ? and how much we should use to inhibit ash production?
Regards.
- Karaj, Tehran, Iran
July 27, 2013
A. Sir:
Cd and Sb (antimony) are extremely toxic. Magnesium causes much white rust. Tin cracks the steel if over 0.4%. Cast iron is known for excess dross. Usual dross is less than 0.6% of production. Ash with no ash box is 0.8% of production, with ash box ash is 0.4% of production and with motorized ash box is 0.2% of production. Bad flux (e.g. straight ammonium chloride) causes much smoke and ash.
Regards,
Galvanizing Consultant - Hot Springs, South Dakota, USA
Q. Dr. Thomas H. Cook , thanks for your answer.
You say about using "ash box", I search about it, but I find just some general explanation : (A manual ash box is about 16 inches square on top and about 18 inches square on the bottom (or a rectangle of similar square inches). This semi-pyramid shape keeps the ash from plugging up the ash box. (The sides get bigger as you go down.) Both top and bottom are open. The manual ash box is mounted about 1/3 in the zinc and about 2/3 out of the zinc. The total height of the ash box is about 18 inches, etc.)
But, How does it work?!
Could you please send some picture or video about working ash box ?
We use ammonium chloride in direct, as melting flux, and you hint that using directly, increase ash and smoke production. Is there any other flux to use with less ash production?
Thanks a lot.
- Karaj, Tehran, Iran
A. Sir:
To use an ash box, simply use the ash shovel with 1/4 inch holes and skim off the ash and put it into the ash box. From time to time poke the ash in the box downward and it will remelt. This is a dirty, smoky job for the worker and the zinc should not have lead or nickel in it. Normally this cuts ash in half. A motorized box does this automatically and zinc recovery is better. A thin steel cover keeps much smoke down. For kettles with not enough surface area for an ash box there is a commercial ash recovery machine (looks like a small cement truck) costing about $80,000 which pays out in one year for a galvanizer doing 30,000,000 pounds galvanizing/year.
Regards,
Galvanizing Consultant - Hot Springs, South Dakota, USA
Q. Thanks a lot for your answer.
In general, we use Ammonium chloride in direct, as flux, and as we know, it makes lots of smoke, dross and ash.
We have not big problem with smoke and dross. In fact, the ash production is our Big problem and I have to reduce it.
What you offer to use as flux (liquation) in direct for "driving out" stage (and less ash production)?
Regards.
- Karaj, Tehran, Iran
August 13, 2013
Q. Is there any other material to use?
Thanks for your helpful answers.
regards.
- Karaj, Tehran, Iran
August 28, 2013
Q. We are a recycling company with more than 10 year on our field. Our goal is to supply galvanizers with quality zinc, and selling the low quality zinc in other applications. In the past days we have received a complaint regarding the quality of our zinc (we have spectrometer and analyze each melt) and the zinc we supply for galvanizers is 99.70% Zn Min and .15% to .30% Fe Max. Our customer is telling us our zinc is generating excessive dross and ash in their process (I have supplied the same zinc to other galvanizers who haven't had any problems). They are wire galvanizers and have increased their production in the past months, as I know they have an induction heater in the pot and they check the concentrations on the flux but don't review the iron content on it. My question is the following, which could be the causes generating the excessive dross and ash?
Enrique Garcia- Monterrey, NL, Mexico
April 21, 2014
A. Hi Enrique. Dr. Cook asserts that excessive ash is most often the result of poor flux, and excessive dross is the result of poor kettle design and maintenance. Mr. Crowley added that Iron in the flux, perhaps from poor rinsing after pickling, and very wet steel, are other causes of excess ash. These sound like they may be related to your customer's increased production rates? Please try your best to frame your questions in terms of the answers that were already provided if you can :-)
Thanks and Regards,
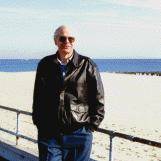
Ted Mooney, P.E.
