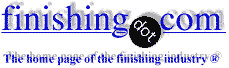
-----
ASTM A193 Anchor Bolts hot dip galvanized
Q. Can you cement over the base of a galvanised steel shed?
JOHN MC CLURE- DUMFRIES UK
June 17, 2020
A. Hi John. We appended your inquiry to a thread which discusses the several aspects of this. In general the galvanizing can react with the alkalinity of the cement, causing hydrogen bubbles which can be problematical for some applications. But if you're just saying you want to pour some casual concrete and it will run into old galvanized siding, I'd say go for it :-)
Regards,
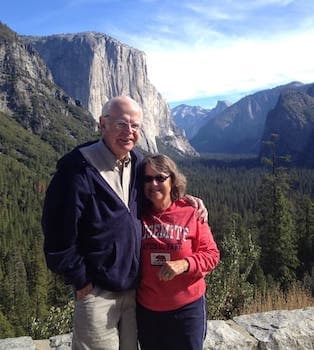
Ted Mooney, P.E. RET
Striving to live Aloha
(Ted can offer longterm or instant help)
finishing.com - Pine Beach, New Jersey
June 2020
A. As an amateur I can only report my observations. 15 years ago I placed 1 inch galvanized pipe in concrete for railings. While removing the pipe I observed no corrosion of the pipe at depth in the concrete but around the surface of the concrete significant deterioration in the pipe metal.
Barry Ronnesethamateur - Guatemala
November 28, 2021
Thanks Barry. Re-bar is often galvanized and lasts well. Concrete is dry and should not attack galvanizing, but at the wet interface on the surface it will.
Luck & Regards,
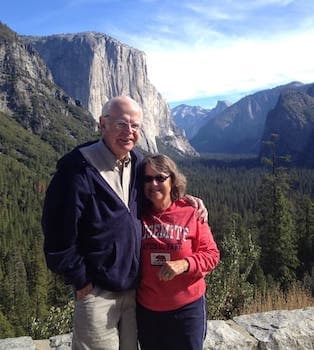
Ted Mooney, P.E. RET
Striving to live Aloha
(Ted can offer longterm or instant help)
finishing.com - Pine Beach, New Jersey
November 2021
⇩ Related postings, oldest first ⇩
Q. My company builds noise-resistant enclosures mostly for power generation. These enclosures have steel frames, and are frequently galvanized. The columns found on concrete, with non-shrinking grout in contact with the underside of base plates. Our engineers are concerned that the grout will react with the galvanizing, causing expansive products of corrosion able to disrupt the anchoring system.
So far, we have been masking the underside of base plates prior to galvanizing, and stripping the masking afterwards so that only ungalvanized steel is in contact with the grout. With so many columns, this is time consuming and expensive.
Can someone suggest something simpler, perhaps an easy to apply one coat barrier system that will prevent these corrosion products forming. The service condition is inside a building, but for thirty years life.
noise management - Calgary, Alberta, Canada
2002
by Stephen Yeomans
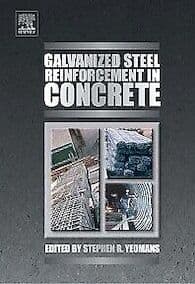
on eBay or Amazon
or AbeBooks
(affil link)
? I guess this is a subject I'm ignorant of. I have only a sketchy mental image here, but the .001" or less galvanized coating is expected to grow so much as it corrodes that it will knock the building out of alignment or snap the column's anchor bolts?
Doesn't sound reasonable; please explain to me what the issue is, someone. Thanks!
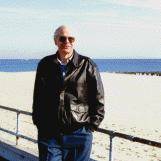
Ted Mooney, P.E.
Striving to live Aloha
(Ted can offer longterm or instant help)
finishing.com - Pine Beach, New Jersey
Q. Point well taken. You need more information.
The problem is with the grout. The expansive products are small but real, and the grout is thin. Any expansion can jack against the A bolts and stiff base plate, so there is a high compressive stress in the grout, and tensile bursting stresses at the edges. Grout has no virtually no tensile strength, so we get progressive spalling, and over time, it simply empties out from under the plate.
Regardless of the age of the structure, both grout and galvanizing remain chemically active, so the problem never goes away. Hence the need for a durable barrier.
noise management - Calgary, Alberta, Canada
2002
A. I may be barking up the wrong tree here so first I will state what I think the condition is. The grout is put down, the column put on top and them the whole lot bolted together. In its service life it never moves or gets taken apart. The zinc in contact with the grout pushes the grout out and this is the problem. The zinc must not contact the grout.
Would a simple coat of paint on the column base do the trick? It is in a sealed environment so it should not suffer the same problems as paint exposed to the elements.
