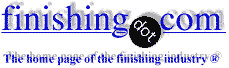
-----
Electroplating of inorganic particles such as diamond dust
Q. I am doing an investigation of plating inorganic particles with an electroplating bath such as copper or nickel. For example, when people put diamond particles in a nickel bath, the diamond particles are plated on the target and are embedded in the nickel matrix. This way, it ends up a surface which is wear resistant.
I wonder if we put TiO2 particles in a nickel or copper both, would the nickel particles get plated on the target and do we see a pure white color plated surface?
thin films - San Jose, Calif.
2006
A. I can't tell you the color or how much TiO2 you can occlude in the deposit, but I doubt that you could get anything resembling white paint; my guess is it would be more metallic looking.
Small amounts of TiO2 are occluded in low embrittlement cadmium deposits, so I'm confident that it is possible to occlude some percentage of TiO2 though. An alkaline bath sounds more promising because acid will dissolve TiO2, I believe.
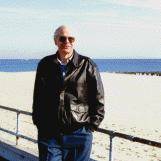
Ted Mooney, P.E.
Striving to live Aloha
(Ted can offer longterm or instant help)
finishing.com - Pine Beach, New Jersey
Q. I want to electrolytically plate Ni with inorganic particles added to change the surface properties of the Ni metal finish. For example, if diamond particles are added, the surface will be more resistant to wear and tear. My question is that if I add TiO2 particles to the Ni solution before plating, will the plated Ni surface have a shining white color or not?
Chung W. Ho [returning]thin films - San Jose, Calif.
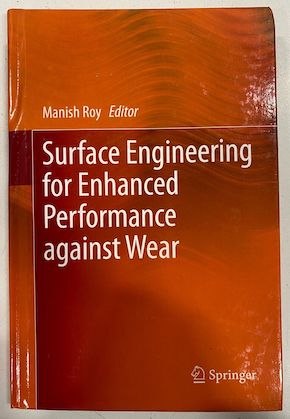
on eBay or Amazon
or AbeBooks
(affil link)
A. I think we are losing something in the translation here. You cannot electrodeposit non-conducting particles onto a nickel surface because the particles do not possess any charge and don't give a monkeys fig whether they go to the anode or cathode. What you are trying to do is called composite plating. The technology has been around for about four decades, but most people have had little success in making it work on a commercial scale unless they bought proprietary systems. This is because the original developers wrapped it up in patents and did not tell the full story. One of the tricks to good composite plating is to use the correct blend of surfactants - anionic, cationic, non-ionic and/or zwitterionic. The trick is to get just enough ionic activity on the particle to help attract it to the cathode. This can be coupled with adequate agitation and/or allowing the particles to gently "fall" from suspension onto the workpiece. the particles are then surrounded by the depositing metal and become trapped, a bit like something falling into a swamp. You will not be able to get a paint-like finish to the surface because the particles are trapped in a matrix of metal and will therefore be discontinuous. I would suggest you spend some time reading the patents and a couple of text books on composite plating technology - they should give you further guidance.
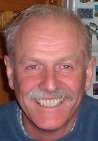
Trevor Crichton
R&D practical scientist
Chesham, Bucks, UK
Q. Comparison of the following categories in terms of market share and expected growth:
- Electro- vs electroless plating of composites,
- Metal types (Nickel, Gold, ..) used for the composites,
- Filler used for the composites (Boron Nitride, Silicon Carbide, PTFE, Nanodiamonds, other),
- Applications of composites and main filler per application,
- Drivers for growth of the composite plating segment, e.g., substitution of Chrome (VI) plating in specific applications?
- Cost breakdown of composite plating and differences in costs of fillers?
Analyst - Hyderabad,Telangana, India
November 14, 2015
A. Hi cousin Sheshank. I'm guessing you're trying to develop a market report on composite plating, as opposed to writing a thesis or public article on the subject? It sounds like a good topic, but I doubt that you'll get consolidated information from a public forum ... maybe occasional pieces of anecdotal data like "We prefer electrolytic to electroless because ...", or "We moved from diamonds to boron nitride because ...". You'll probably have to consolidate it yourself.
