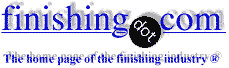
-----
Galvanic Corrosion between Galvanized Steel and Aluminum
< Prev. page (You're on the last page)
Q. Hi, I'm repairing some camper roof damage from where a tree fell on the top. It is an aluminum frame with aluminum rafters. Couple rafters were bent slightly (about 2") in a few spots - they are actually hanging about 2 inches low but top of rafters for most part are fine. Plan is to place 1 1'2 (3/16th) angle iron alongside of each rafter which will also sit on top of the wall frame on each side, and bolt to the rafter every 15 inches after jacking back into original position. Span is only 8 ft. What type of bolts or tapping screws would you recommend so we don't have issues? Should never be exposed to water or other liquids unless there is a leak. Are bolts the best to use or should we use self tapping? Also, we hope to have the angle iron powder coated if that helps. Thanks!
Chris Carda- Sioux Falls, South Dakota, US
April 1, 2015
A. Hi Chris. Although steel and aluminum are far from being galvanically compatible, galvanic corrosion only occurs in the presence of a wet and electrically conductive liquid like saltwater. Inside a camper I can't picture it being an issue.
It's a good idea to powder coat the angle iron because steel rusts. Zinc plated or galvanized hardware ought to be fine, and you'll probably find nuts & bolts easier to work with than self-tapping screws.
Regards,
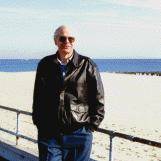
Ted Mooney, P.E.
Striving to live Aloha
(Ted can offer longterm or instant help)
finishing.com - Pine Beach, New Jersey
March 2015
Q. Hello All
I picked up on this very pertinent and interesting thread via the internet , my question is as follows
Here in South Africa there is a boom in PCV solar installations, our company is a balance of system supplier including roof mounting structure for solar panels on all kinds of roofs, including roofs made from galvanised steel.
We have products which are galvanised steel, i.e., galvanised steel strut going onto galvanised steel roofs, but also we have lots of enquiries for aluminium strut to be used to do the same job which is to go across the galvanised steel roof to be able to clamp and locate the solar panels. Starting from the roof, here is the order of the installation: GALVANISED ROOF SHEET, ALUMINUM STRUT, ZINC COATED CLAMPS TO CLAMP THE SOLAR PANELS TO THE STRUT, GALVANISED BOLTS TO BOLT DOWN THE STRUT. These installations are guaranteed for 25 years. You can imagine in a developing country like South Africa there are thousands upon thousands of installations taking place, so this subject has become very important and I would appreciate all comments and advice.
Many thanks.
- Johannesburg , Gauteng , South Africa
April 7, 2015
A. I don't know if this helps you, Mike, but about 10 years ago I was able to purchase (very cheaply) 3 solar hot water systems. These had been on the roof of a motel right next to the salt water reach of the Nambucca River in New South Wales. The owners were taking advantage of a government subsidy to upgrade to heat exchanger type heaters. The alumimium absorber panels were mounted on a galvanised angle iron frame so as to give them the appropriate angle of slope for the thermo-syphon principle to work.These panels were held in place on the frame with galvanised self-tapping screws. The panels had been manufactured in 1994. In order to remove them from the roof, I needed to dismantle the whole apparatus. The only sign of corrosion visible was some white powder around the site of the screws. In 2011 I installed one of these systems on my own roof and a recent inspection has shown no sign of further corrosion. I must admit that I live about 80 kilometers from the ocean so salt isn't a problem but average annual rainfall here is around 1000 milimeters (39.37 inches)
I hope this helps,
Graham Turner
- Grafton, N.S.W., Australia
April 13, 2015
April 15, 2015
Hi Graham, thank you for your information; it is extremely valuable. Nothing beats a physical report from a site that is several years old. For your information we have 4 branches of our company here in SA , but the one I work in is 6 hours from the nearest sea; we here in Gauteng on the South African Highveld at altitude have a very dry climate (vehicles of very advanced years show no signs of rust). Many companies are using aluminium frames on galvanised sheet roofs for mounting solar panels mostly due to weight reasons, but we also have had produced a very light galvanised steel strut and the only aluminium we have involved is the frame of the solar panel in 4 very small areas where each panel clamps to the strut.
Best regards
Mike
- Gauteng South Africa
May 5, 2015
Q. Hi everyone,
I have read lots of threads and I find your discussions very interesting. However, since I am not an expert in coatings / plating procedures (I am a civil engineer), I would appreciate your advice regarding the following problem, which -- I believe -- is relevant to this thread:
I own a house which is about 40 m from seashore. Thus, bear in mind that there is a lot of "salt spraying" - "electrolytic environment". The windows of this house are made from aluminium which is painted through electrostatic process. The aluminium seems to behave exceptionally (it has been 8 years since I installed the windows). The problem comes with the hinges and their mounting parts (screws).
