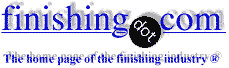
-----
Palladium-Cobalt Characteristics and Plating Problems
Q. Palladium Cobalt (PCP) is used in our plating shop to substitute for Palladium Nickel(PNP) for nickel-free products. Anyone could advise me some characteristics of PCP plating solution such as :
(1) What is the effect of temperature, pH, Be on the composition of Pd & Co;
(2) As stated in manual of the supplier, PCP layer normally contains 80-90% of Pd; In practice, close to/more than 90% Pd is plated in the layer (checked by x-ray); any good suggestion to keep the Pd content lower?
Sun Lick, - Hong Kong, China
2000
Keep Karat of Palladium Cobalt Plating Stable?
2000by Abner Brenner
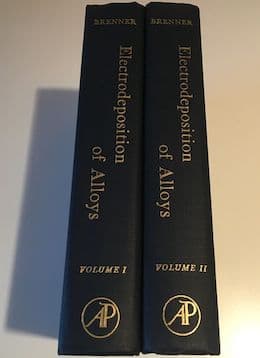
on eBay or Amazon
or AbeBooks
(affil link)
Q. Palladium Cobalt (PdCo) is used instead of Palladium Nickel for Nickel-Free product. Due to the costing, it is preferred to use as low Pd content as possible (e.g., 80% Pd/20%Co.)
When a new PdCo bath is used, a 80%Pd/20%Co karat layer could be kept in normal plating operation. However, when the bath is used for several months, the karat of Pd/Co gets higher and higher and the replenishment of Pd gets higher to keep the bath content. As some supplier explained to me, even the cobalt content checked by AA is kept at certain level, the Co(II ion), which can easily deposit with Pd, in the bath changes to Co(III ion), which could not deposit with Pd, after the bath is used for a while.
Is it true?
If yes, is it possible to convert the Co(III ion) to Co(II ion) in the bath? Or how to keep the karat of Pd/Co plating as low as possible?
Deville Yiu [returning]Sun Lick, Hong Kong, China - Hong Kong, China
A. Hey Deville Yiu, When the bath is new the ratio of Pd/Co in the bath gives you the correct ratio of metals in the deposit. As the bath ages maintaining the same in-bath ratio fails to maintain the right deposit ratio. The way to look at the problem is: you have always needed to replenish the amount/ratio of metal deposited and you don't need to worry about the ratio of Pd/Co in the bath as this will change as the bath ages. Let the metal deposited control the ratio in the bath chemistry. And I don't think using a reducing agent is a good idea.
Regards,
Fred Mueller, CEF- Royersford, Pennsylvania
2000
A. If using a properly complexed cobalt a shift in Co oxidation state and alloy composition shouldn't be an issue.
Bruce Stacy- Greenville South Carolina USA
February 27, 2011
Palladium cobalt alloy magnetic properties
Q. I am looking for specific data on the magnetic properties of palladium cobalt alloys. The best that I have been able to find is that they may be slightly magnetic. I need some specific hard data. I have a low level magnetic requirement. Can you help?
Thank you.
Frank MajeskeBoeing EDD - Torrance, California
2001
Palladium-Cobalt Adhesion Problem
2007by William Safranek
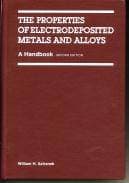
on eBay or Amazon
or AbeBooks
(affil link)
Q. Dear Sir/Madam,
I am having an adhesion problem with my electrolytic Palladium/Cobalt Alloy deposits on Electrolytic Nickel plated on Copper. First I plate Electrolytic Nickel on Copper, then plate Electrolytic Palladium/Cobalt on the Nickel. The Alloy composition should be 80% Palladium and 20% Cobalt.
The substrates are cleaned in 20% Sulfuric Acid before electrodeposition. I do not think my adhesion problem is caused by poor surface preparation. I think the problem is due to stress in the deposits either because of incorrect alloy composition or a deficiency in the stress reducing agent. The Cobalt concentration is controlled by a chelating agent, the concentration of which is unknown.
The thickness of the deposits is 2.0 microns run at a current density of 16.0 Amps/square foot.
What are your suggestions to improve the adhesion problem.
Thanks,
Plating Engineer - Danbury, Connecticut, USA
A. I don't think I agree with you about the cause of the adhesion problem not being surface preparation, Maurice. But what doesn't adhere to what? Does the nickel come off the copper or does the palladium-cobalt come off of the nickel?
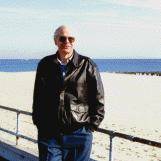
Ted Mooney, P.E.
