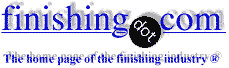
-----
Polishing Stainless Steel to a Mirror Finish
Current question and answers:
Q. I have a question along similar lines.
I have been trying to buff a stainless steel pot lid. I have tried grey, green, white and brown compound with a sewn cotton buffing wheel (concentric circles of sewing) and an un-sewn buffing wheel. I am left with a very, very faint lines which are seen easily when putting it up to a light.
Is it actually possible to get a very near-mirror finish using these buffing wheels and compounds?
With an un-sewn buffing wheel what would be the best compound to use?
By the way, the polishing machine I am using to put the buffing wheels on is actually a bench grinder. I took off the right side wheel and put the buffing wheel on in its place.
- St Catharines, Ontario
November 20, 2020
(affil links)
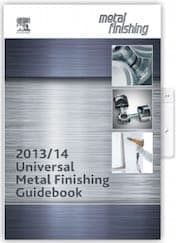
free pdf is currently available from academia.edu
A. Hi Christopher. My knowledge is only book knowledge, mostly from doing hundreds of postings on this topic. So we'll have to wait for someone else to really answer your question, but I can repeat what I've heard...
First, download the Metal Finishing Guidebook immediately -->
It has chapters entitled "The Science of Scratches--Polishing & Buffing" and "Buffing Wheels & Equipment" -- but I doubt that it will be available forever. Second, never use a buffing wheel with a fine abrasive if it has previously been used with a rougher abrasive; there is just no way to know that no rougher grains remain. Third, the ever-fineness of abrasives and mirror finishes can probably go on forever -- some people say they've used india ink as their final abrasive :-)
Luck & Regards,
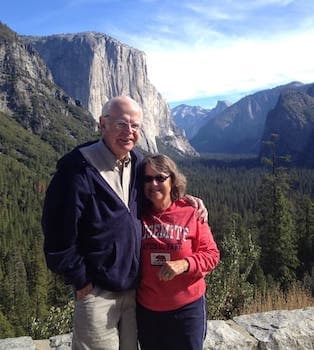
Ted Mooney, P.E. RET
Striving to live Aloha
(Ted is available for instant or longterm help)
finishing.com - Pine Beach, New Jersey
November 2020
November 20, 2020
After reading through this thread I went back and used a floppy buffing wheel (without the sewing) and a very small amount of white compound.
Using the technique described by another poster whereby I did not press too hard, but very lightly ran the wheel over the piece, the piece looks much better and quite acceptable for what I wanted. I found it interesting that there was a 'sweet' spot between pressing too hard and pressing too lightly.
Yes, there are still extremely fine 'swirl marks' but they are no where near as bad as they were before and are much less noticeable.
Thanks for the book recommendation. I have downloaded it and uploaded it for others to easily access as I didn't like having to sign up to access it. The link is here: http://matrixfiles.com/pdf/Metal_Finishing_Handbook_2012.pdf
- St Catharines, Ontario
⇩ Related postings, oldest first ⇩
Q. Hello Everyone! My name is Lawrence. I am the Quality Manager at a Precision Machine Shop where we make parts for the Military, NASA, Aviation Industry and Medical Industry.
We are having a problem Polishing a 301 Stainless Steel part to a mirror finish. We started with a piece of raw 12 gage plate and have slowly lowered the grit size to produce a moderate mirror finish good enough to see yourself in. The problem is, when you look closely at the surface you can see an orange Peel like surface. How can we get rid of this and bring the luster out better? Any suggestions on the total polishing process will be greatly appreciated. Thanks!
Quality Manager - Scottsboro, Alabama
2007
A. Sounds like a heat problem due to lack or little lubricant or rush. The correct sequence depends on what you or your customer define by mirror, the volume of parts, their weight and surface geometry among other variables. I can speak about low volume, relatively large and heavy parts with complex and selective surfaces to be polished to A-1 (mirror class defined by the Society of Plastics Engineers close to optically perfect with a total roughness and waviness value around 2 or less microinches). You need oil or mold maker stones down to 600. sandpaper down to 1500 or better. Then felt bobs and diamond paste down to 3 microns. A very clean environment (including hands, cloths and hair of the operator). And, above all, patience...a lot of patience. For large volume of small parts you'll have to ask a mass finisher. Good luck.
Guillermo MarrufoMonterrey, NL, Mexico
2007
Q. Thank you for the feedback. These parts are for the outside surface of an aircraft window. They are low volume now but may become higher in the future. They are bent to the shape of the aircraft within .06 (in) and they have countersunk holes about every inch or so. They are roughly four foot square but have an odd shape. They have a window opening in them making them around three inches wide from the outside of the part to the inside cut out.
