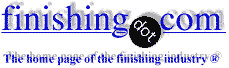
-----
Problems with Pickling and Passivating 304 Stainless Steel
Q. We have recently seen a problem with pickling and passivating 304 stainless parts. We are getting a very rough, black finish on the parts. When we inquired with our subcontractor who does the pickling/passivation, we were told that if there is a high carbon content, this is the result. Would 304L be a solution to this problem?
Regards
Jake
Quality Manager - Franklin, Pennsylvania, USA
2007
A. It sounds like your parts are being etched by the process. There is no reason for this to happen even with standard 304 (AISI 304) stainless steel if the pickling and passivation baths are correct. 304L is low carbon and may be better in the bath that is being used, of course, but it depends on the application of the final part whether you can use 304L.
adv.
Contact us if we can help further.
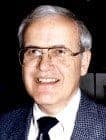

Lee Kremer
Stellar Solutions, Inc.

McHenry, Illinois
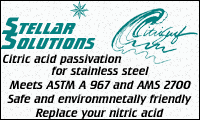
2007
A. Readers can only offer wild guesses because you have not said what your pickle and passivate processes are. I have passivated a lot of 304 and similar alloys and have not seen the problem. Exactly what 304 alloy are you using? A high sulfur content for free machining could turn black if heavily pickled.
James Watts- Navarre, Florida
2007
A. Any more info on this, Jake?
304 is rated 'very easy' in pickleability (easier than 316 & 316L) in AvestaPolarit's 'Handbook for the pickling and cleaning of stainless steel.' 304L would be better only if the 304 was sensitized, i.e., welded or improperly heat treated.
My wild guess: An heat treatment problem: either excessive oxidation (oxide still present) due to prolonged high temperature annealing or carbide formation due to an improper furnace atmosphere.
- Goleta, California

Rest in peace, Ken. Thank you for your hard work which the finishing world, and we at finishing.com, continue to benefit from.
2007
Passivation 304 SS for 960 hours salt spray
Q. Does anyone know of a passivation solution (manufacturer name and product) from a US supplier that could meet the ISO 9227 salt spray requirements for 960 hours?
Eddie Leon- scranton, Pennsylvania USA
September 3, 2019
September 2019
A. Hi Eddie. We can't post suggestions of specific brands or suppliers in this public forum (why?), but Stellar Solutions [a finishing.com supporting advertiser] and Russamer Lab [a finishing.com supporting advertiser] are reputable sources.
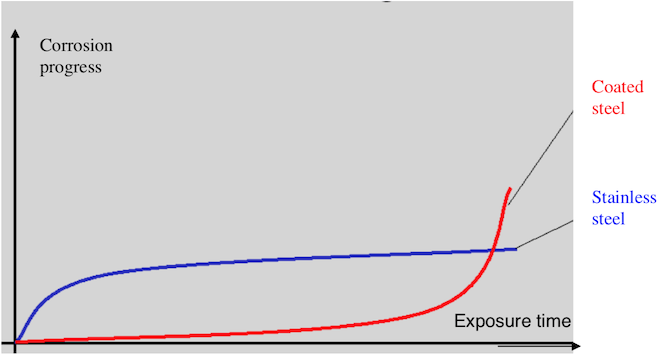
(courtesy www.worldstainless.org)
There is probably more to proper passivation than the solution per se, however; but it's also highly debatable whether 960 hours of ISO 9227 salt spray is a reasonable test of passivation. There are many good papers on the subject, but my favorite is probably "The salt spray test and its use in ranking stainless steels" from www.worldstainless.org because its simple pic explains the issue in a literal flash -->
-- You learn what you're going from the test fairly quickly, whereas the extended hours introduce 40 days & 40 nights of potential experimental error :-)
We encourage comments about these issues.
Regards,
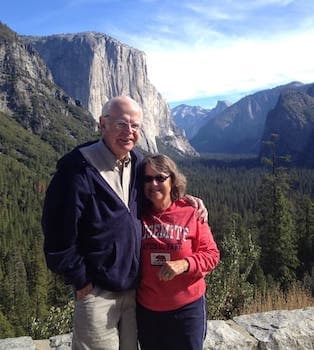
Ted Mooney, P.E. RET
Striving to live Aloha
(Ted can offer longterm or instant help)
finishing.com - Pine Beach, New Jersey
September 7, 2019
A. You can easily make a DIY passivation solution for high-chromium 300 series that meets the ASTM A380
Code G specification, and which is what we use for 304:
20-40% vv of 42° Bé(67%) Nitric acid in DI water
20-30 g/L Sodium Dichromate Pentahydrate (AKA Sodium Bichromate)
Immersion time dependent upon choice of temperature range. There are two options given in the Specification.
We use the hot one, which requires a sacrificial CPVC tank liner that is replaced annually, as this solution is very aggressive to plastics.
Change the solution when it becomes visibly dark and/or outside testing reveals Fe contamination above your shop limits.
Also, we run the Nitric at the lower end of the range, so the tank also conforms to Code I for other alloys, as well as AMS2700 Ty2, in case it is requested. Our parts pass 24h immersion; we have never had a salt spray request on this, but the method given is called out in the relevant Specification and would be the place to start your testing.
Threaded/blind hole parts require more attention in the form of continuous manual swishing or a roller barrel to be successful. This is in addition to normal tank mixing.
Be aware that this solution is extremely hazardous to operators and the environment, and all rinse waters, DI resins, broken equipment (the vapors kill mixer motors pretty fast), etc. that have come into contact with it must be treated and/or shipped as hazardous waste, and it needs to be run in a hood or other enclosure equipped with an air scrubber- even more so if using the heated option. I can't stress enough that this is literally THE MOST dangerous tank in our anodize/ conversion/ electropolish/ passivate shop, hands down.
Hopefully one of the resident Citric gurus will chime in to suggest a safer alternative for those who are unwilling or unable to set up this nasty process! We use Citric for a lot of alloys but 304 is not one of them. Yet. :) Though it IS allowed under AMS2700 Method 2 (see Table 4).
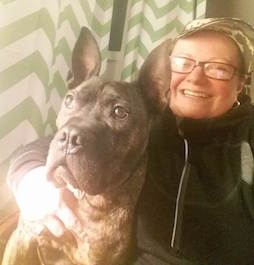
Rachel Mackintosh
lab rat - Greenfield, Vermont
A. Eddie,
The salt spray data I have capped things at 200 hours, so I don't know what the theoretical maximum hours is for 304. But if 960 hours is realistic, then I'm sure following ASTM A967 or AMS2700 will get you there. Probably either nitric or citric methods will do, though of course citric has safety advantages.
(Thanks for the shout-out, Ted!)
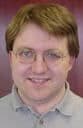
Ray Kremer
Stellar Solutions, Inc.

