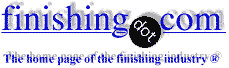
-----
Is there a maximum thickness limitation for Zinc coating per ASTM B633?
Q. Hi friends,
I happened upon a problem: our product (steel) needs a finishing process: Zinc, clear chromate per ASTM B633-85, SCI, TYPE3, COLORLESS. This standard requires a Zinc thickness at least 5 µm (0.0002"), but no top limitation, our supplier made it with thickness 0.08",
Who can help me on this case whether it is reasonable? If not, how to negotiate with supplier, and how to make the tolerance for their reference?
Thank you with all my heart!
teradyne - China
2007
A. That is very reasonable unless there is a "fit" problem for the final assembly. To get at least 5, you have to exceed it by a rational factor or risk more QC inspections and more rejections. More is better until it is too much for your purpose.
You have the option of specifying the max amount in your Purchase Order.
If I do your work, I will charge a lot more for 5 to 6 than 5 to 8. Above 8, it is costing me money, so I do not want to exceed that if at all possible.
- Navarre, Florida
2007
Hi Helly. James' answer is excellent, but there is a typo in your question. You are certainly not receiving plating of 0.08", as that is an unheard of zinc plating thickness. Even a hundred times thinner at 0.0008" would be quite heavy for zinc electroplating. You probably mean, as James assumed, 8 µm?
Regards,
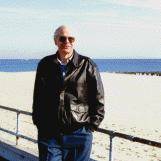
Ted Mooney, P.E.
Striving to live Aloha
(Ted can offer longterm or instant help)
finishing.com - Pine Beach, New Jersey
Zinc Plate / ASTM B633 thicknesses tolerance
Q. Hello Guys,
I wanted to know if there is a tolerance for the ASTM B633 Thickness classes (SC1 5µm, SC2 8µm, SC3 12µm, SC4 25µm). One of my customers is asking me to issue a certificate of compliance for parts he requested to be 50.8 microns of thickness, this clearly exceeds the 25 microns on SC4. So, I just wanted to make sure that he is correct? assuming that the standard says "Thickness, MIN (minimum) µm" .
Thank you all!
- San Diego, California, United States
October 23, 2014
A. Hi Manny. James Watts has already answered a very similar question; it does not sound like a problem. But lest I be misreading your question, you certainly cannot issue a certificate of compliance to a spec unless you have a copy in your possession because there is more to compliance than thickness. Good luck.
Regards,
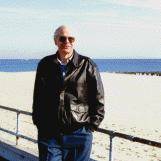
Ted Mooney, P.E.
Striving to live Aloha
(Ted can offer longterm or instant help)
finishing.com - Pine Beach, New Jersey
October 2014
October 24, 2014
Q. Hi Ted,
Yeah, I guess my question was misunderstood. What I really wanted to know is that if I have a customer that requires one of the ASTM B633 thickness classes, and let's just assume we are talking about SC2 8 microns, what thickness tolerance do I have?
I would assume that 8 microns is my minimum, or else it would be considered an SC1 right? And then my top tolerance would be the next thickness class which is SC3 right? So, basically anything between 8 microns and 12 microns is where I would need to be in order to comply with my customer's spec.
So, based on the above, what happens with a 25 micron spec requirement? What would be my top limitation? 30, 40, 60 microns? I honestly have never seen anything run at 50 microns (in zinc plating) or for that matter anything above 25 microns (SC4) and that isn't very common either.
My question was referring more to the type of tolerance you see in regular drawings e.g. ± lets say 2.5 microns.
if there is no top limitation why don't I just have 1 thickness class starting at 5 microns?
Perhaps there is another standard that regulates thickness classes above 25 microns?
I apologize if this shows my lack of experience -- it's just that I truly want to understand how this works.
Thanks!!
- chula vista, California
A. Hi again, Manny. Zinc plating is often done for corrosion resistance, which tends to be proportional to plating thickness; so it is common to specify a minimum plating thickness. There is no "generally understood tolerance" on plating thickness. My pdf of ASTM B633 got corrupted and my books of standards are in storage, so I can't tell you what ASTM B633 says -- you'll have to read your copy and tell me instead -- but I'm confident there is no implication that the maximum thickness of one classification cannot exceed the minimum thickness for the next. Often, the thickness of zinc plating will be specified something like "x µm minimum thickness on all surfaces touchable by a 3/4"dia. ball, and all non-touchable visible surfaces covered" -- but it's all only what the customer specifies.
We frequently tell students who post on these pages that we're happy to help them with the answers but we simply can't help them with the questions. That is, if they don't understand what the teacher wants, clarification has to come from the teacher, not with a guess from us. I think we're in a similar position here :-)
Your customer can specify anything he chooses, irrespective of ASTM B633 or any other standard, such as "per ASTM B633 except minimum thickness of 50.8 µm", and your job is to comply or decline to quote. The designer seems to wants 50.8 µm of zinc plating somewhere, somehow, but neither you nor the buyer seem to quite know what he means by that. ASTM B633 can't clarify it, and reders can't clarify it :-(
50.8 µm is outrageously heavy for zinc electroplating and I personally think the designer should probably talk to a metal finishing consultant about whether mechanical plating, hot dip galvanizing, or dip-spin zinc rich coatings might be a more appropriate finish for his needs, rather than you and the buyer scratching your heads worrying about maximum allowable thickness when the specified minimum thickness is already probably impractical :-)
Best of luck.
Regards,
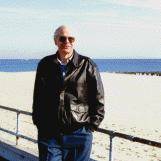
Ted Mooney, P.E.
