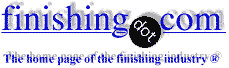
-----
Can Trivalent Chromium degrade into Hexavalent Chromium?
! In my lab a long time ago I did change the trivalent ^ hexavalent chrome into hexavalent ^ trivalent chrome using sodium metabisulfite (just as a waste).
After raising the pH to 10.5, let it rest overnight -- you will see all trivalent chrome at the bottom of the precipitation tank.
Aerospace chemist/Plating /Lab technician/hazardous waste specialist - Brooklyn, New York
May 2, 2022
A. Hi Elvis. I think you've inadvertently swapped the words 'trivalent' and 'hexavalent' in your first sentence.
Luck & Regards,
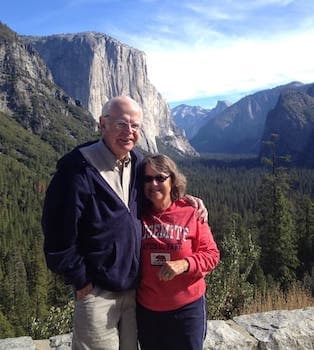
Ted Mooney, P.E. RET
Striving to live Aloha
(Ted can offer longterm or instant help)
finishing.com - Pine Beach, New Jersey
A. I find the phrasing in this post so interesting. Does trivalent chromium "degrade" or "revert" to hexavalent chromium, as if hexavalent is the natural state or inevitable state of chromium, and all it takes is time for this change to occur.
This is a redox reaction. Trivalent means +3, chromium atoms missing three electrons. Hexavalent means +6, missing six electrons. Atoms and ions don't gain or lose electrons easily, usually it happens only when other atoms or ions give or take some electrons in an oxidation-reduction reaction. So the first point, trivalent chromium can't change to hexavalent chromium without the presence of an oxidizing agent.
The gain or loss of electrons can be energetically favorable or disfavorable, referred to by chemists as the reduction potential. A reduction-oxidation reaction only occurs if the net energy change is favorable. If you look at the Latimer diagram for chromium, zero valence chromium "wants" to become trivalent chromium, and hexavalent chromium also "wants" to become trivalent chromium. So to oxidize trivalent chromium into hexavalent chromium, you need an oxidizing agent that "wants" to be reduced by a greater energy amount than trivalent chromium "resists" being oxidized. This means it's not impossible, but is less expected to commonly occur.
I know the expectation here is influenced by hexavalent chromium being the industry standard for a very long time, but the industrial default isn't necessarily the same as the chemical default. Though obviously real-world conditions aren't always going to be the same as what the raw math tells us, either.
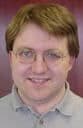
Ray Kremer
Stellar Solutions, Inc.

McHenry, Illinois
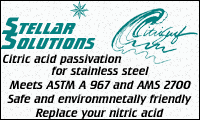
⇩ Related postings, oldest first ⇩
Q. I am currently doing a RoHS compliancy assessment for our products and this question came up today, could a RoHS compliant finish with trivalent chromium change in some way into hexavalent chromium? We use a multitude of acids and other nasty chemicals I really know nothing about (I'm an electrical engineer) We probably won't have to worry about it but it would be nice to know anyway.
Dylan GiffordRoHS compliancy Intern - Winooski, Vermont, USA
2007
A. It takes very, aggressive oxidizing conditions to convert trivalent to hexavalent chromium. If the parts were exposed to such, to the extent that the RoHS hexchrome limits were exceeded, there's little doubt in my mind that it would also degrade the coating. To the point that they would be so ugly, that no customer in his right mind would accept them.
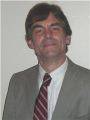
Dave Wichern
Consultant - The Bronx, New York
A. Hexavalent chromium tends to be oxidising in nature, having a tendency to head to the trivalent state. To convert trivalent chromium to hexavalent you will need quite forcing conditions, ones you won't find in a normal treatment shop or electronics business. So I am pretty certain you will not have to worry about RoHS compliance.
