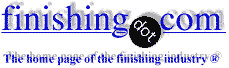
-----
Faraday effect in chroming yields "trouble areas"?
2006
Could anyone please confirm me, that when a chroming plant tells me, that because of the Faraday effect my product might suffer from weaker chrome plating in some trouble areas, namely around place where two tubes are welded together.
I take it to understand, that because of the differently distributed mass of steel in the product, the conducting of electricity varies and consequently has less "plating effect" in the "trouble areas?
Thanks in advance.
Morten Hecquet
importer of Towel radiators. - Kolding, Denmark.
2006
It is true that plating thickness is usually lower in low current density areas, and that chrome plating may be absent in those areas if careful attention is not paid. You probably should specify, and insist upon, full coverage with chrome and some minimum nickel plating thickness. Regarding the nickel plating thickness, it is common to specify the minimum thickness for any area that can be touched by a 3/4" diameter ball rather than debating whether it is possible to measure the thickness in a weld crevice and things like that.
If I am picturing your towel radiators correctly, there are a series of parallel horizontal tubes on which towels can be hung, and at each end the tubes are welded into a vertical "header". It's not so much that the welding is a problem as that the design results in "inside corners", and the plating current follows the path of least resistance, tending to not flow much into inside corners.
Ted Mooney, P.E.
Striving to live Aloha
(Ted can offer longterm or instant help)
finishing.com - Pine Beach, New Jersey
Only to add the mentioned effect is related to the shape of the part. The current sees the surface and prefers tips and edges refusing inside corners and cavities. Mass has nothing to do with it.
Guillermo Marrufo
Monterrey, NL, Mexico
2006
Hexavalent chromium plating solutions are very inefficient and also require a (relatively) high current density. Consequently, when there is a wide current density distribution on an article, the chromium thickness will vary significantly. The combination of poor efficiency and high cd requirement makes the problem worse. As a rule of thumb, the highest current densities are on the edges of articles and the lowest is in the middle. Consequently, you will get chromium build-up on the edges and a much thinner deposit at the middle. If there is a variable conductivity on the substrate, this too will have an adverse effect on the thickness control. Thickness can be controlled by careful design of the product and by using robbers and/or secondary anodes to redirect the current to where it is needed.
Trevor Crichton
R&D practical scientist
Chesham, Bucks, UK
2006
I have a similar issue on the inside of a 90 degree corner. Would reducing the angle to say 80 degrees and increasing the inside radius (effectively adding material to the corner) help?
Sheri Huther
- Oak Creek, Wisconsin USA
January 14, 2011
Yes, Sheri, that would help a bit for the nickel plating thickness distribution and a great deal for the chrome.
Hit your browser's "back" button if easily bored . . . but most plating, including nickel plating, follows Faraday's Law of Electrolysis pretty closely. That is, if the primary current distribution provides half as much current density to that inside corner as to other areas, then the nickel plating will be about half as thick on that inside corner. If you can get a little more current in there via a larger radius and smaller angle, you'll get a little more nickel thickness.
But chrome plating is different in that there is a cut-off current density below which no chrome at all will deposit. Rather, all of the current will simply turn the water of the plating solution into hydrogen and oxygen. So inside corners are a major problem for chrome plating: if you try to turn the current up enough for any deposition on the low current density areas, the high current density areas may burn. Often it is necessary to put auxiliary anodes in that corner to minimize the distance from the anode to that corner. Good luck.
Regards,
Ted Mooney, P.E.
Striving to live Aloha
(Ted can offer longterm or instant help)
finishing.com - Pine Beach, New Jersey
January 14, 2011
Q, A, or Comment on THIS thread -or- Start a NEW Thread