Problem No. 1: There seems to be no aluminium hinges to fulfill my functional needs. At the moment I use Roto Fentro hinges, which are of unknown material and coating (the company doesn't answer my e-mail), but have definitely shown both white and red corrosion products after 3 years of exposure.
Problem No. 2:The mounting of the hinges has to be with DIN 7983 (ISO 7051 - UNI 6956) PH oval screws. I believe that the screws that were used, are just zinc plated. This may have "saved" the aluminium windows from galvanic corrosion, but couldn't stop the screw corrosion which has shown extensive red corrosion on the head and white corrosion on the main body.
As you can understand, the above problems sum up to the fact that I have to replace about 1200 corroded screws along with new hinges. Since it will be an expensive and tiring job, I need to find some materials that are more resistant in corrosion under "marine environment", and - at the same time- won't cause any damage to the aluminium through galvanic corrosion.
From what I have read so far, I have concluded that for screws I could use SS 316, with Dacromet or Geomet Plus coatings. Is that correct or do I have to look for Dykor, Xylar, Xylan or Delta coatings? Is the combination of SS 316 and Geomet possible or am I totally wrong?
Furthermore can any of the above coatings comply with my expectations regarding "extra corrosion resistance and minimum galvanic corrosion"?
For the hinges, I have been on a dead end since I cannot find SS316 hinges (only SS304), and I have excluded bronze and any other copper alloys in fear of galvanic corrosion.
Any help would be most apreciated.
Thank you in advcance.
- Athens, Greece
August 18, 2015
Sir,
Most of your comments show great understanding of the issues. In my opinion, you can't leave a seacoast structure for long periods without maintenance. From the photos it almost looks like salt encrusted on some of the surfaces.
The aluminium is performing well only because it is well coated. Zinc in contact with aluminium is sacrificial as you mention, but you really don't want them to have the chance to exchange electrons. The fasteners and hinges should be fully coated after installation except where there is moving contact. Anytime screws and other fasteners are installed they will damage the coatings, and I would suggest paint/coating after installation. Any place that other materials contact the coated aluminium, re-coat to prevent any moisture to the extent possible. Most coatings are slightly moisture permeable but do the best that you can. Where there is moving contact, use a lubricant and periodically renew it to exclude moisture. And inspect the aluminum frames for any coating failures or possible sources of moisture ingress, re-coating as needed.
316 stainless will still pit unless kept clean or coated. The GeoMet that you mention seems to be a line of products but most of them seem to contain zinc flake. It's not worth protecting stainless steel with zinc coatings.
Some copper alloys/bronzes will form a patina that will stop further corrosion, but you will have to use compatible bronze fasteners for best results. And coating/sealant where in contact with aluminium. If a patina is acceptable visually, bronze would not require coating, only lubricating for moving parts.
Seacoast is the worst environment other than actually aboard a ship, for corrosion, because a ship flexes more. The expression, "you pay me now or you pay me later" applies here. Either you apply and maintain coatings, sealants, and lubricants regularly, or eventually you replace all hinges and 1200 fasteners again.
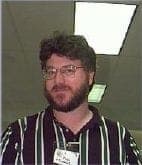
Paul Tibbals, P.E.
gas & electric
San Ramon, California, USA
(My opinions are not related to nor a statement of my employer's)
Options for mounting solar panels on residential metal roof
October 16, 2016Q. Need to mount 36 solar panels (36x66") on my house steel-panel roof. Solar panels will be mounted in 3 rows of 2 panels each (covering about 16 x 40'). For the metal framing I'm considering...
Option 1. Galvanized Unistrut steel channels lag screwed thru the painted steel roof to rafters below with zinc plated or galvanized hardware. Unistrut to unistrut connections would be made with zinc plated nuts and bolts. With zinc anodic to steel, I'm concerned about corrosion between the lags and the steel roof.
Could that be a long term life (20+ years) problem in the "mild" environment of middle Tennessee?
If I understand the corrosion mechanism correctly, wouldn't the lag screw's anodic zinc around the hole where the lag penetrates the steel roof be sacrificial? - eventually eroding the zinc to expose the underlying lag screw steel thus SLOWING corrosion at the (steel to steel) hole?
Option 2. Aluminum U-channels screwed thru the painted steel metal roof to rafters below with galvanized lags. Aluminum to aluminum connections would be made with zinc plated nuts and bolts. With zinc anodic to both aluminum and steel, I'm concerned here about corrosion between the lags and the steel roof as well as between the zinc fasteners and the aluminum channels and brackets (3 metals).
Where are the main corrosion threats for this option, and what do you recommend for improvement while keeping the cost down?
Thanks much,
Jack
home owner installing solar panels - Jamestown, Tennessee, USA
A. Hi Jack. I have heard, and I believe it, that rooftop residential installations away from the ocean are not particularly conducive to galvanic corrosion because rainwater is relatively non-conductive. I think you'll be best served with the galvanized Unistrut and galvanized hardware rather than introducing a third material of construction (aluminum).
