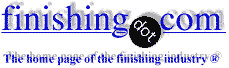
-----
Black/Brown stains on electroless nickel plating

Q. Hi all, my company does Mid P EN with corrode steel material, we sometimes encounter brown stains near the hole. After checking conductivity and flow rate of DI water at post-treatment, all seem to be ok. I cannot pinpoint the root cause of this reject. When this type of reject happens, it usually comes out continuously. Can a high Fe content in bath cause this issue? If there is delay in pretreatment area especially at HCl area, can it cause this type of reject to happen, or worse contaminate the EN bath?
Ikhmal Ezzany- Melaka Melaka
December 24, 2021
⇩ Related postings, oldest first ⇩
1999
Q. In our nickel plating, because we don't want to plate nickel on glass, (the part base is Kovar), we add more stabilizer, and control the Lead at 0.4 ppm-0.6 ppm, recently we always find brown stain on the part after nickel plating, can not remove by washing ... who can tell me what is the problem? thanks
Cindy XuA. I'll bet it's rust, Ms. Xu, and that your electroless nickel is not thick enough and your drying/displacement system is not functioning adequately. Kovar is not rust resistant.
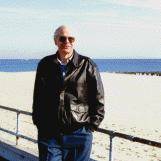
Ted Mooney, P.E.
Striving to live Aloha
(Ted can offer longterm or instant help)
finishing.com - Pine Beach, New Jersey
1999
Q. I am looking for information on Precipitation Hardening of Electroless Nickel per AMS2404. I understand the theory of the process but need some practical information. First, is this something that the plater takes care of or does the plater generally sub-contract to a heat treater? Secondly, the optimum temperature and time for this post-plate procedure is generally 650 °F for two hours in a controlled atmosphere. Can one heat at 500-550 °F for 10-12 hours and achieve adequate results? Third, will the EN finish discolor at the 500-550 °F temperature in ambient atmospheres?
David Black- Wrentham, Massachusetts
2000
A. David,
You can heat treat your parts at 590 °F. for 3 hours and get the hardness you need 60Rc +. the part may come with light brown stains on them if not covered with fiber glass cloth. All platers should be able to do this heat treating in house.
Tom Mason- Carol Stream, Illinois
2000
Multiple threads merged: please forgive chronology errors and repetition 🙂
Q. Our company experiences a significant increase of material defects due to brown stain. We always thought that this is caused by high conductivity on water rinses. We maintain the conductivity of our rinses to less than 1 uS/cm. Still brown stain persists. Would there be any other causes of this problem?
Thanks.
Plating company - Cavite, Philippines
2006
A. Suggest to:
1. Check if Ni bath metallic contamination such as Cu is high. If so, run dummy at 2-5 ASF for several hours;
2. Measure nickel thickness (too low?) and porosity (too high?)
3. Verify whether plating parts are completely dried after plating;
4. Storage condition such as temp and relative humidity is important also
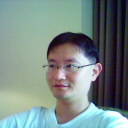
David Shiu
- Singapore
2006
A. Brown spots causes are existence of Fe3+; mechanical contaminations; overdosage of brightener/leveling agent; or pH value is too high. Best regards,
Ada Garber- Istanbul, Yurkey
2006
Q. We are experiencing a problem with brown staining/ tarnishing appearing a few hours later on radio components that we are electroless nickel plating . The components are machined from solid aluminium billets and are electroless coated for one hour using a high phosphorous solution. After plating they are rinsed in de-ionised water and then blown with compressed air to clear any blind holes , corners, etc.Does anyone have any advise for us ? We cannot use any de - watering or oil based coatings as some components are then powder coated afterwards .
MARK WRIGHTelectroplating - DURBAN, KZN, SOUTH AFRICA
2006
A. Hello Mark,
Can you pinpoint if the staining is coming from blind holes or corners on the part? If so, an air agitated DI rinse may be in order. I like to use a 2 to 3 counterflow rinse system with the last rinse being air agitated. As you probably know the last DI rinse should be the cleanest. Good Luck!
Process Engineer - Syracuse, New York
2006
A. I THINK FINAL DI WATER RINSE SHOULD BE HOT TEMP. 60-70 °C.
IMMERSION TIME 2 TO 3 minutes WITH AIR AGITATION.