Brian TerryAerospace - Yeovil, Somerset, UK
2007
A. From a theoretical viewpoint trivalent chrome can be quite easily oxidized to Cr6 with peroxide in alkaline conditions.
From a practical view point it is highly unlikely that these conditions would lead to Cr6 being left in any chromate coating left on the plated part after exposure to the above solution, that is the Cr6 would be in solution.
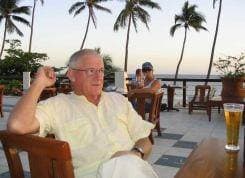
Geoffrey Whitelaw
- Port Melbourne, Australia
Q. Hi Brian,
You mention it would require 'quite forcing conditions' to convert trivalent chromium to hexavalent chromium. Would you be willing to provide a few examples of what forcing conditions might be please? Thank you in advance.
- NY
July 30, 2023
A. Hi A.
Geoff annunciated one of those conditions (powerful oxidizing chemicals under certain conditions), Celio & I another one (electricity under certain conditions), and Dave has said such conditions would likely ruin the component anyway. Bob & Tom have said that it can happen relatively easily but to such a limited degree as to probably be inconsequential. It is also well known that people can take trivalent chromium vitamin supplements without poisoning themselves.
We'd like to help further or more exactly, but the question is quite open in a similar way to "what will happen if I run a red light" :-)
Please introduce yourself and explain what prompts you to pose this question. Thanks!
Luck & Regards,
Ted Mooney, P.E. RET
Striving to live Aloha
(Ted can offer longterm or instant help)
finishing.com - Pine Beach, New Jersey
Trivalent Chromate Conversion Coating found to contain Hexavalent Chromium
Q. Can hexavalent chromium be produced in a chromate conversion coating that states it is purely made with trivalent chromium compounds such as chromium (III) nitrate?
If pH or temperature is not maintained, can hexavalent chromium ions form?
Are there any process parameters that if not controlled can cause hexavalent chromium to be formed in trivalent chromium tank?
These questions are related to fastener plating of chromate conversion coating over zinc electroplating over bare steel.
One further question, is there any way to effectively remove hexavalent chromium conversion coatings and re-plate with trivalent chromium conversion coatings from small fasteners in barrel?
Engineer - Newnan, Georgia, USA
2007
A. Hi Jeremy. First question last: Yes, it is generally easy to strip the zinc plating and chromate conversion coating and start over. If contamination of your tanks weren't an issue, it's as easy as re-running the parts because the chromate will come off in the electrocleaner and any remaining zinc will come off in the acid dip.
I get the sense that you are soliciting comment while being somewhat guarded about the actual facts -- like whether you are the supplier of the conversion coating chemistry, the shop applying it, or the buyer of the parts :-)
It's theoretically possible to convert trivalent chromium to hexavalent through a chemical or electrochemical reaction, but probably quite unlikely that poor operation of a trivalent chromating bath will cause it to generate hexavalent chromium, although you might read Geoff Whitelaw's very interesting comment about chromating baths that contain hydrogen peroxide in letter 10026.
I get the sense that someone is holding parts that test positive for hex chrome and you are asking how this most likely happened -- but probabilities of alternative scenarios are difficult to compute when we have little of the background information to go on. Good luck.
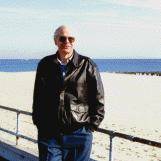
Ted Mooney, P.E.
Striving to live Aloha
(Ted can offer longterm or instant help)
finishing.com - Pine Beach, New Jersey
Q. I appreciate your response. This is just a preliminary inquiry - homework if you will. I have found hexavalent chrome in parts that are being sold as hex-free and solely using a trivalent chemical conversion coating (Chromium Nitrate) over zinc. So, where could it be coming from? If the pH gets high, what happens in a trichrome bath? Likewise, if the temperature gets high? Are there any parameters that if not controlled produce hexavalent chrome? Does anyone have the chemical equations?