Regards,
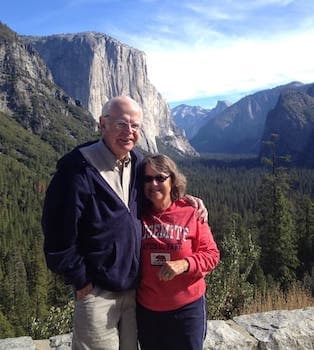
Ted Mooney, P.E. RET
Striving to live Aloha
(Ted can offer longterm or instant help)
finishing.com - Pine Beach, New Jersey
October 2016
Aluminium shade battens screwed to hot dipped galvanised steel frame
Q. I am designing the components of a simple sunshade structure - galvanised steel frame with aluminium RHS battens between the frames. I am concerned about the risk of corrosion between the two dissimilar metals and also the screws to be used to fix the battens to the frame.
Seeking advice on best way to prevent / minimise corrosion is this situation. Structure is located around 1.5km from a (partly) salt water lake (but not breaking waves).
Structural Engineer - Bairnsdale, Victoria, Australia
October 17, 2016
Anodized magnetic drain plug
Q. Can I use an anodized aluminum drain plug on my steel oil pan without creating a galvanic reaction?
david kron- us
June 23, 2017
A. Hi David. I don't know what kind of 'oil pan' you are thinking of. The oil pan on your car's engine? Just get a steel plug.
Personally I avoid, to the maximum extent possible, the use of any aluminum threaded stuff. It always corrodes and locks up. By my age I've removed numerous stuck light bulbs with pliers, wasted hours hacksawing off aluminum hose fittings, replaced several locks that had aluminum keys stuck in them ... :-)
Regards,
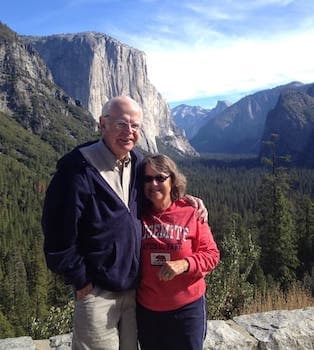
Ted Mooney, P.E. RET
Striving to live Aloha
(Ted can offer longterm or instant help)
finishing.com - Pine Beach, New Jersey
June 2017
Q. Ted thanks for your reply on the drain plug question. I intend to put oil on the thread of the plug before threading it into the pan. It will be changed every 9 months. the advantage to this anodized plug is that it has a steel magnet at the tip to catch the engine shavings. What do you think? Thanks David.
David kron- teaneck New Jersey
June 25, 2017
A. Hi David. These magnetic drain plugs are widely used, and are available with either anodized aluminum or stainless steel bodies. There is no real potential for corrosion inside the engine because the environment is oil not water. Seems like a pretty safe application :-)
Regards,
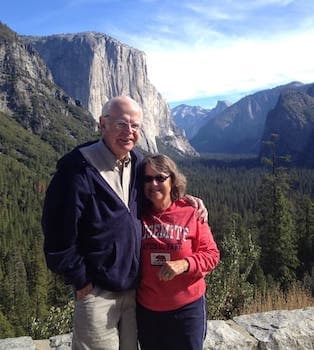
Ted Mooney, P.E. RET
Striving to live Aloha
(Ted can offer longterm or instant help)
finishing.com - Pine Beach, New Jersey
June 2017
Q. Hi,
I have a situation where I am mounting a Hot-dip galvanised cable tray to aluminium struts. I can separate the tray from the struts using rubber however I am not sure what screws I should then use to fix the tray to the struts as I am afraid that they may rust and the tray will eventually become loose. I originally thought that stainless self drilling screws would be ok but have since read that these would probably be worse than a galvanised screw. The cable tray is on a roof and will be exposed to water however it was about 30-40 km from the ocean so not much salt in the air. Any solutions for a self drilling fastener? Thanks
- Melbourne, Victoria, Australia
November 1, 2017
![]() |
A. Hi Andrew! TEL - N FERRARIS - Cañuelas, Buenos Aires, Argentina November 2, 2017 A. Australia has in many ways lead the world in the development of self-drilling fasteners. Australian Standard AS 3566.2 defines demanding requirements for coatings for self-drilling fasteners. These standards were developed by BHP Billiton (now Bluescope) to provide protection equivalent to their Galvalume roofing material. These fasteners are mechanically plated with a zinc-tin alloy (no hydrogen embrittlement) and topcoated with proprietary topcoats. One Australian supplier is Buildex (in Australia, formerly Deutscher). Other manufacturers meeting AS3566 are also satisfactory. ![]() Tom Rochester CTO - Jackson, Michigan, USA Plating Systems & Technologies, Inc. ![]() ![]() November 2, 2017 |
Q. We have traditionally been using SS 18-8 lag bolts for all our roof mount solar applications on asphalt shingle roofs. In the mount design, an aluminum base plate about 3/8" thick is lag screwed into the rafter (through the roof and sheathing). The base plate is flashed and an L-foot bolted to a stud on it. The mount supplier recommends using 5/16" x 5" SS lag screws to affix the base plate to the roof. What is the advantage to using stainless vs 5/16" hot dipped galvanized? Are the former simply stronger and more resistant to breakage during installation than the latter, as some have suggested? Or is there a material compatibility issue to be considered here, between the aluminum base plate and the lag screw? Or is it one of long term corrosion resistance? Note that all our installations are in snow country, far from marine environments.