THEN DRY HOT AIR, OIL-FREE
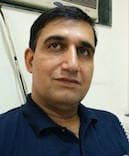
Ajay Raina
Ludhiana, Punjab, India
2006
A. Dear,
The quality of rinse water can cause brown stains. First make sure you use DM water for rinse. Second check silicate in rinse water. There are chemicals and color disk to check silicate in water. If you exceed 1 ppm of silicate, you are likely to get stains. A regeneration of DM plant will bring down silicate contamination. Check silicate and try. Best wishes.
plating shop employee - Gandhinagar, India
2006
Brown Stains on E-less Ni/Au plating on Silicon Wafer
Q. Good Day,
We are using an Electroless Ni/Au plating on Al of a silicon wafer for microelectronics application (we pre treat the Al surface by etching away the oxides and cover it with Zincates, then Ni, then Au). Recently we encountered brown spots on the pad surface. EDS spectrum shows highly significant levels of 02 (Ni Oxide?). While Au is quite low on the surface with brown stains than those without.nPlus significant high level of F (where does this come from?).
Can you share some expeience, comment on below findings?
thanks a lot.
semiconductors - Cabuyao Laguna Philippines
2007
A. Oscar,
I can only assume your electroless gold is a borohydride type. I have found that frequent bath analysis is necessary, prior to each running of parts. These baths are compatible with silicon, but not polyethylene. You also have to be very careful with your water source when you replenish the volume level, and the final rinse. City water should never be used in either case. Carbon polished DI water is a big help.
Because you are going over Ni, some Ni ions are lost to the bath in the reduction process. If the nickel concentration is too high in the bath, it will become unstable. This is probably why you suspect Ni oxide on the surface. Unless you are using complexing agents in the bath(which I won't get into), it may have a rather short life. You could perform a lab test with a liter of the gold solution to make sure you are getting the thickness of gold per minute that you should. If you don't get the thickness and the bath analysis is good, do a titration for Ni. I bet you find the concentration is too high for the bath. Good Luck!
Process Engineer - Syracuse, NY USA
2007
Black stains formation on electroless nickel plating
Black stains formation on electroless nickel (MP) plated surface after two to three days.
Giving good pre-treatment and post treatment. After plating it shows good bright finish and with in one or two days it started to form the stains. Because of this we are facing a lot of problems. Please help us
plating shop employee - Faridabad,Hariana
December 15, 2008
January 15, 2009
A. Hello Mr Mehra,
Looks like your EN bath has metallic or organic contamination somewhere. You need to find out its source and eliminate it. The contamination may also be from leaded steel parts; assuming all other process parameters are adhered to and you ae using a good process supplier.
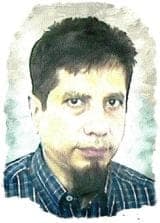
Khozem Vahaanwala
Saify Ind

Bengaluru, Karnataka, India
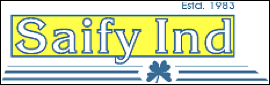
A. Aluminum contamination will start out as a dull then gray then a dark gray/black EN coating. Lead will normally stop the plating.
James Watts- Navarre, Florida
January 16, 2009
Q. We are having problem regarding rust in our plating on Fe material, we already increased our concentration on acids and plating thickness but still rust exists. What are the countermeasures do you suggest we should implement? Thank you.
Mie LeoverasPlating Company - Cavite, Philippines
August 11, 2009
August 12, 2009
Hi, Mie. Are you from the same plating company in Cavite as JM Puguan, and is this a continuation of the same question? Several suggestions were already made. Can you frame your question in terms of those previous suggestions? Thanks!
Regards,
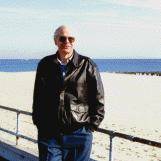
Ted Mooney, P.E.
Striving to live Aloha
(Ted can offer longterm or instant help)
finishing.com - Pine Beach, New Jersey
Q. Hi.
Actually my company produces the product from electroless nickel plating.
Currently my company also has same problem about the stain issue. Until now we also cannot solve this problem. We already do adjustment at rinsing tank, but still have stains. Can you advise me of the solution to avoid this problem.
- Selangor, Malaysia
March 28, 2013
Hi cousin Nur.
Apologies, but nobody has replied to you yet. But if you have "the same problem" please read the suggestions for that problem
Please try to express your ongoing "same problem" in terms of those suggestions. Thanks! Good luck.
Regards,
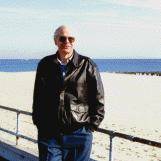
Ted Mooney, P.E.
Striving to live Aloha
(Ted can offer longterm or instant help)
finishing.com - Pine Beach, New Jersey
June 3, 2013
Q. What is the process of doing nickel plating per AMS2404 for the material AMS5643
I have read like plating will be of 3 types Low phosphor, medium phosphor and high phosphor. Which process suits the material AMS5643 H1075 condition?
Raghu Vamsi Machine Tools Private Limited - Hyderabad, Telangana, India
February 10, 2016
A. Hi cousin Saritha. There are several good books which introduce electroless nickel plating. In addition to the three phosphorous contents of acid baths, EN-phosphorous can also be alkaline based, and there is a boron based electroless nickel too.