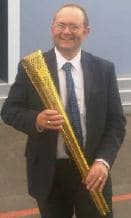
Martin Trigg-Hogarth
surface treatment shop - Stroud, Glos, England
2002
A. We know that Zinc reacts with the formation of voluminous white corrosion products, which are a combination of various insoluble zinc compounds. It has been observed that alloys of zinc, like Zinc/Nickel will form dramatically fewer voluminous byproducts during corrosion. The higher the nickel percentage is (8-12%), the slower the reaction with corrosive environments, and the lower the volume of insoluble corrosion byproducts on the plated coating. The slower reaction means longer life of the functional part that is plated.
This is only a suggestion for something to look at. My suggestion would be a plated coating 0.0005 inches thick with an iridescent passivate on top. Tests should be run to see if this helps answer your question in the building industry.
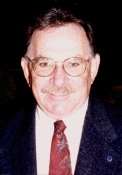

Ed Budman [dec]
- Pennsylvania
With deep sadness we advise that our good friend Ed passed away Nov. 24, 2018
2002
Multiple threads merged: please forgive chronology errors and repetition 🙂
Admixture to prevent fresh cement reacting with galvanized rebar and anchors to form hydrogen gas?
by Stephen Yeomans
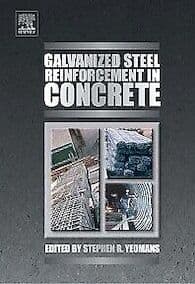
on eBay or Amazon
or AbeBooks
(affil link)
Q. We are structural engineers specifying galvanized reinforcing steel for reinforced concrete that has low cover thickness. Fresh cement in contact with galvanizing generates H2 gas at the interface by reaction of Zn with OH in the cement. A concentration of gas bubbles formed in cement paste on the interface decreases the bond strength of concrete with reinforcing steel. The phenomenon is well known and the antidote is an admixture that either inhibits the reaction or dissipates the gas bubbles. Does anyone know what it is or where to get it?
Leslie Peer- Vancouver, BC, Canada
2003
Q. Does Galvanizing of anchor bolts affect the bond stress between the anchor bolt & concrete?
P.K.Raghuram- Chennai, Tamilnadu, India
2006
A. The admix at the mixer is chromium trioxide. It is added to the water before depositing into mixer @ dosage of about 300 parts per million by weight of mortar's or concrete's mix water. However, a substantially smaller proportion (100 parts per million) may be sufficient to prevent hydrogen evolution. All that works out to approx. 5 to 13 grams or a level teaspoon of chromium trioxide powder for every 100 pounds of mix water.
Tom Rapenske- Richmond, Kentucky, USA
July 16, 2008
----
Ed. note: Tom also reminds the readers that chromium trioxide (hexavalent chromium) is a dangerous chemical and a potential environmental issue; you must be thoroughly familiar with these issues before attempting to work with it like this.
Multiple threads merged: please forgive chronology errors and repetition 🙂
Galvanised posts, partially embedded in concrete, are corroding
Q. As a concretor who places house floor slabs around galvanised steel posts and hot dipped posts I am interested to hear opinions about corrosion rates of those posts. Is it normal to see serious corrosion after just 5 years, on posts going into pad footings and a concrete slab? Are there any standard guidelines for reducing corrosion?
Thank you in advance for your time,
concretor/landscaper - Brisbane, Queensland, Australia
2003
by Stephen Yeomans
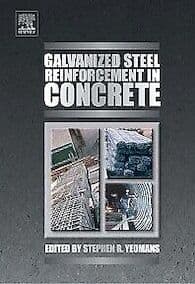
on eBay or Amazon
or AbeBooks
(affil link)
A. Watch out for salt in sand in concrete. Galv steel in concrete is generally ok though.
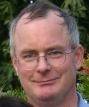
Geoff Crowley
Crithwood Ltd.
Westfield, Scotland, UK
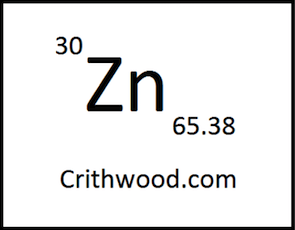
2003
Q. As a home handy man embarking on pergola project using galvanised posts, my question is:- Can galv posts be totally embedded in concrete or do they also have to be sitting on a bed of gravel for drainage
Greg (DYI Project Manager)
dyi - Australia
April 4, 2009
A. Hi Greg. I guess I'd say that if water can get in the top of the post, the bottom has to be open. If water cannot get into the top, the bottom doesn't need to be able to drain :-)
Regards,
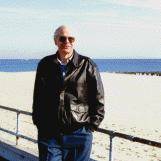
Ted Mooney, P.E.
