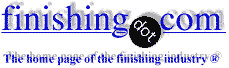
-----
Chromate Conversion Coating of Cast Aluminum: Problems & Solutions

⇦ Tip: Readers want to learn from your situation;
so some readers skip abstract questions.
Q. What is the minimum and maximum etching time for chromate conversion process to avoid water mark ?
Aishah CtEngineer - Malaysia
September 12, 2023
⇩ Related postings, oldest first ⇩
Q. I am trying to establish if there is any limitation associated with chromate conversion of aluminum casting alloys such as 355 or 356. Thanks, Gary
Gary Wonacottcomposites - San Diego, California
2000
A. 355 - 1.3 copper, 5 Si, 0.5 Mg. 356 - 7 Si,0.3 Mg. These alloying constituents create difficulty in chromating, and may reduce the protection, and affect the appearance of the chromate. Proper cleaning and pretreatment can improve the effect of a final chromate conversion coating. See www.finishing.com/chemicals/ for chemicals.
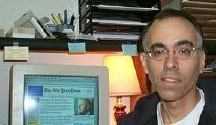

Tom Pullizzi
Falls Township, Pennsylvania
A. Degrease using non-etch alkali cleaner. Warm phosphoric acid based etch cleaners may be used with care, possibly fluoride accelerated. Hexavalent chromate processes are the only ones that will give satisfactory performance bare or painted.
Use high pointage chrome content and maximise coating weight without getting loose coatings. Aim for a rich golden yellow colour. Do not use hot water rinsing and keep dry-off below 100 deg C Roger
Roger Bridger- Croydon UK
A. The only limitation I know of surface wise is the limitation on corrosion resistance associated with castings, its around 1/4 to 1/6 the corrosion resistance associated with wrought material. Other than that, there's no downfalls per se with chromating casting material, it does provide increased resistance, but to what extent is questionable.
Matthew Stiltnerplating company - Toledo, Ohio
A. Casting aluminium is a problematic because of the hig silicone content in the alloy . Special treatment for removing the silicone obstacle with proprietary formulation can remove the obstacle. In my career I developed and sold product for that problem.
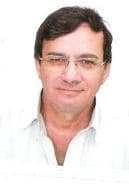
Yehuda Blau
YB Plating Engineering and Quality - Haifa Israel
2000
Multiple threads merged: please forgive chronology errors and repetition 🙂
Process parameters for yellow chromate conversion on die cast aluminum
Q. I need to find out the process parameters (pH, temperatures, solutions, times, etc) for the yellow/gold chromate conversion process on die cast aluminum alloys. I have ASTM B449 and MIL-C-5541 E, but neither of them go into the kind of detail I need. I would appreciate some feedback as soon as possible. I understand that there may be different processes (depending on the chemical manufacturer), but at this point, I would be happy with an example of what works for any one of them.
Steven Macri- Philadelphia, Pennsylvania, USA
2005
A. Essentially you need a hot cleaner (140 °F) acid activator, process tank and at least 1 preferably more rinses after each step and a final hot water (110 °F) rinse.
Gene Packmanprocess supplier - Great Neck, New York
2005
A. The processing parameters change fairly dramatically dependent upon the method of application (spray, dip, or brush) and chemical. If you are trying to evaluate a current supplier you may want to find out which chemical their using and contact the manufacturer of the chemical. If you are contemplating adding the capability to your facility, you may want to decide which of those application methods you prefer and then refer to the QPL for MIL-C-5541 to find which manufacturers make which chemicals for that application method. Then, again, contact the manufacturer and ask for the process parameters for their product.
Good luck,
Compton, California, USA
A. Do you want to know the parameters of chromate solution?
Now some of product are treated by chromate.The parameters of chromate is:
pH=1.5-2.2
Cr(VI): 6-9
Temperature: 25-35 °C
Time: 1-3 minutes
Good luck!
- Jinan Shandong, China
2005
Dark smut on conversion coated cast aluminum parts
Q. I just had some cast aluminum parts (alloy 380) chromate-conversion coated. The result is totally unexpected. We are somehow new to cast aluminum parts. The majority of our products are made out of extruded aluminum, employing alloys with a lower silicone content. In the past, conversion coating has not presented any problems for these machined parts. However, when we conversion-coated the cast parts, I noticed a very uneven coat (patchy yellow spots) and some sections presented a dark smut film. The purpose for the conversion coating is not only to protect the aluminum parts against corrosion but mainly for powder-coating preparation. Besides specifying ASTM B449-67, is there any other criteria I should specify to obtain satisfactory results with conversion-coated cast aluminum parts? Should I specify any other type of coating more suitable for this kind of process? I would greatly appreciate any insight on this issue.