Striving to live Aloha
finishing.com - Pine Beach, New Jersey
A. Dear Mr. Enrique Garcia
Your Iron content is too high for a galvanizing operation, Iron solubility at 450 °C is 0.035 %; excessive iron will combine with zinc (1 gram iron with 24 grams of zinc) and create dross.
I guess you are doing pyrometallurgical reduction, but galvanizers require 99.995% purity for zinc, which cannot be achieved by your method.
- Doha, Qatar
Q. I will change the flux bath to below composition :
NH4Cl = 172 gr/lit
ZnCl2 = 225 gr/lit
pH = 3.9 -4.2
ACN=1.17
B.N (@15 °C)=25
IRON content=1.19 gr/lit
volume of bath = 23 M3
dry galvanizing system
WHAT IS THE DROSS/production CHANGES in variation of bath temperature?
- tehran, iran
May 22, 2014
Control of ash generation
A Guide to process Selection & Galvanizing Practice"
by M. J. Hornsby
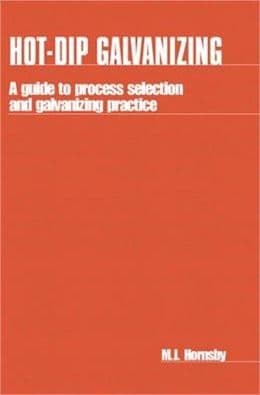
on eBay or Amazon
or AbeBooks
(affil link)
Q. Dear sir,
We are facing the problem of ash generation in kettle. Our ash generation is 1.16 %. It is very high.
We are using 30 baumé double salt flux for galvanizing, and we are galvanizing tower lines (5 mm to 20 mm thickness) and cable trays (2 mm) material. Our flux temperature is 30 °C.
How are we to solve this problem?
Please give your expert advice to me and help us to solve the problem.
student - satara, Maharastra, India
May 12, 2015
Hi Kiran. We appended your inquiry to one of several earlier threads on the subject. After noting some of the good advice that has been offered, you may wish to post some more specific questions about that advice. Best of luck! For the record, "expert advice" can be offered only by paid consultants with on-site access to the full situation, but hopefully this forum chatter will be of some help :-)
Regards,
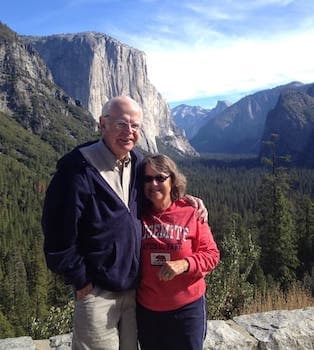
Ted Mooney, P.E. RET
Striving to live Aloha
finishing.com - Pine Beach, New Jersey
A. Some more info would help to answer this.
What is the flux Fe %?
Do you have capacity to heat flux to higher temp?
What is flux full analysis?
Do you rinse before flux? once or twice? Clean water or dirty?
Do you have a drier between flux and zinc?
When you state zinc consumption, what terms are you using? Is that ash weight as a percentage of zinc consumed? or wt ash as % of steel coated? Or what?
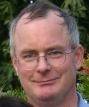
Geoff Crowley
Crithwood Ltd.
Westfield, Scotland, UK
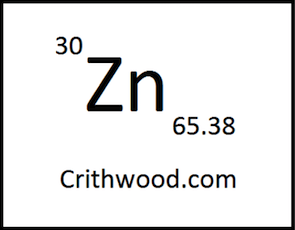
June 13, 2015
Hot dip galvanizing: The ash box
Q. Good morning!
We run a galvanizing plant and are reviewing some processes, in order to reduce zinc consumption. We do not flux neither rinse the material and also we haven't a ash box.
On this post there is some explanation on what it is and how to use a ash box, but there are some things that are not clear.
It is said that the ash will be put on the ash box, and from time to time the ash should be poked downward to remelt. In my understanding, the ash has a different chemical composition than pure zinc, so I suppose what will remelt is the zinc that gets removed together on the skimming, not the ash itself?
