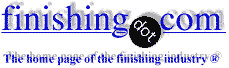
-----
Can't get part to anodize!

Q. Chris, I am having what seems to be the same issue you are having. The parts bubble, the cathode bubbles, but no anodizing. What did you end up doing to fix your issue?
Ike Urbanik- Mission Viejo, California
September 25, 2022
A. Hi Ike. Chris' posting was from 22 years ago and his e-mail is bouncing. Again is there more bubbling on the part or on the anode? Our first guess is always that you have the polarity reversed, especially if you think bubbling on the parts is a good thing :-)
Luck & Regards,
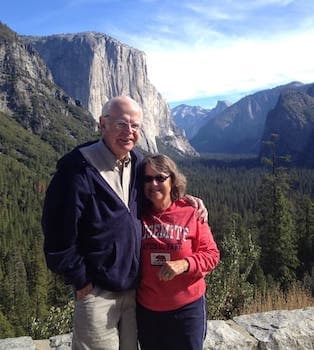
Ted Mooney, P.E. RET
Striving to live Aloha
(Ted is available for instant or longterm help)
finishing.com - Pine Beach, New Jersey
Q. I am using BK Precision 0-48 vdc, 5 amp benchtop adjustable power supply.
Also using acetic acid
⇦ on
eBay
or
Amazon [affil link] and salt for the test sample. Will move to sulfuric acid once proof of concept is successful. But may move to sulfuric now as vinegar
⇦in bulk on
eBay
or
Amazon [affil link] isn't working.
I've also tried four different sources of aluminum.
Small parts as testing:
1" x 4" x 1/8" strips
1" x 1" round bar
.5" x 1" x 3" bar stock
Oxidation just is not occurring.
Either the acid isn't right or power supply isn't set to the right voltage or current. Not sure what else it could be.
- Mission Viejo, California
September 27, 2022
A. Hi Ike.
If I were you I would switch to sulfuric acid right away. I have never heard of any kind of anodizing with vinegar, and although that certainly doesn't mean it can't work, trying such variations would be something for an accomplished anodizer to try to develop. When starting out, probably with no experience and no instrumentation, you're pretty much limited to following the cookbook :-)
Luck & Regards,
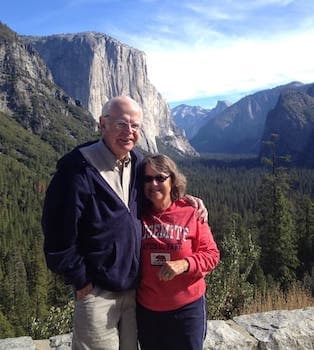
Ted Mooney, P.E. RET
Striving to live Aloha
(Ted is available for instant or longterm help)
finishing.com - Pine Beach, New Jersey
⇩ Related postings, oldest first ⇩
Q. Can someone please help. I've got the book Artists Anodizing Aluminum: the Sulfuric Acid Process [on Amazon affil links] and followed the steps to exactly to anodize. EVERY time I try, the aluminum doesn't anodize. After the anodizing bath the part still conducts electricity, and the dye won't stick at all. What am I doing Wrong? Also sometimes the part comes out of the anodizing bath black like its covered in smut, what's up with that?
Thanx,
Chris
Chris FrancisHampton Virginia
2000
? Are you sure you have the polarity right?
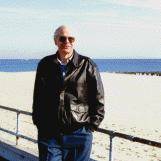
Ted Mooney, P.E.
Striving to live Aloha
(Ted is available for instant or longterm help)
finishing.com - Pine Beach, New Jersey
Q. Thanks but I'm quite sure the polarity is correct. If I switch it Nothing at all happens -- no bubbles. It seems like everything is going okay but the metal just doesn't anodize. Isn't the bubbling a sign that it's working? And any ideas about the smutty stuff.
Chris Francis [returning]Hampton Virginia
2000
A. I don't have that book so I don't know whether you are following the instructions correctly, nor whether they are right or wrong. But the work must be the anode, and reading between the lines I still feel it's probable you have the polarity reversed.
