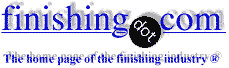
-----
Passivating Stainless Steel with citric acid
1 2
January 7, 2016
Q. I am inspecting parts and noticed that our supplier did not passivate the parts (Stainless Steel - 17-4) according to the callout in our drawing "PASSIVATE IN ACCORDANCE WITH ASTM A967, citric acid ONLY".
The supplier performed Acid Pickling (3X type) by means of i)Hydrochloric Acid (1-2 mins), ii)Camm SUS CP118 (2-3 mins), and then iii)Nitric Acid (1-2 mins).
Our customer wanted these parts to be passivated specifically using citric acid . Before I reject these parts, I have the following questions:
1) Is it good for a single part to be passivated using more than one method (e.g., passivate using an acid pickling method with the use of Hydrochloric Acid and Nitric Acid, then wanting to go back and passivate using citric acid )?
I would think this wouldn't be desirable due to the thin oxide layer that is formed after the part is initially passivated.
2) Would "re-passivation" remove the thin oxide layer or would it add another thin layer on top - resulting in a finished part that has slightly larger overall dimensions?
Thanks for your input!
- Denver, Colorado, USA
January 8, 2016
A. Jeff,
Hydrochloric acid is bad, bad, bad for stainless steel. It's not something to use for pickling even if you wanted pickling. Thank goodness it was only 2 minutes.
I have no idea what Camm SUS CP118 is.
In the major industry passivation standards, every listed nitric acid passivation treatment requires a minimum of 20 or 30 minutes.
Not only did they not passivate your parts they way you asked, they used nothing resembling any known accepted pickling or passivation treatment and probably did the parts more harm than good. Find a different supplier, and as a parting shot you can ask them if they were TRYING to ruin your parts.
As to your questions:
All the acid bath is doing in passivation is removing iron. (Well, nitric passivation picks away at the other metals too, but more slowly.) Extra time in the passivation bath/additional treatments generally will just have no effect, since all the iron at the surface is gone already. In your case I would definitely passivate again (if the parts still look okay), since there is probably a lot of iron there after the abuse your parts went through. Since you already are locked into using citric acid , you could even do it yourself if you wanted to. Run them an extra long time just to make sure.
Note that "oxide layer" does not mean passivation is a coating. Iron is removed, forming a thin iron-depleted surface layer in the metal itself (mostly chromium at that point), and the oxide layer is formed from that via addition of oxygen atoms from the O2 gas in air. The chromium oxide that's there (there's always at least a little of it, even on an unpassivated part) is unaffected by the acid bath (totally unaffected by citric, mostly unaffected by nitric). The acid just picks away the iron from around the chromium oxide.
Let me know if I can help you further with this.
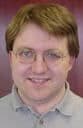
Ray Kremer
Stellar Solutions, Inc.

McHenry, Illinois
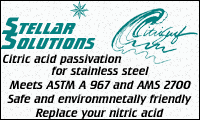
A. Hi Jeff,
I am with Ray on this one, the process used could potentially damage your parts such that they may fail in service.
17-4PH steels typically have Ultimate Tensile Strengths (UTS) above 140ksi, meaning that if they have been anywhere near hydrochloric acid they need de-embrittlement, a minimum of 6 hours at 375 °F within 4 hours of treatment (if lower end of the strength range), 24 hours at 375 °F within an hour of treatment (if upper end of strength range).
If you are using the 17-4PH steel in the H1150 state (UTS 135ksi) you may just about get away with it, otherwise I would be really concerned about these parts.
Aerospace - Yeovil, Somerset, UK
January 11, 2016
Q. I am using citric acid for passivating SS surgical instruments. As for the usual process, the chemical bath will have contamination of detergent (Potassium hydroxide solution) and some oil stains which is caused the chemical bath becoming opaque color.
My intention/plan is to purify the chemical bath instead of changing to new acid so that the acid returns back to clear condition. What method would be possible to clear off the chemical bath?
Thank you.
medical industries - Penang, Malaysia
September 6, 2016
A. Ooi Cherng Wee,
You really shouldn't be dragging potassium hydroxide precleaning solution on your parts into the acid bath. All it does is neutralize the acid and waste good acid. Use a good clean water rinse between your preclean stage and your acid dip stage.
If you are dragging oil into your acid bath, you also need a better precleaning stage than you have currently.
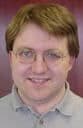
Ray Kremer
Stellar Solutions, Inc.