Also, considering that the zinc is what remelts and the ash stay on the box, eventually it will be full. When that happens, and we poke the ash little bit more it will float back (through the bottom opening) outside the box? I suppose it should not happen, and when the ash box is full we should clean it. But how is it done? I mean, if we just pull the box up the ash will fall trough the bottom opening on the box (which is larger than the top one). Or I'm wrong, and the ash will be stuck in the box (and that's why the bottom opening is larger, so we can poke and force the ash out)?
Thanks for the help!
- Londrina, Parana, Brazil
July 14, 2015
A. You could probably reduce zinc consumption a lot by rinsing and fluxing.
Without this there must be high zinc consumption, increased bare spots, and other quality issues.
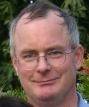
Geoff Crowley
Crithwood Ltd.
Westfield, Scotland, UK
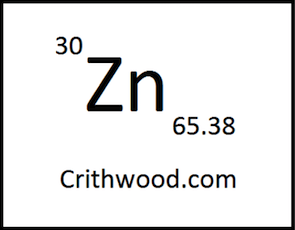
Q. Hello Geoff!
Thanks for your answer!
We are working on setting up the fluxing process, but due to space and layout constraints the rinsing will have to wait a little bit =(
But another major issue that we have is that the ash removed contains a lot of "pure" zinc, which get removed together with the ash while skimming. Then we sift the ash and throw the (now solidified) zinc back on the kettle. This process takes a considerable amount of time and raises a lot of ash in the air, preventing us from continuing the work until it settles. We only do that at the end of day, but still it is a process that I believe could be completely removed with an ash box, because there will be little to no solidified zinc on the ash (because it will drain back in the kettle, right?). Besides, an ash box is just a box, easy to build and setup, and we could start benefiting from it really quickly.
- Londrina, Parana, Brazil
July 24, 2015
A. Do some calculations before you do a lot of work removing metallic zinc from ash.
There's labour cost, heat, flux maybe, and tools.
The ash you end up with doing this work will get a lower price from those that buy such ash.
If you don't remove the metallic zinc they pay more for the ash.
Check the difference. It's just math to see if its worth the cost of the work to get it out and end up with a lower value ash.
You can never get all the metallics this way, perhaps get it to a point where 20% of the weight of the ash is returned to the kettle.
If you use an ash processing machine, then you might get 70% of the initial ash weight back as metallic zinc for putting back in the kettle.
There's no right and wrong in this, you have to work out what works best in your own situation. In different countries labour costs are different, ash sales prices different, gas (heat) costs are different.
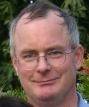
Geoff Crowley
Crithwood Ltd.
Westfield, Scotland, UK
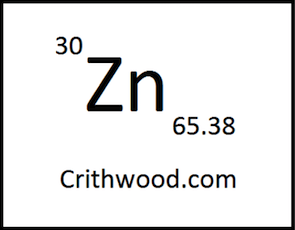
Q. Dear Sir,
I want an assistance on the followings;
1.What amount is the zinc content of zinc ash after galvanization?Are there any difference between zinc ash and zinc dross?Please let me know if there are any elements apart from zinc in the ash withe their respective percentage amount.
2.If there are any figures about the percentage of lead, and similar elements in their respective ashes after certain processing like galvanization
Ethiopian metals industry development institute - Addis Ababa, Ethiopia
May 3, 2016
A. The question is too vague.
The metallic content of ash is highly variable from 80% to 10%, depending on what is done with it, how the plant is operated and so on.
It would be easier to answer with more information on what you really want to know.
Ash and dross are very different. The only common thing about them is that they contain some zinc.
Dross is iron/zinc alloy crystals, and the chemical analysis varies from one plant to the next.
The content of residual elements in both is also highly variable.
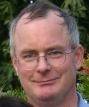
Geoff Crowley
Crithwood Ltd.