Bhima NittaInstaller - North Bennington, Vermont, USA
January 9, 2018
A. Hi Bhima. My wife and I love Bennington & North Bennington and try our best to visit every year or two! I ask for your deference for a moment or two of reminiscing …
Way back when I was an underclassman in Engineering school, we started with courses in statics & dynamics, strength of materials, metals lab and so on, trying to absorb the theory of how to design so things were safe but economically feasible. But as we got closer to graduation we started to be taught about "codes": you don't build a steel frame building based solely on how strong you calculate a beam ought to be and how hard you think the wind will blow based on your own experience, and how many people you guess might stand in one room based on the parties you've attended; rather, design codes are written based on actual experience from successes and failures in hundreds of thousands of buildings. So, in addition to your own calculations, you always consult the building codes.
What I'm getting at is that -- while I'm happy to offer my personal opinion on a one-of-a-kind situation for a hobbyist or homeowner -- in this day & age where we have millions of rooftop solar cell installations which we should be learning from, I'm uncomfortable making suggestions based solely on my own limited understanding of general galvanic theory :-)
Yes, my guess is that 18-8 lag bolts are a better idea galvanically, and longer lasting, and probably of equal strength, and probably less likely to stain a roof if something goes south and they start to rust ... but surely there is a whole world of actual experience out there which should be tapped into somehow. There must be an organization of solar panel manufacturers and/or installers who are publishing journals, sponsoring seminars, and accumulating, tabulating, & publishing information on successes and failures of different materials and fasteners in rooftop solar installations. Good luck!
Regards,
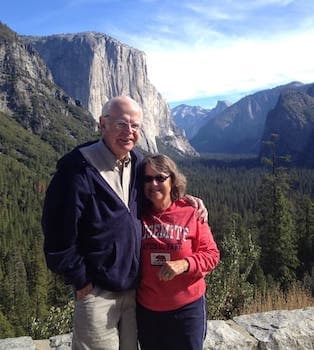
Ted Mooney, P.E. RET
Striving to live Aloha
(Ted can offer longterm or instant help)
finishing.com - Pine Beach, New Jersey
January 2018
January 10, 2018
Thank you, Ted. You're probably quite right - there should be resources for solar installers I can tap into. I'll look into them.
Regards,
Bhima
PS: When you come up to North Bennington next, come by and check us out! We are Power Guru and we are at 5, Bank St.
- North Bennington, Vermont, USA
Hot dip galvanized fasteners are rusting
January 23, 2018Hi,
We are facing issue of Fastener rusting.
The fasteners are of Hot Dip galvanised and the connecting part is a Galvalume (55% Al+45% Zn) coated steel.
We are using this kind of connections in all the solar fields across India.
I am confused whether it is a Galvanic corrosion or Failure of Zinc coating of Fasteners.
Regards,
Harshith
Quality - Hyderabad, India
Q. We have an outdoor shelter in a park that is located about 300 m from a harbour environment and 2.5 km from the ocean.
It has been installed for just over 13 months. The construction is galvanised mild steel RHS framing with powder coat over the top, a corrugated color steel metal roof. The curved sections with no corrosion are Aluminium with powder coat. The fastenings are 304 SS.
Can anyone help explain why there is corrosion on the galvanised frame? But not the aluminium.
Could it be poor pre-treatment before powder coating?
Inferior metals?
When it was installed the period was quite wet and stormy -- what if the uprights that are concreted had partially filled with salt spray / rain water during construction (I don't think there are drain holes) -- could this cause some sort of electrolysis across the framing.
- Melbourne, Victoria, Australia
February 23, 2018
A. Hi Paul. I can't see the roof real well, but it looks like it's fine ... which indicates to me that the pretreatment and powder coating of the steel structure may be of questionable quality. According to the American Galvanizers Association and British Standards Institute at
https://www.galvanizeit.org/hot-dip-galvanizing/how-long-does-hdg-last/in-contact-with-other-metals
and
https://www.galvanizeit.org/design-and-fabrication/design-considerations/dissimilar-metals-in-contact
this installation doesn't seem like it should have been problematic.
