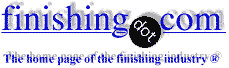
-----
Measure nickel & gold thickness on brass: SEM/backscatter or XRF better?
Q. I work at a Swiss Machining shop and we sometimes send parts out for plating, such as nickel and gold over brass. We are having trouble determining a method of how to measure the thickness of our plating. We have data from two (2) different sources with conflicting results, can you give me some insight on which method such as the scanning electron microscopy using a backscattered electron detector or fluorescence x-ray measuring devise is preferred. Which of the two would give me accurate true data? I would very much appreciate your opinion on this matter. We are applying 50 micro inches (min) type II gold over 200 micro inches (min) electroless nickel.
Thank you for your time,
Quality Control - Clackamas, Oregon, USA
2007
A. I would prefer SEM with the backscattered electron detector. The thing with XRF is that you have to calibrate it according to the coating you are applying and if the correct calibration is not available then it can give wrong readings. There is no such problem with SEM-BSE, just make sure that sample preparation is done properly and SEM is done by an expert.
Prat George- Baton Rouge, Louisiana
2007
2007
A. Jim
You need to tell us what is the shape and size of the parts, why you doubt the measurements and why they are important.
Plating is rarely uniform, particularly on small parts - it always builds up on edges.
From the spec you quote and 'swiss machining' would I be far wrong in guessing that you are making connector contacts?
Small parts are barrel plated and as well as plating distribution on each part, the average plating on parts tends to a normal distribution (Gaussian) curve. If you specify a minimum thickness, expect to pay for a thickness that allows three standard deviations over this.
But let's assume that you are comparing two measurements on the same point on the same part ...
In many years in the industry I have yet to see a SEM in a plating shop. With skill and knowledge it could be used to measure thickness but it is not the tool for the job.
XRF is the industry standard for plating measurement BUT it must be a dedicated instrument configured for the job, running the right software and properly calibrated. The calibration curve is complex and modern algorithms are a good fit. The resulting accuracy is good enough to satisfy bullion assay offices.
Don't even think of using microsections to compare thickness. Gold is soft and edge definition is almost impossible to guarantee.
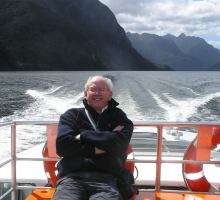
Geoff Smith
Hampshire, England
Nickel electroplating problems
Q. Dear sir/Madam
I am master Student, faculty of nuclear application and I am preparing a B.S Thesis.
I want to ask you how can I measure thickness of Nickel thin film (deposit) after electrodeposition without any device?
- russia
July 10, 2020
A. More words please, Shalva, Russia :-)
It is an oxymoron to ask how to measure something without a measuring device. You probably have some devices and methods in mind which you want to exclude, and it would probably be best if you attempt to name them, or describe what you can't do and why. Presumably destructive testing is excluded.
It is more or less possible to approximately 'measure' the thickness, at least theoretically, by using an ampere-minute meter and applying Faraday's Law of Electrolysis. Good luck!
Luck & Regards,
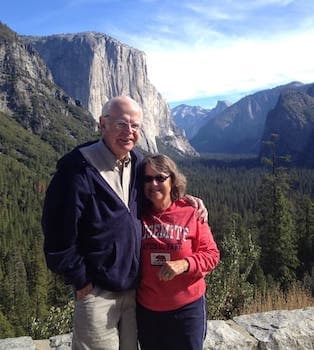
Ted Mooney, P.E. RET
Striving to live Aloha
(Ted can offer longterm or instant help)
finishing.com - Pine Beach, New Jersey
July 2020
July 14, 2020
Dear sir Ted
Thank you for your reply . and I am so sorry for my incomprehensible and insufficient question.
Now I will try to explain my whole experiment...
1 g of Ni was dissolved in a 69% solution of HNO3. Then concentrated H2SO4 was added to the film. Then 10 mL 25% of NH4OH was added. After neutralization we have/had 4.75 g (NH4)2SO4 to the solution . The solution was then placed in an electroplating cell. For electroplating a power supply was used, where the voltage can be given. An ampere meter is connected in the anode line in series connections to determine the current. As anode is a Pt-sheet, cathode is Cu-foil. The experiment was performed at room temperature.