Westfield, Scotland, UK
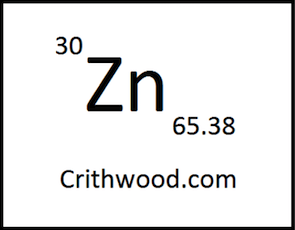
A. Sir:
Skimmings or ash, in my experience 40 years ago were 95% to 99% metallic zinc. More recently with contaminated fluxes the ash does contain various flux contaminations including: aluminum, nickel, calcium, copper, magnesium, manganese (from the steel), potassium, and sodium. In the USA many galvanizers are lead free and using special high-grade zinc. In the "old" days with 1% lead in the zinc, heavily "worked" ash can be as high as 5% in lead. Aluminum in the ash is usually 100 times more than in the molten zinc and may be present as chloride or oxide. Uses for ash include micronutrient fertilizer and micronutrients for farm animals, depending on impurities.
Galvanizers' dross is usually between 2% and 4% iron. Small amounts of chromium and nickel are sometimes present. Uses for dross are brass and other alloys.
Regards,
Galvanizing Consultant - Hot Springs, South Dakota USA
Q. Sir I'm plant in-charge in panipat india. My group works in steel Structure line and galvanisation. Our monthly production in GI is 550 mt and approx. 30 mt zinc consumed per month.
Dross generated is 2.5 mt to 3 mt, white ash 3 Mt and black ash 2.5 mt. So, sir, please guide me whether its quantity is satisfactory or not satisfactory?
Jitendra GuptaEmploy - Panipat India
April 1, 2017
A. Your Dross formation is almost OK, it is approx. 10%. It can be further reduced.
Ash again 3 MT + 2.5 MT. It is tremendously high. It needs immediate attention. It can be brought down to total 7%.
- Delhi, India
Q. Sir,
I have a galvanizing plant and our problem is we are not able to get good finishing. In galvanizing of cable trays, in perforated cable trays zinc is getting stuck in the gap; and zinc usage is more than what it should be.
Can you please suggest what should I do to make the finishing better and avoid zinc wastage?
Thank you sir.
galvanizers - Vadodara Gujarat India
July 10, 2017
A. Hi Maya. It sounds to me like you are saying that the galvanizing is bridging a gap that you feel it is not supposed to be bridging. Photos would probably help.
Regards,
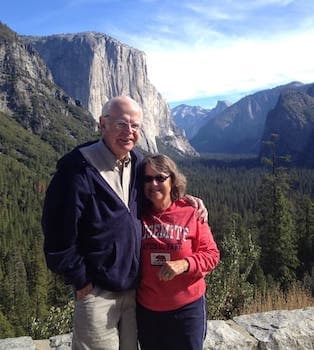
Ted Mooney, P.E. RET
Striving to live Aloha
finishing.com - Pine Beach, New Jersey
A. Sir:
I expect that your flux is poorly formulated. Likely your ACN is too low.
Regards,
Galvanizing Consultant - Hot Springs, South Dakota
Q. Dear sir
I have some problem regarding this topic. our factory normal monthly production is 1000 MT and we try to regularly dross removing twice per month. Its average dross weight was 2500 Kg. But some value has increase to over 5000 kg. My problem is to have any relation to production and dross weight?
Thanking you
- Colombo, Sri lanka
July 12, 2019
A. 1,000 MT/month is 1,000,000 kg/month. Dross is normally 0.5% of production. Thus 1,000,000 Kg times 0.005 equals 5,000 kg dross/month. I think you wrote that you dross every two weeks at 2,500 kg per drossing and it recently doubled to 5,000 kg/drossing. My experience is that a sudden increase in dross usually comes from misaligned burners on the outside of the kettle or very excessive dross in the kettle due to using a clam rather than a scoop. Untreated the kettle is likely to burn through.