Regards,
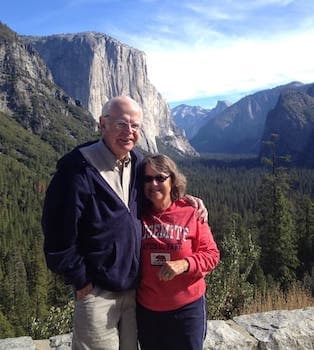
Ted Mooney, P.E. RET
Striving to live Aloha
(Ted can offer longterm or instant help)
finishing.com - Pine Beach, New Jersey
February 2018
A. Hi Paul, how are you doing? I send a great hello from Continental Europe to South Hemisphere!...
Is the paint flaking or bursting out from the galvanized substrate? It is not really perceptible from the pictures.
And for what understood, no (visible) defects on the aluminium powder coated parts, correct?
- Hagen, Germany
February 27, 2018
February 28, 2018
Q. Hi Marco
I have sent through some better images.
You are correct that there is no sign of corrosion on the roof or the aluminium curved section - only the galv.
It appears the powder coating is only failing where it is not exposed to the weather. Attached are 2 photos of the failing in close-up --
(click pic for higher resolution)
Thanks Paul
Paul Goodwin- Melbourne, Victoria, Australia
A. Hi Paul,
I would risk to say that this could be induced by galvanic corrosion, after all you have aluminium and stainless steel all together with zinc - at some part there should be a connection point between these metals that will close the electric circuit and accelerate the corrosion.
Another point leading to this can be also the pretreatment of galvanized previous to painting that may be causing the defect but from this side, I would bet on the galvanic corrosion.
- Hagen, Germany
March 5, 2018
March 2018
A. Hi. I respectfully disagree with galvanic corrosion being the cause of this problem, and believe that the galvanized structure was not properly pretreated and powder coated. The surface area of exposed aluminum and stainless steel is so small that, while it might theoretically cause localized pitting & corrosion near the joints and directly contacted area, I can't see it causing broad swaths of galvanized surfaces many feet away corroding, especially phosphatized and powder coated surfaces.
Regards,
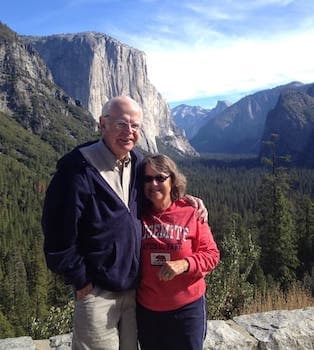
Ted Mooney, P.E. RET
Striving to live Aloha
(Ted can offer longterm or instant help)
finishing.com - Pine Beach, New Jersey
March 6, 2018
A. I agree with you Ted.
It certainly looks like inadequate or inappropriate pre-treatment of the HDG.
To find that the areas which are not concealed do not fail so badly is quite understandable as these would have the benefit of natural washdown from rainfall.
I also wonder if the Al & HDG were cured simultaneously (i.e., in one oven cure cycle)? If that is the case it is quite possible that the heavier HDG sections did not achieve full cure whilst the lighter Al sections might well have.
If the HDG sections are not fully cured then the polymers will not have completely cross linked and that would also contribute to poor corrosion resistance.
I suspect it to be a combination pre-treat and cure induced failure.
Hope this helps.
Regards,
Bill
trainer - newcastle nsw australia
Q. I'm designing a steel-framed house (cold formed steel) for a client who wants to use clear anodized aluminum windows. The house is in a hot and humid climate, ten miles from the sea (near Jeddah, Saudi Arabia).
I can insulate the window frame from the metal studs with Bituthene or similar rubber-like flashing, but the self-tapping screws through the aluminum nailing fins will still create direct (local) contact between the aluminum and the galvanized metal studs.
Will a certain type of screw material alleviate this problem? Or screws with a special coating?
Thank you for your help!
- Jeddah, Saudi Arabia
March 12, 2018
A. Caspar Mol wrote asking about galvanic concerns when fastening aluminum windows to a steel-framed structure. One answer is elastomeric memory-foam products (an "expanding foam tape") "Hannoband" that fills the void between the window's frame and the rough opening. Relatively few screws are needed, perhaps one each side. If you use a stainless steel fastener, the point of contact with the aluminum will be much less likely to led to corrosion. Furthermore, since the window will lack the conventional nailing flange, there will be no galvanic contact there. Also, the method has superior air tightness, leading to less infiltration, a plus.
Arthur OgawaTeX Consultants - Three Rivers, California, US
July 19, 2019
Q. Our neighbor's contractors put a hole in our aluminum fence; they offered to patch it with galvanized steel fencing. Won't these metal interact/rust quickly?
Thanks
- halifax nova scotia canada
March 14, 2018
A. Hi Valerie. It's obviously difficult to accurately predict exactly what will happen and when, but we do know that it's not advised to repair aluminum with galvanized metal this way, so it doesn't sound unreasonable of you to require that the repair be done with aluminum (unless we don't have enough of the story to comment appropriately).