McHenry, Illinois
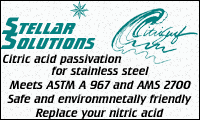
September 13, 2016
Q. How do you determine the proper specific gravity and pH levels based on Citric 3 and Nitric 3 passivation per ASTM A967?
Soogie Machamer- Frazer, Pennsylvania, USA
September 16, 2016
Q. Hi, I'm a newbie here! and I read all the comments and suggestions here. We are passivating our water system which is made up of SS 316L with citric acid followed by nitric acid. Can citric acid be used alone for passivation and omit the use of nitric acid? If ever we are omitting the latter what is the best explanation for that?
Thank you!
- San Pablo City, Philippines
September 29, 2016
September 29, 2016
A. Jemarie,
Yes, passivation uses either nitric acid or citric acid , not both together. Refer to the industry standards (e.g. ASTM A967) on this.
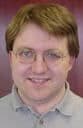
Ray Kremer
Stellar Solutions, Inc.

McHenry, Illinois
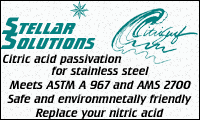
Q. Hi,
We sent our part to supplier to do passivation for B8-CL2 material. But the result showed two types of color as per picture. This is not same lot but different order and different day. Please see attached file. Right side is too dull for us we rejected this part.
How do we know if the part is a reject or not ? Please help.
Nora NorainiF- Johor Bahru, Johor, Malaysia
October 6, 2016
Q. Hi there,
I got some 316 SS parts citric passivated for use in a product for medical/surgical use. The parts seem greasy or waxy.
What do you think this is? Is it that the citric acid solution dried prior to washing it off?
How can I fix it? Warm water bath, or citric passivate again, or nitric passivate, or something else? Is this harmful for use in our product?
Do you have any testing suggestions to avoid this in the future? I preferred citric passivation, rather than nitric, because it is environmentally friendly, but I worry this may be a problem in the future. Please help!
Thank you in advance!
- Baltimore, Maryland, USA
October 12, 2016
A. Jane,
Somehow I missed this question earlier.
My best guess is bad rinsing with rinse water that was not being refreshed enough to stay clean. We have seen that happen before. If the rinse bath is good, check the source and age of the material in the acid bath. Usually there is no shelf life for this sort of thing but odd things have been known to happen from years in storage in a hot warehouse or whatnot.
Depending on what the residue actually is, probably a warm water soak will clean them off, but failing that I would try some solvents (acetone, alcohol, etc.)
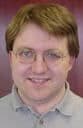
Ray Kremer
Stellar Solutions, Inc.

McHenry, Illinois
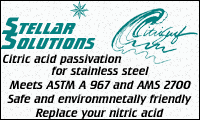
November 10, 2016
Q. Hello,
I read all the interesting conversation about using nitric/citric to passivate stainless steel. I'm currently a student working in a company who wants to change its bath of nitric acid to a citric one; I am in charge of looking to THE solution, in order to have a less-toxic treatment. I also have to find how to use hydrogen peroxide (as an oxidant I suppose, in post-passivation as I read).
I have currently no idea about the concentration of citric I have to use, or what I have to put in the bath.
If you can forgive my english, I would like a little precious help about this project.
Thank you for reading!
- Lyon, Rhône, FRANCE
November 3, 2016
A. Clément,
As has been mentioned many times above, ASTM A967 is a good reference document for the passivation process.
A peroxide post-treatment isn't used very often. Usually letting the surface dry in air is enough to form the chromium oxide layer. Most people aren't in such a hurry that they have to use peroxide to speed up that process.
(adv. If you like, I can put you in touch with the distributor for my products in Germany.)
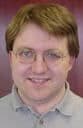
Ray Kremer
Stellar Solutions, Inc.