The most obvious bubbles are hydrogen at the cathode. If there are also bubbles at the other pole, they are oxygen bubbles at the anode. Water is H20 so you will always have at least twice as much hydrogen as oxygen.
If the bubbling on your workpiece exceeds the bubbling on the other pole, and if the bubbling is fairly well distributed, it's probably hydrogen and the polarity is reversed. If there is more gassing at the other pole than on your work the polarity is correct, but....
Organic contamination will lead to release of oxygen at the anode; it's possible the parts aren't really clean.
I don't know if you are applying enough voltage, nor whether your acid is strong enough to attack the aluminum and create the porosity necessary for dye absorption. What kind of amperage and voltage readings are you getting and what is the surface area of your part?
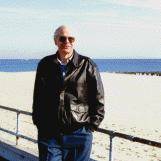
Ted Mooney, P.E.
Striving to live Aloha
(Ted is available for instant or longterm help)
finishing.com - Pine Beach, New Jersey
Q. Hi, Thanks for the previous help but one last question. I've got the book Artists Anodizing Aluminum: the Sulfuric Acid Process [on Amazon affil links] and all my parts anodize great now. My question is how do I achieve a Gloss or semi-gloss finish after sealing. The parts look great as far as color goes but always have a matte finish. Do I need to clear lacquer everything? Thanx Chris
Chris Francis [returning]- Hampton Virginia
2000
A. Hello again, Chris. Please tell the curious readers what changed that took you from no anodizing to satisfactory anodizing.
You do not need to lacquer your parts, but they will be no shinier, and actually a little less shiny, after anodizing them than before. If you want a bright finish you must polish/buff the parts before you anodize them. Good luck.
Regards,
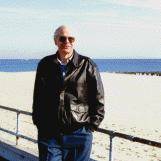
Ted Mooney, P.E.
Striving to live Aloha
(Ted is available for instant or longterm help)
finishing.com - Pine Beach, New Jersey
Q. I'm having an issue with Anodizing also. I have a Mastech HY3030EX 0-30v 0-30A power supply. I'm using a large aluminum heat sink at my negative electrode so the surface area is as big as my work piece. My acid is battery filler (1 part) mixed with water (3 parts). I didn't have DI water handy so I used filtered water for now. When I set up my power supply for "Constant Current" (1.5A for the 37.44 square inch part) the Voltage starts at 4.8v then over an hour drops to 1.0v and I get black spots and pits on the aluminum and a minimal oxide layer (so very little dye takes). If I set the supply to constant voltage (15V) the amperage takes off. I have actual anodizing dye and Nickel Acetate for sealing... I'm almost certain it's the power supply that's kicking my butt, but not sure how to remedy it.
Richard Dubey- Torrington, Connecticut USA
September 17, 2012
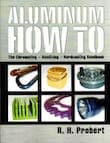
Aluminum How-To
"Chromating - Anodizing - Hardcoating"
by Robert Probert
Also available in Spanish
You'll love this book. Finishing.com has sold almost a thousand copies without a single return request :-)
A. Hi Richard.
- Don't start at 15 volts; you'll burn the parts before you've even started.
- Your 1.5 A is low by a factor of about 2. Figure 12 amps per square foot.
- Most heat sinks are anodized and thus not conductive.
Regards,
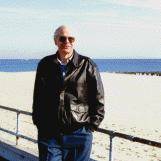
Ted Mooney, P.E.
Striving to live Aloha
(Ted is available for instant or longterm help)
finishing.com - Pine Beach, New Jersey
Q. The heat sink might have been clear anodized, I let it sit in Sodium Hydroxide till it was bubbling well. I don't actually "start" at 15v. I set the supply to 1.5A (although I hear varying amounts for ASF, a lot of 720 calculators say 6 ASF). But the supply is set to be locked at 1.5A (maybe should be 3A) and when I hook up the part, the voltage (which is floating) starts at 4.8v then by the time an hour is up goes down to 1.0v.
Should I put a power resistor into the circuit to increase the resistance in work circuit to get the circuit Voltage up to 12-15v? I figure (at 1.5A or 6 ASF) my resistance is around 3.5 ohms (if I'm reading 4.8v at start). So to get the system voltage up to 15v I'd have to add 6.5 ohms more.
does this make sense?
