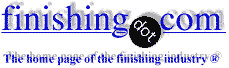
-----
Reducing galvanizing thickness by adding nickel salts
Q. Dear Sir,
To reduce the coating thickness,some galvanizers use Ni contained salts and the other metallic salts in the fluxing or directly adding Nickel into Kettle,
Do you suggest any idea or solution besides of above suggestion?
Thanks
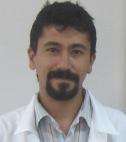
Hakan Esen, Material Engineer(BSc.)
galvanizing plant manager - Bursa, Turkey
2007
A. Sir,
Listed in the order of most effective first, the following have been found to reduce zinc coating thickness on reactive steels (those higher in silicon and phosphorus):
(1) IQM (my trade secret; it means Improved Quality Method)
(2) quadraflux (read my article in Metal Finishing)
(3) lower zinc temperature (828 F; 442 C; requires deep kettle with adequate thermal capacity)
(4) short zinc immersion times (approx. 1 to 3 minutes; which requires absolute flux control and quadraflux)
(5) process control of caustic, pickling, flux
Regards,
Galvanizing Consultant - Hot Springs, South Dakota, USA
Q. Hi,
According to some articles, Ni tablets are preferable in the molten zinc to reach the less zinc consumption. As I asked before, what is the range of Nickel in the molten zinc and which type is preferred (nickel powder, nickel tablet and Ni based flux)
For 1 and half year, we utilize nickel salts based flux solution, and suppliers in Dubai (Middle East Conference of IZA) suggest advantages of utilization of nickel,especially tablet form.
What do you think about this phenomena? (addition type,nickel effect and optimum range)
Thanks
Regards..
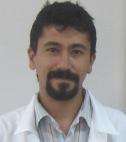
Hakan Esen, Material Engineer(BSc.)
galvanizing plant manager - Bursa, Turkey
January 27, 2009
![]() |
A. An other option is buying zinc that is already does with Ni. This saves any issues about how much Ni is recovered into the melt, and of getting the dosage rate wrong. Buy it premixed and save all uncertainty. ![]() Geoff Crowley Crithwood Ltd. Westfield, Scotland, UK ![]() March 9, 2009 March 10, 2009 A. Sir: Galvanizing Consultant - Hot Springs, South Dakota, USA |
Q. Dear sir,
We are general galvanizers. We are galvanizing steel gratings, structural steels,oil pipes. All materials having silicon percentage from 0.15-0.40. Our zinc consumption per ton is 60 kg. Our consumption is very high. The coating thickness is 150 to 300 microns. Please advise us how to reduce zinc consumption in high silicon materials.
galvanizing. - Dammam, Saudi Arabia.
June 14, 2011
Q. Dear Mr Cook,
Good day to you,
Referring to the above mentioned "Nickel suspended in wax", do you mind sharing the measurement results of nickel content in the smoke?
Also, regarding the mentioned IQM, can I get a brief introduction? Not sure how to proceed.
Thanks & regards,
- Selangor, Malaysia
September 30, 2013
Q. Hi
I am a mechanical engineer but work in hot dip galvanized pipe industry in Vietnam. My factory has been in operation for only 1 year.
We are planning to use NiCl2 (NiCl2 and NH4Cl) in aqueous Flux solution before galvanized.
I do not know when I use NH4OH and H2O2 to treat acid (HCl) and Fe2+ in Flux solution whether to affect NiCl2 in Flux solution, thanks to the analysts help me.
The reason we want to use NiCl2 in Flux solution to reduce the zinc layer thickness. I need some expert advice for this and give me the proper concentration of NiCl2 and NH4Cl (the immersion time is 1 minute in zinc tank).
Thanks & regards,
Vina One Steel Manufacturing Corporation - Ho Chi Minh City, Vietnam
March 5, 2019
A.
Nickel is well known to produce human lung cancer. Also it is unlikely that you can maintain proper nickel in the flux or purify out the iron. Because pipes are normally made from relatively non-reactive steel, and zinc immersion times are short (one minute), I expect your flux is not well formulated.
In South Africa, four pipes galvanizing lines had very low ACN and high baumé. This produced 200 microns on the inside of the pipes with very rough coatings. We increased the ACN, and made other changes and got between 20 and 40 microns on the inside of the pipes. The plant managers said the inside zinc coating was as smooth as a baby's butt. We also heated the air for the outside blow which decreased the outside zinc coating thickness. They also put in two steam accumulators which gave a much better internal blow.
The major pipes galvanizer in the USA uses super-heated steam.
Regards,
Galvanizing Consultant - Hot Springs, South Dakota, USA
March 6, 2019

Q, A, or Comment on THIS thread -or- Start a NEW Thread