Thanks.
Electronics Enclosures Engineer - North Hills, California, USA
2006
A. You chromate aluminum metal. You do not chromate the 15.4 % of non-aluminum alloying ingredients of 380. Many chromating job shops do not know how to reduce the silicon (and other stuff) from the surface. Some so-called 380 die cast will plainly not uniformly chromate. Thin walls cool faster than thick sections and more silicon comes to the top. The best advice to give your chromater is to Clean, DO NOT ALKALI ETCH, deox for 20 to 30 seconds in 50%/vol Nitric Acid with one pound per gallon ammonium bifluoride.
This will not match your 6061, but it will be as good as you can get on that particular casting.
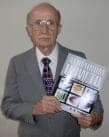
Robert H Probert
Robert H Probert Technical Services

Garner, North Carolina
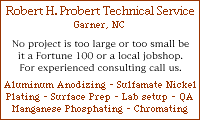
Q. Hello, We are having an issue with some smut/dirtiness making it through our Chem Film line. This smut is a dark powder that you can rub off with your finger. We thought it had to do with our pH and concentration levels of the Alodine at first, but we made some adjustments, (now running the pH around 1.75 and concentration about 1.05 oz/gal.) When the problem continued, we saw that the smut first was visible after the etch tank. We are thinking there is a problem in our etch or deox tanks. However, we are uncertain. See the details of our process below. We have a few questions that directly relate to this issue as well as ones that may indirectly lead us to a solution.
1. What are some recommendations or suggestions?
2. Are our chemicals for the etch and deox sufficient and correct?
3. Is the amount of air agitation a large factor to removing smut?
a. We do have air agitation but have lost some air pressure recently and are considering the lower agitation a possible cause.
4. We perform water break test after our cleaner in Tank 1. Should we be performing this test after the deox? If the water break test fails, should the job be re-started?
Thank you in advance for your time and suggestions.
Our Line is as follows.
CHEMICAL FILM PER MIL-DTL-5541 CLASS 1A
MATERIAL: 6061, 2024 aluminum
Process | Chemical & Concentration | Time |
Degrease | SC-78K 4-10 oz/gal | 2-10 min, air agitation |
Dip Rinse | in & out, air agitation | |
Spray Rinse | in & out | |
Etch | SC-608B 4-10 oz/gal | 30 secs, air agitation |
Dip Rinse | in & out, air agitation | |
Spray Rinse | in & out | |
Desmut Deoxidize | SC-592 6-15% | 1-3 min, air agitation |
Dip Rinse | in & out, air agitation | |
Spray Rinse | in & out | |
Chem Film | ALODINE 1200s | 15 sec - 3 min air agitation |
Dip Rinse | in & out, air agitation |
Joseph Lonigro
- Magnolia, Arkansas, USA
October 16, 2017
A. Joseph, try a 10-15 minute final rinse and letting the parts dry before handling them. Sounds to me like residual residue from the Alodine.
Ryan UnderwoodPPC - SAVANNAH, Georgia USA
October 18, 2017
A. Joseph
I would not etch the parts unless absolutely necessary i.e. the surface has a heavy mill skin. If you must etch the parts, deox the parts prior to etching so that you can reduce the etch time. Less etch, less smut. Solution agitation accelerates the rate at which the deox will remove smut. If the deox isn't up to par on chemistry, a longer immersion would likely help.
Your rinse times are on the short side for me. Very short. If you don't get the soap off the surface of the parts, the water break test isn't worth much. Yes, start over if the WB test fails. If you perform the WB test after the soap, you know you won't have contaminants that could interfere with subsequent steps.
- Green Mountain Falls, Colorado
Alodine 2600 chemical post treatment on diecast ADC10 (~A380)
Q. Hi,
We have some custom designed early sample diecast parts that are supposed to be Alodine 2600 coated. The parts have cosmetic issues that lead us to be concerned that maybe the chromate step could have been accidentally skipped. An associate engineer suggested a way to test is to apply pressure to a surface with a white cotton glove or equivalent. If black residue transfers from the part then it may not have been chromate coated. I did so, and black residue transferred.