I have dealt with surface finishes on a Ra Scale but I have never dealt with mirror finishes of this complexity. The specification that was given to me said that you have to be able to see a badge clearly with no distortion from one foot away and you have to shine a light from four feet away and have no cloudy spots visible.
I can see right now that our environment is going to be a problem because we sand blast in the same area. Where can we purchase the Oil and Mold makers' stones? I don't mean to sound ignorant but what are bobs? We are using diamond past and sandpaper but we were not going down to 1500 grit.
Again Thank You for taking the time to help us it is appreciated very much.
Quality Manager - Scottsboro, Alabama
2007
? What is size of your component? Problem maybe because of over heating.
Santosh Kashikarengineering - Mumbai, India
2007
A. Add to Guillermo's list, part size and if possible what surface finish you have prior to reworking

AF Kenton
retired business owner - Hatboro, Pennsylvania
2007
A. Large hardware stores or those specialized on abrasives will have the stones or just type "polishing mold maker stones" on a search engine. Several well known brands (Boride, DME and Gesswein) come to mind. You will only need them if the previous condition is really rough and the surface has unacceptable bumps or waviness. Otherwise you can use flat sandpaper and scotchbrite wheels mounted on rubber cups and high speed rotary motors (you need at least 10,000 feet per min). The felt bobs are pretty much like polishing wheels (they are also known as felt buffs) but are made of non-woven wool (vegetable or synthetic fibers are more prone to over-heat or scratch the surface). Keep in mind that SS has a very low thermal conductivity so it builds up heat quite fast. Use a light oil to thin your polishing compounds and pastes if they are too heavy. Good luck.
Guillermo MarrufoMonterrey, NL, Mexico
2007
A. Reread your info. This statement "We started with a piece of raw 12 gage plate and have slowly lowered the grit size to produce a moderate mirror finish good enough to see yourself in.", indicates to me you are blasting these parts before trying to polish. DON'T DO THAT! You also sound like a smaller shop that doesn't have access to a large mass finishing machine, so your best process is probably to work these parts with a non-woven wheel or belt system.

AF Kenton
retired business owner - Hatboro, Pennsylvania
2007
A. The orange peel you're seeing is due to large grain size. If possible use material which has been cold worked and not annealed. The orange peel should go away.
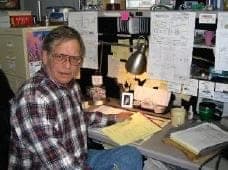
Jeffrey Holmes, CEF
Spartanburg, South Carolina
2007
Q. Thank You for all the responses! I'm sorry that I was misleading on the grit size. I was referring to the sandpaper and diamond past we were using. And "NO" we are not sand blasting these parts (We do know better than that). We have polished smaller parts in the past for the medical industry just nothing of this size and magnitude. AF Were could I get information on a large mass finishing machine. Right now we are using hand power tools.
We receive the SS sheet of material with a brushed looking finish on them. I would say it is about a 64 Ra finish. We are then sanding it with 180, 240, 600 & 4/0 grit sandpaper. From there we are polishing with diamond past grade #6, #3 & # 1. Using oil has helped a lot (Thanks Guillermo for that tip!) however we are still getting a pitted surface. Is it possible that we are not going deep enough at the first stages to cut this out of the stock or could it be something in our process? Thank You in advance!
Quality Manager - Scottsboro, Alabama
2007
A. O.K. I noticed you are using 4/0 paper, we don't use that number here. Could it be proportionally around 2000 according to the depth of lines left? How close are you after that paper to a reflecting surface? Are you getting scattered pits or are they throughout the surface. In what stage do they appear or when do they become visible? Sometimes, the polishing compounds tend to produce pits due to excessive pressure exerted trying to clean previous sandpaper lines, but if you look carefully you can trace them back and find out if they were already there or you caused them. Something else, can you get diamond paste 15 and some hair brushes? Give'em a chance at moderate speed.
Guillermo MarrufoMonterrey, NL, Mexico
2007
A. Mirror polish finish as you described is not a problem in sheet form (4'x 10') up to 11 GA or 3.0 mm thick. Ra of 1 microinch even in 11 GA material has not been a problem. However, the raw material substrate must be from the best steel mills in the world to avoid problems with pits and pinholes.