Chapter 11 in "Electroless Plating" by Mallory & Hajdu ⇨
is "Composite Electroless Plating" by Nathan Feldstein of Surface Technology in Robbinsville NJ. Companies like Surface Technology have specialized in offering licensed and patented processes for composite plating for many decades and can presumably supply you with huge volumes of such data, but might not want to offer it for free :-)
Good luck.
Regards,
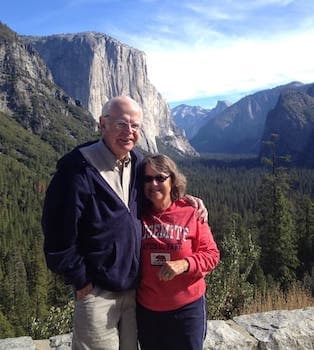
Ted Mooney, P.E. RET
Striving to live Aloha
(Ted can offer longterm or instant help)
finishing.com - Pine Beach, New Jersey
Q. Hello sir, thank you for your reply. I am sorry for not introducing myself, in my first question. I am a market research analyst, trying to make a report on the composite metal finishing one.
I would like to know which type of composite coating is mainly used now -- electroless or electroplating, and which out of these two would have a good future, based on your point of view.
Thanks a lot for your reply in advance
- Hyderabad,Telangana, India
by G. G. Gawrilov
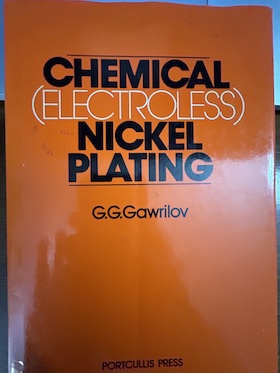
on AbeBooks
or eBay or
Amazon
(affil link)
A. Hi again. I don't personally have any actual data to make such a prediction, although I hope other readers will. But while we're waiting for them, my guess is that electroless has the brighter future. My principal reason for leaning that way is simply that the main advantage of nickel electroplating over electroless nickel plating is much lower cost -- but that tends to fade away when dealing with the complications of composite plating because it's not cheap with either technology :-)
I certainly can't speak for others, but it looks to me like Surface Technology and others are shifting their focus to composite electroless applications; it may simply be that it's not as old hat technology as electroplating, or may be because electroless nickel is more wear resistant and its properties easily manipulated through phosphorous content. "Chemical (Electroless) Nickel Plating" by Gawrilov ⇨
has a few pages on composite electroless plating and mentions this.
Good luck!
Regards,
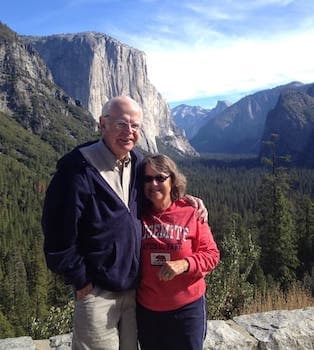
Ted Mooney, P.E. RET
Striving to live Aloha
(Ted can offer longterm or instant help)
finishing.com - Pine Beach, New Jersey
A. Lots of diamond tool bits (such as dental) sold in the market were plated through nickel electroforming process.
Weilong Tang- Toronto, Ontario, Canada
A. Hello,
The only hands-on experience we have with composite plating is diamond files which we regularly use. Best ones (german brand) are plated with a chrome binder. It may be a matter of better processing procedures but they easily outlast those made with nickel binder (electro or electroless?).
Best regards,
Guillermo (Bill) Marrufo
Mold Finish - Monterrey, Mexico
A. Thousands of grinding wheels are faced with electroplated nickel containing small diamonds which are "trapped" in the nickel.
For some wheels which use large diamonds, the diamonds are individually glued to the substrate, then plated with a heavy nickel layer to trap and hold them.
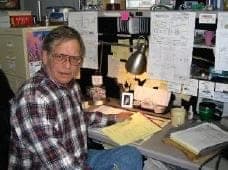
Jeffrey Holmes, CEF
Spartanburg, South Carolina
Q, A, or Comment on THIS thread -or- Start a NEW Thread