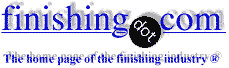
-----
Etch, deox, anodizing, sealing problems on type 2219 (2xxx) aluminum alloy
Q. I am trying to find an etch (i.e., the ingredients) to clean a 2219 aluminum assembly prior to welding to reduce the amount of porosity in the final weld.
Robert Allen- El Monte, California, USA
2001
2001
A. If you can't go for proprietary blends, nitric acid with a fluoride salt is needed if you use a silicated non-etch cleaner and no etching in between. If you want to chemically polish you can try mixtures of nitric, phosphoric, acetic acid ⇦ on eBay or Amazon [affil link] with water at room temperature or a little higher.
For the alkaline etch or cleaner, it really doesn't pay to try to formulate your own cleaner. Surfactants make all the difference, and it doesn't pay to buy them and mix them yourself. Try the Chemicals directory for suppliers.


Tom Pullizzi
Falls Township, Pennsylvania
Multiple threads merged: please forgive chronology errors and repetition 🙂
DE-OXIDIZING
Q. Has anyone had any trouble using a deoxidizer with fluoride as an ingredient on 2219 Aluminum.
Garry Pickettaerospace - Los Angeles, California
1998
A. We are the largest user of 2219 aluminum in the country. We make/made the External Tank for the Space Shuttle. We use fluoride in our deoxidizers successfully for many years.
Michael Campbell, Senior Materials EngineerLockheed Martin Manned Space Systems
1998
Q. Sir, please help me in providing information regarding removal of copper from aluminium alloy 2219 from its surface.
Thanking you sir,
Ravi Kumar- Chennai, India
2002
A. Hi Ravi.
The step being discussed here, de-oxidizing (perhaps more properly called de-smutting) is about removing the copper, silicon, and other non-aluminum alloying materials from the surface of the aluminum. The simplest, but not only, path forward would be to contact a supplier of metal finishing process chemistry and ask for a de-smutter for series 2xxx aluminum. If I am misunderstanding the question or your situation, please get back to us.
Regards,
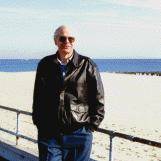
Ted Mooney, P.E.
Striving to live Aloha
(Ted can offer longterm or instant help)
finishing.com - Pine Beach, New Jersey
Treatment &
Finishing of
Aluminium and
Its Alloys"
by Wernick, Pinner
& Sheasby
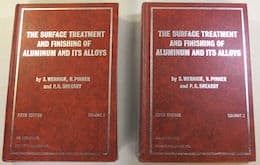
on eBay or Amazon
or AbeBooks
(affil link)
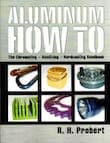
Aluminum How-To
"Chromating - Anodizing - Hardcoating"
by Robert Probert
Also available in Spanish
You'll love this book. Finishing.com has sold almost a thousand copies without a single return request :-)
ANODIZING
Q. I am trying to anodize an aluminum alloy 2219. But it is not getting properly anodized. What type and class of anodizing should I use. I am a lecturer in GIKI and want to demonstrate to the student the process of anodizing.
Muhammad BashirGIKI - Pakistan
2006
2006
A. Hello Muhammad. Type II is easier than Type III (hardcoating). This type of aluminum requires proper desmutting before anodizing, then a bit higher voltage than the easier aluminums (could push 18 volts); otherwise, standard amperage, chilled to cool room temperature, standard concentration should work even if not optimum. If you tell us the voltage, current, temperature, and concentration you are using we may be able to spot something you are doing wrong; but it is hard to summarize everything that you should be doing right because that subject fills whole books :-)
As a quick tip, though, consider anodizing 1xxx or 6xxx series aluminum for your demonstration instead of 2xxx because the high copper alloys are more difficult; and if you sample is old and the grain boundaries have become more pronounced, it will be even harder. Good luck.
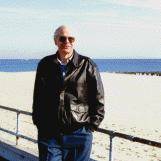
Ted Mooney, P.E.
Striving to live Aloha
(Ted can offer longterm or instant help)
finishing.com - Pine Beach, New Jersey
SEALING
Q. We have some aluminum 2219 forgings that were anodized to MIL-A-8625 / MIL-PRF-8625
[⇦ this spec on DLA] Type II several months ago. Some of the parts that were stored in a damp environment have experienced pitting.
Is there a test that we can perform months after anodizing to confirm that the parts were anodized and sealed properly? An anodizer that we consulted suggested that the parts may not have been sealed adequately. I have looked at ASTM B457 but too much time has elapsed. We can't use ASTM B680 because it's destructive and we do not have a test specimen that we can sacrifice (only the finished parts). People mentioned a "Sharpie" or dye test but per ASTM B136, the dye test is not applicable to alloys with greater than 2% copper.