McHenry, Illinois
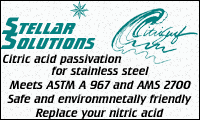
November 7, 2016
citric acid does not passivate (oxidize) stainless steel. It activates (reduces) the surface so that, then, the air can oxidize (passivate) it. The types that contain nitric acid actually oxidize (passivate) the surface for better protection.
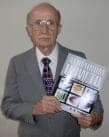
Robert H Probert
Robert H Probert Technical Services

Garner, North Carolina
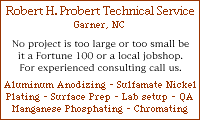
November 7, 2016
Here we go again :-)
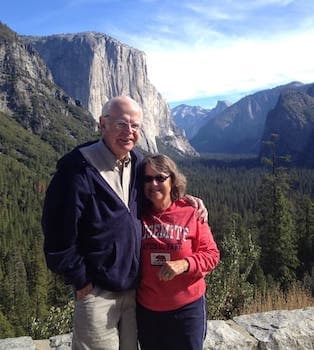
Ted Mooney, P.E. RET
Striving to live Aloha
(Ted can offer longterm or instant help)
finishing.com - Pine Beach, New Jersey
November 2016
A. Robert,
No claim is made as to the formation of chromium oxide within the citric acid passivation bath. It's certainly not reducing the surface, though. The acid (H+ ions) oxidizes (removes electrons from) the iron atoms, which converts them to ions and removes them from the surface. The chromium remains zero-valence (electron count matching the proton count) until oxidized (formation of metal oxide via giving up electrons to an oxygen atom resulting in a covalent bond) by oxygen gas, peroxide, or a similar oxygen source.
It is a long-standing belief by many in the industry that the formation of chromium oxide takes place within the nitric acid bath, but chromium oxide measurements comparing nitric-passivated and citric-passivated parts have called this into doubt. Certainly nitrate is an oxidizing agent in the sense that it can takes electrons away from other things, but that would result in chromium atoms removed from the metal surface and released into solution as ions (which indisputably does happen in nitric acid) rather than the formation of chromium oxide.
Regardless of when or how the chromium oxide layer is formed from nitric acid passivation, test data shows the results with citric acid to be equal or superior.
Ted,
;-P
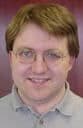
Ray Kremer
Stellar Solutions, Inc.

McHenry, Illinois
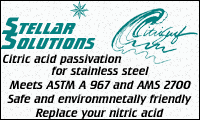
November 10, 2016
November 16, 2016
Good day Ray.
Holy crap!
I thought I knew about passivation and waste treatment.
What an eye opener! Ions, electrons, great explanation!
I do agree with the chelators (my gold drag outs are heavy!) and without using DTC, waste treatment was a headache.
Personally, I would send the citric acid rinse water STRAIGHT to sanitary, as iron limits here in Ontario are very lenient.
I do enjoy your posts!
Regards,
Aerotek Mfg. Ltd. - Whitby, Ontario, Canada
? Hopefully I do not offend, but surely there must be some method for the objective measurement of oxide film thickness.
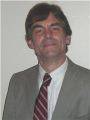
Dave Wichern
Consultant - The Bronx, New York
November 28, 2016
A. Dave,
In fact there are methods for measurement of oxide film thickness. They are just expensive and most people in the general industry wouldn't want to use them.
We do have some of this data, however, that was gathered a number of years ago by customers in the semiconductor industry. They do show the thickness from citric passivation to be slightly higher than that of nitric passivation.
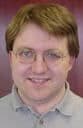
Ray Kremer
Stellar Solutions, Inc.