Striving to live Aloha
(Ted can offer longterm or instant help)
finishing.com - Pine Beach, New Jersey
October 2014
Q. What is the most cost effective way to treat the surface of a 10 feet long pre-galvanized electrical metallic tube, to protect the pre-galvanized zinc coating of 60 microns?
And is it possible to drop the pre-galvanized steel sheet and electroplate/mechanically plate un-galvanized steel sheet to produce the same zinc thickness?
El Delta El Masreya - Cairo Egypt
January 20, 2019
A. Hi cousin Amed. This is your second question on the same theme of post treating pre-galvanized EMT (you also posted on thread 55350), but we don't seem to be getting to what is actually going on ... because I don't understand why you keep talking about post-treating pre-galvanized material you have bought, when I have never heard of such a thing (I'm not saying it can't be done or has never ever been done, but I spent over 50 years in this industry and never saw it, so it is very far from routine).
Whatever chromate post-treatment is required is supposed to be done by the galvanizer. Sorry, 60 microns is probably not a practical thickness for electroplating and to my knowledge your can't mechanically plate sheets of steel. Can we make a guess that the material is getting white rust and the seller is trying to convince you that it was your job to prevent this via a post-treatment? I don't think it is.
If you are manufacturing the EMT conduit yourself in-house from sheet, you can use bare steel and then galvanize or electroplate it and chromate conversion coat it after fabrication, but you will not get zinc on the inside by electroplating, and as mentioned, I don't think you'll get 60 microns.
Regards,
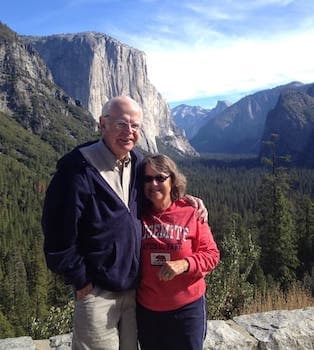
Ted Mooney, P.E. RET
Striving to live Aloha
(Ted can offer longterm or instant help)
finishing.com - Pine Beach, New Jersey
January 2019
Q. Thank you so much for this answer Mr.Ted, your prompt reply and urge to help with your unquestionable knowledge in this industry has inspired me a lot actually. I'be read a lot of threads and learnt a lot from your answers.
I've digested your answers and I'd like to describe the logistics situation with raw material (pre-galvanized steel sheets). The Chemical composition and mechanical properties of the mild low carbon pre-galvanized steel sheet we require isn't available in the Egyptian market most of the time, therefore, we tend to make a bit of importing from China, and use local steel sheets with good credit points. Therefore, many times it has happened the sheets make it to the factory with no treatment (I have orders and can't wait for imports to make it, so I tend to be obliged. Therefore, the questions would be:
1. If we construct an in-house treatment tub (Trivalent chromium compound, silane and acids) and driers used for post treatment; would it affect the end product negatively? or would it protect the welded area where the sheet has faced heat conditions and a new zinc layer automatically gun sprayed after welding (which has no protection) (I understood it's not common practice but I thought I'd give this question a shot).
2. What would the Best pre-galvanized steel sheet (chemical/mechanical/testing) specs be for EMT Conduits 1/2", 3/4", 1", 1.5"?
3. I produce Zinc die cast fittings (for tubes) made out of zinc zamac 3 having at least 99.6% zinc content. I need a post treatment to keep it shiny and protected as are having a hard time with fittings getting a lot darker than they should.
Again Mr.Ted it a pleasure to be in this dialogue with you; I greatly appreciate your kind support and I feel pleased to have exchanged words with you. Much respect.
Delta - Cairo Egypt
January 21, 2019
A. Thanks for the kind words, Amed. I now understand what you want to do and why. Sorry, though, I don't have actual experience in the manufacturing of EMT from pre-galvanized sheet, so I would not be familiar with the usual thickness standards and pre-galv specs, nor the relevant ASTM, ISO, UL, CSI, etc. standards for the product line.
But the thing is, metal finishers (especially high production shops) look for robust processes, not processes which propose to improve the corrosion resistance by some vague amount on some variable percentage of their production. For example, a process which will work if the parts happen to be clean but which will fail if the parts happen to be dirty isn't of much value. A process which will work on the existing zinc coating if it's relatively fresh, and in the area far from the weld zone, but not near the weld zone and not if the zinc coating has aged for 2 months isn't very useful to you.
That's the problem with trying to install a simple chromate conversion line: Sure, it might help sometimes; some of your EMT and some of your diecast fittings may be good (but some will not be). The correct answer is quite a bit more complex and involves installing a zinc electroplating plus chromate conversion coating line which incorporates alkaline electrocleaning, acid activation, zinc electroplating, chromate conversion coating, and drying.
Before planning an installation, I suggest that you do some development work, either with a local electroplating shop or a plating process supplier, and examine the quality of work that results from trying to just chromate conversion coat & silane treat the EMT vs. the results from alkaline cleaning, acid activating, zinc electroplating, and chromate conversion coating & silane treating it. Input from readers with EMT experience is welcomed.
Regards,
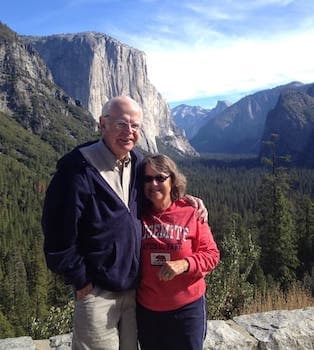
Ted Mooney, P.E. RET
Striving to live Aloha
(Ted can offer longterm or instant help)
finishing.com - Pine Beach, New Jersey
January 2019
Q, A, or Comment on THIS thread -or- Start a NEW Thread