The type of electroless nickel is not chosen based on the substrate material, but based on the needs of the surface. Solderability (boron best, low phosphorous good); and ferromagnetism (low phos), or freedom from it (high phos) can be criteria; but often the principal consideration is corrosion resistance (low phos is usually best for alkaline conditions, and high phos for acidic) or wear resistance/hardness (heat treated high phosphorous is best). It's not always easy to choose, but books like Mallory & Hajdu list dozens of automotive, aerospace, oil & gas, and electronics applications and what type of EN is usually chosen for them. Good luck.
Regards,
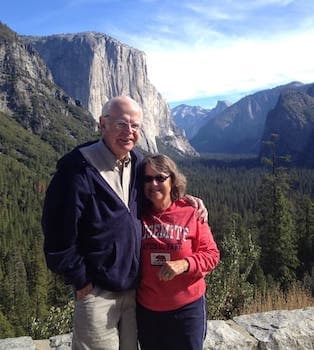
Ted Mooney, P.E. RET
Striving to live Aloha
(Ted can offer longterm or instant help)
finishing.com - Pine Beach, New Jersey
Q. Hello.
I am working in a plating company. I am quality assurance assigned to electroless nickel, with aluminum as base metal.
We'd had this problem since our early start up until now whereby we encounter unremovable black stain usually on holes of parts. These black stains will occur when our MTO reaches 1.0 and beyond, but is not consistent. Affected area is low thickness compared to other good areas. We use nickel sulphate solution and our reducing agent is sodium hypophosphite. All the monitoring parameters such as pH, temp., dipping time, concentration were controlled. We were thinking that it was air trapped during plating and was being oxidized. Kindly recommend what step we should do to eliminate the black stain.
Thank you.
- Cavite, Philippines
November 16, 2020
A. Hi, Antonie,
I think first thing first is to verify those black stain area is EN plated or not. For aluminum base material, there is a test called Alizarin test (hopefully it's the right spelling), you might remove those stains by water or IPA then conduct this test. Pink color indicating poor coating coverage.
You might update us once the test is done. Thanks.
- Singapore
November 18, 2020
A. Hi Antoine,
As suggested by Raymond, first you need to check if the black stain area is EN plated or not.
In my opinion it is more likely that the surface is nickel plated and then oxidized, because nickel oxide has a dark color, unlike aluminum oxide that is clear.
Black stains near holes, especially blind and threaded holes, are due mainly to insufficient rinsing after nickel. This usually happens on medium phosphorous electroless nickel, while high phosphorous tends to stain less.
Trapped air does not allow nickel to be deposited in the hole but should not lead to black spots.
- Soncino, Italy
January 14, 2021
Black Stain in blind and threaded Holes
Q. Hello
Hope all of us are doing well.
This is a continuation of what I've inquired about before:
I am working in a plating company. I am quality assurance assigned to electroless nickel, with aluminum as base metal.
We'd had this problem since our early start up until now whereby we encounter unremovable black stain usually on holes of parts. These black stains will occur when our MTO reaches 1.0 and beyond, but is not consistent. Affected area is low thickness compared to other good areas. We use nickel sulphate solution and our reducing agent is sodium hypophosphite. All the monitoring parameters such as pH, temp., dipping time, concentration were controlled. We were thinking that it was air trapped during plating and was being oxidized. Kindly recommend what step we should do to eliminate the black stain.
Thank you.
- Cavite, Philippines
January 15, 2021
A. Hi cousin Antoine. I was wondering why you tried to post this continuation as a new thread rather than here, then it hit me that perhaps you never received our notification about where your thread and the two responses offered could be found :-(
Hopefully you'll see it this time and be able to say "We conducted the Alizarin test, and ... " or "Although we were unable to do that Alizarin test because ..." :-)
Luck & Regards,
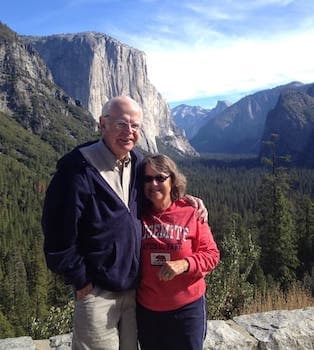
Ted Mooney, P.E. RET
Striving to live Aloha
(Ted can offer longterm or instant help)
finishing.com - Pine Beach, New Jersey
January 2021
----
P.S: Although we receive notice if an e-mail address bounces, we don't get one if our response was filtered as spam. Readers who wish to participate should probably please start by 'whitelisting' mooney@finishing.com
• Please see also thread 45977, "Electroless nickel plating is turning black, tarnishing"
Q, A, or Comment on THIS thread -or- Start a NEW Thread