Striving to live Aloha
(Ted can offer longterm or instant help)
finishing.com - Pine Beach, New Jersey
Q. We require anchor bolts J-type (dia 42 mm, 36 mm, 20 mm acc. to ASTM 307 Gr. C) to be fixed in CONCRETE FOUNDATIONS carrying a load of 325 tons. Vendor is asking whether the bolts be hot zinc plated or not. Please give your expert opinion on the following:
1. Would it be beneficial to have zinc-plating on the anchor bolts?
2. Would it effect the bond strength of anchor bolts with CONCRETE? If yes, then to what extent?
3. Is there any other purpose of hot zinc-plating else to offer corrosion resistance?
Early response will be highly appreciated.
fertilizer company - Sadikabad, Punjab, Pakistan
2006
----
Ed. note: We appended your posting to a thread where Tom R has suggested a chromium trioxide admixture in the concrete, Ashfaq. You only get 'expert opinion' by retaining a consultant who will offer it, but the tone of Tom's posting seemed to imply that this admixture stuff is pretty much standard procedure.
Q. Is it acceptable to hot dip galvanize ASTM A193 Gr. B7 material (threaded rod 3" size) and to be used for anchor bolts (embedded in concrete)?
Yes or no associated with the specific reasons if you please.
buyer - Yanbu, KSA
2007
A. Technically, ASTM A193 materials are for high temperature applications where zinc coating may be detrimental (cause embrittlement). But, this isn't a high temperature application, and is near the Red Sea, so extra corrosion protection via galvanizing may be worthwhile. Galvanizing of Grade B7 should be OK (provided the galvanizer doesn't excessively acid pickle!). As the galvanizing temperature is about 200 °F below the tempering temperature of Grade B7, no softening problem.
For use at ambient temperatures, an alternative threaded rod equivalent in strength to the expensive B7 (AISI 4140) is ASTM A354, Grade BC. Other mechanical properties: same elongation (16%), nearly the same reduction in area (45% vs. 50% for B7). Use heavy hex nuts per ASTM A563, Grade C or DH. Grade C has thin zinc coating, DH has thicker zinc and threads tapped slightly oversize after coating to accommodate similarly coated rod. Either ASTM A153
, Class C (hot dip galvanizing) or ASTM B695, Class 50 (mechanically plated zinc) may be specified for coating. Per ASTM A354, the threaded components (bolts or rod & nuts) should be coated and shipped together.
- Goleta, California

Rest in peace, Ken. Thank you for your hard work which the finishing world, and we at finishing.com, continue to benefit from.
2007
Multiple threads merged: please forgive chronology errors and repetition 🙂
Chromate conversion coating on a cement mortar's hot dipped galv. reinforcement?
February 19, 2008I'm a farmer who has mistakenly built a faulty ferrocement (several layers of small diameter galv steel mesh encapsulated in a thin cementitious mortar) water tank. I'm told that encapsulating a hot dipped galvanized wire reinforcement in a cementitious matrix has an adverse chemical reaction between the zinc and calcium hydroxide, producing adverse hydrogen gas and/or calcium zincate that prevents the necessary good bond between the steel and the hardened cement paste. Seems some galv. wire or stucco-type mesh has a chromate quench or dip applied at the galv. plant to successfully 'passivate' the zinc and prevent the problem, but it also appears that lots of wire mesh used in ferrocement technology does not (mine!). I'm also belatedly told that most expanded metal stucco meshes will likely have that chromate conversion coating, but other wire reinforcement will likely not.
How can I find more info on this matter and determine if the galv wire (i.e., 1/2" hardware cloth, 1" chicken wire', expanded metal stucco mesh) I've encapsulated has been passivated? Is there an exact ASTM # I should be looking for to guarantee application of the chromate coating? It is very difficult to get any info at all from galv wire mesh suppliers or manufacturers about this detail, most just shrug their shoulders or ignore small-potatoes me.
A rumored, just-as-good, equivalent to a chromate conversion coating is to passivate the wire mesh's zinc by exposing it to 6 weeks of sun and rain so that the zinc oxidizes and dulls, but that surely didn't work for me. Tame or wild opinions as to its potential to successfully passivate under cementitious (alkaline) encapsulation?
homeowner using HD products in cementitious composites - Richmond, Kentucky
A. This sounds like an interesting problem, but no doubt worrying for you.
I'm surprised though. A lot of steel reinforcing is galvanized. Mostly for concrete work where there's high corrosive chance like seaside. Thousands of tonnes of rebar is galvanized. Some passivated, but not all. Not heard of the trouble you mentioned.
You didn't say if this has manifested itself as a real problem or merely a theoretical one.
If real, what symptoms did you see?
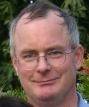
Geoff Crowley
Crithwood Ltd.