Striving to live Aloha
(Ted can offer longterm or instant help)
finishing.com - Pine Beach, New Jersey
2007
Q. HI TED,
THANKS FOR REPLYING. THE PALLADIUM/COBALT COMES OFF THE NICKEL. THE NICKEL REMAINS ON THE COPPER.
MAURICE
- DANBURY, Connecticut, USA
2007
A. Nickel plating passivates very quickly, Maurice. Do the parts go to the palladium-cobalt immediately after nickel plating? If so, you may need to reduce rinse time. If not, you may need to activate the nickel plating with a Wood's Nickel strike.
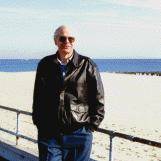
Ted Mooney, P.E.
Striving to live Aloha
(Ted can offer longterm or instant help)
finishing.com - Pine Beach, New Jersey
2007
Q. Hi Ted,
Thanks again. I rinse the parts for approximately two minutes after Nickel Plating before they go in the Palladium/Cobalt bath. This is mainly to prevent contamination of the Palladium/Cobalt bath with any "drag out" from the Nickel bath. I try not to expose the parts to air. Am I rinsing too long?
- Danbury, Connecticut, USA
2007
A. Well I can't say that 2 minutes is sure to passivate the parts, but it is on the very long side. And the problem you are having is the nickel surface, so it seems it would likely be either excessive brighteners or passivation.
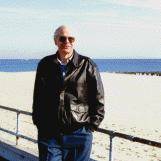
Ted Mooney, P.E.
Striving to live Aloha
(Ted can offer longterm or instant help)
finishing.com - Pine Beach, New Jersey
2007
! Hi Ted,
A chemical analysis of the Palladium/Cobalt Plating solution showed that a component used as a stress reducer was way below the recommended level. I added this component to the plating solution, allowed it to mix for about two hours, and the adhesion problem went away. Repeated tests since have still showed no adhesion problems.
- Danbury, Connecticut, USA
2007
2007
Glad to hear it's solved, Maurice! Sorry, I didn't really pay close enough attention to your wording :-(
Although a deposit which cracks off because it is excessively stressed is not exactly the same thing as a deposit which pulls off because it lacks adhesion, there is no point in my being pedantic, especially since you've solved the problem, and I could have understood your situation better by reading more carefully :-)
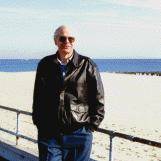
Ted Mooney, P.E.
Striving to live Aloha
(Ted can offer longterm or instant help)
finishing.com - Pine Beach, New Jersey
Q. Hello. I am having similar problems but, in my case it is palladium nickel. I am plating 30 micro inches to a formed part and we are seeing some lifting on the edge of the part. Tried Wood's Nickel with low current but, the problem continues. How high should the current be in the Woods Nickel?
marco salazarplating - waterbury Connecticut
October 8, 2018
October 2018
by Jack Dini
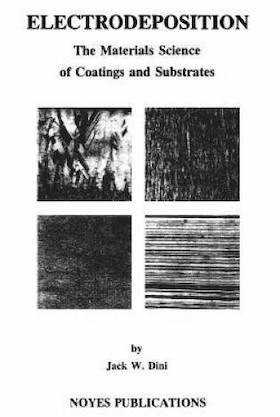
on eBay or Amazon
or AbeBooks
(affil link)
A. Hi Marco. According to Dini's "Electrodeposition", it looks like 100 ASF is ideal but 27 ASF is enough for most purposes.
But Maurice found that lack of stress reducer in the plating bath was the actual problem for him. Are you confident that it's not your problem?
Regards,
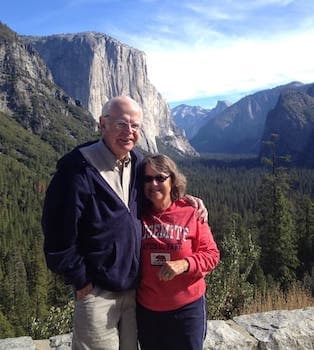
Ted Mooney, P.E. RET
Striving to live Aloha
(Ted can offer longterm or instant help)
finishing.com - Pine Beach, New Jersey
Q Could anyone text me a supplier of PdCo plating solution?
Andy LiuSuzhou MT - Suzhou, China
January 3, 2020
Ed. note: This RFQ is outdated, but technical replies are welcome, and readers are encouraged to post their own RFQs. But no public commercial suggestions please ( huh? why?).
Q, A, or Comment on THIS thread -or- Start a NEW Thread