The factory responded that the parts are chromated with Alodine 2600, a clear chromate. The alloy is ADC10.
This is an electronic enclosure where surface resistivity is critical. I do not currently have access to surface resistivity probes.
Do you have any knowledge if I should be concerned regarding the ability to wipe the part with pressure and get black residue/particulate to transfer?
I have monitored this site off and on for years, first time posting.
Best Regards,
- north chelmsford, Massachusetts
January 24, 2019
Q.
We are designing a modem and are having a similar problem with ADC10 die cast parts.
I posted a previous question last Friday (Jan 25) but after further searching of this site and others, I now have the phrase dark or black smut which seems to be more specific.
Questions:
1.) Our enclosure is an electrical enclosure that needs low electrical surface resistivity, we have specified Alodine 2600 clear, for RF containment.
Do you know if this black smut will act as an electrical insulator?
Some areas I can see the black residue clearly, other areas if I wipe hard I can get black residue to transfer.
Would I be correct to assume that areas that do not appear black likely have good electrical surface resistivity?
bleck design group - north chelmsford
A. Hi Tom, black smut on Aluminum castings is a very common issue and nearly always stems from problems surrounding the DeOx step: insufficient time in the DeOx (should pass a white glove smear test before proceeding), the wrong kind of DeOx (Nitric-Sulfuric-Ferric combination is great), insufficient concentration in the DeOx (run to Manufacturer's recommended levels), too much contaminant buildup (Silicon is an easy red flag to test for and maintain below 30ppm- your alloy has a LOT of it, up to almost 10%, which makes the Alodine process more difficult even in a clean DeOx tank), insufficient rinsing, or some combination of these. Furthermore, if the tank is being used for a two step process on castings- yours or others'- such as Alodine->Mask->Strip->Hardcoat (this is very very common) that requires time in a caustic etch prior to DeOx to remove the unwanted portion of the Alodine, these problems may become more serious due to a much faster rate of contaminant buildup.
And then the conversion coating simply does not work, and you are not getting back parts processed per your PO.
I've never checked resistivity of the smut itself as it's not supposed to be there to begin with. It is a deposit of alloying constituents, and should have been removed by the time the part leaves the DeOx tank.
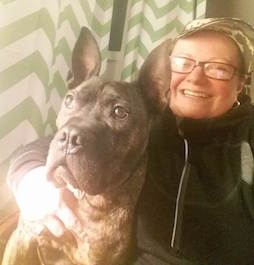
Rachel Mackintosh
lab rat - Greenfield, Vermont
Thank you Rachel.
We will investigate the chromate line being used for our parts.
bleck design group - north chelmsford
A. I preach that the ferric based deox is not the best for most diecast. Clean in non-silicated, skip the alkaline etch, deox in 50%/vol commercial nitric acid with one pound per gallon ammonium bifluoride, watch the part turn frothy white all over, 'bout 20 seconds in a fresh bath, rinse twice and chromate. But, again, all diecast metal is different, the recipe has wide ranges.
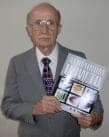
Robert H Probert
Robert H Probert Technical Services

Garner, North Carolina
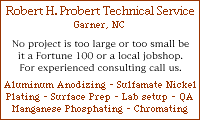
January 30, 2019
Cast aluminum turns black when chromate conversion coated
Q. what is the process for aluminium cast chromatizing? After cleaning the colour should be yellowish.
WE TRIED OUR PROCESS BUT OBSERVED THAT COLOUR IS BLACK.
Please give suggestion which process is better for material must be in yellowish and it withstands 1000 hours salt spray test.
And cast aluminium powder coated.
Dynamatic - Bangalore, India
March 18, 2020
A. Hi cousin B. We appended your inquiry to an existing thread where it seems to have already been answered. Please ask clarification questions as required. Good luck.
Regards,
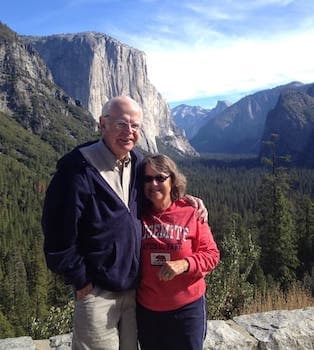
Ted Mooney, P.E. RET
Striving to live Aloha
(Ted is available for instant or longterm help)
finishing.com - Pine Beach, New Jersey
Q, A, or Comment on THIS thread -or- Start a NEW Thread