McHenry, Illinois
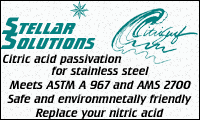
December 2, 2016
December 6, 2016
Ray,
First, thank you for your answer.
I was at university for a month so I hadn't seen your post. I checked A967/A967M, it looks pretty interesting and useful for the rest of my research.
It looks like there are many things to learn about passivation of stainless steels; maybe I will come back to you for some advice! Thank you again for your help.
- Lyon, Rhône, FRANCE
Wastewater treatment for citric acid passivation
Q. I have a customer who I'm trying to sell on setting up a SS passivating line.
Question: does the rinse following the citric acid step pick up enough Ni and/or Cr to require waste treatment? I'm pretty sure that the post HNO3 passivate rinses would.
Is there a good IX method for treating such rinses? NO3- is a lousy complex former; citrate is something of a chelator. The former would likely respond to plain vanilla hydroxide precipitation; the latter, perhaps not.
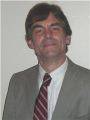
Dave Wichern
Consultant - The Bronx, New York
November 8, 2016
November 10, 2016
Actually, Mr Kremer on his website answered my questions. Apparently, the citric doesn't pick up Ni and/or Cr. I should have looked there before posting.
One thing that citric rinses will have that nitric rinses don't is biochemical oxygen demand (BOD) That might be cause for concern, in some places.
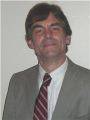
Dave Wichern
Consultant - The Bronx, New York
November 10, 2016
Dave,
With citric acid passivation, zero Ni and Cr is removed from the surface of the steel and these elements will not be found in the acid bath or the rinse water.
Correct, with nitric passivation you will find these elements in your waste stream.
The wastewater from a citric line can't be sent through a metals precipitation system due to the chelating nature of the citric, but then, you don't have to either since iron is the only metal in there and isn't considered hazarous.
(Some users must anyway because they perform other processes producing heavy metal waste and are mandated to treat all waste streams though the precipitation system, in which case the citric acid must be treated and removed from the solution first.)
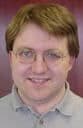
Ray Kremer
Stellar Solutions, Inc.

McHenry, Illinois
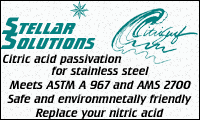
A. Dave,
Citric passivation does not pick up any Cr, Ni, or other heavy metals from the stainless. Only iron, for which no waste treatment is required.
If the company's total waste stream must be treated for heavy metals because they are doing other things in addition to citric passivation, then they do need to pretreat the citric waste stream to remove the citric due to it being a chelating agent.
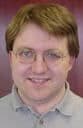
Ray Kremer
Stellar Solutions, Inc.