Westfield, Scotland, UK
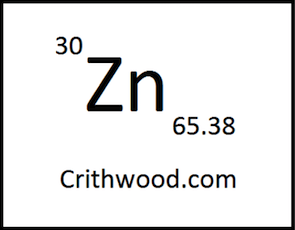
February 25, 2008
February 28, 2008
Geoff,
I have a real, bonafide, failed tank, 'internally' structurally flawed, not theoretical. I have a small sampling of excellent photos at a photo sharing website for you to see various photos of --
1.)some of the tank's actual members amidst the construction process as the problem was noticed and
2.)multiple test samples set up to simulate tank's bonding problem.
At the approx. 1/16" deep interface of the zinc and the mortar you will can easily notice a 'crud' of unhydrated cement paste/mortar that could be washed away with water and a light scrubbing with a toothbrush. But since I'm asked not to post website addresses here you'll have to give me some other solution within finishing's discussion system that a greenhorn could accomplish? These photos will probably prove interesting.
https://www.flickr.com/photos/14073523@N05/?saved=1"
farmer, tank builder - Richmond, Kentucky
![]() |
February 28, 2008 Yes we generally discourage most links, Tom. They almost always break in short order and hurt our site's usefulness as an enduring reference work. For example, Yahoo Photos closed recently and in place of 2 billion photos, there are now at least 2 billion broken links on the internet from just that one source. Some months from now people may be trying to learn from this thread, only to see broken links instead of your photos. Although we've linked as you requested, we greatly prefer that readers email photographs for posting here to insure that interested future readers will see the photos we're speaking of not broken links. Thanks for your understanding! ![]() Ted Mooney, P.E. Striving to live Aloha (Ted can offer longterm or instant help) finishing.com - Pine Beach, New Jersey ---- Ed. note 2009: Sorry readers, but as predicted the link to the photos is already broken :-( |
March 20, 2013
Q. Item : Yellow Colored Stud Anchors Bolt
(1) Coated material information : MSDS
(Chrome %, others %)
(2) Coated thickness : how many micron
(3) Method of coating
(4) Coating status : 1 layer or 2 layers
- Jubail, Saudi Arabia
A. Hi, cousin Noufal. I apologize if we are having language difficulties, but your posting has neither verbs nor personal pronouns, so I don't know what you want :-(
Are you asking readers to guess the finish on anchor bolts that you have located, based solely on their color? Or are you asking someone to write a finishing specification & process for anchor bolts for you, complete with MSDS?
Many finishes are probably available for anchor bolts. One such finish that would be yellow would probably be zinc plating of 0.005" thick or so with a yellow trivalent chromium conversion coating. Am I getting close to understanding? Thanks.
Regards,
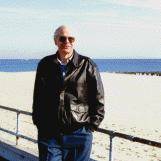
Ted Mooney, P.E.
Striving to live Aloha
(Ted can offer longterm or instant help)
finishing.com - Pine Beach, New Jersey
March 20, 2013
Plated Nelson studs are corroding. Will hot dip galvanizing solve it?
Q. Can anyone specify do we have Hot dip galvanized studs (NELSON); if not what is the best procedure for studs to galvanize as electroplating wasn't able to protect the studs from corrosion
Syed Osman- Riyadh, Saudi Arabia
December 16, 2015
A. Hi Syed. Nelson is just a brand name, so I'm not 100% sure whether you are thinking of a stud that is embedded in concrete, or is part of an automobile that gets electrocoated and painted, or what. But since you say that zinc plated ones get corroded, I assume that further painting/coating is not done.
Hot dip galvanized studs will be more corrosion resistant than zinc electroplated studs because the zinc coating will be several times thicker. But galvanizing may or may not be enough, and it may not be possible for small studs. If you can explain the application, people may be able to offer a better prediction or a better solution. Thanks.
Regards,
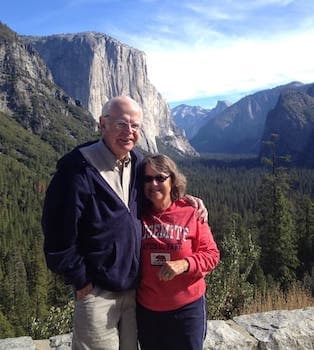
Ted Mooney, P.E. RET
Striving to live Aloha
(Ted can offer longterm or instant help)
finishing.com - Pine Beach, New Jersey
December 2015
A. I believe (as you have not mentioned the grade, type) you must be talking about B7 Studs and 2 H nuts used in petroleum refinery. Ideally the studs and nuts should be HDG. In case of rework- Electroplated studs are not suited for HDG as they need deeper cut for drainage of zinc.
Nitesh Kumar Agarwal- Kolkata, India
May 20, 2016

Q, A, or Comment on THIS thread -or- Start a NEW Thread