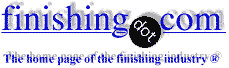
-----
Chromate rubs off of zinc plating
Q. Hello,
We are doing zinc yellow passivation on a small component of size 35 mm X 15 mm. The problem is yellow passivation is coming out when rubbed against rubber sheet. passivation has shine and is in bright yellow color. Does passivation quality depend on base material quality? We are using MS CRCA sheet. Please help use in finding solution for this problem.
Best Regards,
power systems - Hyderabad, India
2005
A. Faiz
From one Hyderabadi to another...
- Rinsing after Zinc plating is important. 2 flowing water rinses are necessary. Clean water.
- One Nitric acid dip of 10 to 15 mls per liter Nitric acid for 20 secs is necessary .
- The passivate I trust is made up as per the manufacturer's instructions.
- The passivated parts must be rinsed well in clean water 2 to 3 rinses.
- drying in air is fine , but if you bake don't cross 80 °C. 3 to 5 minutes.
- Lastly , the yellow passivate needs 24 hours curing time before doing any sort of testing.
Hope this helps.
Regards,
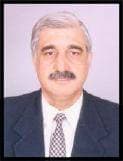
Asif Nurie [deceased]
- New Delhi, India
With deep regret we sadly advise that Asif passed away on Jan 24, 2016
A. YOU HAVE NOT MENTIONED WHICH TYPE OF PLATING BATH YOU ARE USING. HOWEVER WASHING BETWEEN PLATING AND CHROMATING, AND PROPER PREPARATION OF PASSIVATION BY USING LR GRADE NITRIC ACID WILL IMPROVE. EXCESS CONCENTRATION OF CHROMATE MAY CAUSE POOR ADHESION, MAINTAIN MINIMUM THICKNESS OF 8 TO 10 MICRON OF ZINC COATING.
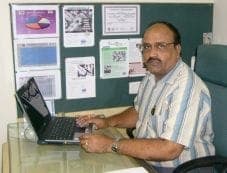
P. Gurumoorthi
electroplating process chemicals - Chennai, Tamilnadu, India
2005
A. The previous responders are all quite correct. A few other points if you please. The reason it is necessary to know if you are using an alkaline or acid plating bath is that acid chloride additives tend to increase the total organics in the bath and consequently interfere with the formation of hexavalent yellow films. The solution to this is to purchase a chromate formulated to be effective on chloride zinc, rinse well and pre dip in 0.5% nitric (although sometimes 1% sulfuric acid works better!). It is also helpful to reduce the total organics in the plating bath by lowering the amount of brightener used, carbon filtration and oxidation. Further, be sure that there is no oily residue on the surface of the zinc bath (for all types of electrolytes), rinse tanks or chromate.
When using an alkaline electrolyte good rinsing and maintenance of the acidity of the acid pre dip is a must to keep from getting the chemistry of the chromate out of balance.
Finally, as mentioned in the other replies, do not overheat when drying. If work is done in a barrel do not over rotate when chromating and do not over dry. Among the other don'ts for barrel work is do not reverse direction of the dryer to aid in stopping the rotation. This causes the parts to scrape against each other and remove the chromate.
process supplier - Great Neck, New York
2005
A. Mr.Faiz , In Bangalore platers are using a chrome fixer which normally fixes the passivation , even after rubbing passivation won't removed, which has to be used @3%,and as a last rinse before drying.
All the best.
- Bangalore, KARNATAKA, India
2005
Multiple threads merged: please forgive chronology errors and repetition 🙂
Q. I purchased a small plating shop that does Zinc and Anodizing. We have suddenly run into a dull finish on our zinc parts and the color is wiping off (rectifier?) They used to be shiny with a rainbow luster. We recently sent a sample to MacDermid for analysis to see if we are properly mixed. We run cyanide^NON-cyanide, have added brighteners and still not getting results. We are a work in progress so please be kind ;)
Thanks, Mike
company owner - Rancho Cordova, California USA
2007
![]() |
A. First of all, DON'T add any more brightener to the plating tank. It doesn't sound like it's the problem. ![]() Dave Wichern Consultant - The Bronx, New York 2007 A. Mike, ![]() T.K. Mohan plating process supplier - Mumbai, India 2007 |
Q. Hey Folks, I was in error when I said I was using cyanide. The guys tell me it is non-cyanide alkaline zinc. My apologies for the misinformation. Thanks for the responses so far. I will share the results once we have everything fixed.