McHenry, Illinois
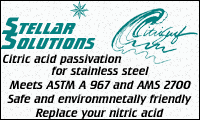
November 23, 2016
Q. Hello again,
My company asked me to find some solutions using hydrogen peroxide. By that, I mean using H2O2 as oxidant (yes, replace acid by peroxide). I've don't know if it is even possible, without heavily heating or under high pressure. If you have any idea, thank you !
Clément
- Lyon, Rhône, FRANCE
December 7, 2016
A. Hi Clément. It is true that peroxide is an oxidizer. I am familiar with its use for etching and bright dipping copper, where it is mixed with sulfuric acid and used as an alternative to nitric acid, persulphates, etc.
I am personally not familiar with attempts to use it for passivation of stainless steel and cannot say whether it would have any usefulness.
But it would be important to find out why it was suggested. If it's because a sister company manufactures it and you wish to support that effort, for example, that could be a justification. But if it's based on some general principles issue of wanting to use less toxic or dangerous materials, you should fully investigate the hazards of hydrogen peroxide before assuming it's safer than proven solutions like citric acid :-)
Luck and Regards,
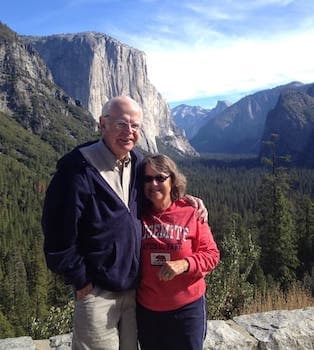
Ted Mooney, P.E. RET
Striving to live Aloha
(Ted can offer longterm or instant help)
finishing.com - Pine Beach, New Jersey
December 2016
![]() |
December 8, 2016 Hi Clement, ![]() Anna Berkovich Russamer Lab ![]() Pittsburgh, Pennsylvania ![]() December 8, 2016 Clement, ![]() Ray Kremer Stellar Solutions, Inc. ![]() McHenry, Illinois ![]() |
Thanks Ted, Anna and Kray.
So it is possible to passivate stainless steels using H2O2, according to Anna. But Ray seems to say it is too long, so does the short duration have a link with H3PO4? Does it help for the #1 part ?
Ted, my company want to reduce its impact on environment, I will look for H2O2 properties.
I also need to work at neutral pH, I guess it will not be the case, using some H3PO4 !
Regards,
- Lyon, Rhône, FRANCE
December 19, 2016
December 22, 2016
Q. Hello,
My name is Clément, and I am a french student.
I am currently working in a company which deals with stainless steel.
At the moment, they are using nitric acid to passivate, and they have some problems with bichromate. All of that is not that good for environment, and that is why I have many objectives :
- Eliminate dichromate (used for martensitic stainless steel).
- Find some issues on the side of the citric acid , maybe in order to replace the nitric.
- And develop a bath of passivation using hydrogen peroxide.
I have read about ASTM A967 on finishing, but I have not a lot of clue about the hydrogen peroxide.
If anyone know anything about that, it could be very useful for me !
Thank you for any help you can bring !
Clément
- Lyon, Rhône, FRANCE
A. Hi Clément,
opinion! If your company works hard to make your product last longer, they'll reduce their impact on the environment a hundred times as effectively as they will by trying to substitute "less toxic" passivating agents. I don't think it's coincidence that worldwide pressure to reduce the use of phosphatizing before painting coincides with the world now drowning in truly crappy steel patio furniture, gardening equipment, and other objects that last 1-3 years when we know perfectly well how to finish them to last 15-20 years. We eliminated a pound of phosphate at the cost of mining, smelting, rolling, fabricating, painting, packaging, selling and landfilling a ton of steel every 3 years instead of every 20 -- with all the transportation waste between each of those steps as well :-(
Let's hope your company doesn't move in the same direction when finishing stainless steel. Our planet just cannot afford the assault on sustainability that today's pressure to reduce toxics in finishing seems to be wreaking. Proprietary citric acid formulations are a proven solution which eliminate chromic acid and nitric acid; you don't need to hunt for "less toxic" than that, although you should certainly endlessly hunt for "better at prolonging the life of stainless steel" :-)
Regards, and best of luck,
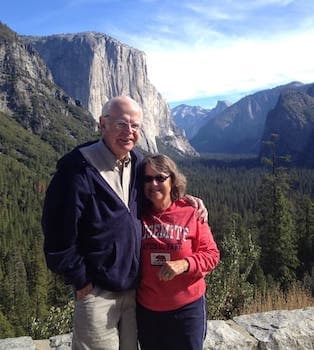
Ted Mooney, P.E. RET
Striving to live Aloha
(Ted can offer longterm or instant help)
finishing.com - Pine Beach, New Jersey
December 2016
Q. Hi Ted,
I understand your point of view, and I only can agree. But I'm not really involved into the politic of my society, they just gave me this job, and here I am! I am a student, and this is my work's subject in the company (because I am one month at school, one month at company). So yeah, we should work on the life duration of produced steel, but this is not my job here. I am just a chemist working on bath's compositions :-)
Regards,
- Lyon, Rhône, FRANCE
December 23, 2016
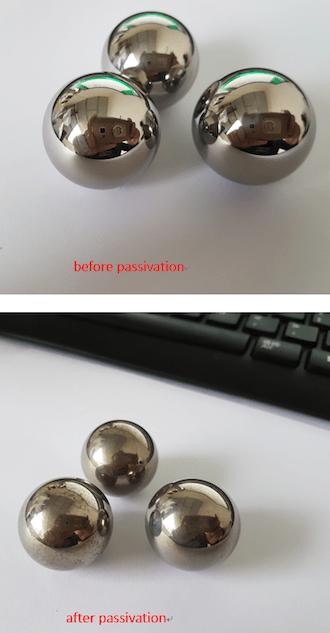
Q. We are working on a project of effective passivation of steel balls made from 440C material that need to pass 2-H salt spray test. We've been comparing citric acid and nitric acid. The problem with 50% nitric acid is it will occasionally fail, the balls can't pass salt spray test. However, with 7-10 weight percent citric acid , the balls can pass salt spray test but the surface is somehow changed in the bath, becoming not shiny.
After acid bath, all samples are soaked in sodium dichromate at 70 °C for 1-H. can someone give me a clue of what happened? Why surface changed in citric acid batch?
Rui Fang- Sichuan,China
April 12, 2017
Keeping CA6NM Cast Stainless steel Rust Free
Q. I have greatly expanded my limited knowledge of passivation by reading through this 10 year old thread! But I didn't find anything to answer my specific question. We procure pumps for our customer with pump casing castings made of CA6NM, a 400-series stainless steel that develops a thin rust layer on as-cast surfaces. Our customer objects to the rusty look, but would also like to avoid the lifetime maintenance burden of painting the pumps.
My understanding of the rust layer on as-cast surfaces (but not machined surfaces) of this material is that it is purely cosmetic and results from the heat treatment that creates a thin chromium depletion zone on the surface that then rusts in the air. Any machining or grinding on the surface strips away this chromium depletion zone, leaving those surfaces largely "rust" free.
So my question is, what is the best, most cost-effective method of preventing this rusty appearance on non-machined, as-cast surfaces that we can require of the pump/casting supplier? Is passivation a good option for CA6NM? Would simply wire-brushing the entire surface maintain a rust-free appearance by removing the chromium depletion zone?
- Newport News, Virginia USA
May 11, 2017
Ed. note: This RFQ is outdated, but technical replies are welcome, and readers are encouraged to post their own RFQs. But no public commercial suggestions please ( huh? why?).
A. Jim,
A lot of the problems with stainless steel come down to what happens during the heating and cooling of alloys. The operative technical term is "eutectic temperature", but the key ideas are that during slow cooling from a fully liquid state, the different metals in the alloy have a tendency to self-segregate, producing local regions where the alloy composition is quite different from the overall alloy composition. This comes into play with castings. A second key idea is that you can produce this effect even when the temperature didn't quite reach the full melting point, which comes into play during heat treatments and the heat affected zone of welds.
So the surface of a stainless casting is theoretically "not quite right" to begin with, and then throw in the roughness and porosity (the amount of which does vary depending on the exact casting method, e.g., sand vs. wax & such) and things are even worse.
Some sort of mechanical descaling method, usually bead blasting, does seem to help in most cases.
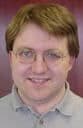
Ray Kremer
Stellar Solutions, Inc.