Regards,
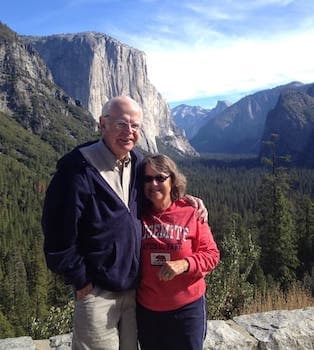
Ted Mooney, P.E. RET
Striving to live Aloha
(Ted can offer longterm or instant help)
finishing.com - Pine Beach, New Jersey
March 2018
Q. WOW I'm so impressed by the availability of expert opinions.
My issue: I have purchased a slide on camper constructed from galvanised steel panels, it is to sit on my aluminum truck tray.
I just learned about galvanic reaction and as the camper and tray will be exposed to rainwater and sea spray, I am hoping that you can provide a simple solution to prevent erosion.
Would a rubber mat, i.e., such as commercial kitchen flooring mat on the tray be a prevention solution?
Thanks
- Malvern, Victoria, Australia
June 15, 2018
June 2018
Hi Wendy. If the galvanized camper is not bolted to the aluminum truck body, a flooring mat to keep them from touching would be a complete solution. But if there is a metallic path from one to the other (bolts with no insulation for example), galvanic corrosion is possible, especially near the bolts.
Regards,
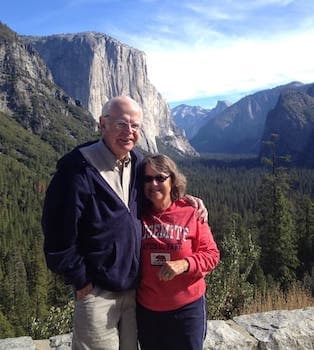
Ted Mooney, P.E. RET
Striving to live Aloha
(Ted can offer longterm or instant help)
finishing.com - Pine Beach, New Jersey
Best U-bolts for Aluminum Boat Trailer
Q. My situation: I need to replace the springs connected to the galvanized steel axle on my aluminum i-beam tandem boat trailer. While I am at this, I want to also replace some rusty U-bolts holding the 3" square cross members to to the i-beam frame. The trailer currently has 1/2"x3"x5" galvanized square u-bolts. The trailer is about 12 years old, threads are rusted on the galvanized bolts. The trailer goes in an out of salt water about 10 times/year and I typically rinse it off in a freshwater pond after use. I have not cut off the u-bolts but I do not see too much corrosion on the i-beams or cross members where the galvanized bolts contact the aluminum, a bit of light chalking.
My choices for replacement U-bolts are zinc plated, Galvanized, or Stainless. What do you all think?
- Cape Cod, Massachusetts / USA
August 12, 2018
A. Hi Ralph. Zinc plating is not suitable for saltwater exposure, probably not even for a freshwater only trailer.
Galvanized worked originally and will work again, but make sure they are actually galvanized (hot dip galvanized) by looking for the characteristic mottled crystalline look or dull drips. If they are shiny, smooth, drip-free and not mottled, they are probably not actually galvanized (some people started calling zinc plated fasteners "electrogalvanized", and then hungry marketers started feeling justified in shortening this to " galvanized"). If a standard nut fits them, they are not hot dip galvanized.
Stainless would be okay too but probably prohibitively expensive.
Regards,
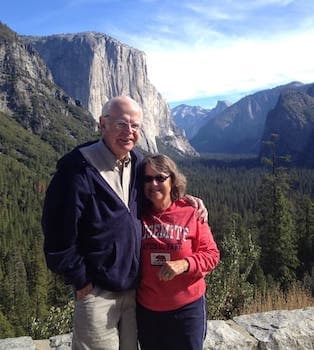
Ted Mooney, P.E. RET
Striving to live Aloha
(Ted can offer longterm or instant help)
finishing.com - Pine Beach, New Jersey
August 2018
Q.
Thank you Ted for the quick response!
The stainless is a bit more expensive but not prohibitive, so I may go with it. I was also a bit concerned about the strength of the stainless vs galvanized. Can I mix all three?
- Cape Cod, Massachusetts
August 15, 2018
A. Hi again, Ralph. You already know, if only from reading this thread, that you ideally shouldn't mix any metals unless they are insulated from each other … the more so on a salt water trailer. But, although aluminum coated bolts are used on aluminum airplanes, they are probably not available, affordable, and practical for an aluminum trailer, so you are forced to do at least a little mixing.
I would pick either galvanized or stainless fasteners and stick with it rather than tossing a salad. Good luck.