Jeremy Lynn [returning]- Newnan, Georgia, USA
A. The equation itself isn't really complicated, Jeremy:
Cr+3 - 3e- --> Cr+6
But you need an oxidizing force (electricity or a fairly powerful chemical oxidizing agent) to remove those electrons that way. Second opinions are welcome but I can't see temperature or pH causing this.
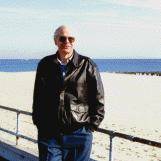
Ted Mooney, P.E.
Striving to live Aloha
(Ted can offer longterm or instant help)
finishing.com - Pine Beach, New Jersey
A. Got to say that I agree with Ted and that merely temperature and/or pH would not give you the conditions to form hex chrome from tri chrome.
It sounds to me more like a cross-contamination problem. You don't say what level of hex chrome you are finding, are we in the low ppm, high ppm or even higher? This will give us a clue to the extent of your problem.
Are there more than one type of chromate conversion on the line? If there is then it would sound like there has been drag in to the tri chrome conversion coating. Just an idea.
Aerospace - Yeovil, Somerset, UK
A. You don't say how you determined that there is hex in the tri chromate coating. One type of widely used test, generally said to be described in GMW 3044, can give a false positive in the presence of iron, cadmium, zinc (yes zinc) and certain organic compounds (sometimes found in zinc brighteners). A more accurate test is one which is done on an ICP to check for hexavalent chromium.
Gene Packmanprocess supplier - Great Neck, New York
A. Dear Pals at finishing.com,
Just for your information, I have been through a complicated situation like this with a company that used inox. [stainless] steel tanks instead of the plastic recommended by us and the tanks have been releasing hexavalent chrome into the liquid and contaminating the parts.
Regards and good luck!
- São Paulo, Brazil
Hi Celio. Thanks greatly for this info. Can we assume that this was an electrified tank? Electricity can probably turn chrome metal or trivalent chrome into hexavalent.
Can any other readers relate a similar experience?
Regards,
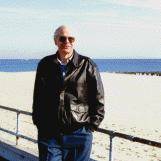
Ted Mooney, P.E.
Striving to live Aloha
(Ted can offer longterm or instant help)
finishing.com - Pine Beach, New Jersey
Does Trivalent Plating Revert Back to Hexavalent Plating
Q. I am a mechanical design engineer, and not an expert on zinc plating and chromate conversion. I specify my products per ASTM B633. I am aware of the RoHS compliance and avoiding the use of Hexavalent chromate conversion. The solution to this has been to apply a Trivalent chrome conversion. Recently a plating supplier suggested that the trivalent conversion coating gets converted to hexavalent coating over time and during shipping and thus rendering the part unfit. Does this phenomenon occur? Please advise? Thank You.
Bhaumik ShahEngineer - Buffalo, New York
2007
A. Time will tell, Bhaumik, and the richness of experience in a thousand different applications -- but the current belief is that we can count on it not happening.
Readers may be interested in the somewhat parallel thoughts expressed in thread 10026, "Trivalent conversion coatings with hydrogen peroxide added ... why?"
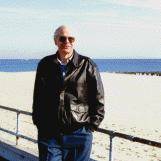
Ted Mooney, P.E.
Striving to live Aloha
(Ted can offer longterm or instant help)
finishing.com - Pine Beach, New Jersey
A. I believe there is an equilibrium reaction between Cr+6 and Cr+3 that is dependent on pH, but when in a solution like a conversion coating certain alloys (2024) will have reactions occur on the surface where some Cr+3 is converted into Cr+6. In general though the concentration is extremely low, and very difficult to measure.
Bob Hagerty- Patuxent River, Maryland USA
June 5, 2020
A. As a direct answer to your query - most of the trivalent chromium in a trivalent passivate remains in the trivalent state. But most of the chromium in a hexavalent passivate is also trivalent.
In October, 2007, Plating & Surface Finishing published an article by me and Zachary W. Kennedy entitled "Unexpected Results from Corrosion Testing of Trivalent Passivates" (Plating & Surface Finishing, October 2007, Volume 94, Number 10, pp 14-18). No one, to the best of my knowledge, has refuted our results, which are that trivalent passivates generate hexavalent chromium during the corrosion process. In my opinion, that is how they work.