Engineer - Pittsburgh, Pennsylvania, USA
September 20, 2012
A. Neither of the tests you mention are in accordance with MIL-A-8625 / MIL-PRF-8625
[⇦ this spec on DLA]. That spec calls out two tests that pertain to seal quality: Salt spray (ASTM B117), and light fastness. I'm assuming your parts are class 1, not 2 (dyed). If they are class 1, the light fastness test would not apply.
I'm not sure why you're hesitant to perform a potentially damaging test to your part(s) if they are no good as it stands now.
To add a bit of defense to the anodizer: The alloy you mentioned potentially can be up to 6.8% Cu. It's very possible that your lot of material was not very homogenous, and the pitting you are seeing is the result second phase Cu particles.
Sorry I can't be much assistance in recommending any additional testing outside of the ones you mentioned, but keep in mind that you can't hold your anodizer responsible for meeting testing requirements that are not listed in the specification, unless you specified that on your purchase order. Also keep in mind that most, if not all, seal quality testing (except impedance, or admittance) will damage the coating in some way if the parts are not properly sealed.
Here's a link to the spec which details the testing requirements to insure parts meet the specification.
http://www.wbdg.org/ccb/FEDMIL/a8625.pdf [ed. note Nov. 2016: sorry that link is now broken].
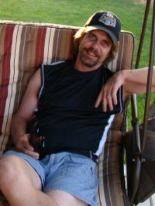
Marc Green
anodizer - Boise, Idaho
September 22, 2012
A. Dear,
Alloy 2219 and all 2xxx Alloys are more susceptible to pitting corrosion than other Aluminum Alloys even though the samples are sealed. 2219 alloys are Graded C in Anodizing process (Poor Protection) and show also some conductivity even after anodizing due to copper content on the surface. Those areas which have copper will have no protective layer, making a suitable dig for pitting corrosion. So it's not the matter of sealing.
Thanks
- Islamabad, Pakistan
October 1, 2012
January 8, 2016
Q. Hello Friends,
We are getting more and more 2219 for hard anodize and we are still having issues. The customer wants 1.8-2.2 mil of coating. Our process parameters are the following:
Clean
Etch
Deox
Hard Anodize is at 16% w/w sulfuric acid at 32 °F and we have a proprietary additive as well.
I tried a sample rack of 9 parts. I meticulously measured the surface area I had as best as I could (3.05 ft2) and calculated that to get 24 asf, I would need about 73 Amps. I ramped up to 73 amps in 5 minutes and I was going to hold at 73 amps for 54 mins to get 1.8 mil per the 720 rule. We don't have a hold amperage feature on our controller yet so we were manually adjusting the voltage as needed to hold the 73 amps. A strange thing would happen during the run. It would be holding fine at 73 amps and then out of nowhere it would start to run away and increase in amps rapidly to 50 or 60 amps higher. I would drop the voltage back down to prevent the burning and it would stabilize again at the 73 amps. It did that 3 or 4 times during the whole run. I thought it was very strange. I've never seen anodize do that before. At about 30 mins, I stopped the run to take the parts out and see how they were doing. I was baffled when I took them out and I saw all these spots on them (I called them measles). It almost seemed like it was anodizing selectively at certain spots and not on others. I continued the run to see if it would fill in but that never happened. I decided to measure them anyway and I had some parts with almost 3.0 in thickness and some with 0.8. I only had one burned part.
We tried again yesterday with a full load of parts but ramped them slower and we were only anodizing at about 20 ASF to see if the slow coating buildup would help the problem but the same pattern occurred. The parts were holding at amperage and would run away high again to about twice the amps it should be. This time we would wait to see if the amps would go down back to where they were before and eventually it did after a few minutes. We checked the parts and didn't see any burning. Super strange. It still had the measles spots but we just kept running it slowly until the parts looked all anodized. We measured them and they were over 3.0 mils
Does anybody have any suggestions? Why does it spot up and run away in amps? Any advice would be welcome.
Thanks!
Geronimo
- Oxnard, California USA
A. Hi Geronimo. In my limited experience those current fluctuations are the result of poor contact. What happens is the voltage is low and the contact is weak, so one part is not anodizing. Then you gradually raise the voltage and you reach a point where it's high enough to break through whatever insulating film was keeping current from flowing to that part. Now you not only have more parts drawing current, but one of them has no anodizing built up on it, and the voltage is already high, so it's draws too much current and burns, while starving the other parts.
The racks we see in the photo don't appear to be the anodizing racks but racks for some subsequent process. [ed. note: Photos were removed at request] Are you sure the anodizing racks make good contact with all parts all the time?