Regards,
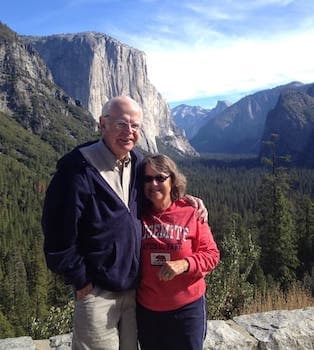
Ted Mooney, P.E. RET
Striving to live Aloha
(Ted can offer longterm or instant help)
finishing.com - Pine Beach, New Jersey
August 2018
Q. Will my anodized aluminum solar panel frames face galvanic corrosion?
Hi, my company is planning to build up a small solar park on the roof, but my company is close to an iron mine (undergoing one). The material of the frames are aluminum alloy coated with 15 microns type II anodized coating. Since the iron mine will cause some iron residue (either in the form of atoms, ions or oxidized compounds) to stay on the surface of the anodized frames, which might jeopardize the formation of rust, and possibly galvanic corrosion where anodized surface is incomplete or scratched. Considering the life of solar panels are at least 25 years long, will the frames face critical issues in the long term? Is there any way to solve the problem in that case? (e.g., increasing the thickness of anodized coating?) Thank you very much and I appreciate your opinions!
- Henan, China
February 13, 2019
March 18, 2019
A. Firstly I don't think that any air contamination from the Iron mine is of any real danger to your Aluminium frames.
You could powder coat/paint the Aluminium with UV resistant material, it will only extend the life.
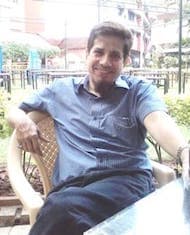
Khozem Vahaanwala
Saify Ind

Bengaluru, India
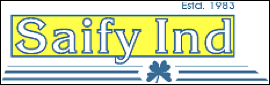
Q. Hello,
I am building an observatory from shipping containers. It's 11' by 20' with a 6' high wall around it and it is on top of the containers. It's going to have a roof 11' by 20' that will open 90 degrees (11' radius) with 2 linear actuators.
I'm trying to keep the roof weight down and would like to know if it would be ok to use aluminum as the framework and metal corrugated roof sheeting instead of steel as I had originally intended. I have three 6' long heavy duty steel piano hinges that will be welded to the existing steel framework. I could bolt the hinges to the aluminum, perhaps with some type of material between. There will be rubber gaskets between the existing steel framing and the roof framing to keep out dust, etc.
It doesn't have to last forever but I don't want galvanic action to corrode things in a few years. Thanks for any advise you can offer. I might add that the location is in the Nevada desert, very dry.
- Jean, Nevada, USA
July 21, 2019
A. Hi Bill. You can't have galvanic corrosion without a conductive liquid. It doesn't sound to me like you have anything to worry about.
Regards,
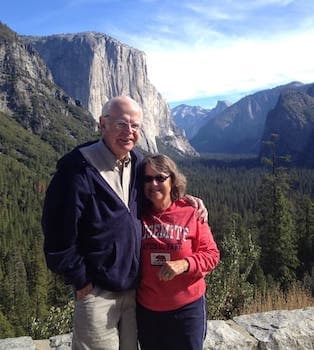
Ted Mooney, P.E. RET
Striving to live Aloha
(Ted can offer longterm or instant help)
finishing.com - Pine Beach, New Jersey
July 2019
Hi Ted,
Your very fast and reassuring response makes my project a lot easier to complete.
Many thanks,
- Jean, Nevada, USA
July 22, 2019
Q. My house in Fayetteville NC is having insulation put into the walls where it had no insulation before. I removed the aluminum siding and need nails to fasten the aluminum siding back onto the wall but unable to find 2-3/4" aluminum nails. Will galvanized steel nails be ok with the aluminum pieces of siding? I can only come close to the correct screw or nail, so the galvanized 3" nails are now the only way.
Also, a layer of insulation board will be put on just before the siding and zinc plated steel washers are to be used to help fasten each sheet. What is the best nail to use with the washer? The air gets very humid here in the summer months and whether or not these metals will corrode later will make or break this project!
Doing it Myself - Fayetteville, North Carolina, US
August 22, 2019
A. Hi Richard. I don't think I agree that aluminum nails are unavailable -- I see both 2-1/2" and 3" on Amazon and eBay. But if aluminum fasteners weren't available I think stainless is a better bet than galvanized or zinc plated for compatibility with aluminum, minimal rust staining, and long life.
Regards,
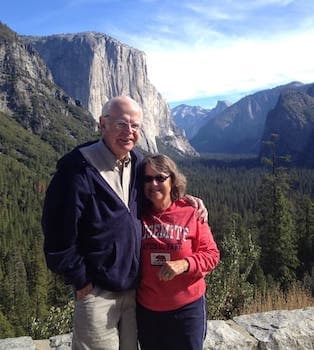
Ted Mooney, P.E. RET
Striving to live Aloha
(Ted can offer longterm or instant help)
finishing.com - Pine Beach, New Jersey
Q. Ted, well that's interesting on both situations because I've heard others say the opposite with regards to SS nails in contact with the aluminum siding, plus adding in some moisture. I reference a chart made by Fastenal and it strongly recommends not going with SS. What grade of SS would I need to use? There are a couple of grades out there and I would like to get the correct grade if I go with SS.