Regards,
Galvanizing Consultant - Hot Springs,South Dakota USA
I agree with Dr Cook. Any sudden increase in dross needs investigating. There's a chance that it has come from the kettle, and that's serious.
But it could also come from other sources, and while costly and inconvenient, they are less of an emergency. Sources could include higher Fe in solution entering the kettle, material loss (steel) into the kettle (broken wire?) etc.
If you're removing 5 tonnes dross, then you should increase the drossing frequency to weekly. As said above, use a scoop or spoon and not a clamshell. In my opinion clamshells are not good, they remove some but don't do what's really important - to ensure there's no piles of dross left up against a sidewall or endwall. Such piles of dross create local hotspots which accelerates kettle wear at that point. It does this by preventing convection currents in the liquid zinc from dispersing the heat input.
Be sure that you are removing dross and not excessive zinc. Once out of the kettle the dross should be vibrated, or cut with a shovel in order to squeeze out the zinc from the sandy crystalline dross. Keep the zinc in the kettle, get the dross out.
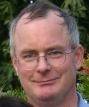
Geoff Crowley
Crithwood Ltd.
Westfield, Scotland, UK
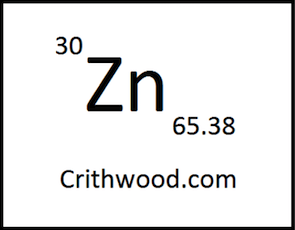
A. Geoff, I still do not have proof that iron in the flux causes dross. Iron +3 chloride is quite volatile-- melting at 282 °C and boiling at 315 °C and if hydrated with 6 waters it melts at 37 °C and boils at 282 °C. Thus the bag house for kettle smoke contains about 1% iron. I have a "wet" kettle client that had 9.5% iron +2 in his flux and he dumped it and put in new flux. His dross did not go down, however the use of new top flux decreased by 20%. There was a time that you said you had proof that iron in the flux causes dross and you said you would send to me. Where is it?
I just do not like all these galvanizers being fixated on iron in the flux. There are 6 or so parameters that are far more important in the flux.
In the old days I purified many, many fluxes for iron. The galvanizers said "O'boy the dross will go down." It never did. %GZU did go down and is far more important than dross.
Regards, Tom Cook
Galvanizing Consultant - Hot Springs, South Dakota USA
Tom,
I agree also that fixation of Fe in flux isn't good. There are many inter-related factors in running a galv plant. Fixation on flux (any parameter) isn't good either.
But although this thread has drifted a little from the problem of increased dross production (and I think we've together covered the potential sources), I believe there is a strong relationship between %Fe in flux and what you call GZU - total zinc consumption. We call it "zinc pickup" but actually that is an erroneous name, as it implies zinc on the job. We count total zinc consumption, expressed as percentage of tonnes steel galvanized.
Over the 10 year period of analysis the linear regression of that number, zinc pickup (GZU) and %Fe in the flux is ... GZU = 0.82x (%Fe in flux) + 5.19. with R2 being 0.88.
That R2 suggests a strong relationship, but not perfect. There are many reasons for variation, including my observation that GZU monthly is too short a period to get a meaningful measurement, and that nothing happens instantly in flux and kettle management, it takes time to see results.
As you have said though, there are many other factors and these include ratio (ammonium chloride to zinc chloride), strength (which we measure in % and you in density - Baumé), other contaminants such as Na, K, etc., temperature, drying of the steel, and that's before we get to the variations caused by differing metallurgical practices in the kettle (Ni, Al, Bi, Pb, Fe, Sn. etc.)
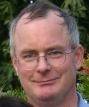
Geoff Crowley
Crithwood Ltd.