McHenry, Illinois
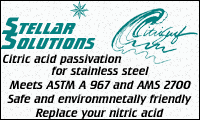
September 20, 2019
Passivation Process for 304SS Fasteners for Battery
Q. My company is a manufacturer of stainless steel fasteners.
I have some part of SS304 that is to be "tested in 24 hours at 60 °C for 24 hours in 1.28 H2SO4. Fasteners should not exhibit any weight loss and immature immersion when the test period is over". Which solution to use for Passivation so that the product can pass it in the above test. Any advice is appreciated.
- India
July 17, 2020
A. Hi Avinash. I don't know what "1.28" sulfuric acid means, but I'd try citric acid passivation, and if it doesn't survive the test, then I'd try electropolishing.
Luck & Regards,
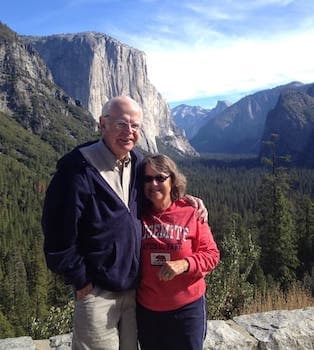
Ted Mooney, P.E. RET
Striving to live Aloha
(Ted can offer longterm or instant help)
finishing.com - Pine Beach, New Jersey
July 2020
Q. Hello Sir,
Testing parameter is "Tested in 24 hours at 60 °C for 24 hours in 1.28 specific gravity H2SO4. Fasteners should not exhibit any weight loss and immature immersion when the test period is over".
I tried Nitric Acid + Sodium Dicromate for passivation. But after passivation, part not pass in above test.
Which other solution to use for Passivation so that the product can pass it in the above test. Any advice is appreciated.
- India
July 18, 2020
A. Hi again. If passivation by immersion has not worked, try electropolishing as the passivation method. However, I have no particular reason to believe that this desired test result is achievable or non-achievable, so you might double-check with your customer that they have received similar 304SS fasteners that passed in the past.
Luck & Regards,
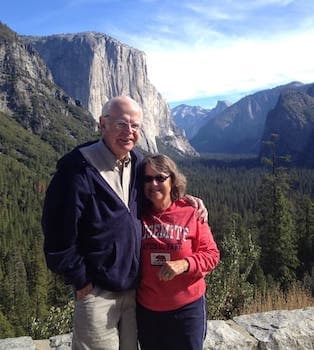
Ted Mooney, P.E. RET
Striving to live Aloha
(Ted can offer longterm or instant help)
finishing.com - Pine Beach, New Jersey
July 2020
August 14, 2020
A. Hi Avinash,
Assuming that it is achievable to pass the acid immersion test, which Ted is right to question, go back and be sure you have done the following in your process:
-Match the solution you are using to passivate to the correct concentrations and temperatures for that alloy. This information is found in ASTM A380
table A2.1 Part II.
-Test your solution once you have made it to be sure the concentrations are as you intended to mix them
-Be certain that your precleaning is effective. This means parts MUST go into the process free of grease and scale. Oils dragged in to the nitric-dichromate bath on parts are trouble!
-Use a mildly alkaline soap that is well agitated, preferably with ultrasonics as well, particularly if there are tight contours on the part.
Without knowing your existing process, it's hard to give more than general things to watch out for.
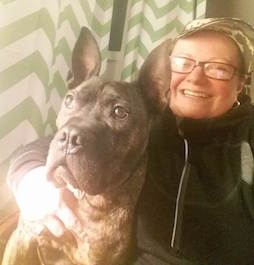
Rachel Mackintosh
lab rat - Greenfield, Vermont
A. Not achievable, Passivation is an oxidation process. Sulfuric Acid is a reducing agent. No matter how passivated (oxidized) you attain, the activation (reducing) of the sulfuric acid (at any strength over time) will remove the oxidation.
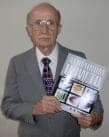
Robert H Probert
Robert H Probert Technical Services