On the second item, I have been unable to find any aluminum nails longer than 1-1/2 inch which is a "standard" find for siding nails. All the home supply stores and stores listed online go up to 1-1/2". But I will check out Amazon if you are finding longer aluminum nails!
Thanks!
- Fayetteville, North Carolina, US
August 22, 2019
A. Hi again Richard. If I were you and I was sure Fastenal "strongly recommends not going with SS", then I wouldn't. But I don't know specifically what document you are referring to and whether you are interpreting it correctly, because the Fastenal chart I see says that 300 series stainless "marginally" increases corrosion in aluminum. Plus, both aluminum and stainless tend to build insulative oxide layers reducing the corrosive effects.
But personally, for the insulating board, if aluminum nails and washers aren't available, I would suggest any 3xx stainless nails and washers -- whatever is readily available 303, 304, etc.; 316 is premium stainless and is "better", but probably less available and not worth it. Aluminum throughout remains the preference of course.
Regards,
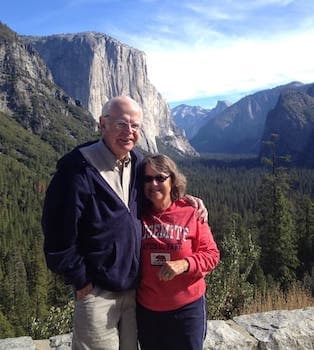
Ted Mooney, P.E. RET
Striving to live Aloha
(Ted can offer longterm or instant help)
finishing.com - Pine Beach, New Jersey
Q. Hi Ted, yes the chart is an article from Fastenal and the table shows SS listed pretty far down from aluminum. The farther from the aluminum on the chart, the more likelihood of corrosion according to how I interpret it. I would like to post the chart on here for you to see but not sure how to do this.
I have two different fastener situations going on with my project, the first is the aluminum siding and type of nails that will be penetrating the studs to hold the siding up. I plan now to look for long aluminum nails on Amazon. They will need to be 2-3/4 to 3 inches long and the thinner the better.
Second situation is the foamboard being fastened with nails through washers. This nail and washer assembly will not be touching any of the aluminum siding at any point. The washers are zinc plated so I want to use nails (long) that won't create corrosion. So these are two separate things on the same wall of the house.
Thanks.
- Fayetteville, North Carolina US
August 23, 2019
A. Hi again. If you have a URL for that chart or article we can link to it, but there is more to corrosion than the position on the galvanic series or seawater series.
If you're sticking with zinc plated washers on the foam board, then galvanized nails are correct. If you can use aluminum nails on the siding, that's best.
Regards,
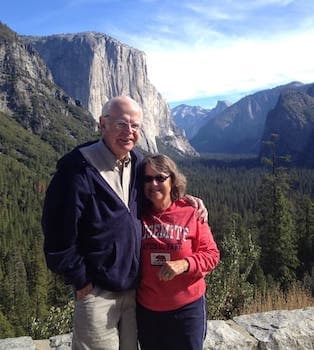
Ted Mooney, P.E. RET
Striving to live Aloha
(Ted can offer longterm or instant help)
finishing.com - Pine Beach, New Jersey
August 2019
Q. I am looking to purchase a coating which I can apply (spray) on zinc to isolate it from aluminum as per the below response from a contributor in this forum.
"I recommend looking into zinc/aluminum dispersion coatings. These thin, dry film coatings protect the steel from red rust while diffusing the bi-metallic cell created when the steel hardware comes in contact with the aluminum."
Can anyone point me to the link to purchase such a coating?
Thanks
Security systems - Mt. Vernon, New York, USA
October 7, 2019
A. Hi Alan. The response in question was suggesting a "dip-spin coating"; you can find various brands with the search term "dip-spin zinc-aluminum". That particular product cannot be sprayed on.
But there are lots of brands of zinc-rich spray paints, and if you patiently google for "spray zinc-aluminum -thermal -flame" will find one or two brands of spray-on zinc-aluminum. Sorry we can't recommend or link to brands or sources though (why?).
Regards,
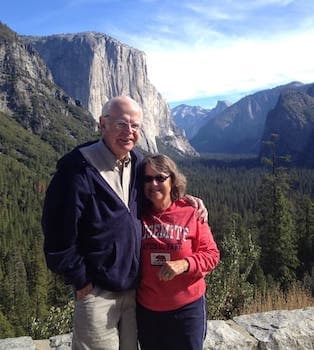
Ted Mooney, P.E. RET
Striving to live Aloha
(Ted can offer longterm or instant help)
finishing.com - Pine Beach, New Jersey
October 2019
Thank you.
Security - Mt Vernon
October 9, 2019
Q, A, or Comment on THIS thread -or- Start a NEW Thread