If the generation of hexavalent chromium is suppressed (as in, for example, a Kesternich Test) trivalent passivates offer no increased protection in accelerated corrosion testing. (This I reported at Sur/Fin in 2009).) At this point in time, IMHO, the accepted position is that if the articles in question are free from hexavalent chromium at the conclusion of the plating process, they are arguably RoHS-compliant.
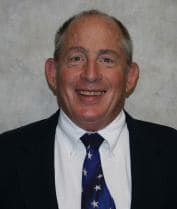
Tom Rochester
CTO - Jackson, Michigan, USA
Plating Systems & Technologies, Inc.

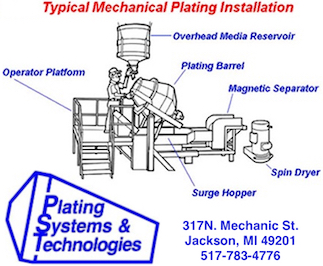
opinion! Thanks again, Tom. I'm very much in favor of metal finishing having a lower environmental impact, but I am also bothered by the almost universal tendency to legislate and deliberately stay blind to the consequences. So I appreciate it when you try to help us see that just because we wish something were true doesn't necessarily make it so!
- Item: We all know that a child can remove nearly all of the chromate from a zinc plated item with a pencil eraser, whereas a skilled machinist can't separate the zinc plating from a steel item, yet the European Union says the chromate is "homogeneous" with the zinc, but the plating is not "homogeneous" with the steel. When you're on a mission words lose all meaning :-)
- Item: Shops are constantly pressured to stop phosphating, when the truth is that eliminating phosphating before painting is an environmental travesty. Outdoor items used to last decades -- my expanded steel patio set was zinc phosphated, electrocoated, and powder coated -- and is going strong after being outside in the sun, rain, and snow 365 days a year for well over 20 years, 15 of it on an open deck over a salt water lagoon, plus a week or so submerged in brackish water during superstorm Sandy. In the meanwhile I keep replacing my newer outdoor stuff every 3 years or less because it wasn't phosphated. So here we have tons of ore mined, transported, smelted, hot rolled, pickled, and shipped to a warehouse; then shipped to a manufacturer for fabrication, pre-treatment, painting, and packaging; then shipped to a store, sold, brought home, and then landfilled or scrapped again & again & again to save a pound of phosphate once. The deliberate utter disregard for sustainability is mind blowing :-(
- Item: The most devastating environmental discharge in the plating industry (to my memory and I'm getting up there) was the White River fish kill in Indiana, caused not by discharge of a plating solution but of DTC -- a dangerous chemical that no shop willingly buys, wants on hand, nor uses ... but which is forced upon them to be used as a 'scavenger' after conventional wastewater treatment has already been done. I worked for Dr. Leslie Lancy, who brought plating wastewater treatment to the US after decades of success in Europe, and I remember him ceaselessly *begging* the regulators not to "split milligrams" and thereby force shops to use these dangerous unconventional treatments. And while the calamitous discharge in question was to a river, many shops must use DTC to meet their standards for discharge to stinky sanitary sewers :-(
I'm not claiming there isn't another side to the things I've point out -- just that there IS the side I am pointing out.
Regards,
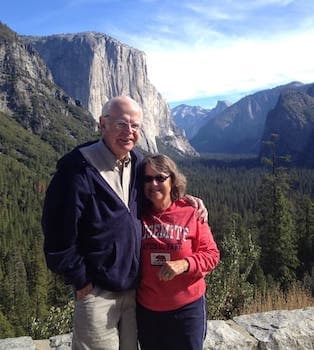
Ted Mooney, P.E. RET
Striving to live Aloha
(Ted can offer longterm or instant help)
finishing.com - Pine Beach, New Jersey
Q, A, or Comment on THIS thread -or- Start a NEW Thread