Garner, North Carolina
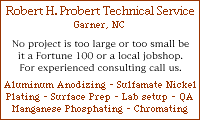
August 14, 2020
August 17, 2020
Q. Hello Rachel,
I pre-clean my product before passivation so that there is no oil, grease and scaling in it.
Let me tell you the whole process of manufacturing our product.
1. Forging
2. Rolling/Threading
3. Cleaning (two times alkaline soap washing & normal water washing).
4. Pickling (HNo3 & HF).
5. Passivation (Nitric Acid + Sodium Dichromate)
6. Testing (Testing parameter is "Tested in 24 hours at 60 °C for 24 hours in 1.28 specific gravity H2SO4. Fasteners should not exhibit any weight loss and immature immersion when the test period is over".)
I review all the parameters of my process and testing twice but nothing worked out.
Would you like to give me some more advice for pickling and passivation so that my product can pass in testing?
Any advice is appreciated.
Regards,
- Haryana, India
A. Hi again Avinash. Robert offered the opinion that the test isn't passable; Rachel offered the opinion that this test may not be passable.
I suggested trying citric acid passivation because it's easy, but offered the opinion that electropolishing (which eliminates all nooks & crannies, and smooths the surface, offering less surface area to be attacked) will improve the situation and might possibly allow you to pass ... but that you should verify with the customer that the test has been passed by other suppliers. I am not sure what any of us can do for you until then. Thanks and good luck!
Luck & Regards,
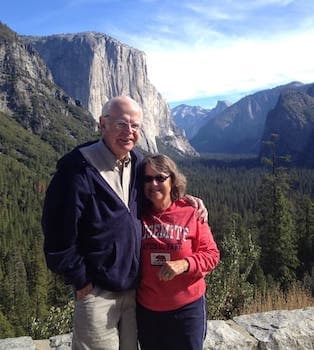
Ted Mooney, P.E. RET
Striving to live Aloha
(Ted can offer longterm or instant help)
finishing.com - Pine Beach, New Jersey
August 2020
August 19, 2020
A. Hi again Avinash,
Even with the info you've on your process, there are so many details that matter here! It's almost impossible to address them all.
Even without the burden of this crazy test you've been asked to perform, threaded parts are particularly challenging and are often done in a basket with a rolling/tumbling action in the tank to knock out air pockets and increase agitation. And it is important that the machining is done with sharp tools and an appropriate feed rate. Subtle issues in the machining can become big problems in the tanks. There are a LOT of variables! This is just one of them.
But at the end of the day, a prolonged immersion in a solution known to be damaging to stainless steels, even when passivated perfectly, may end up being a test not surmountable.
Have you tried passivating and then testing perfectly turned pieces of your stock, with no threads and a well cut finish, to rule out issues with contours or the threading process?
Also, the purity of your rinse waters at each step is important. The final rinse should be in hot deionized water with a very low conductivity. We still don't know so many details. I would not suggest city water for your final rinse.
I agree with Mr. Probert that this test is too aggressive for the material, so I am simply pointing you in the direction of best practices in a more general sense.
Usually proof of passivation is done by controlled water immersion or by copper sulphate
⇦ on
eBay or
Amazon [affil link] test. Have you performed and passed those?
I understand this is frustrating... If you troubleshoot your process bit by bit, eliminating each variable as a source of failure, and using more traditional tests along the way to confirm that you can passivate to generally accepted standards, at the very least you will be able to say with confidence that what you are being asked to do is unreasonable. As my dear work friend who has been doing this for 30 years always says, "we are platers, not magicians"!
Good luck and don't beat yourself up over this.
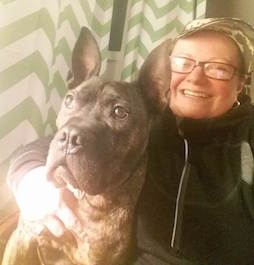
Rachel Mackintosh
lab rat - Greenfield, Vermont

this text gets replaced with bannerText
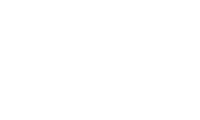
Q, A, or Comment on THIS thread -or- Start a NEW Thread