Mike Wigley [returning]electroplating - Rancho Cordova, California
2007
A. I am a bit confused. Is the work dull that is the problem, or is the rub off of the yellow the problems. Both should be. Alkaline non-cyanide zinc will plate bright with good yellow chromate adhesion. The rinse(s) after plating should be clean and have a near neutral pH. You should then have a pre-dip tank before chromating consisting of 0.5% nitric acid. This will help remove residual alkaline and organic films from the deposit as well as brighten up the finish. A properly formulated hexavalent yellow chromate generally has a pH of between 1.8 and 2.0. If your pH is higher you have either a weak chromate or one which has been contaminated by drag over of the alkali from plating. If the latter is true, additions of acid or even chromate to maintain pH will at some point unbalance the chromate resulting in non adherent films. Finally, as has already been pointed out by previous responders, you rinsing after chromating needs to have adequate flow to be clean. A final hot water rinse (120 °F) is recommended. If you are barrel plating there can be mechanical reasons for finishing problems.
Gene Packmanprocess supplier - Great Neck, New York
2007
A. Hello,
This problem may arise due to 2 typical situations:
1. There is too much of carrier brightener in the alkaline zinc bath.In such a case it does not passivate properly.
2. Usually the Bright dip concentration recommended is 1% v/v so that the excess alkalinity is removed completely before yellow passivation.
Besides the above 2 reasons, there is always a likelihood of acidic fumes condensing on the passivated parts when Relative Humidity is high wiping off the passivation color easily.(this happens in small shops without separate stores for finished goods.)
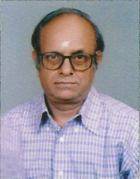
Subramanian Ramajayam
consultant - Bangalore, India
2007
Q. Hi,
I have started an electroplating shop recently and currently using cyanide based system. After electroplating when we are doing yellow (rainbow) passivation; that passivation seems unstable and tends to leave the surface in some places... especially TIG welded places of the part. Can anyone please support me to overcome this situation?
Plating shop owner - Srilanka
October 22, 2017
A. Hi Aravinda. Are you sure you have correctly identified the problem? Before we go on, what evidence do you have that the zinc plating is depositing on, and adhering properly to, those welded areas? Good luck.
Regards,
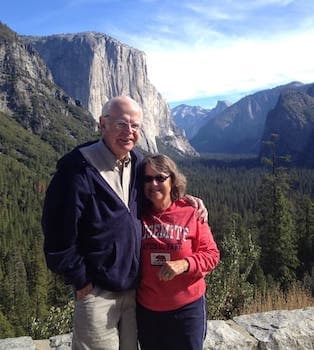
Ted Mooney, P.E. RET
Striving to live Aloha
(Ted can offer longterm or instant help)
finishing.com - Pine Beach, New Jersey
October 2017
Information requested regarding Trivalent Yellow Passivation
Q. We have a component for which we are plating 25 microns of yellow trivalent plating. After plating process, there is hydrogen de-embrittlement process & cleaning. But, we are facing a quality issue in these parts. After three to four days of plating, yellow colour is getting removed by light hand rubbing. After slight hand rubbing, white patches appear on the part. So, request you to share your inputs to improve this situation.
Bharat Kulthe- Pune, Maharashtra, India
December 4, 2017
A. Hi cousin Bharat. The first thing I would do is try doing the hydrogen de-embrittlement process before the chromating. Good luck.
Regards,
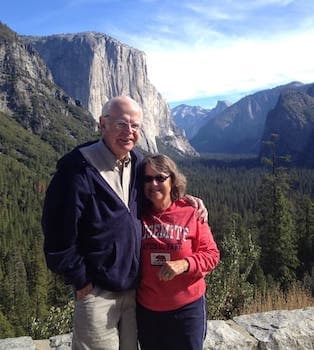
Ted Mooney, P.E. RET
Striving to live Aloha
(Ted can offer longterm or instant help)
finishing.com - Pine Beach, New Jersey
December 2017
A. Hello Bharat,
As Ted said, you may have better results when the chromate doesn't pass through the baking process. AND If I were the process designer for this particular part, I wouldn't dare to bake with the chromate, because the high thickness of the coating makes it more difficult to hydrogen to escape, and chromate makes it harder. You surely will have better results in embrittlement relief baking without chromate.