The electrolytic cell was filled with about 2 ml of the electroplating solution. pH of solution is 9. The electrodeposition was performed for 16 hours. After 16 hours I checked the ampere meter and it show 0.0 mA but the solution was still blue- green color, and deposit was only 2.0 mg. while it should be 18-20 mg at least.
I have some questions about this topic:
Why did this happen?, what is the reason? and next for thickness theoretical calculation I used the formula from "nickel handbook" - 12.294 It/A. and the answer looks wrong. and I want some appropriate formula to calculate thickness of thin deposit.
Thank you for your help. I need it very much.
with best wishes
shalva
- russia
by William Safranek
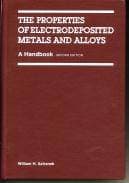
on eBay or Amazon
or AbeBooks
(affil link)
A. "There are more things in heaven and earth, Horatio, than are dreamt of in your philosophy." -- Shakespeare
So I can't claim to have heard of everything, but I am unfamiliar with plating nickel out of an ammonium sulphate solution, and was under the impression that very little nickel can stay ionized at pH 9.0. And if it's not dissolved it can't plate out. Safranek's rather exhaustive text ⇨
doesn't seem to mention attempts to nickel plate at a pH of higher than 5.9.
But why did your ammeter show 0.0 mA? That makes no sense at all. What was the voltage? And what was your basis for expecting 18-20 mg if no current was flowing? How do you know 2.0 mg was deposited?
As mentioned, Faraday's Law is the formula you use to make predictions of the amount of metal deposited vs. ampere-hours: At 100% efficiency 96,485 Amp-seconds will deposit 1 gram equivalent weight.
Luck & Regards,
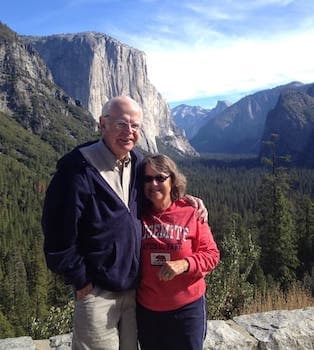
Ted Mooney, P.E. RET
Striving to live Aloha
(Ted can offer longterm or instant help)
finishing.com - Pine Beach, New Jersey
Dear Ted
Thanks a lot for your reply.
When my teacher prepared this solution, then we did 5 electrodepositions under same conditions. A voltage of 2.2 V was applied for 16 hrs (for all 5 samples) . The current remained between 9.0-1.89 mA; 8-2 mA; 6-0.1 mA ; 5-0.44 mA; and 4-00 mA.
First 4 days experiments result- the deposit was from 20-25 mg.( we checked the Weight of backing foil before and after electrodeposition and the difference was for first 4 days 20-25 mg and then only 2 mg)
And last experiment result was Unexpected and I can't understand How? because as I already say the conditions was absolutely same.
Thanks a lot for your help.
- russia
July 15, 2020
A. Hi again, Shalva. Unfortunately we continue to have language difficulties. I am trying, and I know what 'current' and 'mA' mean, but I have no idea what you mean by:
The current remained between 9.0-1.89 mA; 8-2 mA; 6-0.1 mA ; 5-0.44 mA; and 4-00 mA.
But if no current was flowing, no nickel plating should be expected. Maybe it was as simple as a loose wire for most of that experiment.
Luck & Regards,
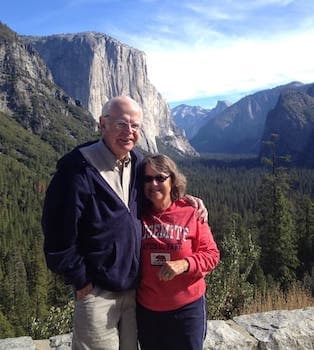
Ted Mooney, P.E. RET
Striving to live Aloha
(Ted can offer longterm or instant help)
finishing.com - Pine Beach, New Jersey
July 2020
Q, A, or Comment on THIS thread -or- Start a NEW Thread