McHenry, Illinois
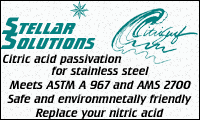
May 12, 2017
Q. Ray, thank you for your response and background on the issue. You stated "Some sort of mechanical descaling method, usually bead blasting, does seem to help in most cases." I have noticed any area of the cast surface that had any grinding or wire-brushing performed did not rust. Do you think bead blasting would be as effective than grinding or wire-brushing in maintaining a rust-free appearance for the long term?
Jim Meadows [returning]- Newport News, Virginia USA
May 23, 2017
May 31, 2017
A. Jim,
I'll just say that any disruption of the surface is better than the original as-cast surface. I've seen a lot variation in casted parts and some of then need more work than others to get to a decent surface.
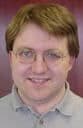
Ray Kremer
Stellar Solutions, Inc.

McHenry, Illinois
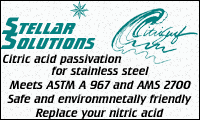
A. Hi
Regarding the question of whether citric acid is as good as nitric I found this presentation.
Interesting reading.
Alternate Finishing, Inc. - Hudson, Massachusetts USA
June 8, 2017
June 9, 2017
A. Different versions of that United Space Alliance/NASA presentation have been floating around for a while. They reach some dubious conclusions about the process times necessary (as compared to those in industry standards on passivation) but overall they do agree that citric is a viable method.
I have more test data and studies from a variety of sources that we've collected over the years.
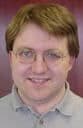
Ray Kremer
Stellar Solutions, Inc.