Regards,
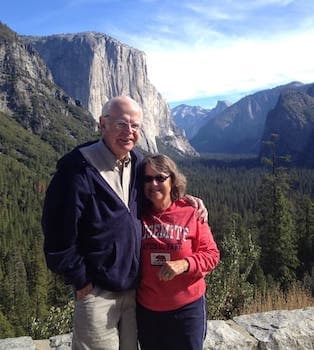
Ted Mooney, P.E. RET
Striving to live Aloha
(Ted can offer longterm or instant help)
finishing.com - Pine Beach, New Jersey
January 2016
Is it possible to hard anodize 2219 with a coating thickness of .001"?
Q. We have a drawing showing a .001" hard coat on a 2219 part. We're only able to achieve .0001 - .00015" of build up (with a total anodized thickness of about .0005" tops). Should we keep trying or have we reached the limit of what we're likely to achieve with this material? I believe our anodizer is using additions in the anodizing solution to reduce breakdown by sulfuric acid during the process but not sure what those are or what concentrations. Anyone able to offer any help/suggestions?!
Lucy Parker- Seattle, Washington USA
November 29, 2016appended
RFQ: Well, from looking at previous responses to questions on this topic, it would appear that we absolutely should be able to achieve .001" anodized coating on 2219. Can anyone recommend an anodizer who might be capable of doing this?
Thanks,
Lucy
Aerospace - Seattle, Washington, USA
November 30, 2016
Ed. note: This RFQ is outdated, but technical replies are welcome, and readers are encouraged to post their own RFQs. But no public commercial suggestions please ( huh? why?).
A. Hi Lucy. People are welcome to suggest what might be done to improve the anodizing, but we can't post brand or sourcing suggestions, only paid ads, sorry :-( (why?)
You may wish to review the list of anodizing shops supporting this site. Good luck.
Regards,
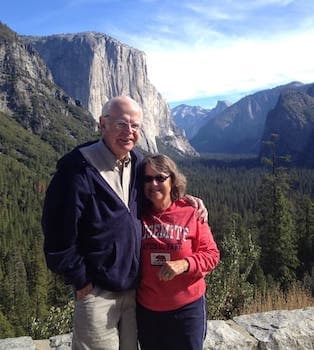
Ted Mooney, P.E. RET
Striving to live Aloha
(Ted can offer longterm or instant help)
finishing.com - Pine Beach, New Jersey
November 2016

April 9, 2019
Q. Dear sir,
We want to qualify type-2 chemical conversation coating as per MIL-DTL-5541
[⇦ this spec on DLA].
We have taken several trials but all got failed even in a single day itself. But 6 series and 7 series aluminium alloy gets passed continuously.
After a along study I have found that the problem is with pre treatment. During pretreatment process of potassium silicate based alkaline degreasing and iron salt and nitric based de-oxidizing the S-phase alloy (Al-Cu-Mg) in 2024-T3, gets into the surface of aluminium alloy and it may be partially or fully not dissolved during the de-oxidizing where my aluminium could etch mildly.
And if we continue the process to Surtec 650 without dissolving those alloys, the coating may not happen on that particular area which causes subsequent failure in salt spray test.
And also we have taken another trial without deoxidation but some small modifications, i.e., polished the surface with silicon carbide emery sheet, acetone
⇦ on
eBay
or
Amazon
[affil link] Warning! Flammable!
cleaning and Turco chemical used for alkaline degreasing. And finally we got salt spray passed. But this process sequence is not acceptable as we skipped the deoxidation process.
If so, could you tell some tip or alternative pre treatment process which can helps to dissolve that S-phase alloy and expose the high percentage of aluminium for Surtec 650?
Could desmutting process instead of de-oxidizing help to dissolve that S-phase alloy?
Could H2O2+H2SO4 combination for desmutting help?
And also, help me to understand more the differences between de-oxidizing and desmutting?
Regards,
----
Ed. note: Our understanding, which could be in error, is that de-smutting is a somewhat more accurate name for the process which which some people sometimes call de-oxidizing. We encourage non-commercial suggestions (different sorts of pretreatments or sequences, but not different brands or sources :-)
Q. 10-15 micron Anodising of 2xxx series Aluminium alloys (having 3-5% copper content) is carried out by sulfuric acid anodising process, and then dichromate sealing is carried out.
After 48 hrs of CASS test, pits are observed on 15-20% area of components.
Requirement by customer is that no spot/pits occur.
Any remedy? Please suggest.
- Nagpur, India
June 7, 2020
![]() |
A. Etch? Deox? Anodizing free acid (affects pore size), Anodizing temp (affects pore size? Anodizing current density (affects pore size)? Chloride content of all solutions (causes pits)? Heat treatment of the 2024 (migrates the copper)? ![]() Robert H Probert Robert H Probert Technical Services ![]() Garner, North Carolina ![]() June 8, 2020 June 8, 2020 A. Without knowing anything at all about your bath conditions and process, that's like asking, "I tried to bake bread but my mother said it was not good, what am I doing wrong?". ![]() Rachel Mackintosh lab rat - Greenfield, Vermont |
Q, A, or Comment on THIS thread -or- Start a NEW Thread