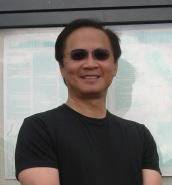
Michael Liu Taylor
specialty stainless steel distributor - Dallas, Texas
2007
A. Mass finishing equipment can work and produce mirror finishes on parts less than 12" square very effectively and efficiently; however, over that size it becomes a little more difficult. I'm not sure you can find enough specific info about this on any website.

AF Kenton
retired business owner - Hatboro, Pennsylvania
2007
Q. AF the size of the part in the 3rd post. They are roughly four foot square but have an odd shape. They have a window opening in them making them around three inches wide from the outside of the part to the inside cut out.
Thanks for the help!
Quality Manager - Scottsboro, Alabama
2007
A. Sorry about my confusion on size. Based upon that info, I would not recommend mass finishing. Much too expensive and questionable results.

AF Kenton
retired business owner - Hatboro, Pennsylvania
2007
Q. Lawrence:
I'm having the same problem (more or less). The orange peel is cause by a combination of things. Mechanical grinding of the surface causes a "Bielby Layer" to form. If this layer forms before you have removed all the scratches one will try to remove the scratches with a grit or sandpaper that is not coarse enough the remove this layer. The resulting heat and friction just "smears" the Bielby layer causing the orange peel.
I am also looking for a way to avoid or quickly remove this layer. Electropolishing is not an option as my parts are 7 feet tall by 12 feet long by 4 feet deep.
Is there an electrostatic solution to this problem?
- Oakland, California
2007
2007
A. Dear Lawrence,
Late response though I hope it reaches you.
I feel that 12 gauge is not such an issue. 301 is also not an issue.
Please note the following;
1. Is it Hot Rolled or Cold Rolled
2. What is the finish of the plate before you start any activity. It is a must to determine where you start!
3. Mirror finish on SS should be achieved at around 3000 Grit (If you want it absolutely impeccable) I know of people stopping at 2000 and being happy. But any thing below that would be really not a great idea.
4. Did you ever explore using Engineered abrasives. If not you must. Any problems with that, ask me.
5. What is the machine you use and the type of abrasive you use? Explain to me please.
6. Are you using any lubrication or cooling media, if yes I would also like to understand that too.
Lawrence, I think Mirrorization of Stainless Steel is not at all Difficult, just that it is Different.
If you have any query, it will be my pleasure to assist you.
Ciao!
- New Delhi, India
2007
I want to thank everyone for the help and advice you have given me. We are now able to produce the mirror polished finish that we were trying to obtain. I want to share the information that we found on our quest in hopes that it will help others obtain their goals.
1) One of the biggest things we learned is not to rush through the polishing steps. If you read the previous post you will hear this over and over. Follow their advice they are right!
2) Make sure every line from the previous operation has been taken out before you continue to the next step. If you go 90 degrees to the last operation you will be able to see the lines you have not taken out yet.
3) Don't put too much pressure on your tool. We found that too much downward pressure is counter productive. It does not get the lines out faster! It actually creates larger grain lines forcing you to back up a polishing step or two just to get the grain out (It also wears belt out prematurely).
We invited 3M to come out to our facility and they recommended a product line called the Trizact series. This is by far the best sanding belts we have found to date. We put it on a hand drum sander with an air pneumatic drum (Dynisher).
We are also using Nushine II made by Nuvite for the final polishing.
Here is our sequence:
1) Sand out all defects with a 90 deg hand sander using 180 grit disk pad.
2) Go over entire part with Trizact A45 using hand drum sander.
3) Go over entire part with Trizact A16 using hand drum sander. (90 deg to last cut)
4) Go over entire part with Trizact A6 using hand drum sander. (90 deg to last cut)
5) Go over entire part with Nuvite F9 polishing compound. (Make sure ALL defects are out.)
6) Finally go over entire part with Nuvite Grade A polishing compound.
That's It!
Thanks again for all the help.
Quality Manager - Scottsboro, Alabama
![]() |
Q. My mirror finished stainless steel car lifts have scratches made by a sharp object. How do I clean and remove the scratches? L.S.Pinto- Mumbai, Maharashtra, India December 5, 2008 Q. I have a flat sheet of stainless steel. I would like to bring the mirror look out in it. hobbyist - Alabama March 14, 2009 Q. Hi everyone, - Ho Chi Minh City June 9, 2009 Hi, L.S., Kenneth, and Thanm. I hope you are well! ![]() Ted Mooney, P.E. Striving to live Aloha (Ted is available for instant or longterm help) finishing.com - Pine Beach, New Jersey June 26, 2009 |
(You're on the 1st page of this topic) Next page >
Q, A, or Comment on THIS thread -or- Start a NEW Thread