McHenry, Illinois
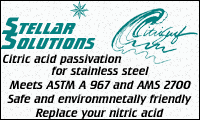
Drying Step in citric acid Passivation
Q. Hello,
I am working for a company that wants to passivate with citric acid on stainless steel piping and tanks. They are pressed for time and are wondering if the drying step is necessary when completing a successful passivation. If the drying step is necessary, is there any way to speed it up or any alternative methods?
Thank you
student employee - Rochester, New York USA
June 14, 2017
Ed. note: This RFQ is outdated, but technical replies are welcome, and readers are encouraged to post their own RFQs. But no public commercial suggestions please ( huh? why?).
A. Charlotte,
The basic idea behind stainless steel passivation is that the acid soak is pulling iron off the surface, which exposes new chromium and nickel. Then the surface is rinsed and dried so that the new chromium and nickel can grab some oxygen from the air and form chromium oxide and nickel oxide.
If you skip the air contact time, you've still removed iron, but the ideal process isn't QUITE complete.
One thing you can do in lieu of air contact time is contact with a peroxide solution, which serves as an alternate donor of oxygen atoms.
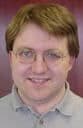
Ray Kremer
Stellar Solutions, Inc.

McHenry, Illinois
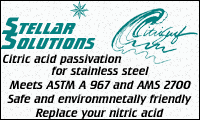
June 23, 2017
RFQ: Okay, so Ray, I'e been trying to find your 9310 product for a while. But as I'm not an industrial user, i.e., I do small work; I'm finding it impossible.
Whether nitric based solutions are better or worse, isn't a real problem, as they both seem to work if used properly. But I'd rather use a safer product whenever possible. Considering my small shop space, that means citric.
So how do I get it?
- Forest Hills, New York, USA
January 1, 2018
^- Privately respond to this RFQ -^
January 3, 2018
A. Mel,
Just click on the link next to my photograph there, that will take you to a page with my contact info. Drop us a line and we'll be happy to sell product to you.
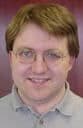
Ray Kremer
Stellar Solutions, Inc.

McHenry, Illinois
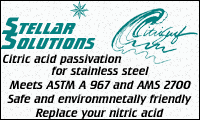
A. I got mine from Bulk Apothecary. They have large volumes and will provide a cert that includes source info.
www.bulkapothecary.com/raw-ingredients/other-ingredients-and-chemicals/citric-acid/
Flexial Corp - Cookeville, Tennessee USA
January 4, 2018
Q. Does passivization using citric acid qualify that process to be under 40 CFR 433?
Mike Roads- Los Angeles, California, US
March 29, 2018
A. Mike,
Regulations like this can be tricky. I recall a magazine article years ago that described a shop's problem convincing their local environmental auditor that their new powder coat booth should not be regulated as a painting booth. The hazards and necessary measures are completely different, but powder coating wasn't a thing when the laws were written and paint was the closest thing to it from the layman's perspective, so that's what the auditor wanted to use.
The 40 CFR 433 doesn't really mention passivation or anything that technically describes passivation, but you can tell their aim there was to capture all metal finishing processes that may involve hazardous chemicals. They probably has just never heard of stainless passivation, or else they almost certainly would have included it. A lot of environmental guys still today hear "stainless passivation" and assume the use of nitric acid.
So what I'm getting at here is that by the strict letter of the law, 40 CFR 433 doesn't include passivation, and by the spirit of the law, 40 CFR 433 wouldn't need to include citric acid passivation, but I wouldn't be at all surprised if many auditors would say that citric acid passivation is indeed included under 40 CFR 433.
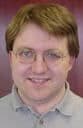
Ray Kremer
Stellar Solutions, Inc.

McHenry, Illinois
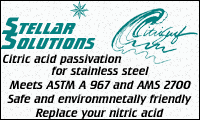
April 4, 2018
Q, A, or Comment on THIS thread -or- Start a NEW Thread