- Torrington, Connecticut USA
September 18, 2012
A. Hi. External resistors should not be necessary, and seem to add a complication. It may simply be that your power supply is defective, as there should be no reason for the voltage to decrease over time; it should be rising, not dropping.
When you start, the resistance is very low. That's why the voltage must be limited (which you are indirectly doing by limiting the current). As the anodized film builds, the resistance increases, and the voltage should be automatically increasing to try to maintain constant current.
Regards,
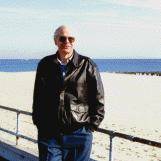
Ted Mooney, P.E.
Striving to live Aloha
(Ted is available for instant or longterm help)
finishing.com - Pine Beach, New Jersey
Aluminum 3003 is not anodizing
Q. I attempted my first anodizing today. My work piece was a polished aluminum 3003 ring. The wire used to suspend the piece into the acid bath was a thin strip of aluminum 6061 (all I had available at the time). After dying, the wire holding the piece dyed nicely. The work I wanted to dye, only came out with what looked like a light white coating. I'm sure I had good contact between the two. Was this the result of using different alloys? The cathode was 6061.
Michael KraussHobbyist, jeweler - warminster, Pennsylvania, USA
September 12, 2015
A. Hi Michael. It's obviously difficult to say what someone has done wrong on their first attempt in a multiple-step process, based simply on it not having worked. But I'd say that the wire material might be the first issue to address; see if you can get some 2024.
Regards,
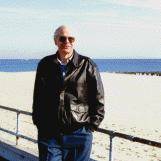
Ted Mooney, P.E.
Striving to live Aloha
(Ted is available for instant or longterm help)
finishing.com - Pine Beach, New Jersey
Hi Michael,
Ted may be right, but 6061 sounds a reasonable racking material to me.
Check that your connection from rack to work is good and firm. If there is a momentary loss of contact, the point of contact on the rack will become anodised and will not continue to conduct current when mechanical contact is remade.
Harry
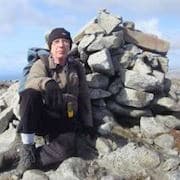
Harry Parkes
- Birmingham, UK

How to do anodizing on Water Bucket made by Aluminium 5052
Q.
Can anyone on this forum help me professionally? Because I really don't know how to achieve and make a setup of it.
Regards,
Zunnurain Mirzarestorer - Karachi, Pakistan
September 3, 2018
Treatment &
Finishing of
Aluminium and
Its Alloys"
by Wernick, Pinner
& Sheasby
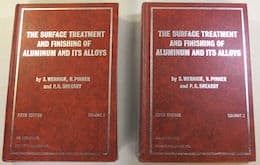
on eBay or Amazon
or AbeBooks
(affil link)
A. Hi cousin Zunnurain. Our "Introduction to Anodizing of Aluminum" should give you a good starting point if you lack experience in this. After reviewing it you may wish to ask some detailed questions. Still, you probably should start your practice on scrap stock rather than on an item that is important to you.
Please understand that if someone says they want to build an airliner or perform an appendectomy, the first thing we would need to say is "what is your starting point ... what do you already know?". Although anodizing a bucket is easier and less risky than those things, there is still a fair amount to it, and it still requires a starting point: the book "The Surface Treatment and Finishing of Aluminum and Its Alloys", for example, will answer all your questions but it's 1,273 pages :-)
Best of luck.
Regards,
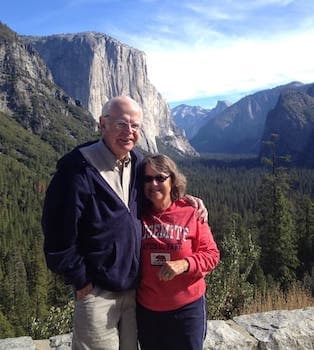
Ted Mooney, P.E. RET
Striving to live Aloha
(Ted is available for instant or longterm help)
finishing.com - Pine Beach, New Jersey
Q, A, or Comment on THIS thread -or- Start a NEW Thread