Westfield, Scotland, UK
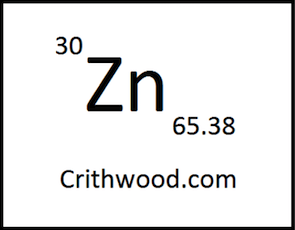
A. Amila: You need to make a "map" of the kettle with the vertical depth of the dross at various locations. To do this you need a 5/8 inch solid steel rod about 3 feet longer than the depth of the kettle. Grind the bottom end about as sharp as a pencil and about 4 inches from the bottom end make a right angle bend. Make another right angle bend in the rod at the top. These two horizontal rods should be in the same direction. Wrap a double wire around the rod at just the right distance from the bottom so that when the rod is pushed vertically down into the zinc the wire will be at the zinc air interface. To map the kettle push the rod slowly into the zinc (careful of zinc splashes) and rotate it on a vertical axis to "drill" through the dross, until you hit the kettle bottom. See that the double wire is at the zinc surface. Next select each end and the middle of the kettle and push the rod probe gently down and stop when you get to the dross. Record how many vertical inches of dross are at various locations in the kettle. Record the dross depths and report back to this website.
Now take the probe with the pencil point from the kettle bottom upward running the point directly on the kettle wall(S). If the point gets stuck and you cannot raise the probe unless you push the probe toward the kettle center, then the eroded cavity in the kettle wall is more than 3/4 inches deep.
Regards,
Galvanizing Consultant - Hot Springs, South Dakota USA
A. Geoff, Thank you for your formula. Thus if the Fe+2 in the flux is 1%, then the %GZU will rise to 6.01% with a probability of 88%? Did you try to curve fit with any other formulas?
Your formula is quite reasonable and is likely valid for your operation. It is nice to have someone to correspond with that thinks a lot like me.
Regards, Tom Cook
Galvanizing Consultant - Hot Springs, South Dakota
Q. Dear sir, I would like to inform you that we have Chinese galvanizing plant setup, and dross produced 3-4 % and ash 5-8%. Sir, tell me how much the correct percentage of dross and ash in international standard.
MOHD TariqSalasar techno engineering ltd - Ghaziabad , India
September 2, 2019
? Are your percentages of ash and dross relative to zinc consumed or production?
Dr. Thomas H. CookGalvanizing Consultant - Hot Springs,South Dakota
Q. I am Wilfredo Lucas, a leading galvanizer in the Philippines.
I am now setting up my accounting system and would like to put a standard value for an ideal generation of zinc dross and zinc ash per production ton.
I need an ideal or acceptable value per industry practice to be the benchmark in setting up my budget.
What is the ideal value I should put as a benchmark for dross generation and ash generation per production ton.
Thanks,
Hot Dip galvanizing - Valenzuela City, Philippines
September 12, 2019
A. Hi Boyet. As a leading galvanizer, have you submitted your own figures to some site where they can be reviewed and incorporated into those tabulations of "industry practice"?
If not, we invite you to submit your figures here and we can try to assemble additional data to go along with them to arrive at standard practice. Unfortunately, to request other readers to offer you their data without you offering any of your own in return has unfortunately proven to usually be a waste of ink. But we do have a dozen or so threads here from which you may be able to glean at least a little info. Please try to summarize it and get back to us. Thanks, and good luck!
Regards,
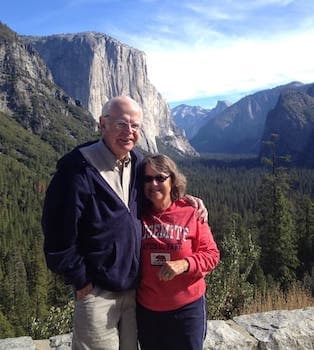
Ted Mooney, P.E. RET
Striving to live Aloha
finishing.com - Pine Beach, New Jersey
A. Sir:
Average Dross/Production times 100% is about 0.5%
Average Ash/Production with MZR recovery is about 0.1%
Galvanizing Consultant - Hot Springs, South Dakota
Zinc recycle costing
Q. Currently, I am using a ash recycling machine and generate about a block of average 450 kgs of recycled zinc.
I am re-using the recycled zinc but I am confused on how am I going to treat this zinc that I dropped on my zinc costing. What value should I put onto it, I don't think it's correct if I price it with the average cost of pure/virgin zinc.
galvanizer - Valenzuela City Philippines
September 12, 2019
More dross when galvanizing high tensile material?