Best of luck!
TEL - N FERRARIS - Cañuelas, Buenos Aires, Argentina
December 13, 2017
A. 25 microns is a lot of plating particularly if it is zinc electroplating. I would be worried about deposit ductility. I think that if you need that much coating or corrosion protection you should investigate alternative processes such as mechanical galvanizing, hot dip galvanizing, dip-spin coatings, or zinc-nickel plating.
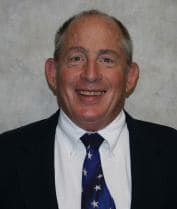
Tom Rochester
CTO - Jackson, Michigan, USA
Plating Systems & Technologies, Inc.

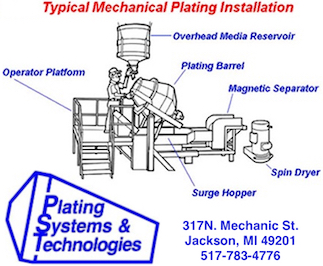
December 18, 2017
Q. Dear Friends,
I am having some doubts related to the zinc passivation. Recently I inspected some door connectors with the coating of zinc passivation. But in that the yellow galvanization is getting removed by rubbing it in thumb continuously for several times, but the coating thickness is nevertheless as required. So, can you please clarify the reason for the removal of galvanization and what will be the future defects due to this?
- Delhi, India.
January 16, 2018
A. Hi Suresh. The yellow chromate conversion coating as it stands is improper -- it should not easily rub off with a thumb. There are several possible and common causes. Insufficient curing time (you should not attempt that thumb test for at least 24 hours after plating), drying at too high a temperature (should not exceed 140 °F / 60 °C), or excessive brightener in the zinc plating tank for starters (plus, of course, a defective chromate bath).
In the USA we do not call zinc electroplating 'galvanization'; I'm not sure of the custom in India. In any case, it is probably not the zinc plating which is being removed with your thumb, but just the yellow chromate conversion coating (passivation). Good luck.
Regards,
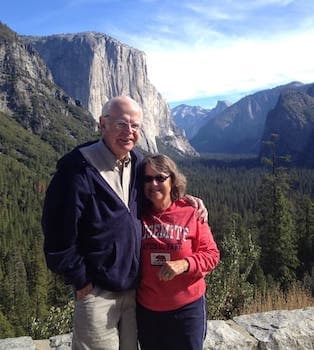
Ted Mooney, P.E. RET
Striving to live Aloha
(Ted can offer longterm or instant help)
finishing.com - Pine Beach, New Jersey
January 2018
A. We have encountered the same problem. Ours was insoluble oils carried from degreasing got into the zinc plating and passivation baths resulting in that the passivation could be rubbed off.
Robert Mathisen- Gjovik, Norway
April 19, 2018
Q. Yesterday a client of mine lamented that the black coating (trivalent black zinc acid passivation with min 10 µm) is rubbing off. Earlier that day I did some other pieces that seemed to be perfect. Client mishandling or other? Some pics:
- Rome Italy
November 24, 2020
A. Hi John. Although your question is about black chromate, and this thread was previously about yellow chromate, they are similar enough that I'm sure there is good food for thought on this page, so we appended your inquiry to it. But first, are you saying you gave the parts to your customer immediately with no curing time? Chromates should cure for 24 hours before handling.
Luck & Regards,
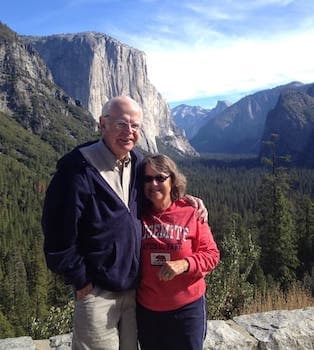
Ted Mooney, P.E. RET
Striving to live Aloha
(Ted can offer longterm or instant help)
finishing.com - Pine Beach, New Jersey
November 2020

Q, A, or Comment on THIS thread -or- Start a NEW Thread