⇦ Tip: Readers want to learn from your situation;
so some readers skip abstract questions.
Q. Dear sir I want to know whether high tensile materials produce more dross with comparison to normal steel, meaning having silicon .45%. Yes or No.
MOHD Tariq [returning]Salasar techno engineering ltd - Ghaziabad, india
September 17, 2019
Q. "Average Ash/Production with MZR recovery is about 0.1%"
Dear Mr. Cook - Sorry for my question - may you kindly explain this further if for example I produce 1,000 MT galva ton?
WIlfredo LucasHDG - Val, Philippines
September 24, 2019
A. Boyet Lucas: Many galvanizers record the zinc ingot produced only to keep an eye on the recovery process, then add the zinc back into the kettle, and do not show it as a zinc addition. There's then no need to attribute a value to it, except remember that it's a tonne of virgin zinc you didn't need to buy. Your zinc consumption is at a new (lower) level, but that zinc you recovered wasn't consumed. Nor is the splashed zinc around the kettle top. You don't do anything with that either do you? Just push it back in, it wasn't consumed.
A. Mohd Tarik: In my experience that steel doesn't produce more dross. It will have a different coating weight, and so consume a different amount of zinc, but not produce dross.
A. Wilfredo Lucas: Let's let Dr Cook answer too, but in my experience, you can have two different ash production levels. With o zinc recovery machine, you produce a lot of ash which contains zinc metallic particles, and if you just measure this ash, then you might expect an ash figure of about 1-2% of the tonnes galvanized. So galvanize 100t and produce 1-2 t ash. With ash recovery, you can expect to extract about 75% of the weight as zinc ingot to go back in the kettle. That means a new ash figure of about 0.5 to 1% of tonnes galvanized. Or, galvanize 100t steel, and make 0.5 to 1t ash.
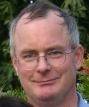
Geoff Crowley
Crithwood Ltd.
Westfield, Scotland, UK
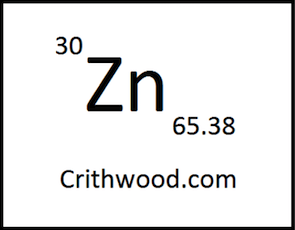
September 25, 2019
A. Lucas, 0.1% is 0.001 (in fractional units). Thus multiply 1000 Mt by 0.001 which equals 1 metric ton of ash coming out of the MZR machine. To get this great result you must be correctly using clean quadraflux as shown in my article in the on-line library on this website.
adv.
Also the galvanizers getting such a good result are using my Nifty.
The skimmings are unworked.
Regards,
Galvanizing Consultant - Hot Springs, South Dakota
Q. We are doing Hot dip galvanizing for bolts in Molten Zinc bath. Every month dross from bath is minimum 4000 kg, monthly production averages 150 Mt.
How to utilize or segregate the Zinc from dross?
- Chennai Tamil Nadu, India
March 18, 2021
A. Hi Shankar. As you see, we appended your question to a long and interesting discussion about reducing dross and recovering the zinc from it. You may want to read the many comments and construct some specific questions about the suggestions. Good luck.
Luck & Regards,
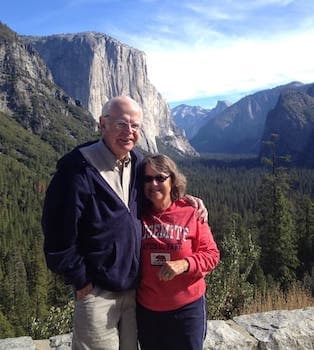
Ted Mooney, P.E. RET
Striving to live Aloha
finishing.com - Pine Beach, New Jersey
Q, A, or Comment on THIS thread -or- Start a NEW Thread